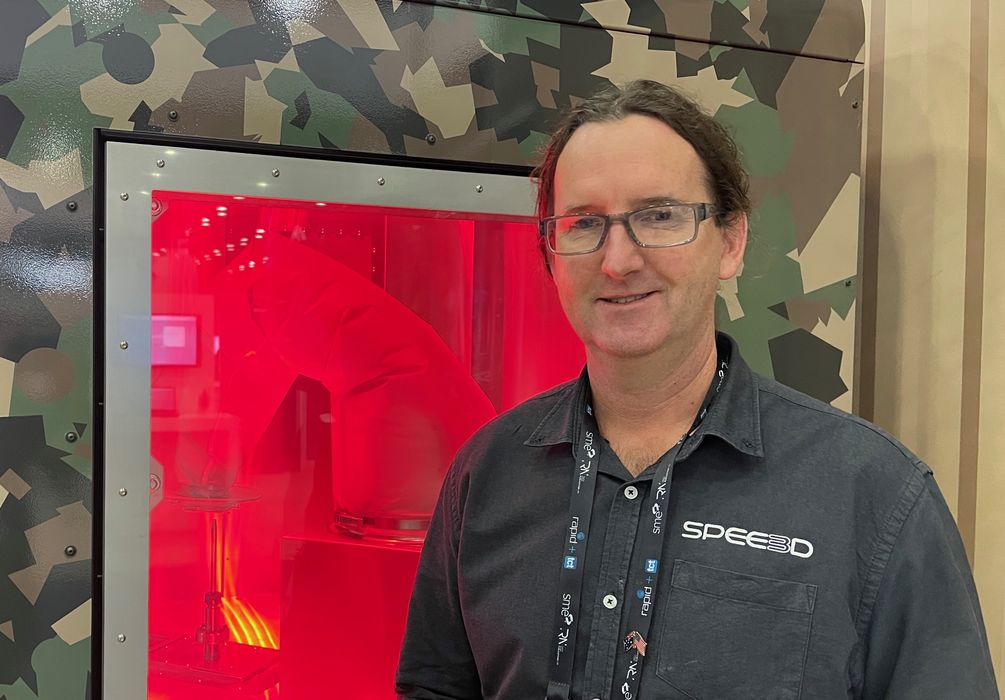
I spoke with SPEE3D’s CEO Byron Kennedy to learn more about the company’s intentions.
SPEE3D offers one of the most unique 3D printing processes: supersonic 3D printing. The process involves jetting fine metal particles at a target with literally supersonic speed. Upon impact the metal molecules naturally bond together and create a solid object. The process is able to handle unusual metals, such as copper, and can produce objects ridiculously fast.
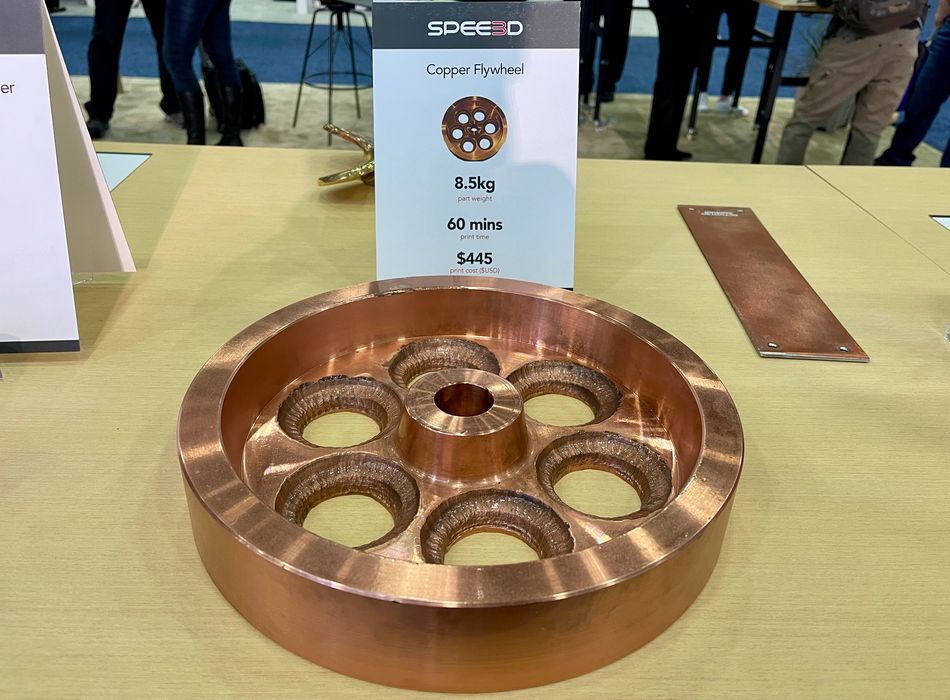
As an example, this heavy 8.5kg copper flywheel was printed in only an hour.
