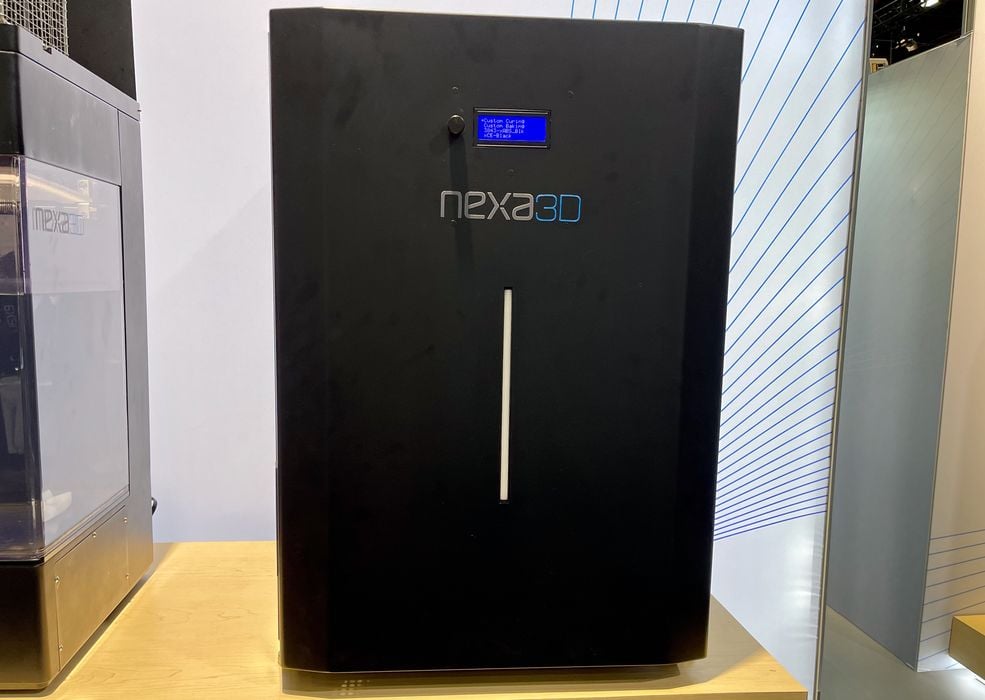
Nexa3D has more 3D printing solutions than you might think.
Founded in 2016 by a group that includes former 3D Systems chief Avi Reichental, who is now the company’s CEO, Nexa3D was initially a developer of a resin 3D printer for industry. Today some may still believe that’s all they do. But nothing could be further from the truth, as the company has been rapidly expanding in the past couple of years and now offers quite a variety of additive solutions for industry.
Nexa3D’s key technology is their proprietary Lubricant Sublayer Photo-curing (LSPc) process, which allows resin 3D printing to occur at tremendous speeds by avoiding the “peel delay” that occurs in most other resin processes. This was first implemented in the company’s NXE series of 3D printers. Prints can be completed in only minutes.
