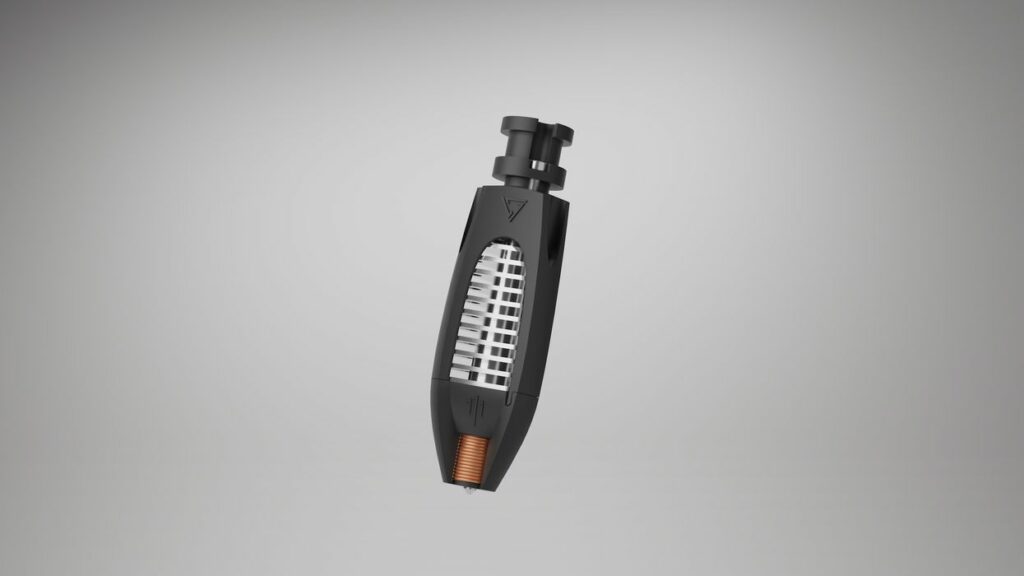
Plasmics launched a hot end with an entirely new heating concept: induction.
Plasmics is an Austrian startup company that launched only four years ago. Since then theyāve been secretly developing their induction technology, and only this week introduced the product via a Kickstarter campaign.
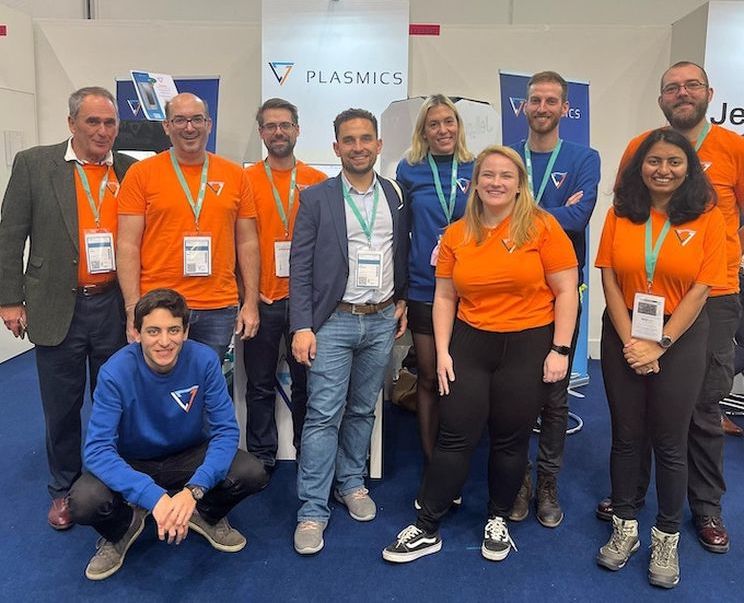
There are plenty of hot ends on the FFF 3D printing market, but they all have one common concept: resistance heating. Electricity is applied, and the heat is generated by resistance. This heat eventually flows through the entire heater block, and hopefully to the nozzle.
I say āeventuallyā, because the process of heating can take some time. Itās expected that FFF 3D printer heat times can exceed several minutes if starting cold.
