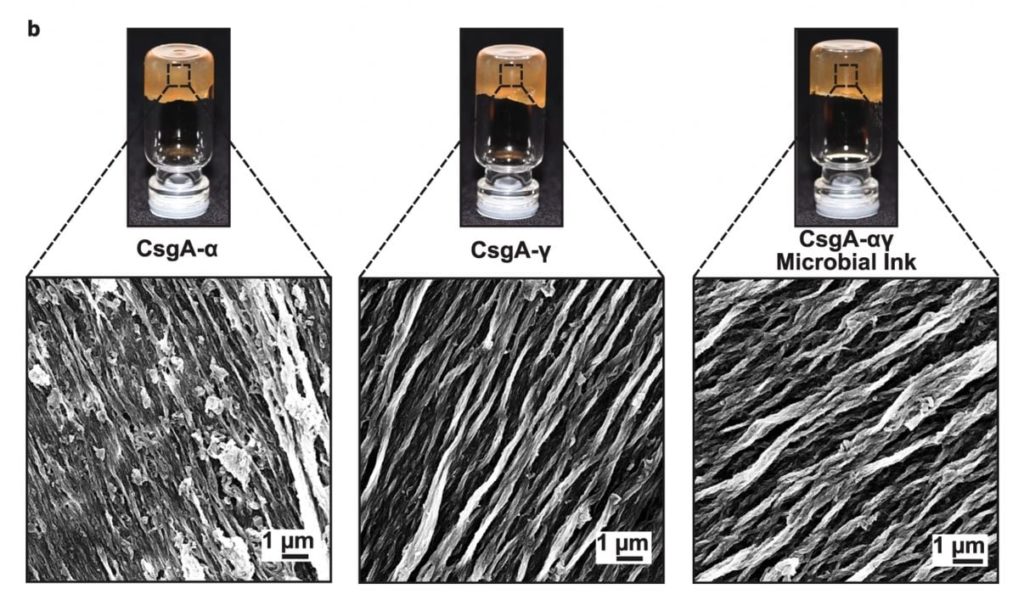
Researchers have developed an incredible new technique for producing material for bioprinters, and it may revolutionize other forms of 3D printing.
The work starts with challenges facing todayâs bioprinting technology. Bioprinting typically involves extruding living cells through a syringe-like extruder to form a shape. After extrusion, the cells live as they normally do, and hopefully join together to form whatever structure was intended.
Sometimes the geometry of the biostructure requires some assistance. This is done by 3D printing âscaffoldsâ of an alternate material in the desired shape. The living cells, which normally have very limited structural capabilities, adhere to the scaffold and then grow from there. Eventually, the scaffold dissolves and hopefully you have the bio structure in the correct geometry.
All this says is that cell material is typically terrible as a building material, yet for biostructures it is absolutely required. How can this paradox be solved?
The researchers undertook a rather unusual approach for solving the dilemma: they produced what they call âprogrammable microbesâ.
Basically they genetically engineered the well-known E.Coli bacteria to produce a bioink that provides the necessary properties. These are described as:
- Design an extrudable bioink that had high print fidelity
- Produce the bioink entirely from engineered microbes by a bottom-up approach
- Create a programmable platform that would enable advanced functions for the macroscopic 3D living architectures
They explain their approach:
âA printable bioink requires a viscosity low enough to facilitate extrusion, but high enough to retain its shape after printing2. In this regard, shear-thinning hydrogels, which decrease their viscosity with increasing shear stress, are an attractive option. Moreover, it should be noted that bioinks are biocompatible materials typically meant to recapitulate an extracellular matrix (ECM) to provide a congenial environment for the growth of living cells with predefined structures and functions. We envisioned that instead of embedding microbes in an ECM-mimicking bioink, we could repurpose the ECM of the microbial biofilm itself to serve as a programmable bioink.â
The researchers were successfully able to re-engineer E.Coli to produce nano fibers using a complex design process. You can see an example of the resulting material at top.
The sample bioink was tested using standard bioprinters, and found to work successfully.
This is a notable development, and not just for bioprinting. Consider this: these researchers were able to persuade a bacteria to produce a 3D printable material. While their experiment used the resulting material for bioprinting, I can easily imagine alternative materials be developed for other forms of 3D printing.
Todayâs mechanical 3D printing environment typically uses composite materials, such as chopped carbon fiber mixed with a base material. These creates a much stronger material for 3D printing.
Imagine bacteria programmed to produce sustainable fibers used for composite materials, or perhaps even creating the entire composite material simply through bacterial action. A 3D printing workshop might have a large tub at the back âgrowingâ 3D print material for use, much like bakers have dough rising overnight.
I canât be certain if this is literally possible, but I can say that the notion of programmable bacteria-produced materials is exciting and could lead to an entirely new field of 3D print materials research.
Via Nature