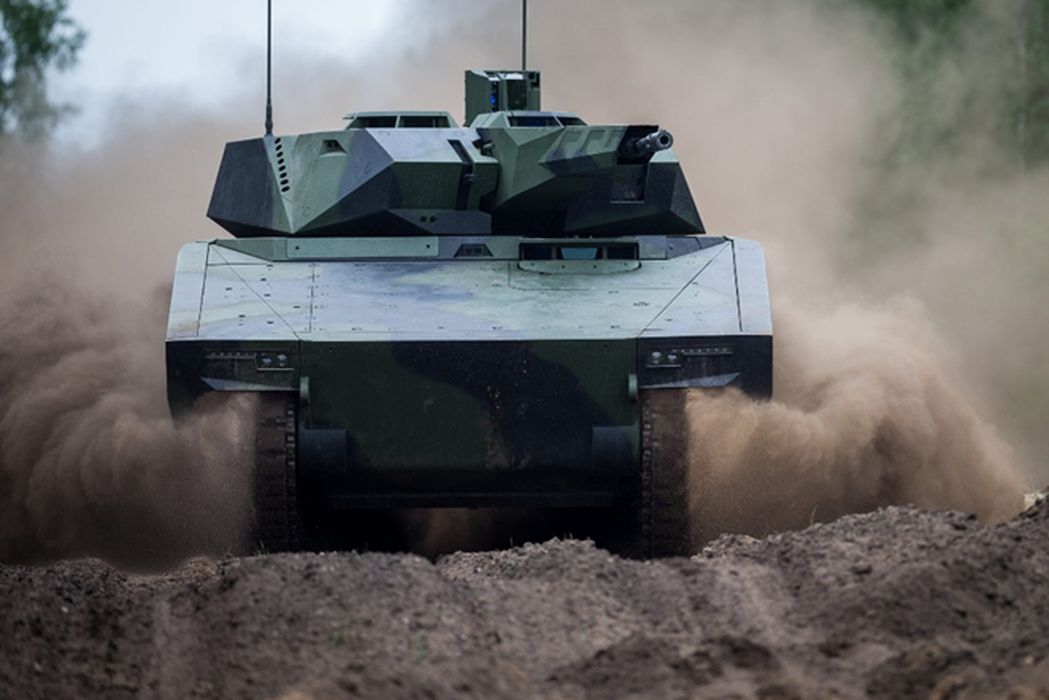
Charles R. Goulding and Preeti Sulibhavi explore how 3D printing has helped to propel Rheinmetall from a middle-sized defense contractor to a leading global defense contractor.
What a difference a war makes.
Before the Russo-Ukrainian War, Rheinmetall, headquartered in Germany, was a middle-sized defense contractor with modest growth rates.
Both the war and Germany’s new defense posture have transformed Rheinmetall into a leading, global defense contractor.
“We are grateful to be a dynamic partner to the German government – both in empowering the German armed forces in line with requirements and in supporting Ukraine. Our products allow us to provide the country with effective assistance in its defense struggle: Our supplies to Ukraine extend from air defense to main battle tanks and infantry fighting vehicles as well as the associated ammunition, from military trucks and sensors to mobile field hospitals.”
– Armin Papperger, CEO
Rheinmetall’s consolidated sales grew by around 7.6% to US$1.5 billion between quarter one 2022 and the same quarter 2023. The company employed 25,486 employees as of March 24, 2023. It is undergoing a vast expansion at the moment.
Rheinmetall is engaged in an impressive expansion program, including the following:
1) New tank and armament factory in the Ukraine. Several factories are producing military goods in Ukraine, and now Rheinmetall is one of them. The company plans to open a US$218 million battle tank factory on Ukrainian soil, capable of producing about 400 tanks a year.
Papperger said in 2023 that factory workers would build and repair Rheinmetall’s Fuchs armored personnel carrier in the manufacturing facility.
Rheinmetall will operate the plant in partnership with Ukroboronprom, a Ukrainian state-owned defense group, which will co-own the facility. In May, the companies announced an agreement to boost Ukraine’s “defense technology capacities.”
2) Lockheed’s F-35 Fuselage manufacturing facility in Weeze, Germany. Rheinmetall plans to build an ultramodern factory for fabricating fuselage sections for the F-35A multirole-combat aircraft at Weeze in western Germany. In collaboration with Northrop Grumman and Lockheed Martin, at least 400 fuselage sections are to be produced starting in 2025. The plant will employ 400 highly skilled workers.
Rheinmetall already has extensive 3D printing expertise.
For example, Rheinmetall continues to exploit the full capabilities of additive manufacturing and has incubated several 3D printing startups under its consolidated group to continually increase development, especially in military and vehicle applications.