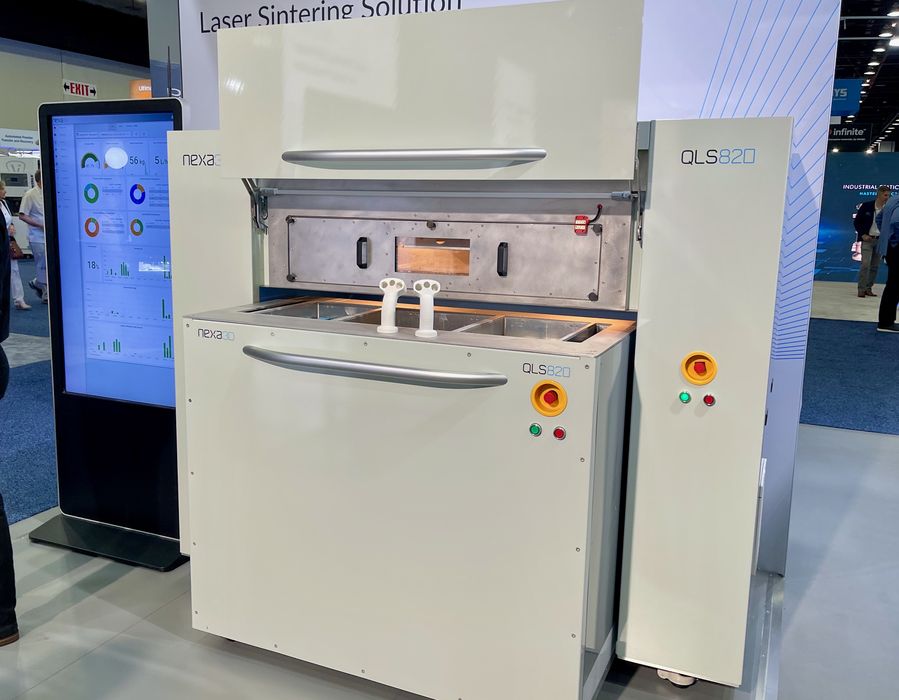
But then in the past few years things have changed. In addition to the NXE series, Nexa3D acquired NXT Factory, a producer of SLS 3D printers. This meant Nexa3D offered two different 3D printing processes, one for resin and one for thermoplastic powder. Their QLS 820 machine is able to print an amazing 8L of material per hour, and Nexa3D bills it as the “World’s Fastest SLS 3D Printer”.
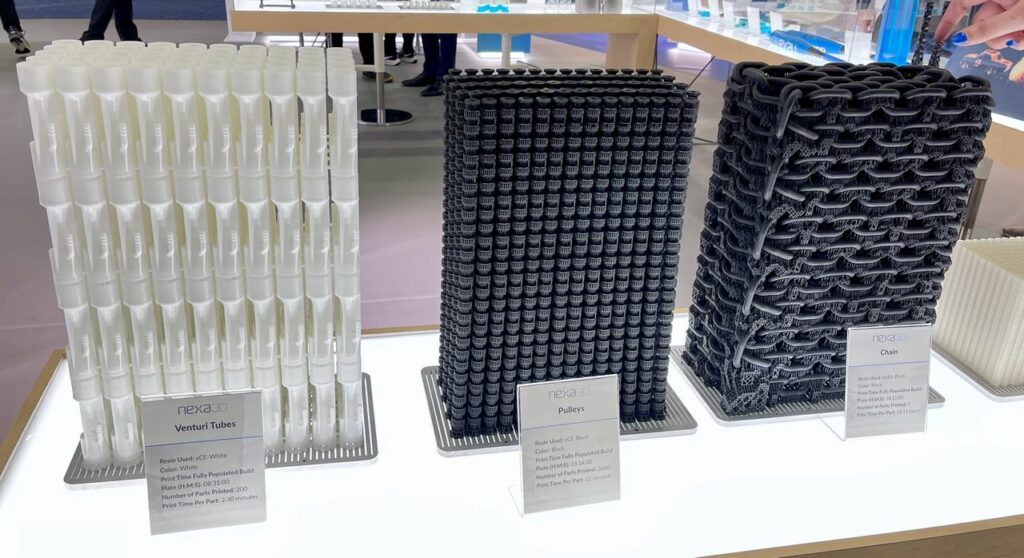
In 2021 the company received a massive US$55M investment round, which seems to have powered them up for a number of new activities. To date they seem to have raised over US$95M, giving them plenty of cash to develop new capabilities.
