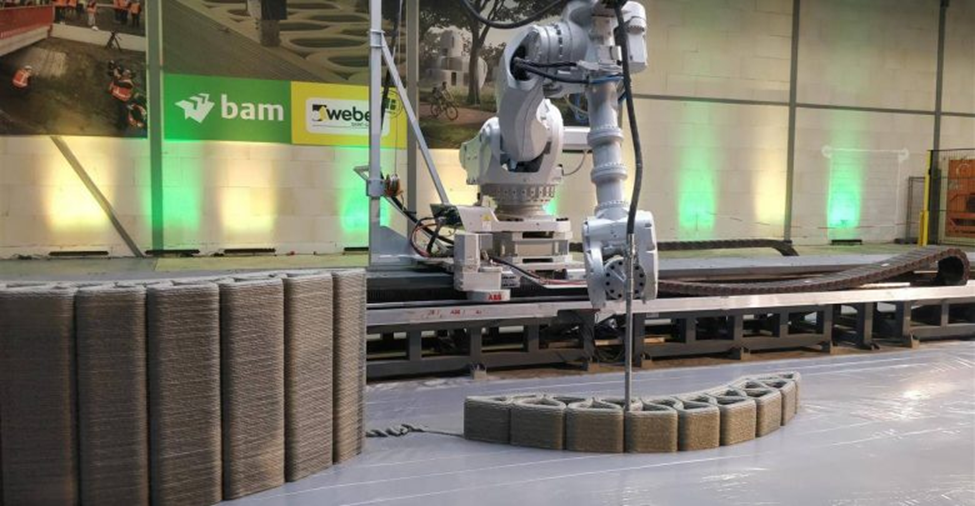
Charles R. Goulding and Arianna Coger consider how Saint-Gobain’s business strategies have been advancing the use of 3D printing in construction.
Saint-Gobain is a multinational construction materials company that has existed for hundreds of years, now operating in 70 different countries worldwide. The company ranks number one globally in the renovation industry, with a large focus on the design, manufacturing, and distribution of materials.
This consistent presence of Saint-Gobain in the market is likely due to their effort to constantly be current with the newest ways to develop buildings and their components. This includes implementing methods to increase the production of environmentally friendly products and help move towards the development of more carbon-neutral buildings. When compared to traditional manufacturing, additive manufacturing / 3D printing allows greater flexibility, reduced material waste, and lower carbon emissions. 3D printing can help facilitate the expansion of efficient construction due to its eco-friendliness, lower costs, and quicker results. Saint-Gobain has taken advantage of this opportunity by pursuing several partnerships and developments that involve 3D printing.
Partnership with Markforged
In 2019, Saint-Gobain partnered with Markforged, an industrial additive manufacturing company, to improve their workflow by using Markforged 3D printers. When Saint-Gobain was faced with a client who requested a modified design for bobbins, they needed to find a solution to produce newly designed spindle adapters that would hold these bobbins.
The decision to purchase Markforged X7 3D printers allowed Saint-Gobain to manufacture these altered designs with ease and provided a solution for the fabrication of any new designs in the future. Within six months, Saint-Gobain achieved a 100% ROI and could easily confirm that their investment was worth it. Since then, the company has implemented Markforged printers in more factories to help streamline manufacturing at other locations.
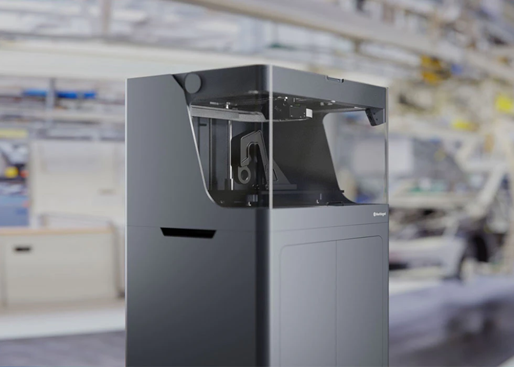
The Longest 3D Printed Pedestrian Bridge
Saint-Gobain has been working on “The Bridge Project,” with Royal Bam Group (BAM), a construction company, to create the world’s longest 3D printed bridge at over 95 feet long. The initial idea for this bridge emerged in 2017. In 2019, Saint-Gobain and BAM opened a concrete 3D printing factory near the city this bridge would be located – Nijmegen in the Netherlands. 3D printing provides an eco-friendlier way to build strong bridges within a shorter period and requiring less labor than traditional construction. The flexibility of 3D printing allows the bridge design to easily be converted to the actual structure without any changes. Using this technology, Saint-Gobain and BAM are helping prove that 3D printing is a viable method for cost-effective construction.
