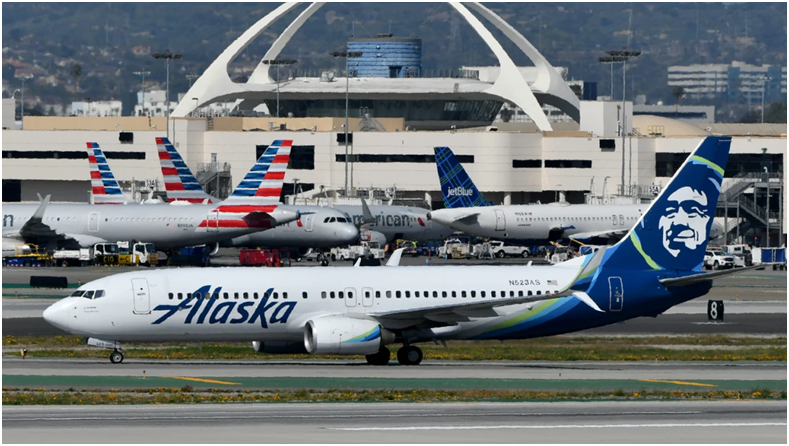
Charles R. Goulding and Ryan Donley consider the rising use of aerospace 3D printing as newer aircraft prepare to enter fleets.
Passenger airplane carriers are confronting the probable post-pandemic reality that they are going to need fewer planes for the foreseeable future. This aspect becomes especially prevalent as older aircraft models are much more difficult to implant advanced technology, such as HEPA air filters, which are already implemented on all modern aircraft, making them relevant as COVID-19 rages on. The industry had already accelerated the retirement of the older portion of its fleets which were originally slated to be phased out over the years however, a reduction in demand for air travel has been catalyzing for permanently grounding older aircraft.
A list of some of the retiring aircraft includes:
- Alaska Airlines – A320 Fleet, A319, A321 neo (Airbus models, 40+ aircraft total)
- American Airlines – A300, A330, Boeing 757s and 767s, Embraer E-190 (80+ aircraft total)
- Delta Airlines – McDonnell Douglas MD-88 and MD-90, Boeing 777s (191 aircraft total)
- JetBlue Airways – E190 (70+ aircraft)
- Southwest Airlines – Boeing 737-700s (170+ aircraft total)
- United Airlines – No final decisions, ER767-400s, Boeing 757-200s and 767s, A320 all in consideration for retirement (190+ aircraft total)
Phasing out older aircraft presents an opportunity to utilize new and up to date models that, in addition to removing older aircraft, could boost airline performances. Not only do new planes use less fuel and require fewer repair-related components, but new planes also have 3D printing topology optimized component configurations that have fewer subcomponents.
Earlier this month, Ryanair, Europe’s largest airline, placed a $22 billion order for 75 additional 737 Max jets from Boeing, by far the largest order for the problematic plane since it was grounded nearly two years ago. The oldest planes that will be retained will likely need enhancements, such as new seating solutions to achieve adequate social distancing as well as entertainment systems that today’s travelers now expect.
Pre-pandemic, airplane manufacturers and their Tier suppliers were some of the largest users of 3D printing for components. During the pandemic, applications for 3D printed airplane components have continued to improve, particularly with metal parts. The industry needs to monitor both of these trends because there will be a reduced need for investing in inventory stocks of conventionally made parts. Some major component manufacturers, including Raytheon, have indicated that they intend to substantially reduce their facility space post-pandemic. Pre-pandemic, the Tier suppliers primarily focused on new plane orders to forecast OEM orders and future component replacements. Our view is that they should also devote more time to prospective airplane retirements.
Boeing
Boeing has long been invested in additive manufacturing – since the early 1990s. The investments came about after Boeing had begun to fall behind on product delivery deadlines to customers requiring the company to shift to methodologies that would improve turnaround time, starting from the design phase to the final delivery phase. In particular, in 2018 Boeing invested in Digital Alloy, a metal additive manufacturing company, for $12.9 million to assist in manufacturing parts made from titanium and other hard metals. This investment marked Boeing’s fourth such investment after supporting Assembrix, Morf3D, and Oerlikon.
Boeing’s commitment to additive manufacturing has proved beneficial as they now have more than 60,000 3D printed parts currently in use for commercial, space and defense products. Parts such as cool air ducts with complex geometries, metal fuel nozzles, spare parts and many more.
Additive manufacturing has opened a breadth of possibilities for Boeing as they can complete more efficient design processes with design solutions never thought of in the past in addition to bringing products to market faster. The roll-out of Boeing 777X in early 2020 with more than 300 3D printed parts – particularly in the GE9X engines – is proof of the success resulting from the integration of additive manufacturing into their production processes.
