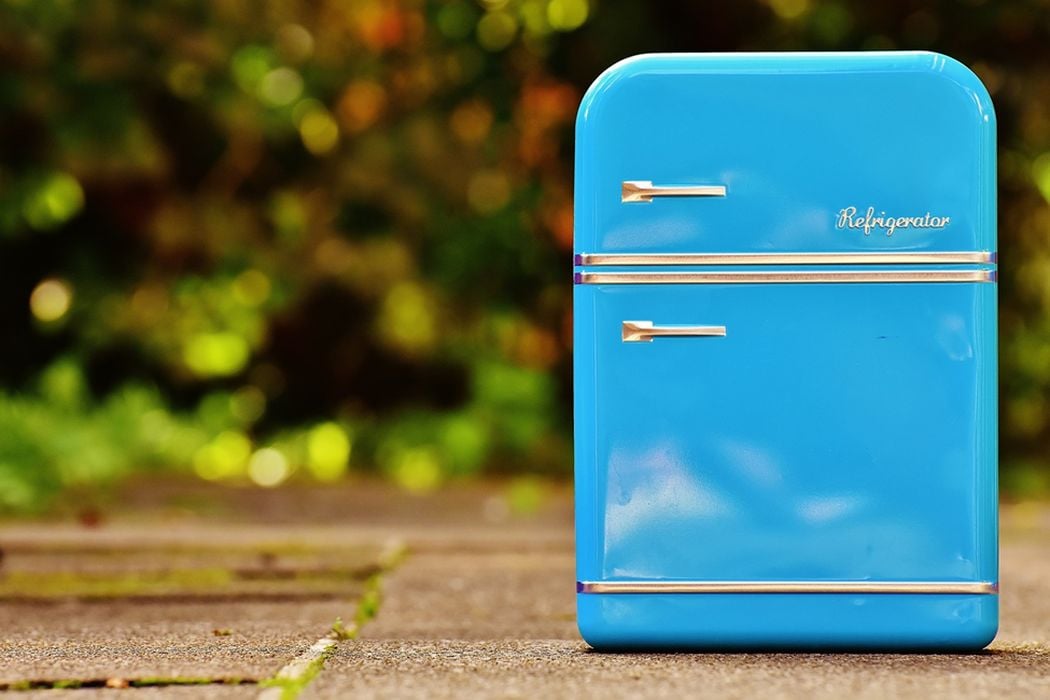
Charles R. Goulding and Preeti Sulibhavi explore the transformative shifts in the appliance industry, from recalls to sustainable innovations.
The appliance industry is undergoing significant changes, marked by recalls, innovations, and a push toward sustainability. The recent recall of 380,000 Frigidaire refrigerators by Electrolux, Whirlpool’s groundbreaking alternative to polyurethane foam for insulation, and the evolving landscape of appliance standards set by the Energy Department are a few recent developments.
Electrolux’s Frigidaire Recall: Navigating Challenges
Electrolux, the parent company of Frigidaire, faced a substantial challenge with the recall of 380,000 refrigerators.
Details of the recall, including the reasons and the steps taken by the company, are essential for consumers to understand the scope and implications of the issue.
Electrolux announced that it was issuing a recall for 380,000 Frigidaire and Electrolux brand refrigerators sold. The recall was initiated after the company received reports of degradation of certain plastic parts.
To address the issue, Electrolux stated it would:
Offer free in-home repairs to affected consumers; provide consumers with a refund if they no longer had the refrigerator and did not wish to have it repaired; reimburse consumers for any food loss resulting from the refrigerator issue, up to a certain amount per household; and, set up a dedicated customer support hotline and website to handle inquiries and reimbursement requests
The recall and customer reimbursement program is expected to cost Electrolux millions. The company stated that by issuing the voluntary recall, it aims to address the refrigerator issue proactively and maintain the safety, quality standards and trust associated with its Frigidaire brand.
Whirlpool’s Sustainable Innovation in Refrigerator and Freezer Insulation
Facing growing concerns over the environmental impact of polyurethane foam insulation used in appliances, Whirlpool announced in late 2023 a new sustainability initiative to utilize an innovative insulation alternative across its refrigerator and freezer product lines.
