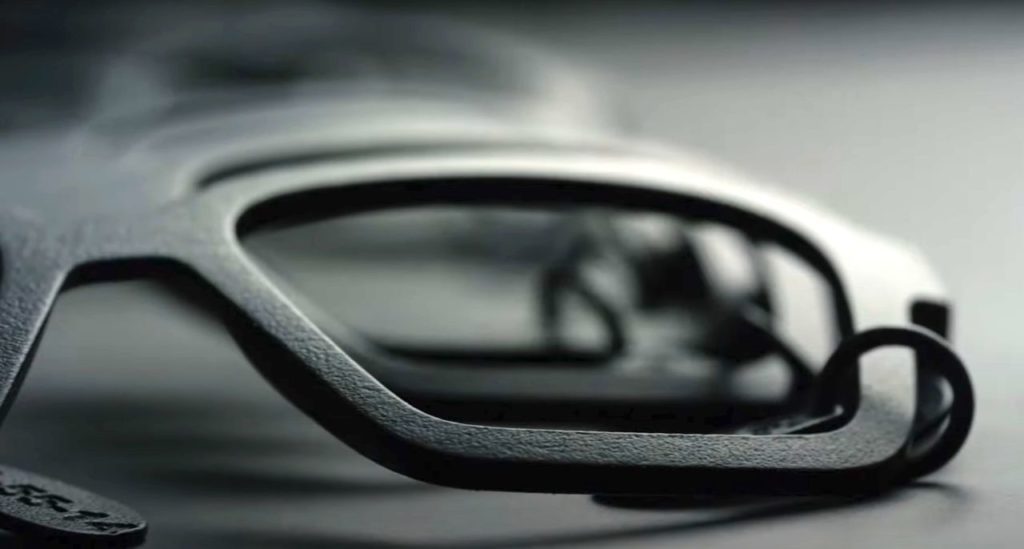
EOS and one of their clients commissioned a study to determine the sustainability of their AM lifecycle.
This has long been a question posed by industry observers: is 3D printing more viable in the environment than, say injection molding or CNC milling techniques? There have been arguments one way or another for years, but could this new study decide the outcome?
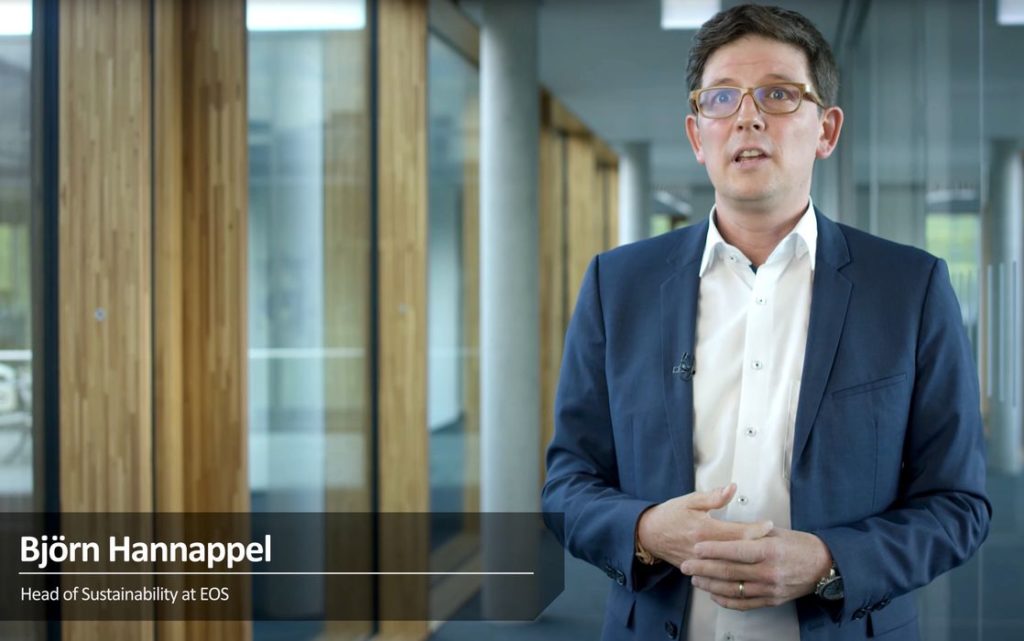
EOS is in a position to attempt to answer that question, as they have a Head of Sustainability, Björn Hannappel. They are one of the few large AM companies to do so, along with Stratasys.
The study involved the production of mass customized eyewear from EOS client YOU MAWO. The German manufacturer uses 3D scans to develop personalized 3D eyewear models that are then 3D printed on EOS equipment.