Recently the Scottish government sought a large market share of Boeing components and is set to open a $15.16 million (USD) research and development program aligned with Boeing. This includes engineering equipment and a 60,000-square-foot facility exclusively utilized for additive manufacturing projects.
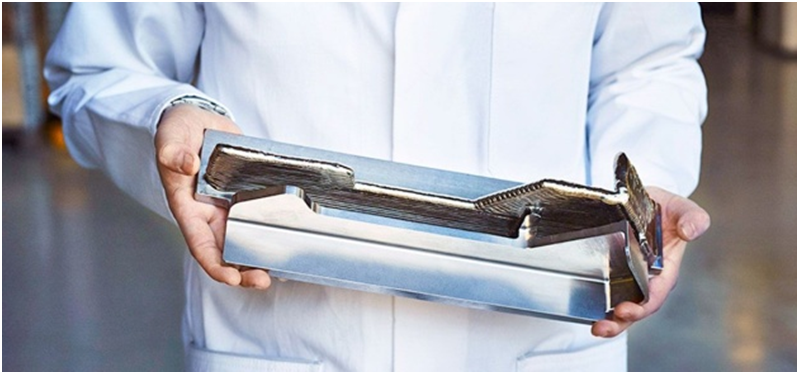
GE Aviation
GE Aviation is another company that is very active in the engagement of 3D printing technology applications for aircraft. In 2012, the company acquired Morris Technologies and Rapid Quality Manufacturing, acquisitions that expanded engineering and manufacturing capabilities for rapid prototyping and end-use production components. Shortly after, in April 2015, GE Aviation received its first FAA clearance to use a 3D printed part in a commercial jet engine. This was aided by a contract with Boeing to use the part in more than 400 GE90-94B engines on Boeing 777 jets. GE Aviation aims to produce over 30,000 complex metal parts using additive manufacturing that can expect to save up to 75% in production costs from material and labor costs, and design time.
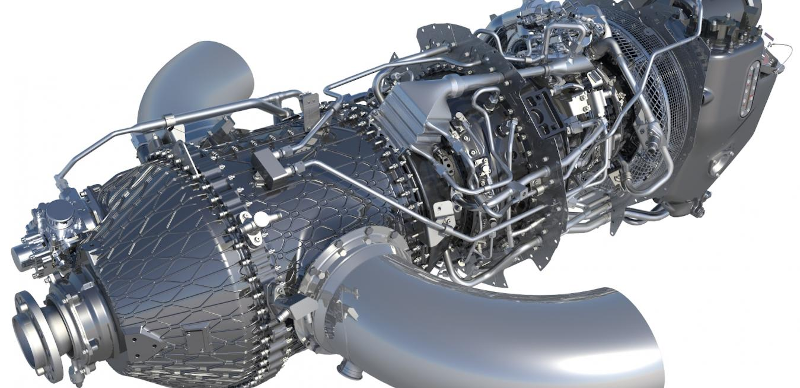
Manufacturers and suppliers utilizing additive manufacturing for aircraft may be eligible for R&D tax credits.
The Research & Development Tax Credit
Whether it’s used for creating and testing prototypes or for final production, 3D printing is a great indicator that R&D credit-eligible activities are taking place. Companies implementing this technology at any point should consider taking advantage of R&D Tax Credits.
Enacted in 1981, the now permanent Federal Research and Development (R&D) Tax Credit allows a credit that typically ranges from 4%-7% of eligible spending for new and improved products and processes. Qualified research must meet the following four criteria:
- Must be technological in nature
- Must be a component of the taxpayer’s business
- Must represent R&D in the experimental sense and generally includes all such costs related to the development or improvement of a product or process
- Must eliminate uncertainty through a process of experimentation that considers one or more alternatives
Eligible costs include US employee wages, cost of supplies consumed in the R&D process, cost of pre-production testing, US contract research expenses, and certain costs associated with developing a patent.
On December 18, 2015, President Obama signed the PATH Act, making the R&D Tax Credit permanent. Since 2016, the R&D credit can be used to offset Alternative Minimum Tax (AMT) or companies with revenue below $50MM and, startup businesses can obtain up to $250,000 per year in cash rebates that can be applied directly to payroll taxes.
Conclusion
Post-pandemic there should be a pent-up demand for new passenger airplanes. However, fewer overall planes are needed for the foreseeable future which should accelerate the retirement of older planes. The 3D printing industry has the opportunity to play a major role in assisting this transition.