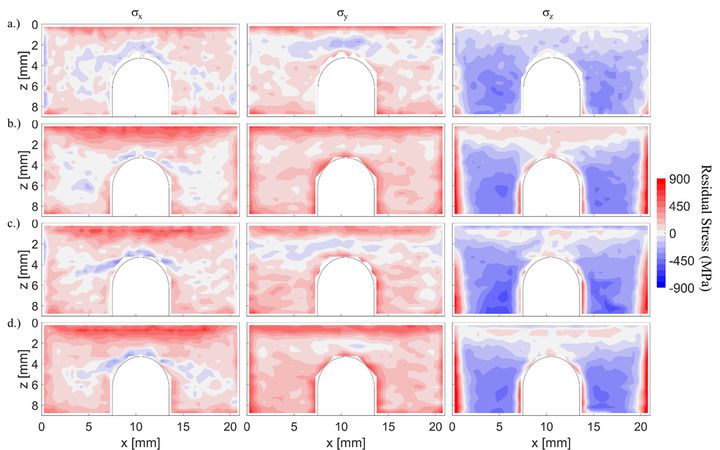
The US NIST has developed a technique for measuring mechanical stress in 3D printed metal parts that could change how 3D printing is done.
Metal 3D printing is one of the more complex disciplines in the industry, and one reason for that is due to the use of durable metal parts for production. These end-use parts must survive in a variety of mechanical environments and therefore must meet specified quality standards.
However, producing high-quality metal 3D prints is a difficult business, mostly due to thermal issues.
The most popular metal 3D printing process is the well-known LPBF process, in which powerful lasers selectively melt fine metal powder on a flat bed, layer-by-layer to gradually build up an object.
The issues start with the heat required to perform that melting. Unlike polymer 3D printing, where temperatures required range from 180C to 400C, metal 3D printing requires much higher heat.
With that added heat comes thermal expansion and shrinkage as metal material cools. Unfortunately this heating and cooling occurs during and after the print job, and encompasses the entire geometry of the part.
Of interest to NIST researchers was the effect of these thermal conditions experienced at the atomic level of 3D prints.
They understood that after a layer is produced by extreme heating, the material rapidly cools. By the time the subsequent layer on top of the first layer begins melting, we have a situation where there is hot on top and cold elsewhere. Thatās never good.
The cooling metal shrinks, and pulls on the still-warm expanded metal material, introducing stress. This micro-stress can be built up over the entire 3D print, meaning the overall strength of the print can be compromised.
To counteract this some 3D printer manufacturers have used whatās called an āisland approachā. In this method the layer is segmented into āislandsā, which are printed serially. In theory, because the islands are each being printed faster than raster scanning, they would lose less heat and thus be less susceptible to the stress problem.
The NIST researchers wanted to see if this was in fact true, and they were able to measure the stress effect in a very interesting way.
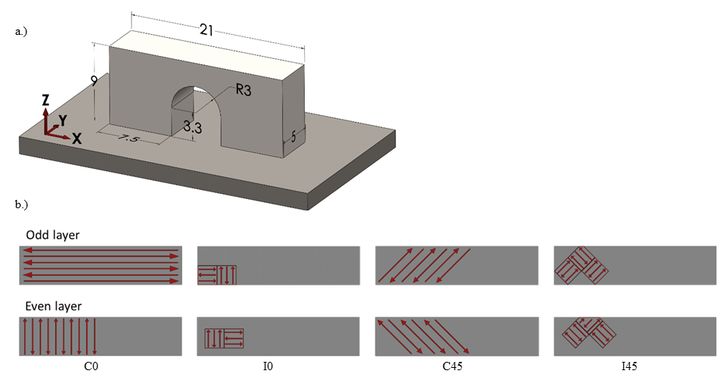
They blasted high-energy X-rays into metal test prints and measured the wavelengths reflected back. By using some calculations, this enabled them to determine āwith high accuracyā the actual distance between atoms in the sample.
The idea is that if the distance between atoms is greater, than the stress is higher. Thus, they were able to accurately measure residual mechanical stress in metal 3D printed parts.
What did they find after testing a variety of commonly used metal 3D printing patterns? Researcher Thien Phan explained:
āThis was very surprising and underscores the complexity of the problem. It shows that, although island scanning may work in many cases, it did not work in ours, which really highlights the fact that we need to have accurate modeling.ā
Evidently while the center of the islands had less stress, the surfaces did not.
While this is simply a research study, it seems to me that a more extensive use of the approach could enable development of much more sophisticated metal 3D printing patterns that could minimize the residual stress effect. Perhaps this method could be commercialized in the future, and that would likely be done by an existing metal 3D printer manufacturer.
Via NIST