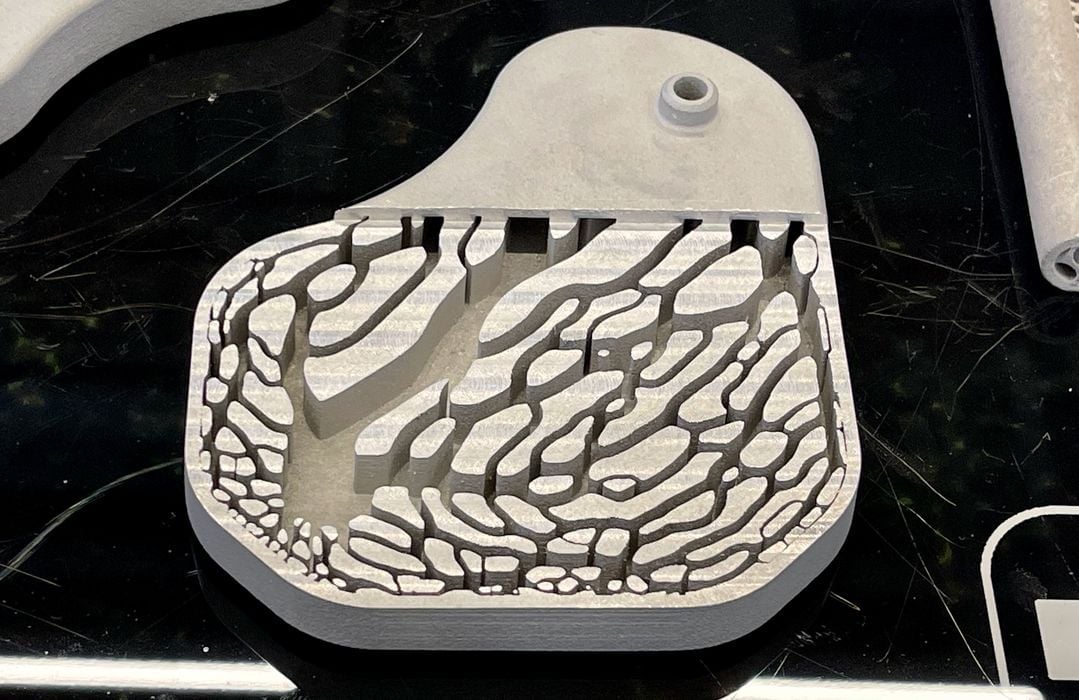
There are two very different news items from Ricoh.
One item is from Ricoh 3D for Healthcare, the company’s healthcare arm. They’ve struck a deal with Materialise to provide solutions for 3D printed anatomical models.
Anatomical Model Partnership
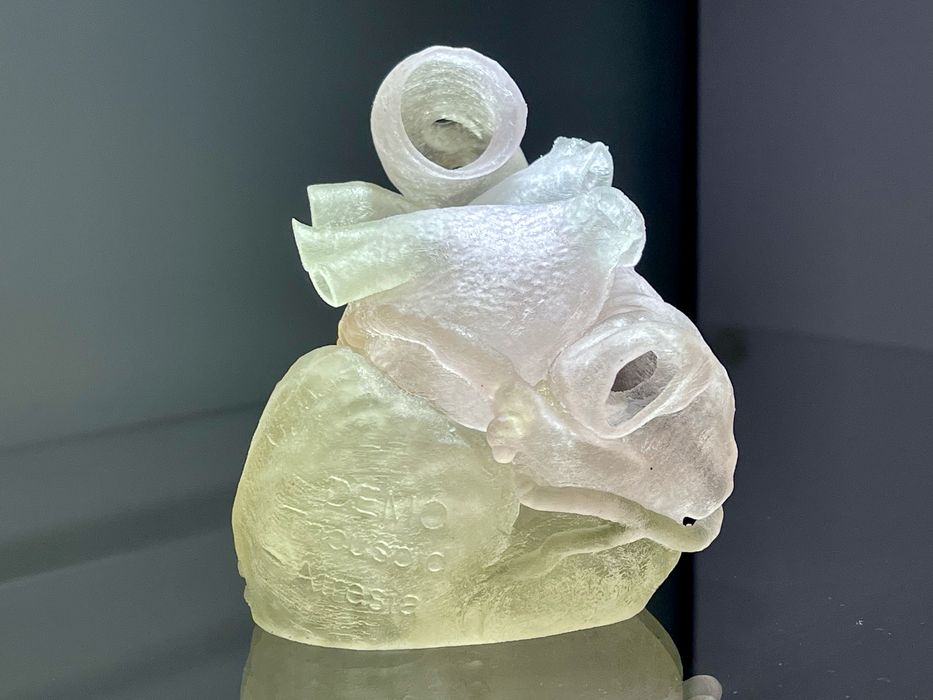
Anatomical models are used in several ways by healthcare professionals, including surgical planning, education and even outreach. Their use is becoming more popular due to easier access and the benefits of using them.
