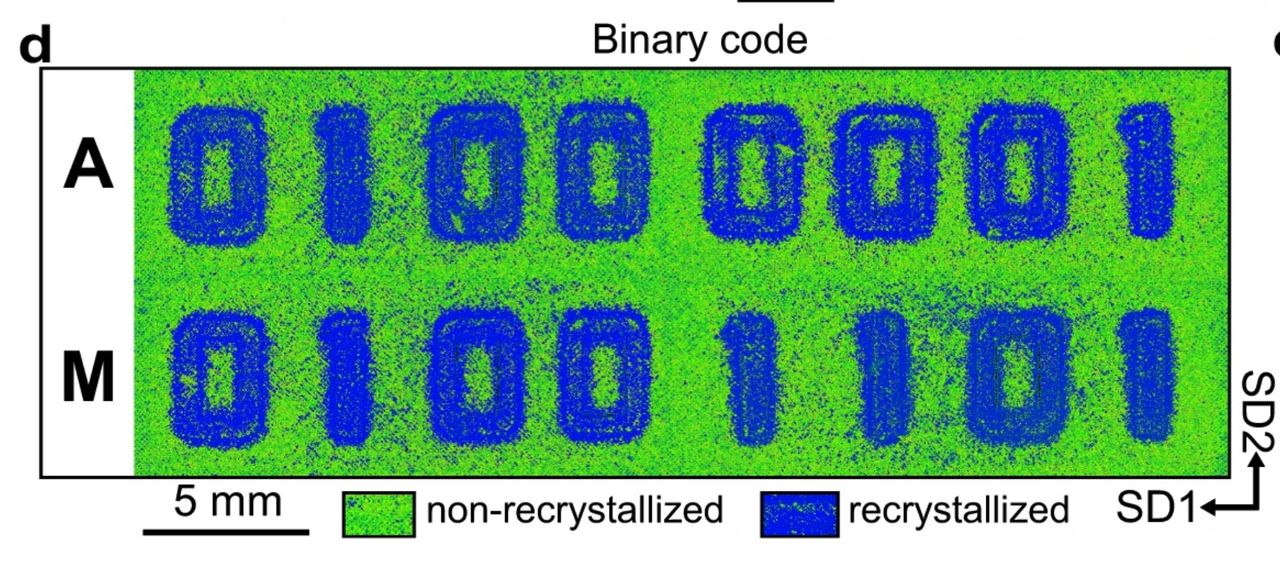
There’s been a breakthrough in controlling the microstructures of metal 3D printed parts.
A joint team of researchers from Singapore and Switzerland were able to develop a process for “programming” the microstructure of metal parts produced using the common LPBF process.
In the LPBF process, a laser tediously solidifies selected portions of a layer of powder. More powder is added, and subsequent layers are produced in a similar way, eventually building up an entire object.
During LPBF processing, each particle of the powder bed gets more-or-less the same laser treatment. The laser dot sweeps across the bed with a specific speed and power, attempting to cover all required areas. The goal has been to cover all spots in the least amount of time.
As you might imagine, this approach means each area of the metal print is treated in a similar thermal manner. The result is parts that have a consistent microstructure, but it’s not often one that’s desirable.
In the non-3D print world, metal has been produced for centuries, normally using the “heat and beat” process. In this approach, mechanical force is applied to a heated part to reorganize its internal microstructure, with a goal of making it stronger. This is partly why you see blacksmiths hammering away at a chunk of hot metal.
In modern systems the same principles are applied, but this really can’t be done using the LPBF process. It puts metal 3D printed parts at a disadvantage, strength-wise, compared to many conventionally made parts.
Why not “heat and beat” the 3D printed parts? That’s usually not possible because the reason the parts were 3D printed in the first place was because they had complex geometries that could not be made using conventional processes. These delicate structures would be damaged or distorted if beaten, so that won’t work.
The new research seems to have found a way around this dilemma. They explain:
“Gaining control over the dislocation density and the alloy’s chemical heterogeneity directly during LPBF would allow engineering the microstructure evolution of the material upon HT and drive recrystallization ‘on demand’, without the need for any additional mechanical deformation.”
They don’t beat the parts, but instead make use of unusual approaches with laser motion.
Two strategies are used: they vary the distance between laser passes. Instead of “just touching”, they may overlap slightly. The second method is to illuminate an area a second time.
They discovered that by varying the parameters of these two approaches they were able to significantly alter the microstructure of that region in predictable ways. They explain:
“LPBF materials can essentially be thought of as stacks of overlapping melt pools, each one producing a localized thermo-mechanical treatment. The rapid heating and cooling associated with each melt pool, in fact, induces expansion and contraction of the material, generating plastic strains and thus driving dislocation accumulation14,15. It follows that the total plastic strain in the as-printed material depends on the number of melt pools per unit area per layer, or the number of melt tracks per unit length.”
This is incredibly good news for anyone using LBPF equipment. That’s because it appears there would be no need for any hardware changes to achieve superior parts: the research indicates there are only print parameter changes required.
This could very well become standard practice for any LPBF operation, and we will soon see much stronger parts emerge from LPBF equipment.
Via Nature