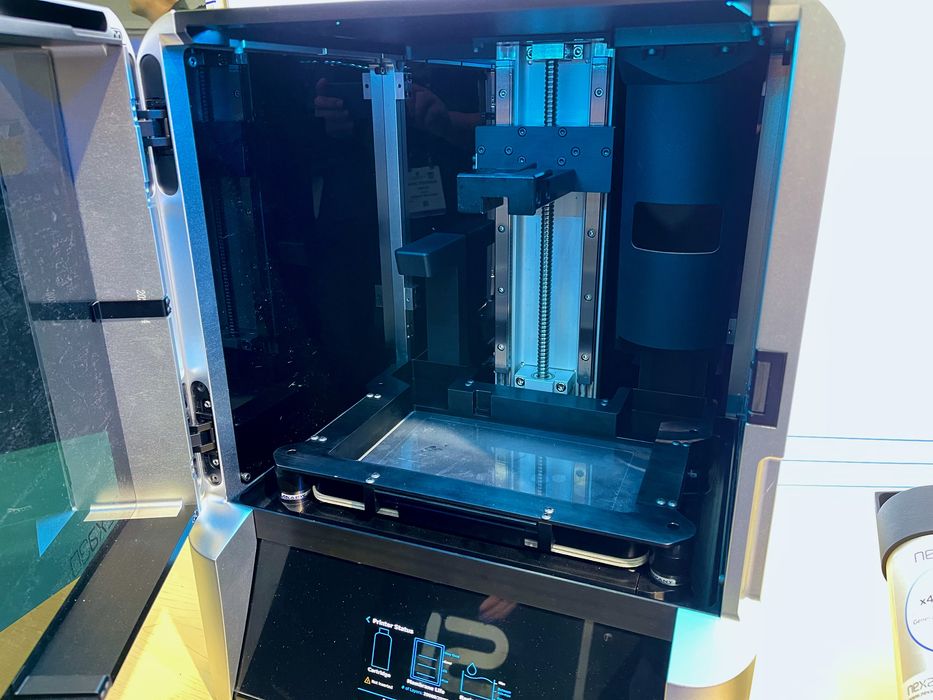
One of the first outcomes after the new investment was their new XiP resin 3D printer, which we were happy to be shown by Nexa3D’s Senior Director, Strategic Communications and Ecosystems (and former Fabbaloo Managing Editor), Sarah Goehrke .
The powerful XiP is a device smaller than their earlier systems, but one that incorporates a number of operational learnings to make it very easy to operate.
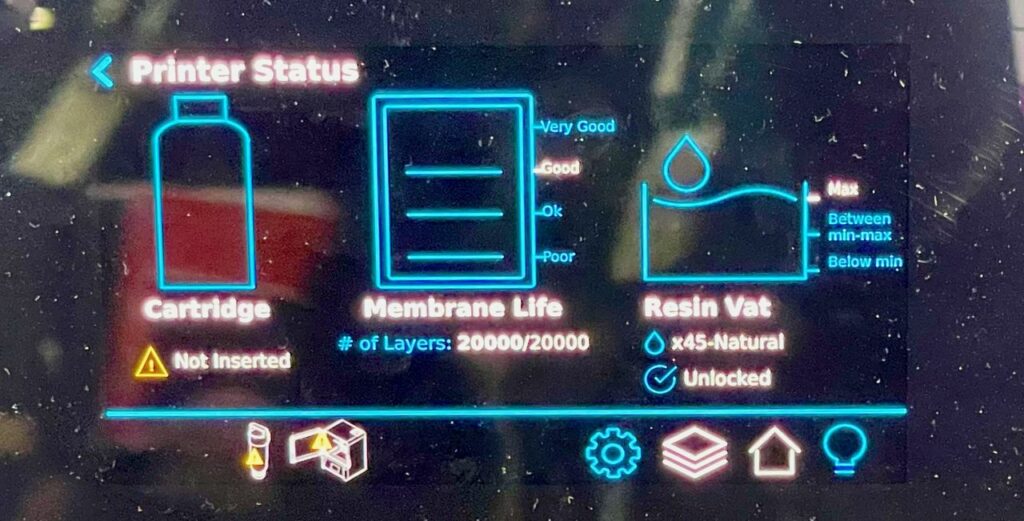
For example, the touch control panel offers visual cues to assist the operator.
The build plate can be operated with only one hand, which is a notable achievement. While I presume it could save you half your cost of nitrile gloves, it also demonstrates the simplicity of the system and the thought that’s gone into the XiP design.
