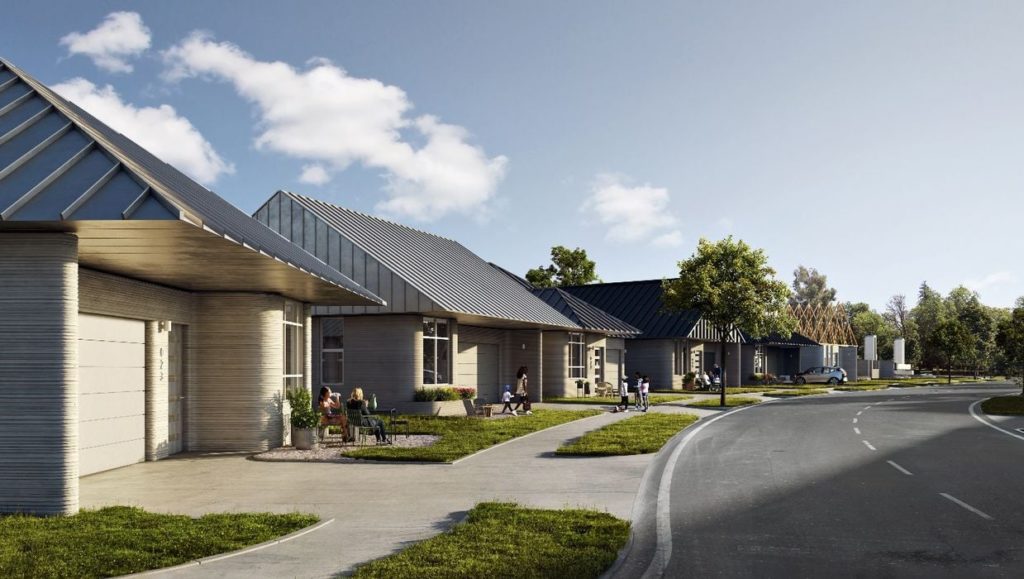
Could 3D printing really be used to solve the global housing crisis? Recent breakthroughs in the technology show we might not be that far off.
When the idea of 3D printing began picking up steam over a decade ago, it conjured up images and thoughts of futuristic buildings and products materializing out of thin air much like a picture being printed from a webpage. It was a widely held belief that 3D printing technologies would quickly revolutionize the construction, engineering and manufacturing industries, but it has been a slow road to develop 3D printing’s potential, especially as a modern construction technique. To date, 3D printing, or more specifically, additive manufacturing, has more quickly taken hold in the manufacturing industry for rapid prototyping and tool production.
As a widely used technology, 3D printing is still in its infancy, and innovators continue to flock to the space. Since its inception, 3D printing has consistently been viewed as a potential means to solve the global housing crisis and provide shelter for millions of homeless or struggling people all over the world. The world continues to deal with a two-pronged housing crisis, with rising home prices, overcrowding in major cities and a general shortage of affordable, structurally sound homes in developing parts of the world. More than 75 percent of markets in the United States experienced double-digit increases in single-family home prices over the past year, and that trend extends to all corners of the globe. Housing remains one of the largest and most important problems facing humanity.
Housing is a near-impossible problem to solve considering how many factors go into fixing its myriad issues, ranging from policy decisions at the highest levels of government, material and labor shortages, shifting demographics and demand, and where housing is actually needed. Even with all of the political and economic headwinds fueling the housing shortage, 3D printing remains an attractive solution. The ability to erect safe, sturdy dwellings in under a day that provide the minimum requirements for human shelter would go a long way to alleviate poverty in the developing world or create affordable neighborhoods in the most attractive cities where space is at a premium.
Early attempts at 3D printing structures have left something to be desired—not much more than glorified, featureless boxes or pavilions. These types of dwellings, which can be whirled out in under 24 hours for close to $10,000, might do in a pinch for building emergency housing or shelter for the homeless but do not offer the type of space desired by the masses. Real breakthroughs in 3D printing of buildings will come when entire neighborhoods full of desirable homes can be built.
After years of trying, it appears that breakthrough is close.
Watershed Moments in Texas
Austin, Tex., one of the hottest housing markets in the United States, is becoming a sort of proving ground for 3D-printed homes. The city is on the rise and beginning to rival Silicon Valley in terms of tech talent. Austin-based company ICON has already built several stunning homes with partner 3Strands and is teaming up with construction powerhouse Lennar to build an entire neighborhood of 3D-printed homes.
“Fundamentally, our country’s housing crisis is a supply issue,” said Gary O’Dell, 3Strands CEO. “3Strands is working to solve this by pushing the boundaries of new technologies that address root causes of this supply issue. By 3D printing these homes, East 17th Street is a significant advancement for the future of construction. We have been overwhelmed by initial buyer demand and could not be more pleased with how ICON has delivered beautiful, energy-efficient and resilient homes.”
The progress made in 3D printing homes is quite stunning. These are not the drab, featureless, cave-like dwellings produced by the earliest attempts. These are Architectural Digest -worthy living spaces complete with solar panels, bright spaces and energy-efficient systems. In its partnership with Lennar, ICON looks set to go even further and produce homes at a neighborhood scale.
ICON and Lennar plan to build 100 homes up to 3,000 square feet with photovoltaic panels on the roofs. ICON will handle the majority of construction, with Lennar providing the finishing touches, such as windows, flooring and fixtures. The homes will be constructed using ICON’s Vulcan robotic printer and its proprietary Lavacrete, which is a mixture of Portland cement and the company’s special additives that facilitate 3D printing.
ICON’s Vulcan is an impressive piece of machinery, measuring over 46 feet long and 15 feet high. It works in tandem with the company’s digital platform, which delivers plans and instructions and works intuitively with real-time data from the field. Materials for printing are delivered by the Magma system that mixes concrete based on current site weather conditions and feeds the printer.
“Construction-scale 3D printing not only delivers higher-quality homes faster and more affordably, but fleets of printers can change the way that entire communities are built for the better,” said Jason Ballard, ICON CEO. “The United States faces a deficit of approximately 5 million new homes, so there is a profound need to swiftly increase supply without compromising quality, beauty or sustainability, and that is exactly the strength of our technology.”
3D Printing for Prefab Homes
Prefabricated homes, or prefab for short, are another favored solution to the housing crunch. The major components of a prefab home are constructed offsite and then transported and erected on-site, accelerating the construction schedule, reducing material and waste and simplifying the construction process. This is another perfect application for 3D printing, where walls and panels can be printed. California-based Mighty Buildings has pioneered a 3D printing system to construct stunning prefabricated homes.
The panels used by Mighty Buildings have numerous advantages over traditional prefabricated systems. Mighty Buildings produces all of its panels in its factory before delivering to the construction site, cutting down on labor time and costs. The panels themselves are made of the company’s proprietary non-silicate Light Stone Material that hardens rapidly under ultraviolet light, which cuts down on carbon emissions by eliminating the use of typical concrete cement. A home built from these 3D-printed panels saves approximately 2.3 tons of CO 2 emissions, according to Mighty Buildings. The company has a goal to get its carbon footprint to net zero by 2028.
Read more at ENGINEERING.com