Producing 3D Printed Houses
In 2018, Saint-Gobain began working on five unique 3D printed concrete houses through a partnership with Eindhoven University of Technology of the Netherlands and several companies. This project is known as Project Milestone.
hese houses were designed to naturally fit in with its surroundings while having a futuristic look enabled by the freedom that comes with printing materials. The development and construction of these buildings are currently ongoing, with only one being completed currently. For the first house, only the structure was 3D printed with cement. With the construction of the following houses, the quality and number of components printed are expected to increase with the advancements 3D printing technology and the additional experience with 3D printing in construction.
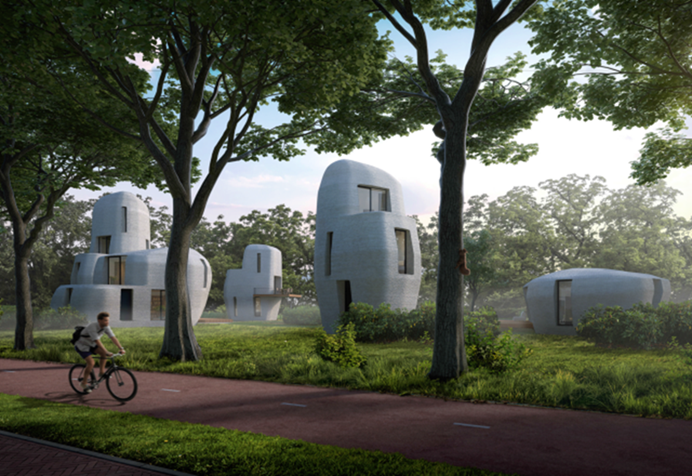
Investments in Innovative 3D Printing Companies
More recently, Saint-Gobain has invested in multiple 3D printing companies to advance their technologies. Announced in March 2021, Saint-Gobain has strategically decided to invest in Continuous Composites, a Coeur d’Alene, Idaho-based company working on developing and commercializing their patented technology called Continuous Fiber 3D Printing (CF3D). Few 3D printing companies work with composite materials such as carbon fiber which has a great amount of strength. As the technology is perfected, Saint-Gobain will be able to use 3D printing in a wider range of construction projects.
Companies that Saint-Gobain has previously invested in, such as Inkbit, continue to build and supply the newest 3D printing technologies. In 2019 Saint-Gobain initially invested in Inkbit, a Medford, Massachusetts-based company, to help them develop and improve 3D printers that use machine vision and artificial intelligence for better manufacturing. This year, Inkbit announced its first multi-material 3D printer using inkjet deposition, a technology that will surely be useful for Saint-Gobain and the construction industry as a whole. Each of these investments continues to help Saint-Gobain prepare for and adapt to the market of the future.
Federal tax incentives, such as the Research and Development Tax Credit, are available for companies that engage in 3D printing activities.
The Research & Development Tax Credit
Whether it’s used for creating and testing prototypes or for final production, 3D printing is a great indicator that R&D Credit eligible activities are taking place. Companies implementing this technology at any point should consider taking advantage of R&D Tax Credits.
Enacted in 1981, the now permanent Federal Research and Development (R&D) Tax Credit allows a credit that typically ranges from 4%-7% of eligible spending for new and improved products and processes. Qualified research must meet the following four criteria:
- Must be technological in nature
- Must be a component of the taxpayer’s business
- Must represent R&D in the experimental sense and generally includes all such costs related to the development or improvement of a product or process
- Must eliminate uncertainty through a process of experimentation that considers one or more alternatives
Eligible costs include US employee wages, cost of supplies consumed in the R&D process, cost of pre-production testing, US contract research expenses, and certain costs associated with developing a patent.
On December 18, 2015, President Obama signed the PATH Act, making the R&D Tax Credit permanent. Beginning in 2016, the R&D credit has been used to offset Alternative Minimum Tax (AMT) for companies with revenue below $50MM and, startup businesses can obtain up to $250,000 per year in payroll tax cash rebates.
Conclusion
The potential of 3D printing within the construction industry is increasingly being recognized by companies like Saint-Gobain. The global movement towards efficient manufacturing of materials and development of buildings is being propelled by 3D printing.