Plasmics hopes to change all that with their new induction system.
Hold on, what exactly is āinductionā?
Induction heating is an electromagnetic process that generates heat in conductive materials, like metals. The metal is exposed to an electromagnet that is charged with a high frequency AC current, which causes electrons to flow inside the metal. These in turn generate heat through resistive effects. The degree of heating can be precisely controlled through moderation of the input energy.
The big advantage to induction heating is that the heat appears first inside the metal object, and does not have to penetrate and flow through the metal object. This means the heat is generated much more quickly.
The most common use of induction heating is found in the kitchen, where special stovetops include these electromagnets, which quickly heat suitable metal pans and pots.
Plasmics has taken this heating concept to the 3D printer hot end.
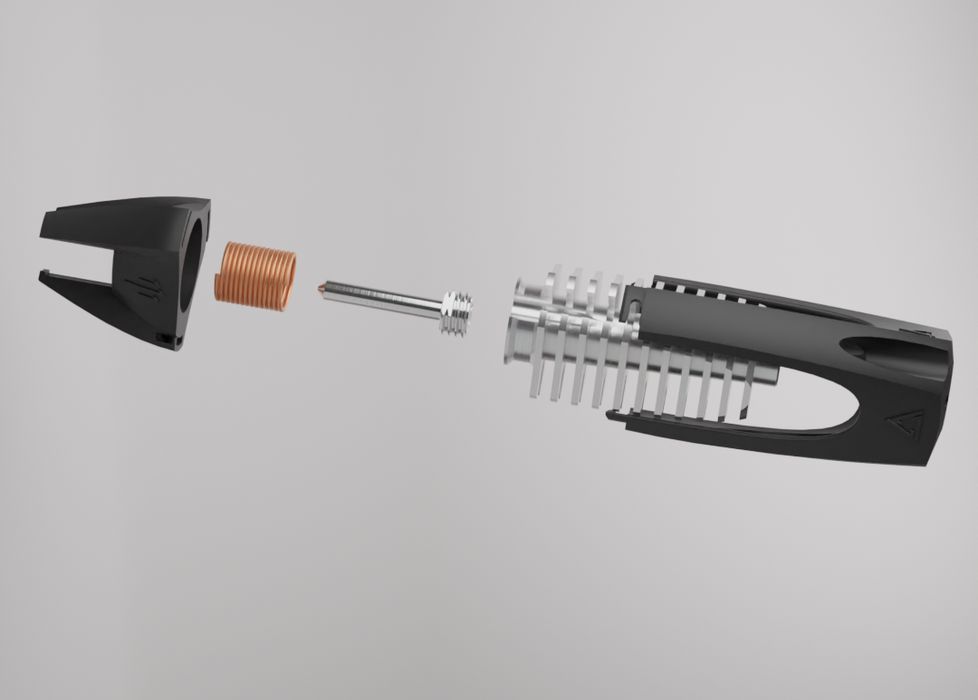
As you can see in this exploded image, the new INo Trident hot end includes a coil that surrounds the metal tube thatās actually heating. The coil provides the oscillating magnetic field. Thereās also the usual cooling fins to remove heat from the ācold zoneā.
Of particular interest is the extremely small size of the hot zone. There is NO bulky heater block! This means the INo Trident is extremely lightweight.
Like all induction heating systems, the INo Trident will heat up very fast ā partly due to the much smaller size of the hot endās metal parts, and secondly due to the use of inductive technology. This means a FFF 3D printer using this hot end will have minimal delays when starting up the 3D printer. In this chart you can see that the INo Trident heats up to 250C in only EIGHT SECONDS! Cooldown is similarly rapid.