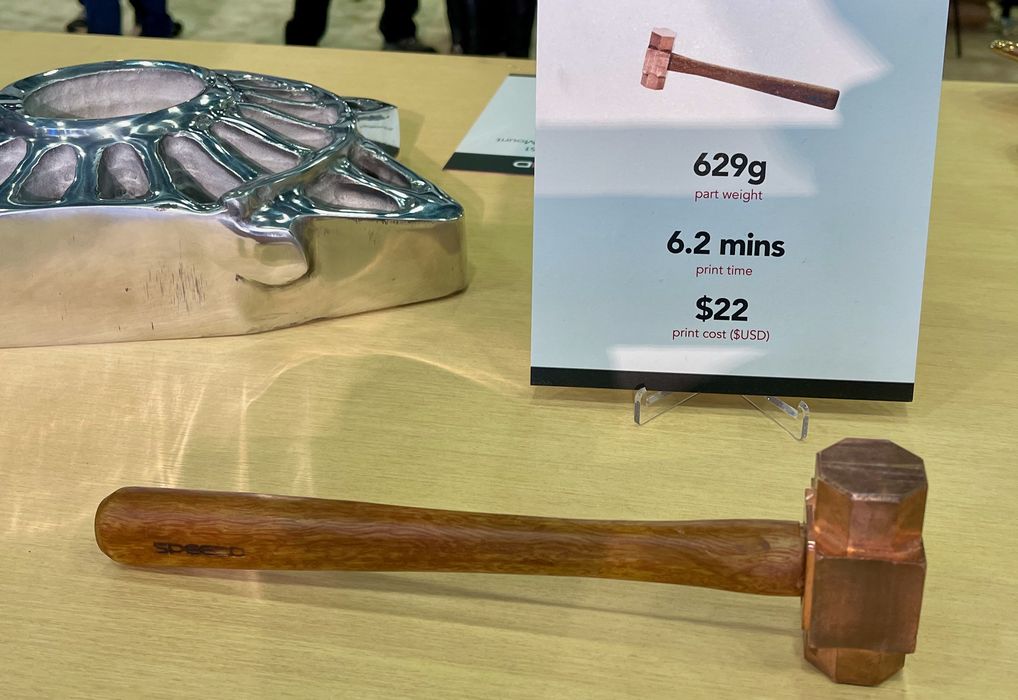
And this copper hammer (just the head, not the shaft) was printed in only 6.2 minutes. That’s an incredible speed for metal 3D printing.
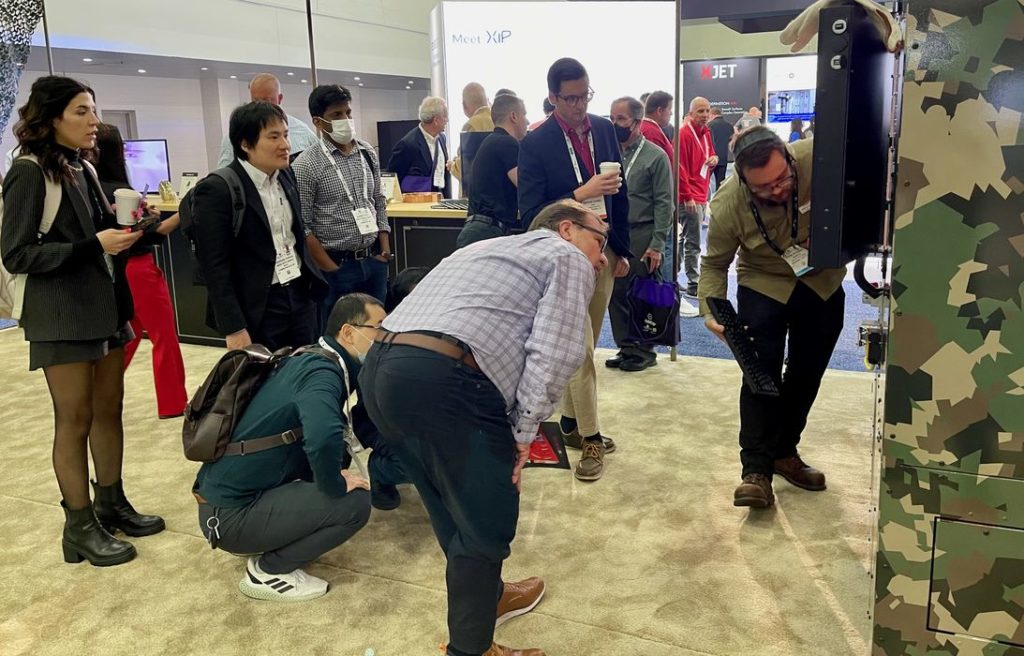
I spoke with Kennedy at Rapid+TCT, where SPEE3D was one of the very few exhibitors that was actually printing objects. Most exhibitors simply displayed unpowered equipment or only print samples. This, of course, led to a continuous crowd of watchers.
