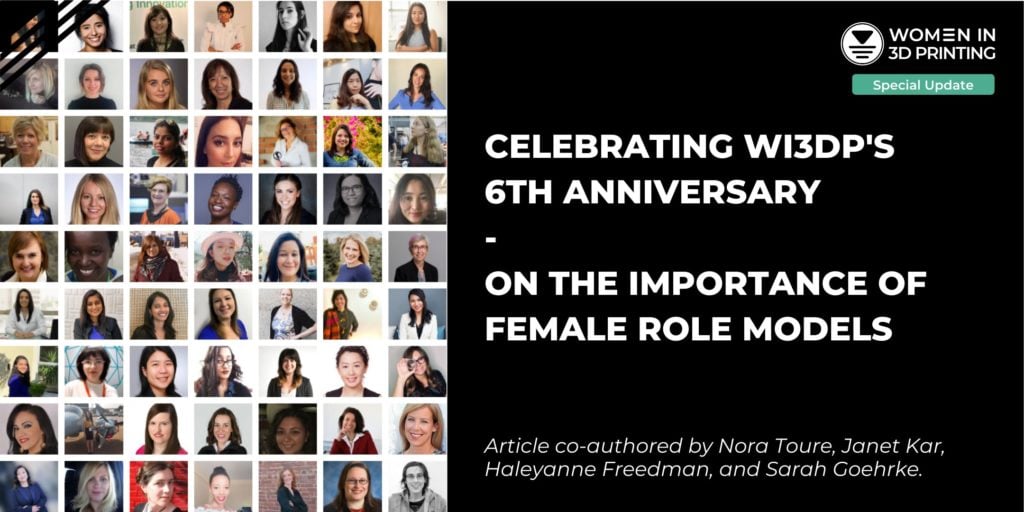
“You can’t be what you can’t see.”
You’ve probably heard that statement before. Whether you agree or not with Marie C. Wilson, I think we can all recognize that “If you can see her, you can be her”. I grew up with my parents telling me that ‘anything one person can do, good or bad, another human being is capable of accomplishing the same’. Meaning, I can do it too, good or bad. So, if I wanted to become an astronaut, like Sally Ride or Valentina Tereshkova, in theory, there shouldn’t be any reason I couldn’t do that.
It’s one thing for your parents to tell you this, but it’s another thing to actually experience it firsthand. In August 1996, I turned 8 and witnessed Claudie Haigneré become the very first French female astronaut to journey into space. And that was it. My parents were right; yes, if I wanted to, I could become an astronaut. I too could go to space. I never did, of course, because I never truly wanted to become one, but the concept still applies to women everywhere.
Why am I sharing the story about me not becoming an astronaut?
Because today, we are facing a widening skills gap especially, in the United States and Europe. If not solved, manufacturers may strain their workers, resulting in higher turnover, lower-quality output, and potentially loss in profit causing them to lose their competitive edge, which affects local economies. Deloitte estimates put the labor shortage at potentially 2.8 million by 2028. Time is ticking, the current workforce is aging, and there aren’t enough qualified applicants to replace them. And whenever there’s an economic crisis, like the COVID-19 pandemic we’re currently facing, manufacturers and their workforce suffer in large numbers, and that is terrifying.
Everything around us heavily relies on the usage of hardware. From the smartphones in our hands to the shoes on our feet, to theLyft rides getting us from A to Z. Our constant demand for personalized experiences, and new and improved products requires manufacturing advancements for our ability to exist in modern society and improve our overall quality of life. The workforce and industry demands are there, yet the worker shortage still exists.
There are a few ways to look at this problem: reduce the number of employees required to operate on-site by way of automation, or hire more people. However, even the implementation of automation requires skilled labor. Engineers, operators, programmers: they’re all still completely necessary.
So how do we fix it? How do we inspire our workforce to pursue careers in manufacturing? According to Deloitte, in 2016, women totaled about 47% of the US labor force — but only accounted for 29% of the manufacturing workforce. Moreover, one of the largest challenges to the Additive Manufacturing industry is the lack of skilled workers to drive technology adoption.
Importantly, estimates point to women comprising a notable minority of the 3D printing workforce. Women only account for barely 11% of women in the additive manufacturing workforce according to this year’s Sculpteo State of 3D Printing report. Such findings are mirrored throughout the additive manufacturing industry, with Alexander Daniels Global’s Salary Survey indicating just 13% women in this workforce.
We have been working on understanding such figures through our own Diversity for Additive Manufacturing reports. Data collected from such industry studies have informed our understanding of what’s needed. We continue to work with companies in this industry toward actionable steps forward to a more equitable future, but it remains a long road ahead.
These statistics have only seen marginal changes within the past decade and only an 8% increase in the last 100 years. So why is female participation in manufacturing growing at such an embarrassingly low rate? Why aren’t we looking towards women to fill these workforce gaps? From the way I see things, it’s because society is failing to inspire young women and build an inclusive environment for them.
Read the rest at Women in 3D Printing