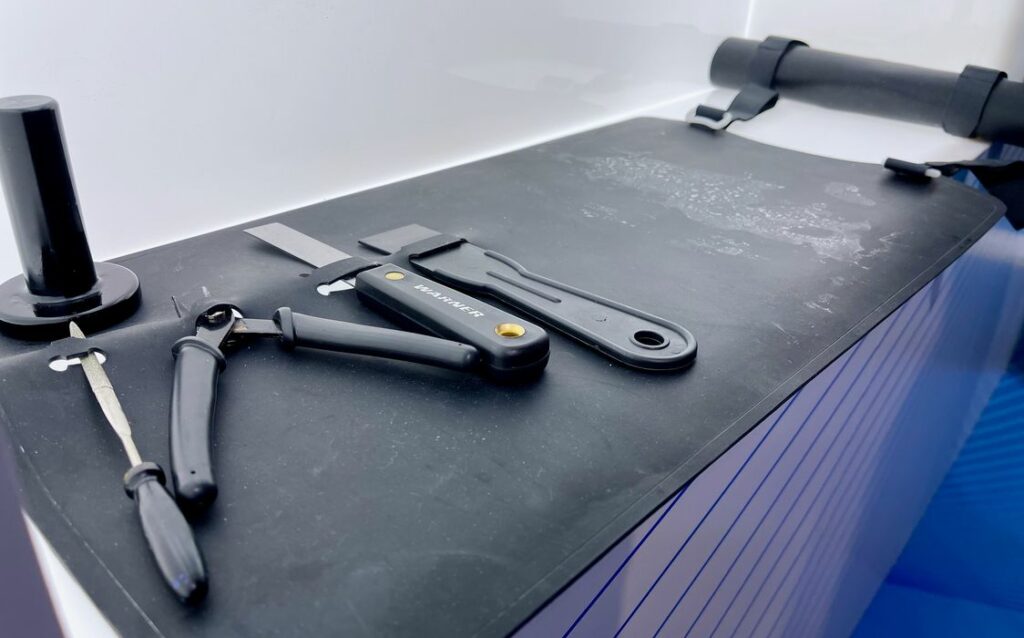
The XiP includes a complete tool kit for handling the prints and machine, located in an easy-to-use roll up system.
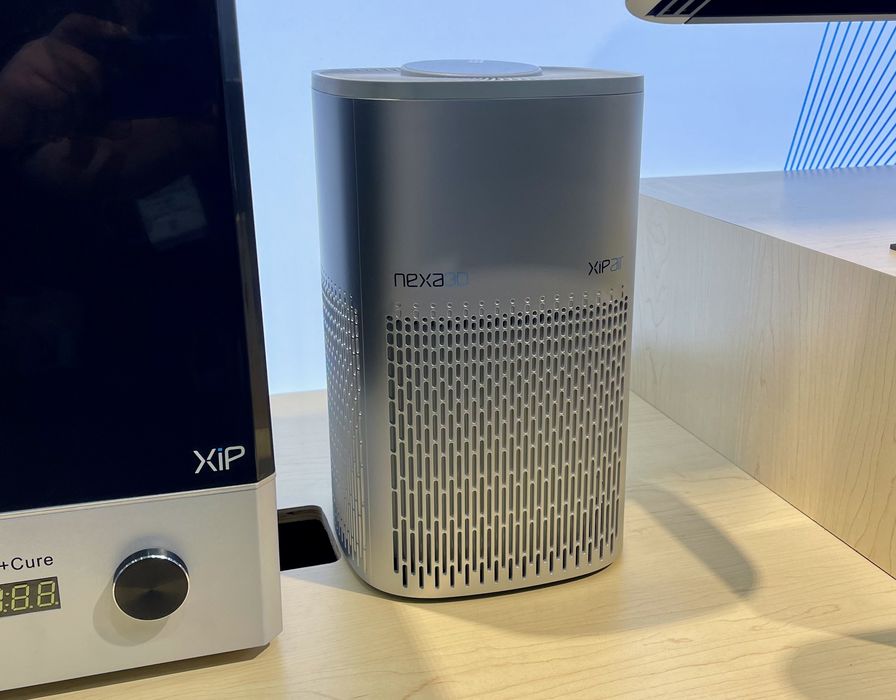
There is an accessory unit, the XiPAir, that effectively absorbs any emissions from the XiP, and an intelligent post processing accessory to “smart cure” parts.
