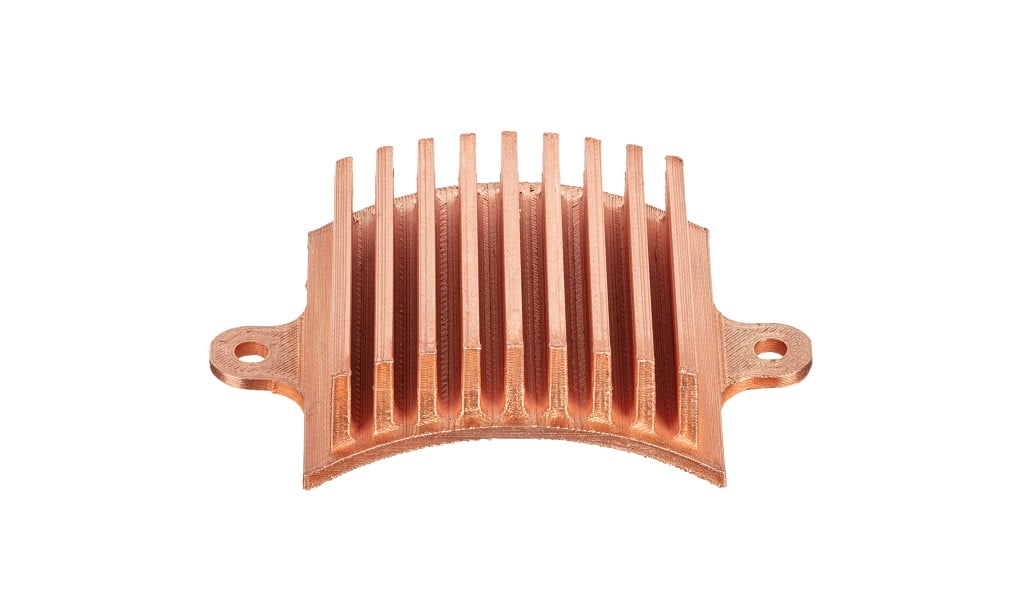
3D printing of certain reflective metals is a difficult challenge for some processes.
The LPBF process (Laser Powder Bed Fusion) is perhaps the most popular among manufacturers of metal 3D printers. It is a process that can produce high resolution, high quality metal parts by fusing fine metal powder with powerful lasers. It is somewhat scalable and has been certified for use in multiple regulated industries.
But itās not all roses and daffodils; there are many challenges with the LPBF process, not the least of which is that it is quite expensive. It requires expensive printers, materials and support staff. It requires expensive post processing equipment and a carefully designed facility to avoid contamination or explosion.
For this reason the use of LPBF has largely been relegated to industries where parts were already expensive, such as automotive, healthcare and aerospace.
Beyond the issue of cost, thereās another issue: reflective materials, and this issue is present in any metal 3D printing process using lasers to melt material, including DED (Directed Energy Deposition), an alternative to LPBF.
Typical LPBF and DED materials are steels, nickel, titanium and alloys thereof. You typically do not see aluminum or copper mentioned as materials for these systems.
This is because they are considered āreflectiveā. In other words, while the laser is able to melt them to produce a part, a portion of the beam is reflected off the material surface. This implies that higher power is required to do the melting, but also more reflectivity is generated.
Where exactly does this reflected energy go?
It hits parts of the 3D printer itself, including the laser apparatus. Because it is so energetic, there is a possibility of damaging or reducing the lifecycle of the 3D printer. Thatās definitely not good.
As a result, reflective materials donāt often appear on the list of suitable materials for LPBF metal 3D printers. This is quite unfortunate, as the use of copper, for example, would be exceedingly useful for many industrial parts, such as heat exchangers or antennae. We are bullish on copper in 3D printing.
However, there are some approaches where ingenious methods do allow the use of some reflective materials:
- Spee3D blasts metal powder at supersonic speeds to fuse metal objects
- Several binder jet systems can 3D print copper by sintering green parts after printing
- Xact Metal can 3D print copper because their optical train engineered to protect from the reflections
- Desktop Metal can 3D print copper using an extrusion technique on their Studio System
- Some DED systems are designed to avoid reflections, allowing 3D printing of some reflective metals
There are ways to produce reflective metal objects with 3D printing, but they may be with processes other than LPBF and DED.