The company unveiled that it has developed a proprietary insulation material made from recycled plastic bottles and natural plant-based fibers including bamboo and hemp. Through an exclusive partnership with insulation startup EcoDome Materials, Whirlpool will leverage this petroleum-free and recyclable insulation dubbed EcoLite.
Compared to traditional polyurethane foams, EcoLite provides markedly better insulation performance and efficiency ratings across standardized industry tests. Refrigerators outfitted with 3 inches of EcoLite tested up to 18% more efficient than the same models using polyurethane, while freezers saw efficiency gains of over 20%. This improved insulation helps Whirlpool refrigeration units significantly reduce electricity consumption and operating costs.
The move to EcoLite also provides substantial sustainability advantages. Over 90% of the insulation’s weight comes from recycled or plant-based materials. By using PET plastic from discarded bottles during manufacturing, each refrigerator helps recycle approximately 7,200 plastic bottles out of landfills or oceans. The natural fibers allow EcoLite to fully biodegrade at end-of-life without releasing toxic microplastics.
Whirlpool confirmed that starting in January 2024, its entire North American refrigerator and freezer portfolio will utilize EcoLite insulation as the new standard. Thanks to the improved efficiency, Whirlpool estimates this transition will eliminate over 12,500 metric tons of carbon dioxide emissions annually as the units reach customers’ homes. The sustainability and performance advantages of this insulation innovation solidify Whirlpoolās commitment to responsible, cutting-edge refrigeration technology.
Industry-wide Standards: New Rules by the Energy Department
Manufacturers are advocating for a new timeline on standards for dryers, stoves, and dishwashers, reflecting the industry’s response to evolving energy efficiency demands.
A detailed examination of the proposed changes and their implications for both manufacturers and consumers is crucial.
The Energy Department’s plan to implement new rules over the next three years will significantly impact the design and functionality of appliances.
Specific examples, such as improvements in refrigerator compressors, advanced temperature controls in dryers, and enhanced motors and pumps in dishwashers, highlight the industry’s commitment to energy efficiency.
The Role of 3D Printing in Appliance Design and Development
3D printing, has become a transformative force in refrigerator and freezer product development and production over the last several years. As the technology has evolved, major appliance makers like Whirlpool and Electrolux have integrated 3D printing in various facets of their operations.
Whirlpool appears keen on leveraging 3D printing’s sustainability potential to align with its corporate responsibility goals. The company uses industrial 3D printers to manufacture prototypes of innovative insulating materials, like the EcoLite insulation it recently adopted. By optimizing the insulation’s form and composition during the design phase, Whirlpool can maximize efficiency while keeping development costs low. 3D printing also allows any last minute adjustments to ensure the insulation seamlessly integrates during full appliance assembly.
In 2021, Whirlpool began outsourcing batches of small plastic components, like air vents and condenser covers, to 3D printing specialist Carbon. The digitization of these parts’ supply chain helps Whirlpool accelerate production schedules and reduces part lead times by over 60%. Their partnership also makes the components trackable using blockchain technology to verify ethical sourcing.
Electrolux is increasingly adopting 3D printing following its recalls of Frigidaire refrigeration units for quality issues. By bringing more prototyping and tooling in-house with industrial printers, Electrolux aims to identify performance problems earlier while optimizing ergonomics and ease of repairs.
Additionally, Electrolux sees additive technology’s low-volume production capacity as an opportunity to address supply chain strains. Recently, the company began 3D printing over 50 types of plastic parts to assemble specialty appliances and quick-ship refrigerator model configurations. By mitigating sourcing and logistics challenges, Electrolux can minimize production bottlenecks during periods of atypical market demand.
The investments into additive manufacturing by the two appliance industry leaders showcase 3D printing’s ascending value with its versatility in sustainability, production agility and quality assurance. As the capabilities grow alongside adoption, the coming years will see rapid expansion of the technology into nearly all facets of refrigerator and freezer unit design..
Conclusion
In an era of technological advancements and increased emphasis on sustainability, the appliance industry is at the forefront of innovation and change. From recalls and alternatives to polyurethane foam to evolving energy standards and the integration of 3D printing, companies like Electrolux and Whirlpool are navigating challenges while pushing the boundaries of what’s possible. As consumers become more conscious of the environmental impact of appliances, the industry’s response through innovative materials, manufacturing techniques, and adherence to energy efficiency standards becomes increasingly critical.