Solidteq is one of the companies that emerged from Rheinmetall and has been applying 3D printing for rapid prototyping up to the production of small series of components. Continually leveraging 3D printing has led Rheinmetall to believe that they can seriously consider 3D printing as an alternative to, or in conjunction with, traditional manufacturing.
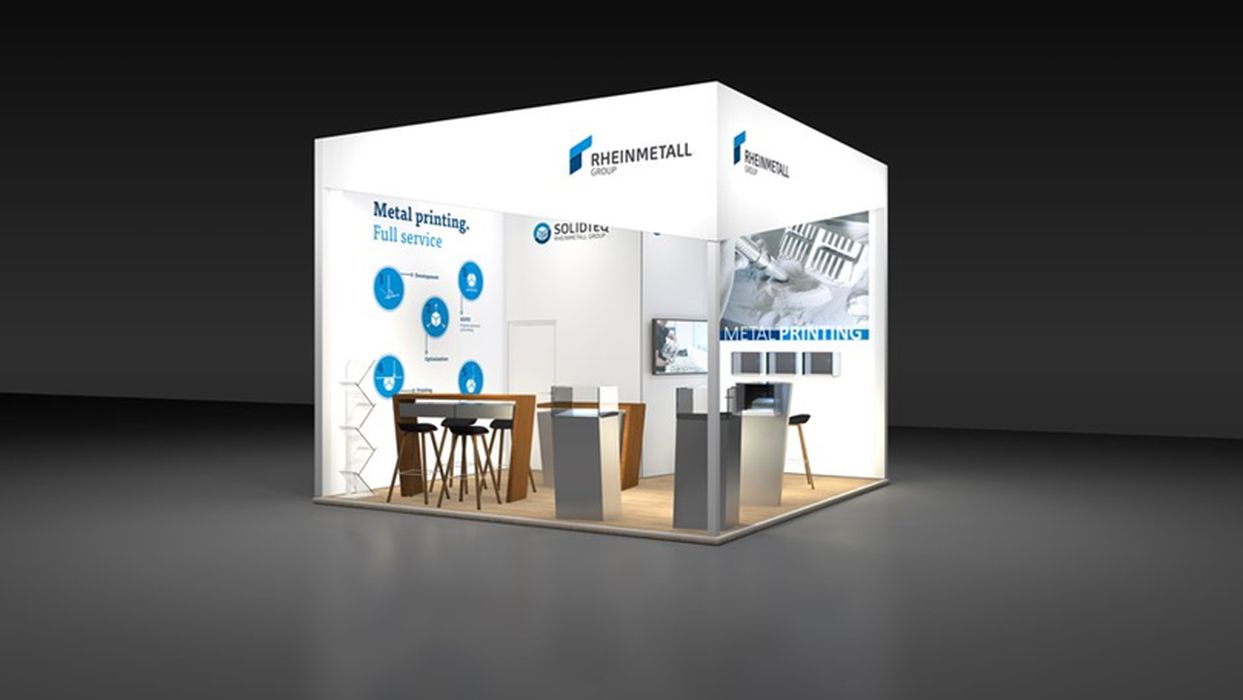
In Australia, Formero (previously GoProto ANZ), an Australian 3D printing and manufacturing service bureau, announced the successful delivery of locally printed 3D products to Rheinmetall Defense Australia (RDA) as part of its Land 400 Phase 3 offer to Australia. Formero is the first Melbourne-based 3D printing provider to work with RDA and provide critical products for its “LYNX KF41” Infantry Fighting Vehicle.
In addition, Formero successfully engaged with RDA’s Team Lynx using a range of digital technologies to create innovative designs for practical solutions. Formero has 3D printed a wide range of functional PA12 components with Multi Jet Fusion (MJF) technology. The properties of the components can rival injection molding. Delivered components include handles and communications panels.
The Research & Development Tax Credit
The now permanent Research and Development (R&D) Tax Credit is available for companies developing new or improved products, processes and/or software.
3D printing can help boost a company’s R&D Tax Credits. Wages for technical employees creating, testing and revising 3D printed prototypes can be included as a percentage of eligible time spent for the R&D Tax Credit. Similarly, when used as a method of improving a process, time spent integrating 3D printing hardware and software counts as an eligible activity. Lastly, when used for modeling and preproduction, the costs of filaments consumed during the development process may also be recovered.
Whether it is used for creating and testing prototypes or for final production, 3D printing is a great indicator that R&D Credit eligible activities are taking place. Companies implementing this technology at any point should consider taking advantage of R&D Tax Credits.
Conclusion
Rheinmetall’s list of expansion projects is impressive and will enable them to support German and other NATO countries increasing defense budget needs. Planned expansions provide the ideal opportunity to integrate 3D printing design and production capability.