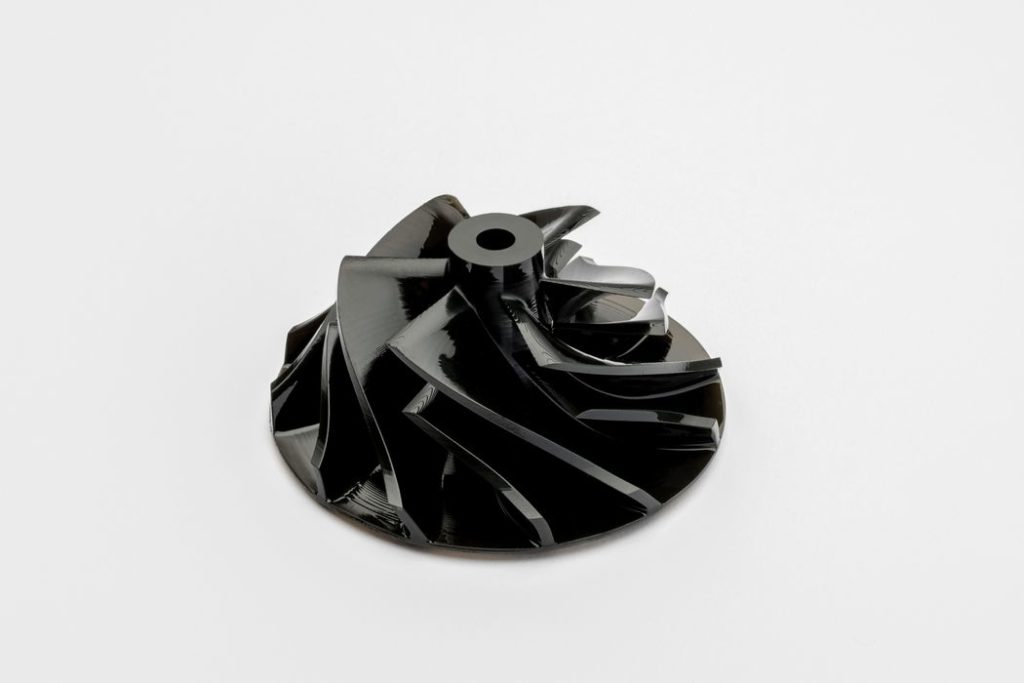
Several new AM materials were announced in the past week.
We often receive notes from manufacturers that have developed new and unique materials, but most times the news value is relatively low and these do not warrant a story on their own. However, we thought we might bundle together several material announcements into one post, this one, for your review.
HDPE For voxeljet HSS Process Demonstrated
voxeljet announced a new material for their HSS 3D printing process, High Density Polyethylene (HDPE).
The company is well known for their large scale sand 3D prints for casting purposes, but few know about their revolutionary new HSS process. It involves using an infrared-sensitive liquid binder that is heated to fuse polymer particles together. More information about HSS here.
It was expected that voxeljet would introduce a series of new materials for HSS because the process is capable of handling a wide variety of polymers. The new HDPE is likely only the first of many for HSS.
More specifically, voxeljet revealed that one of their materials partners, the Fraunhofer Institute, had successfully tested the HDPE material on a VX200 HSS system.
HDPE is a very interesting material that is not widely used in additive processes, even though it is a highly versatile substance that is commonly used to make milk jugs. One of its major properties is that it is water-repellent and considered food safe, and thus it is used for all types of bottles.
With voxeljet’s ability to 3D print HDPE, we may see some interesting new applications of larger-scale HDPE parts.
Markforged Introduces “Precise PLA”
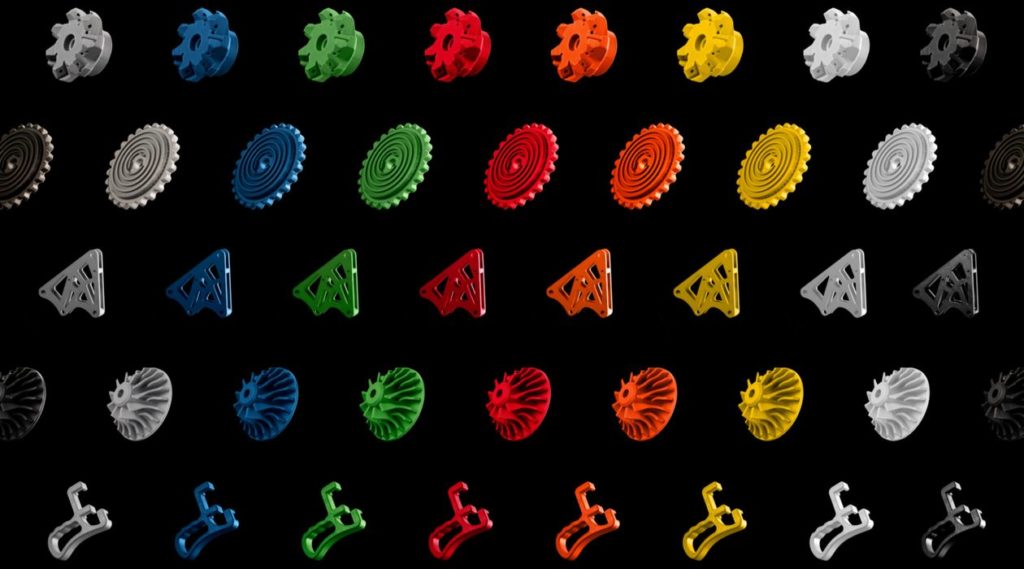
Markforged introduced a new material: PLA. This would seem quite surprising at first, because PLA is the most basic 3D printing material around, and every FFF 3D printer can use it. Or can they?