Their eyewear products are actually quite interesting: they’re 30% lighter than conventional frames, more resistant to bodily fluids, cosmetics & UV light. They’re also extremely robust, as you can see in this image:
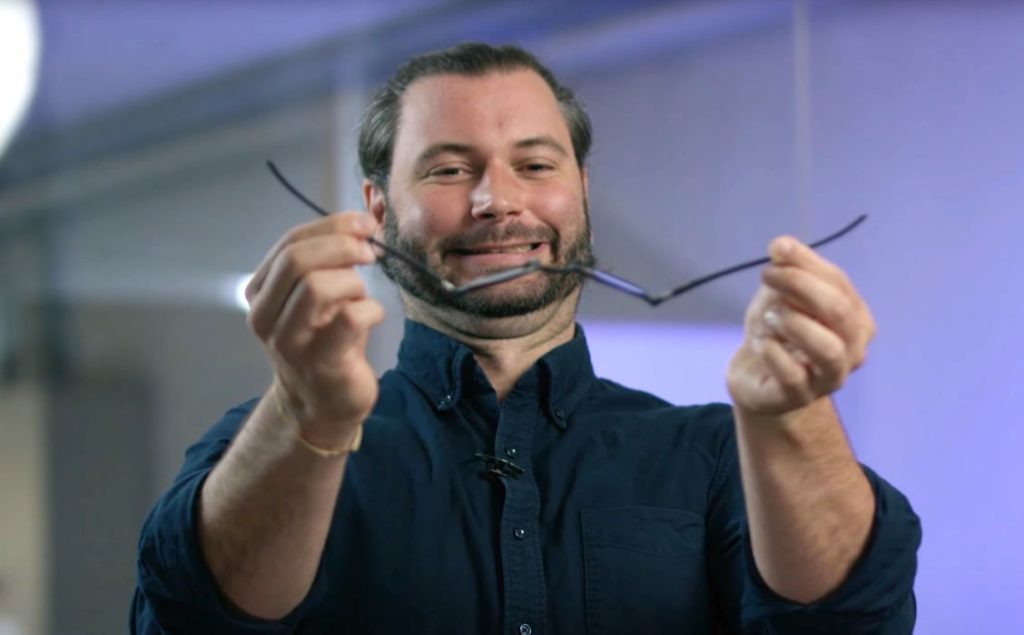
The partners commissioned Fraunhofer EMI to perform a study of the sustainability of the entire production cycle for these frames and compare it to conventional approaches. They explain the nature of the work:
“Fraunhofer EMI, conducted a systemic Life Cycle Analysis (LCA) for YOU MAWO eyewear over the entire life cycle of its 3D printed glasses. From cradle-to-grave, excluding the use phase, this study compares the environmental impact of additively and conventionally manufactured eyewear, covering the life cycle from material sourcing, to production to packaging and shipping. The study also included a hotspot analysis to identify major contributors and potential for improvement, including powder refresh rates, powder feedstock, and energy sources used.”
The results? They explained:
“The study concluded that 3D printed eyewear performs significantly better than the conventional eyewear in all 18 impact categories, such as climate change, human toxicity, ozone depletion, and water depletion. As an example, the carbon footprint of a customized, 3D printed YOU MAWO eyewear product is around 58 percent lower compared to conventionally manufactured eyewear. The analysis also concluded that 3D printed eyewear compared to conventionally manufactured Acetate eyewear, creates 80 percent less waste and can help to avoid lengthy post processing.”
This video describes the study and the products made by YOU MAWO:
This is notable, as it could indicate that AM is a more sustainable approach. But is this really true?
There’s a couple of caveats here that are hidden in the details.
First, it turns out that YOU MAWO powers all their locations with renewable energies. This means that any comparison source powered by fossil fuels would immediately drop some eco-points.
Secondly, the comparison was between Germany-produced AM parts and parts produced overseas and shipped to Germany. This implies that the eco-cost of shipping was a major part of the comparison. Current shipping methods certainly are a major source of CO2, which would be much smaller if parts are produced in their destination locale.
So is this truly a valid comparison?
On one hand it actually does compare real-life scenarios: buying goods in China versus 3D printing them on site. Companies really do buy from overseas, and in some cases do have the option of producing them locally with additive approaches.
However, I’d be interested to know the comparison between German AM and German CNC or injection molding.
On the other hand, maybe this simply indicates that shipping parts long distances is a bad idea? Could it be that locally 3D printed parts are just “better” because they eliminate the eco-unfriendly shipping component of the lifecycle?
That’s my take on this question.