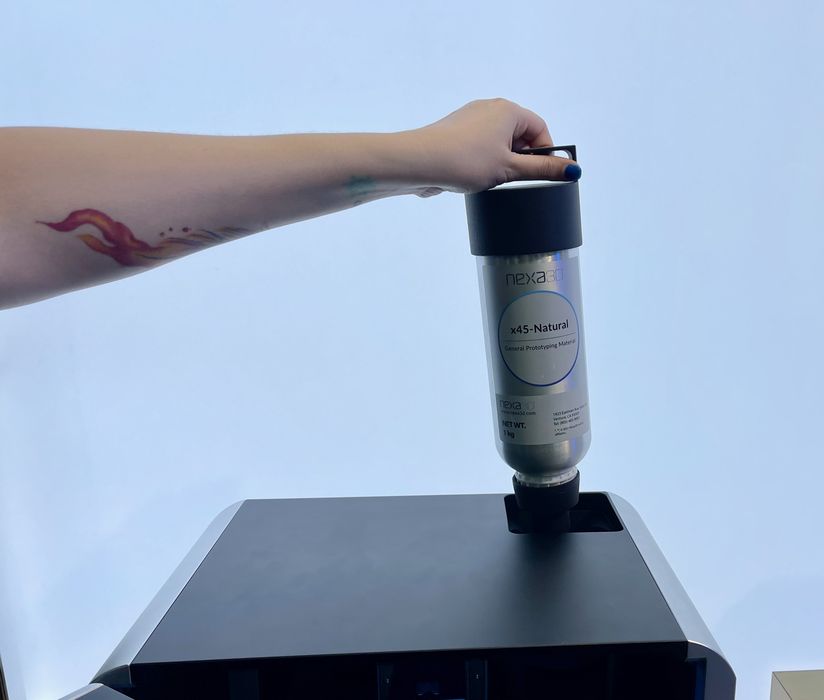
The XiP also includes a unique resin handling system that is basically immune to spills. This is a very important factor for those operating a small resin 3D printer, as most machines at that build volume can create toxic resin messes. It’s these features that could persuade a hesitant buyer to adopt 3D printing with Nexa3D technology.
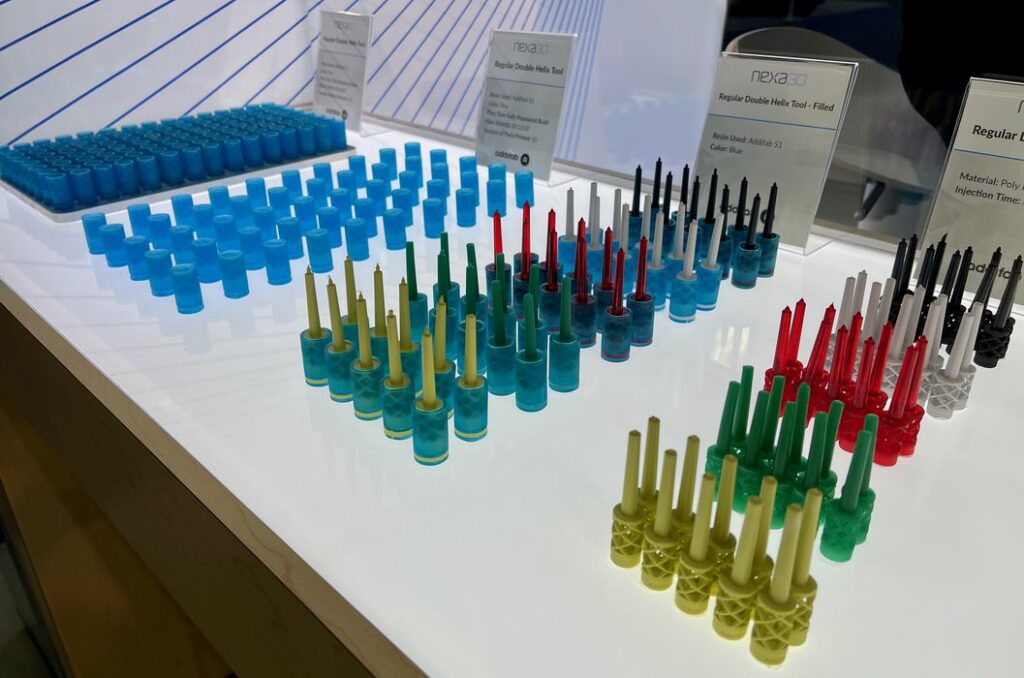
If that wasn’t enough, they’ve also partnered with Addifab to provide yet another process: injection molding. That might seem to be a bizarre technology for a 3D printing operation, but hear me out.