This is where it gets interesting: Markforged’s devices were designed right from the start to use advanced materials, such as nylon, carbon fiber and even kevlar. They were among the first 3D printer manufacturers to deliver the capability for operators to produce strong end-use parts, rather than just prototypes.
But now the tables have turned: Markforged wants to enable their 3D printer operators to also produce inexpensive prototypes. This is quite like the progression from other 3D printer manufacturers that started with basic materials and developed upgrades for advanced materials, except in reverse for Markforged.
One of Markforged’s customers, Steve Michon of Zero Tolerance LLC, explained:
“When using other 3D printers and PLA materials, the results were not as precise as required, even after multiple iterations. Printing parts to the size and quality we need, with the required functionality and at a great price point is critical for our business. Once design validation using Precise PLA is completed, we move to production with Markforged’s Onyx material for functional testing, followed by printing with continuous carbon fiber for added safety for our final, end-use part. With this new material, we can now utilize our Markforged printer to deliver great results repeatedly throughout the entire design and manufacturing process. This is the most reliable additive platform we’ve ever used. It just works.”
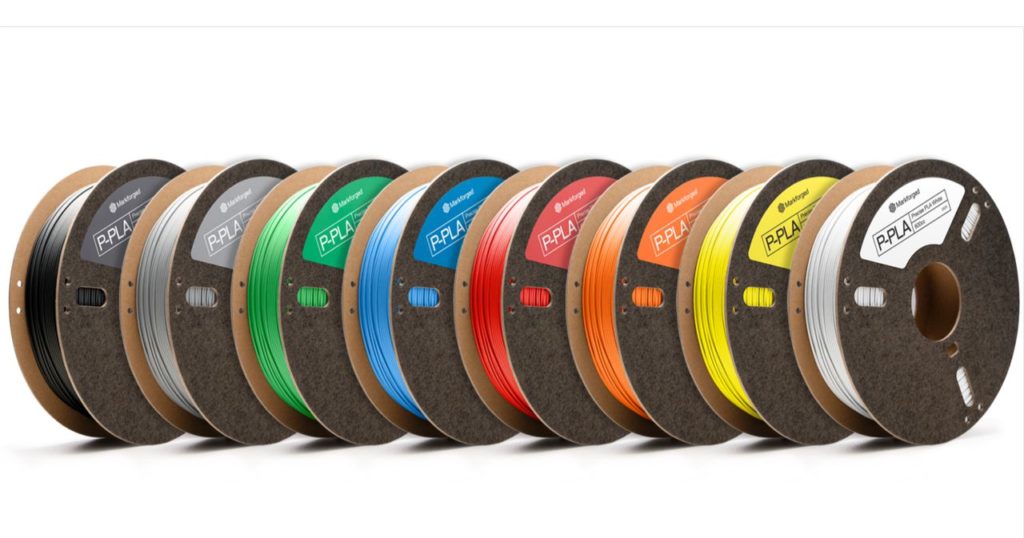
This fills the gap in Markforged’s equipment line in the prototyping area. Markforged will provide the newly named “Precise PLA” in eight different colors for their Mark Two and Onyx Pro machines, with others to follow in the future.