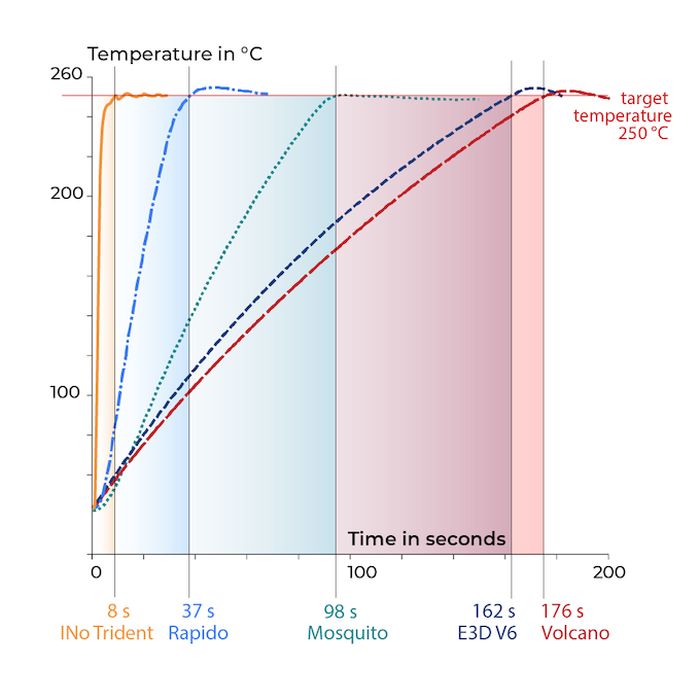
Thereās a very interesting side effect from the ability to āinstantlyā heat up a hot end. If you happened to deploy this technology on a multimaterial 3D printer with several toolheads, there would be no need to wait while switching materials for reheating. Alternatively, there would be no need for keeping all toolheads at temperature (and dripping out wasted material).
Thereās more. The light weight means the toolhead on the FFF 3D printer will carry far less momentum when moving, enabling the 3D printer to raise print speeds considerably. What speed, exactly? Well, that depends on the specific 3D printer using the INo Trident.
One more very surprising fact on the INo Trident is that apparently it DOES NOT REQUIRE A COOLING FAN! Plasmics explains:
āIt can run without a nozzle cooling fan and is manufactured out of lightweight materials.ā
This is quite notable, because typical FFF 3D printer hot ends require two fans: One to cool down the freshly extruded material, and the second to maintain the cool zone and ensure heat doesnāt creep up from the hot end.
Evidently the precise thermal controls enabled by the use of induction heating means heat creep canāt occur as easily and thus no fan is required. Since the metal part is so small there is no āup and downā oscillation of the temperature as is often found with resistive hot ends: no overshooting! The elimination of the cooling fan further reduces weight and thus could increase print speed even more.
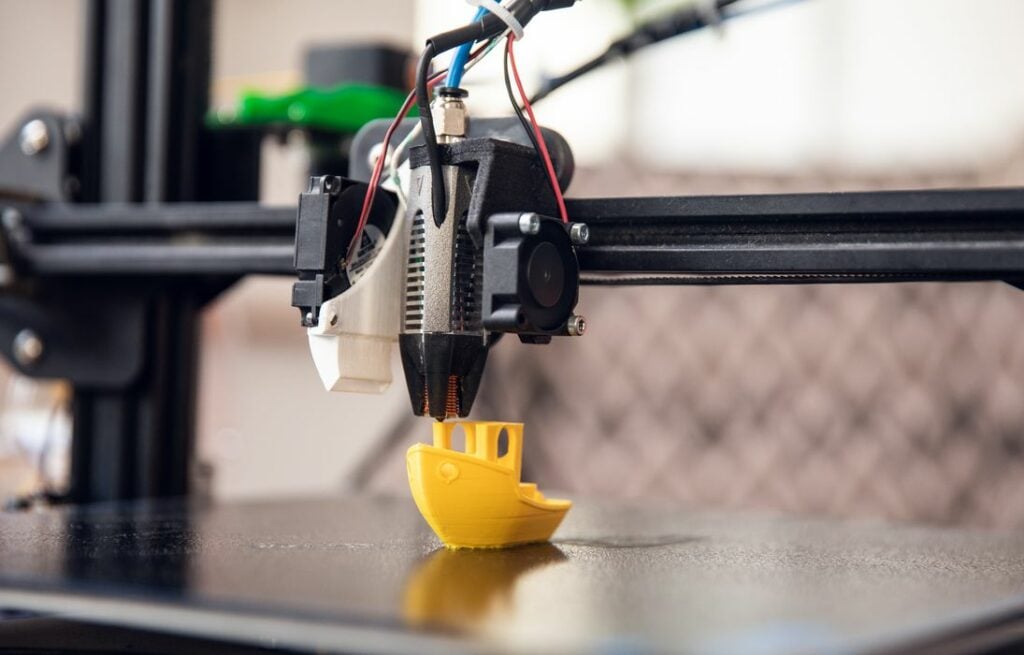
Finally, Plasmics has made the nozzle from hardened tool steel, which enables the component to 3D print difficult composite materials like carbon fiber-reinforced filaments, or high temperature materials like ULTEM.