Addifab offers highly specialized resins that can be used to create functional injection molds by dissolving it after injection. They call this the “Freeform Injection Molding Process”, and it is available for use on the Nexa3D equipment.
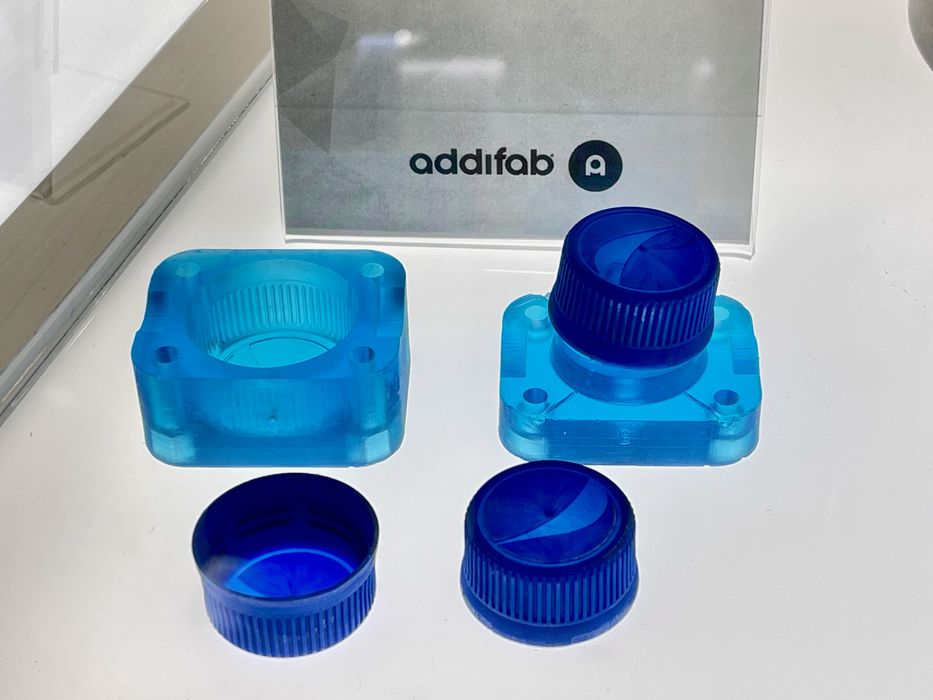
The advantage of this process is that highly complex molds can be created that are not subject to the usual injection molding geometry constraints. It is also able to produce usable molds in far faster time than one would normally expect when using traditional injection molding solutions. Finally, the process can use almost any standard injection molding material, which offers significantly greater material choice over 3D print materials.
Putting all these processes together enables more complex solutions. As an example, Nexa3D built a highly complex helmet art piece, The Nexarator as a demonstration of this capability, which we selected as our Design of the Week.
From modest beginnings as a resin 3D printer manufacturer, Nexa3D has very quickly branched out into several other processes, making a pretty compelling line up for manufacturers to consider. I suspect they will continue to expand their product set in the future.
Via Nexa3D