ALTANA Adds Two New 3D Printing Resin Series
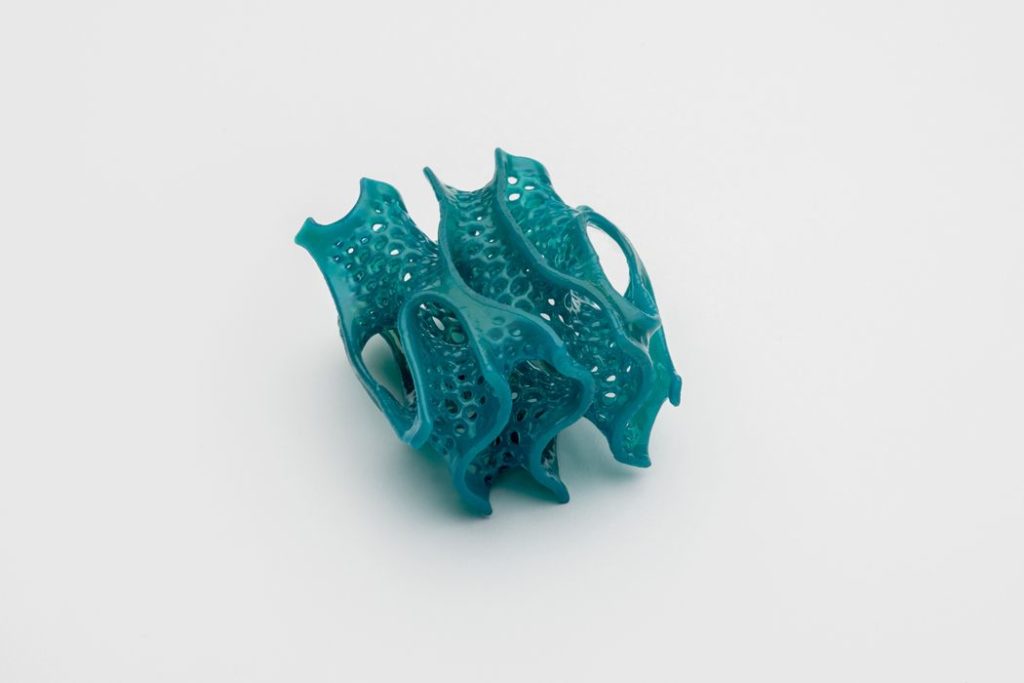
ALTANA is a German chemical firm that produces a line of 3D printer resins they call “Cubic Ink”. The products include a variety of resins offering basic and advanced capabilities, including flexible and rigid offerings.
The news is the introduction of two families of resins for their portfolio, High Performance and Prototyping.
The High Performance series includes four resins:
- VP 1 series: With heat deflection temperatures exceeding 190°C, these
- rigid, solid materials are designed for use in demanding applications at very high temperatures, that is, very high HDT values and stability over a long period of time even in the high temperature range.
- VP 2 series: Solid and thermoforming materials for end-use applications; fast printing thanks to low viscosity and a wide range of applications thanks to adjustable mechanical and thermomechanical properties.
- VP 3 series: Materials with adjustable softness that permit high deformations, that is, materials that can be used flexibly even at low temperatures.
- VP 4 series: High-resolution materials striking a good balance between heat resistance and brittleness at low viscosity, plus good mechanical and thermomechanical properties as well as adjustable properties, so that fast yet high-resolution printing is achieved with great design freedom.
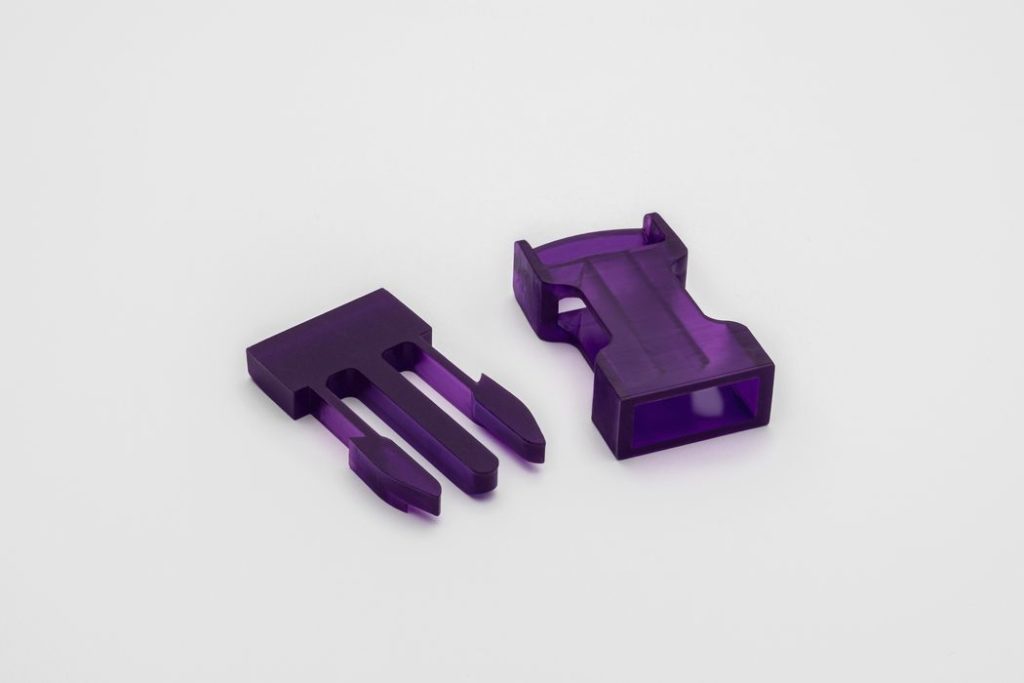
The Prototyping Series also includes four resins:
- Tough series (600 VP): Very high-resolution materials for prototyping and
- general applications with good chemical stability vis-à-vis aqueous systems
- and maximum design freedom.
- Rigid series (200 VP): Dimensionally stable materials for functional
- prototyping with adjustable rigidity.
- Dental series (100 VP): Materials that can be used in dental applications
- for efficient and high-resolution printing with adjustable rigidity and
- uncomplicated post-processing for maximum design freedom.
- Clear series (401 VP): Materials that have special optical effects with high
- transparency as well as an adjustable refractive index.