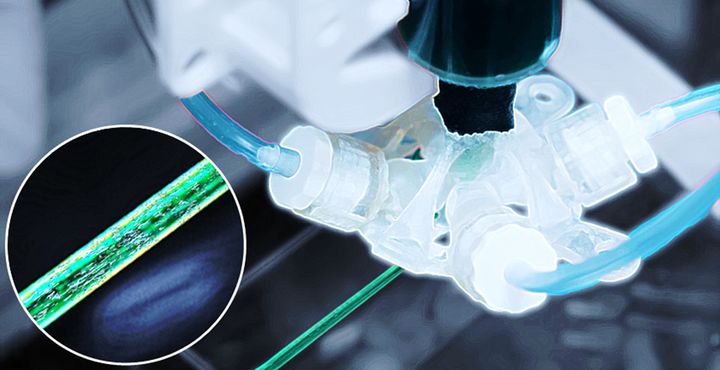
Researchers have developed an unusual “morphing nozzle” that can orient fibers during 3D printing.
The goal of much research is to determine methods of increasing the strength of 3D prints. Typically 3D prints are less strong than equivalent parts made from injection molding simply because the prints have been made with layers of material rather than an integrated solid.
One way to make FFF extrusions strong is to mix in small fibers of much stronger material with the standard polymer. On the market today you’ll find a number of these options, frequently including chopped carbon fiber segments. You can’t extrude pure carbon fiber, but you can if it’s mixed with an extrudable polymer like nylon.
But there’s another issue: the fibers are chopped and so they provide only a limited amount of strength. They emerge from the nozzle in different orientations, and it’s only by chance they provide additional strength as they may line up against encountered forces later.
If only the fibers were oriented in a controlled manner they could provide far greater strength. Some equipment, like that from Markforged or Anisoprint, offer the ability to 3D print continuous carbon fiber, but really they are simply adding a continuous string of fiber alongside normal 3D printing.
While actual continuous carbon fiber is incredibly strong, it might be possible to approach that level of strength if the chopped fibers were aligned. Fortify has determined a way to orient fibers in their fiber-reinforced DLP 3D printing technology, but doing the same in FFF offers a different challenge.
Now there seems to be a new approach for orienting these extruded fibers, which would offer much greater strength. Researchers have developed a special “morphing nozzle”, which can alter its shape to align the fibers as they pass through the hot end and nozzle.
How do they do this? It’s quite interesting. They said:
“Specifically, the nozzle comprises flexible bladders that can be inflated pneumatically to alter the geometry of the material extrusion channel from a straight to a converging–diverging configuration, and in turn, the directional orientation of fibers within printed filaments.”
Basically they are squeezing the material flow to force the fibers to rotate into the desired alignment, just before extrusion. It’s an amazing idea.
I have some thoughts about this.
If you were to orient the fibers to be parallel to the extrusion flow, that would be quite an achievement. However, it also means that the strength of the part would lie along the extrusion lines. These extrusions necessarily move about the 3D model in a path generated to produce the desired shape, which is not necessarily meeting the mechanical stress requirements.
It’s not clear whether the morphing nozzle can orient fibers in other directions, but if so, then we have some very interesting possibilities. The fibers could continually re-align as needed during extrusion paths to provide the right orientation for strength throughout the part.
However, the weak point will still be the layer interfaces that will depend on the relatively weak polymers holding it together.
Via Wiley and University of Maryland