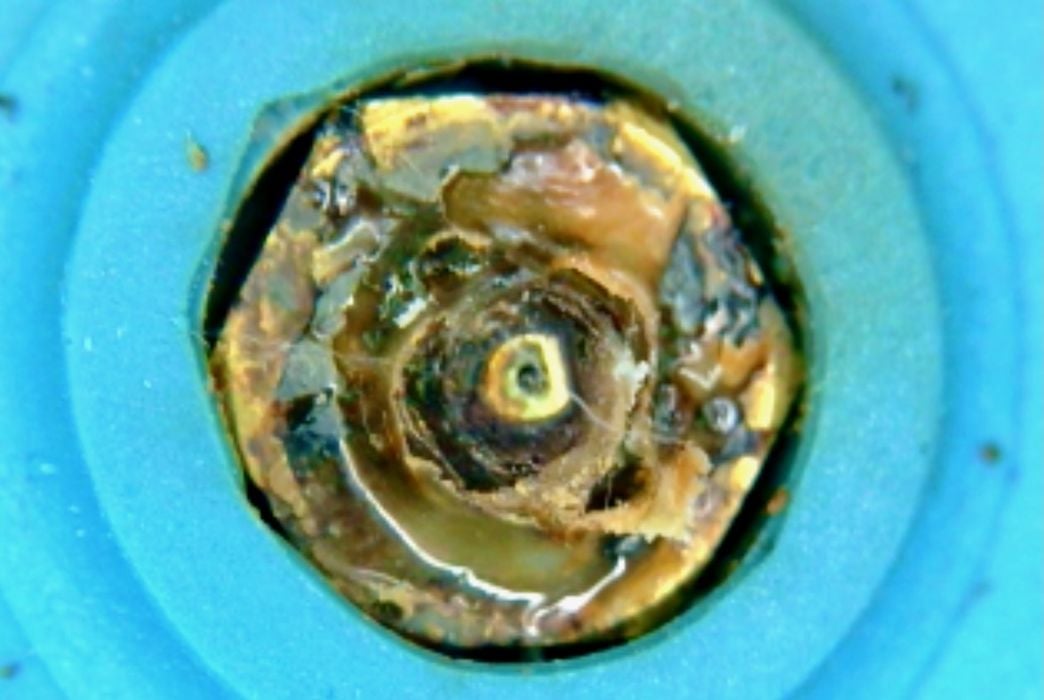
Let’s talk about nozzle wear on FFF 3D printers.
Nozzle wear wasn’t really much of an issue unless you were involved in notable engineering work to develop strong mechanical parts. Nowadays that’s changing.
Materials that are pure polymers, such as PETG, PLA, ABS, etc., flow easily through hot end nozzles on FFF devices. The nozzles, typically made from brass, are easily able to handle these materials and don’t really wear down much. It’s unlikely you would replace a nozzle if you’re using those materials during the typical 2-3 lifetime of a desktop 3D printer.
However, this state of affairs might be changing. The cost of machines capable of handling stronger engineering materials continues to drop, and we’re now finding these machines in more places.
A good example of this is the Creality K1C, a device we recently reviewed. This device retails for only US$499, making it accessible to a huge number of people.
The “C” in the product’s name indicates it is capable of handling stronger materials, including carbon-reinforced materials. In fact, Creality makes and ships a PLA-CF composite material for the K1C.
But what makes a machine capable of handling these stronger materials? What’s actually going on?
The idea is to mix a harder material with a softer material to increase its strength. This is commonly done, and one example you use everyday is concrete: it’s a mix of gravel and cement, where the hard gravel adds strength.
In a similar way this is done with 3D printer filaments, except instead of gravel we have short chopped fibers, typically made of glass or carbon fiber. Like gravel, they make the filaments far stronger than the polymer equivalent.
These fibers make the parts stronger, but also can wreak havoc on your nozzle. Why? Because the fibers are harder than the brass material making up the nozzle. Polymers like PLA, ABS, etc., are softer than brass, so they just pass through. But the harder fibers can cause erosion. Any filaments that contain harder particles can cause erosion, including not only fiber-reinforced materials, but also filaments like glow-in-the-dark, which include some harder components.

Let’s take a look at how this works. Above you can see a cross-section of a 3D printer nozzle. The softened polymer is pushed from the top down, exiting the nozzle. The nozzle is typically 0.4mm wide, resulting in a precision extrusion of that width.

Here we’ve introduced a fiber-reinforced material, possibly PA-CF or even Creality’s PLA-CF. Inside the softened polymer are thousands of tiny short carbon fibers. These float around in random orientations. These fibers must be quite a bit smaller than the diameter of the nozzle, otherwise they would instantly clog.

The polymer flows as before, but look what happens: some of the fibers impact on the inner edge of the nozzle. Because carbon fibers are harder than brass, erosion slowly takes place.

This is the result: the erosion gradually causes this portion of the nozzle to widen. It may not be uniform, but the larger nozzle aperture allows more material to flow — and that is definitely not what your slicing parameters expected. In other words, the machine extrudes more material than it should. This can cause blobs, drips, etc., and wreck print quality.

If that’s wasn’t bad enough, there’s something else that happens. Here we see the CF material being printed, and at the bottom is the ongoing print layer. As you can see, there are carbon fibers in that print — that’s why you’re using this material. However, some of the fibers stick up and impact the nozzle as it travels around the layer. Normally impacts with plain polymer are inconsequential, but here the fibers start eroding the nozzle.

This is in fact worse than the other erosion because not only is the nozzle wider, it’s also a bit shorter than it was before. This means the Z-gap is changing, requiring recalibration.
The solution to all this is to use a “hardened” nozzle, which is typically the key change on “C” machines. These nozzles can be made of different materials that are harder than brass, such as tool steel, titanium or even ruby. The problem is that carbon fibers are one of the hardest materials, and you’ll see even steel nozzles wear out, just at a slower rate than brass nozzles.
How fast they wear out depends on how much material is being printed, and the nozzle’s material. With a brass nozzle I would not be surprised if you destroyed a nozzle with only two spools of CF material. Hardened nozzles would last much longer.
Fortunately, it’s not only possible to buy “hardened” 3D printers. You can also upgrade almost any 3D printer by installing a hardened nozzle, which are available at relatively low cost — unless you go for the more exotic hardened nozzles. I would do that only if I intended to print a large amount of engineering material frequently.
If you have reinforced filament in your workshop, make sure your nozzles are hardened.