Note that Plasmics is selling a hardware component here, not an entire 3D printer. Thus the INo Trident is, at this moment, targeted at DIY folks willing to install the hardware into an existing system.
Plasmics said the INo Trident requires a Raspberry Pi controller running the Klipper firmware (which can also provide high speed operations). They also require a 24V power supply. Evidently they are working on integrating with the more commonly used Marlin firmware, and even Duet, but they are not yet ready.
The one catch on this item is the price. The āearly birdā price on Kickstarter is a whopping ā¬319 (US$313), which while high is close to the price of a super-high-end conventional hot end.
Iām extremely impressed with this development, as it is likely the single most interesting development of FFF technology in many years. The availability of this technology will certainly change how 3D printers are designed, made, used and maintained long into the future.
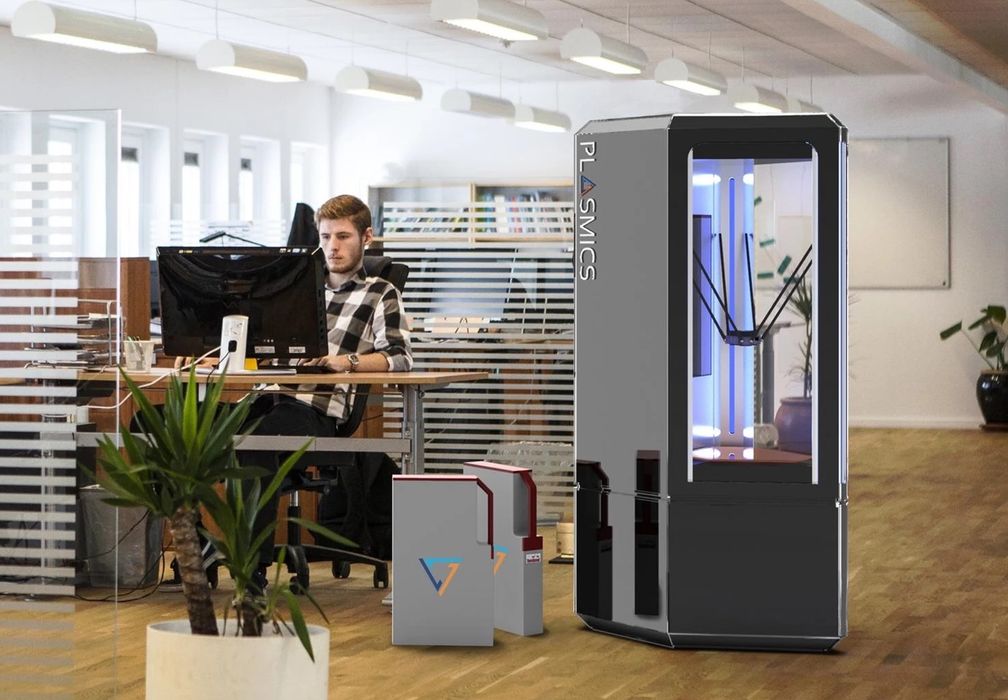
I expect that leading 3D printer manufacturers will strike deals with Plasmics to incorporate or license this amazing technology into their 3D printers, and Plasmics will release their own 3D printer as well.
All hail induction!
Via Plasmics and Kickstarter