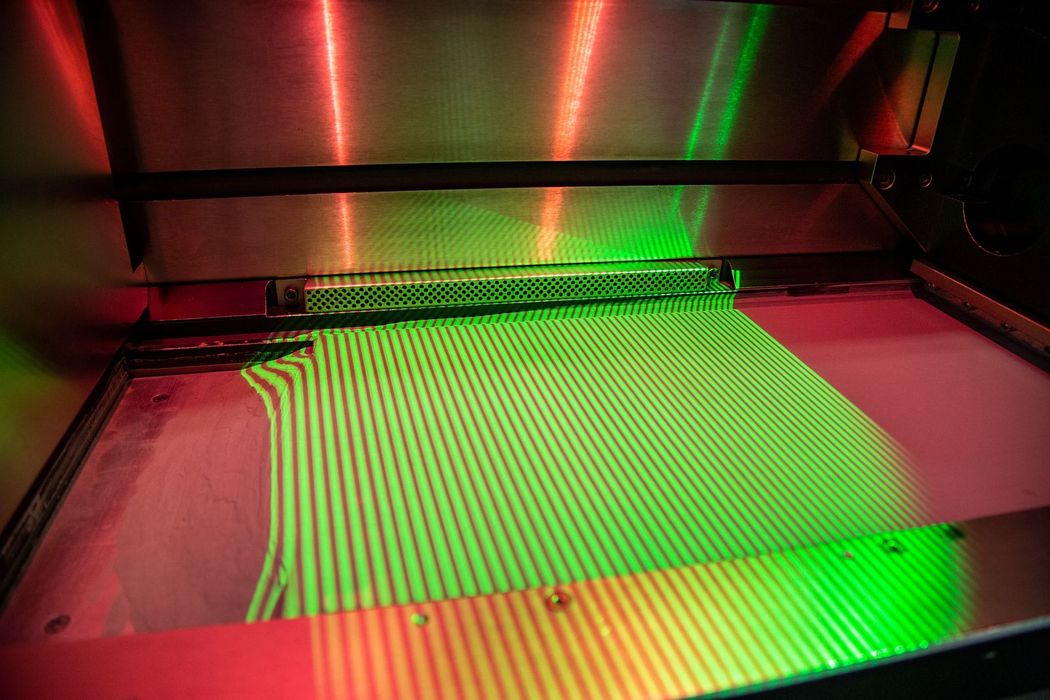
Phase3D announced a new feature in their Fringe monitoring system that can measure powder bed material in microns — in real time.
The Chicago startup company produces a system called “Fringe”, which provides extensive monitoring of almost any metal powder-based 3D printing system. The system involves attaching a special unit inside the build chamber that scans the activity using a structured light approach.
Powder-based 3D printing systems using the LPBF process are suitable for Fringe. This process deposits a thin layer of fresh powder on each printing cycle. The structured light scanner is then able to take a quick capture of the state of the layer and compare it to what should be happening.
If anomalies are detected, the operator is immediately notified. At that point the operator can make a decision on whether to abort the job.
This is quite important, as powder tends to be expensive. A failed print is not only wasted powder, but also wasted time: print jobs are not quick, and re-running a job takes away time from other jobs waiting to run. Cancelling failed jobs early is the most efficient way to handle these situations.
Phase3D provides not only notification of an anomaly, but also does so in numeric form: the operator can then judge how “bad” the situation can be, and make a more informed decision.
Last week Phase3D announced a new feature for Fringe: “True Layer Thickness”. They explain:
“This toolkit measures the quantity, in microns, of metal powder spread across the build area, certifying uniform distribution for every layer of every build. The innovation sets a new standard in inspection for metal powder bed fusion (PBF), providing a new in-situ monitoring toolkit for production scale AM.”
The quality of the part significantly depends on the uniformity of the fresh powder spread on each new layer. If there’s not enough material, then there may be gaps or weaknesses in those regions. If there’s too much powder, then print failures might occur. Either way, you want the correct amount of powder to succeed.
With True Layer Thickness, it’s possible to obtain the exact thickness of each layer, down to the micron level. That provides a significant amount of information about a given print job, and will assist in determination of whether a part meets quality standards.
Phase3D explains the three key aspects of True Layer Thickness:
- Objective Data – True Layer Thickness uses patented Fringe in-situ monitoring technology to create quantifiable measurements, in microns, of how much powder is spread during the metal PBF process.
- Precision and Consistency – This toolkit ensures precise inspection of the amount of deposited metal powder for every layer of every build.
- Industrial Solutions – Tailored to the challenges of industrial manufacturing, True Layer Thickness addresses the requirements for industrial applications beyond aerospace including defense, energy, medical, and more.
You can see that they’ve tuned “TLT” quite precisely for specific industrial applications that often require quality certifications.
With solutions as intricate as Fringe, I’m now wondering about the metal 3D printing operations of the past, and how little information was then available to make quality assessments. It seems that the future is all about leveraging data to ensure parts of all of the required quality.
Via Phase3D