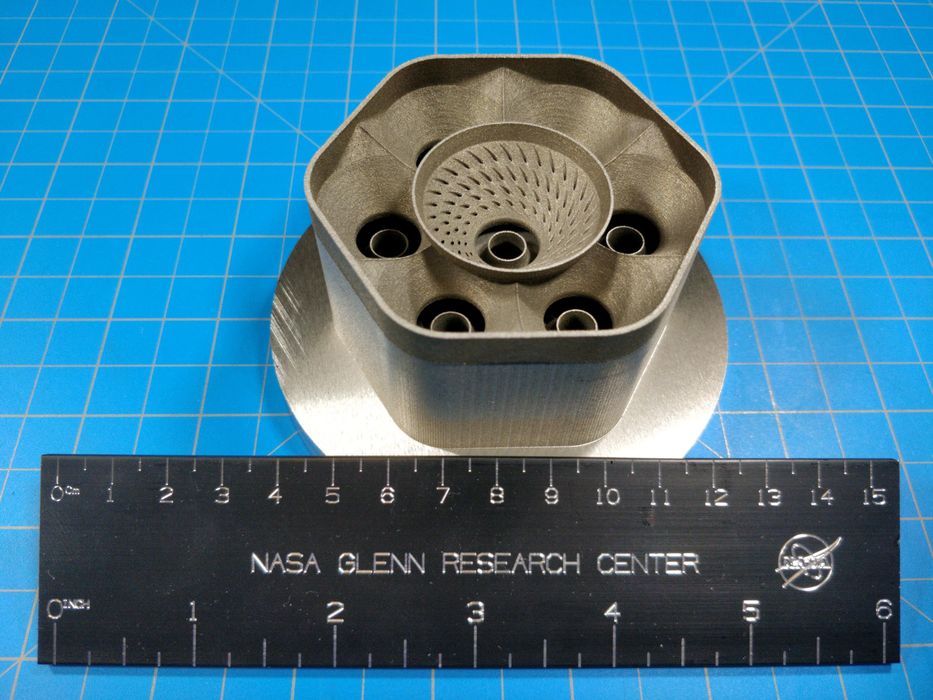
NASA announced the development of a powerful new metal alloy that will be of specific interest by the aerospace sector.
The new material is “NASA Alloy GRX-810”. They explain:
“NASA Alloy GRX-810, an oxide dispersion strengthened (ODS) alloy, can endure temperatures over 2,000 degrees Fahrenheit, is more malleable, and can survive more than 1,000 times longer than existing state-of-the-art alloys. These new alloys can be used to build aerospace parts for high temperature applications, like those inside aircraft and rocket engines, because ODS alloys can withstand harsher conditions before reaching their breaking point.”
GRX-810 is quite interesting because the higher temperature means a rocket engine could run at a higher temperature without compromising the structure. Higher operating temperatures mean the combustion process could be more efficient, leading to better rocket performance.
The malleability is also important, because in these days of reusable rockets, engines must fire repeatedly and reliably. A material that could withstand multiple uses would fit neatly into the reusability trajectory most rocket builders now work within.
NASA listed the performance advantages of GRX-810 when at the extreme temperature of 2000F (1100C):
- Twice the strength to resist fracturing
- Three and a half times the flexibility to stretch/bend prior to fracturing
- More than 1,000 times the durability under stress at high temperatures
Those are incredible statements and surely this material will be of great interest to those manufacturing rocket engines.
Ironically, this material is actually made using a 3D printing process. The oxide dispersion strengthened material was created by using a specialized 3D printer to uniformly spread nanoscale oxides into the alloy. The ratios were determined by using complex computational models that predicted the optimal mix.
NASA explained how this worked:
“Using thermodynamic modeling, one of many computational tools discussed within the NASA 2040 Vision Study, the team discovered the optimal alloy composition after only 30 simulations.
This modeling tool produces results in much less time and with lower costs than traditional trial-and-error processes. The tool also avoids dead ends by showing researchers not just what metal types to incorporate but how much of each element to infuse into the composition.”
NASA did not state whether the new alloy would be used in 3D printers to produce new, strong parts, but I strongly suspect this will be the case. Any metal can be transformed into powder for use in PBF equipment, or made into wire form for use with DED equipment. Either way, NASA’s new material will ultimately make its way into 3D printers.
The new process used in the development of GRX-810 appears to be unprecedented. This suggests that NASA (or others) could use the same technique to develop even more unusual materials for a variety of industrial purposes.
Via NASA
I’m just amazed that NASA leads with Fahrenheit in 2022. Especially after the Mars Climate Orbiter debacle. As an organization that in part is tasked with inspiring the next generation of engineers and scientists, I’d have thought that encouraging fluency in the units predominantly used in those domains would have been important to them.