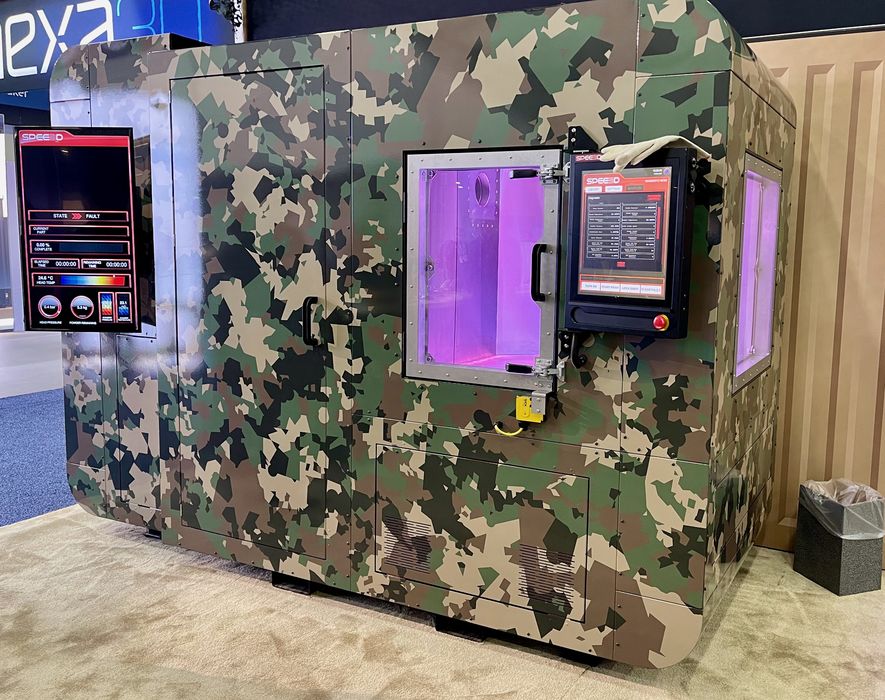
SPEE3D has been focusing on military applications in the past couple of years, and that’s probably a good market for their robust, easy-to-use metal 3D printers. You may notice the camouflage markings on the SPEE3D printer in these images, but I don’t think the printer will literally be on a battlefield requiring camo. Making quick spare parts in the field is far more effective than shipping them from a distant warehouse.
Most recently SPEE3D has been selected by the US Navy to participate in the “MaintenX” program, where the digital inventory concept for spare part production will be tested. The program will involve a series of tests this August in California.
Why is the navy so interested in SPEE3D’s metal 3D printing technology? Kennedy had a simple answer:
“Ships aren’t level.”
This is a profound implication for metal 3D printer manufacturers, almost all of which rely on gravity and level printing conditions for their powder bed processes. That’s not the case for SPEE3D’s tech, which can operate in unlevel and changing conditions, ideal for shipboard 3D printing of metal parts. Kennedy believes his equipment can “handle rough conditions.”
While the MaintenX program would seem to be a good start for getting into the naval market, it could actually lead to a far bigger prize for the company: maritime 3D printing.
While navies around the world operate ships, so do commercial companies, and in far greater number. All of these ships will have similar needs for spare parts, and ship downtime can be extraordinarily expensive for operators. Kennedy said that the “value of parts doubles every 100 minutes of downtime”, and I don’t doubt it.
By proving shipboard 3D printing capability via the military venture, SPEE3D could find themselves in an excellent position to market their equipment to commercial shippers worldwide. It’s possible in the future you might find a metal 3D printer on every major ship, ready to produce spare parts on demand. That could be a massive market for SPEE3D.
And if that wasn’t enough, Kennedy then started discussing mining, where similar remote operations also have very expensive downtime scenarios. According to Kennedy, a “mine is worth a million dollars a day.”
Via SPEE3D