Ricoh has observed that hospitals are increasingly interested in anatomical models, but often struggle to find a solution: they’re doctors, not additive manufacturing engineers, after all.
The idea behind the partnership is that hospitals seeking to set up a “Point of Care” solution center will find it far easier, as the partners are able to provide both hardware and software bundles to streamline the process.
Metal 3D Printing
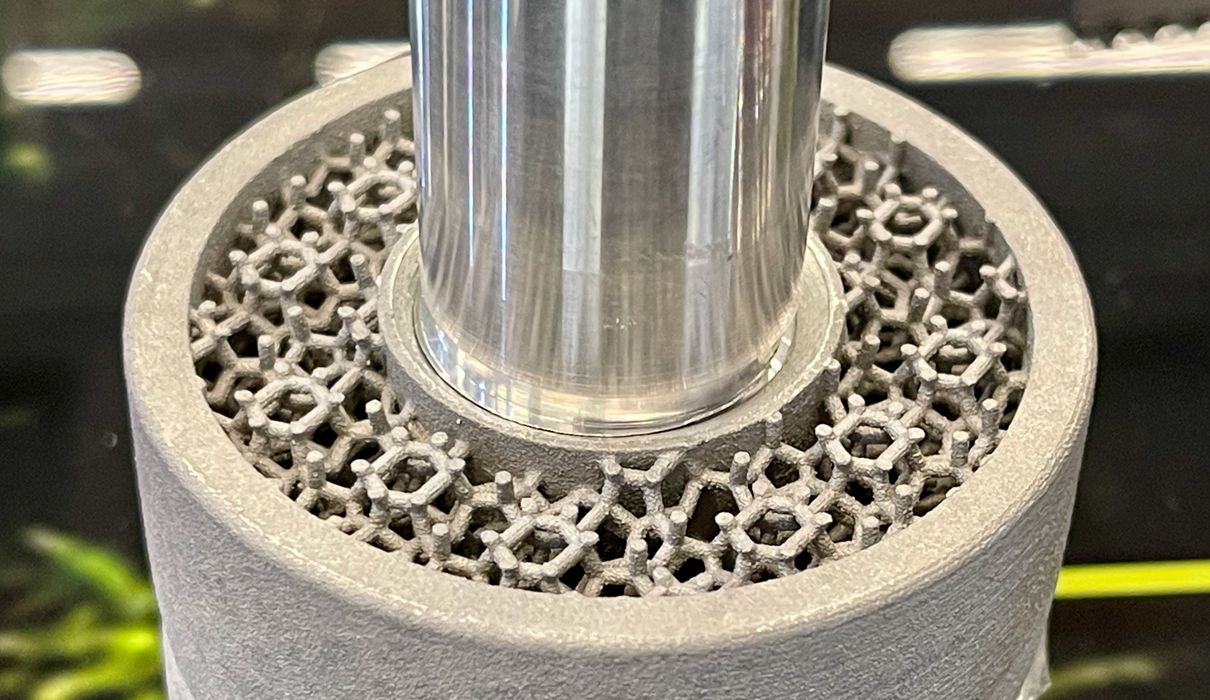
In discussions with Ricoh at Formnext, we learned the company is developing a metal binder jet 3D printer for production applications. Here you can see some sample metal prints in aluminum made by their system.
One of the materials they are experimenting with is an aluminum – silicon alloy, which is said to provide greater part strength.
Like the partnership above, Ricoh is also partnering with a number of external parties to make life easier for clients.
The issue is that 3D printing for industry involves a number complex steps beyond the printing itself. These range from initial design and CAD work, all the way through to post processing after printing.
Many customers, particularly those new to additive manufacturing, find these challenging to learn and adopt. Ricoh’s latest approach is to assemble a series of partners for each stage in the process.
For example, they partner with nTopology to help customers design complex 3D models using that firm’s nTop generative 3D software. They also partner with Siemens for production control functions. Finally, they partner with Addiblast for post processing steps.
This is quite an interesting approach, as it is indeed quite difficult for a potential customer to contemplate all these steps. Imagine a customer having to learn that these steps are required, which providers are available for each, choosing a combination of them, implementing them, integrating their functions together.
That’s quite daunting, and it’s not surprising that some companies avoid use of additive manufacturing entirely because they don’t want or can’t afford to go through all that effort. Here Ricoh has cut through the knot by providing a package of partners that are known to work together.
This is a very good approach that should be used by more 3D print providers.
Via Ricoh 3D For Healthcare and Ricoh