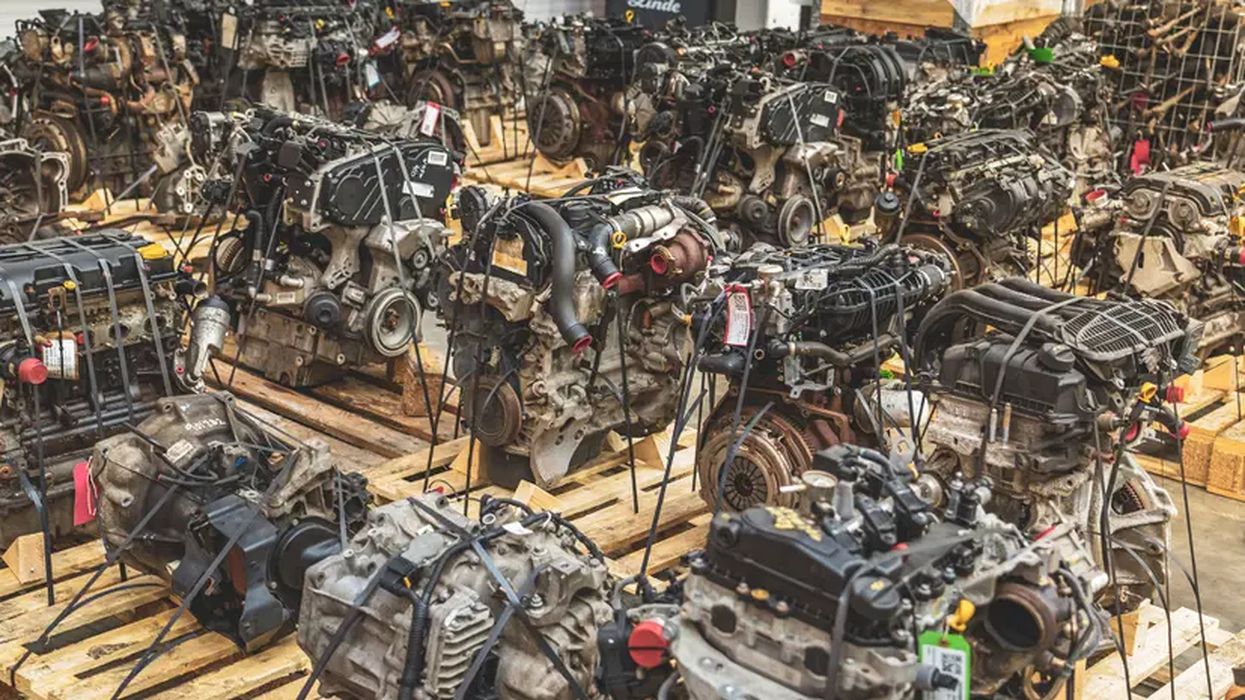
Charles R. Goulding and Preeti Sulibhavi explore the driving factors of the auto de-production model and how 3D printing can enhance this concept.
The July 22, 2023, issue of The Economist has a fascinating article about Charles Trent, a large vehicle recycling company in Britain’s south coast that has recently invested US$13 million to de-produce junk cars.Ā
The company has plans to build five more plants. Essentially, the company is creating a reverse logistic auto assembly line that takes junk cars apart. The first step to the depollution process starts with removing wheels and extracting all fluids and gases.
Similar companies in other parts of the globe include LKQ-Keystone, a Chicago-based company that has 170 dismantling plants, as well as Indra, a French firm that manages 380 recyclers in France. Indra is jointly owned by Suez and Renault.
The U.S. environment is more complicated by the fact that steel processors have been purchasing large segments of the industry for material feedstock. The Charles Trent model could enable them to extract added value from de-producing before transforming the remaining auto skeletons into feedstock.
Deproduction and the sale of the underlying components are lucrative because auto parts currently command very high prices. The price-supporting elements are:
- Increased requirements for the auto industry to provide cradle-to-grave circularity,
- Continued auto part supply chain issues,
- A constrained new car market resulting in a longer life cycle for used cars, and
- Sustained high used car prices justifying repairs.
This volume of deproduction facilities is going to produce actionable, analytical data. The growth of the auto 3D printed components industry adds a new dimension to this business event.
When the deproduction data coupled with auto parts predictive machine learning analytics wear data demonstrates that certain parts are in stronger demand than other parts then 3D printing can be utilized to fill the production gap.
As both the OEM and aftermarket 3D printed parts markets continue to grow and the number of non-3D printed auto parts will continue to shrink.
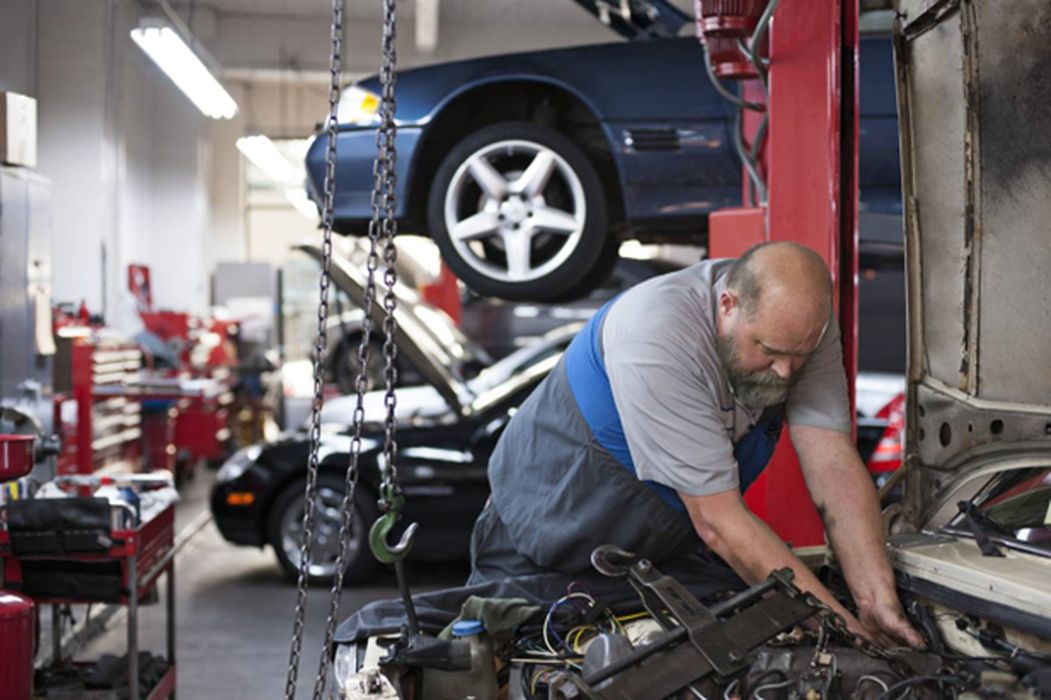
Automotive Recycling and 3D Printing
Circular manufacturing involves reducing the amount of energy involved in production. We have covered auto part recycling before, but the trend has expanded and the scope is much greater.
3D printing fits into this concept in that it reduces the amount of material used in a car by about 40 percent while maintaining structural stability.
In addition, the opportunity for aftermarket channels is obvious here. If certain parts are retained from the de-production production process and need some repairs, 3D printers can offer high-quality solutions in-house and at reduced cost. Then, these parts can be transformed into replacement parts and reintroduced into the auto parts supply.
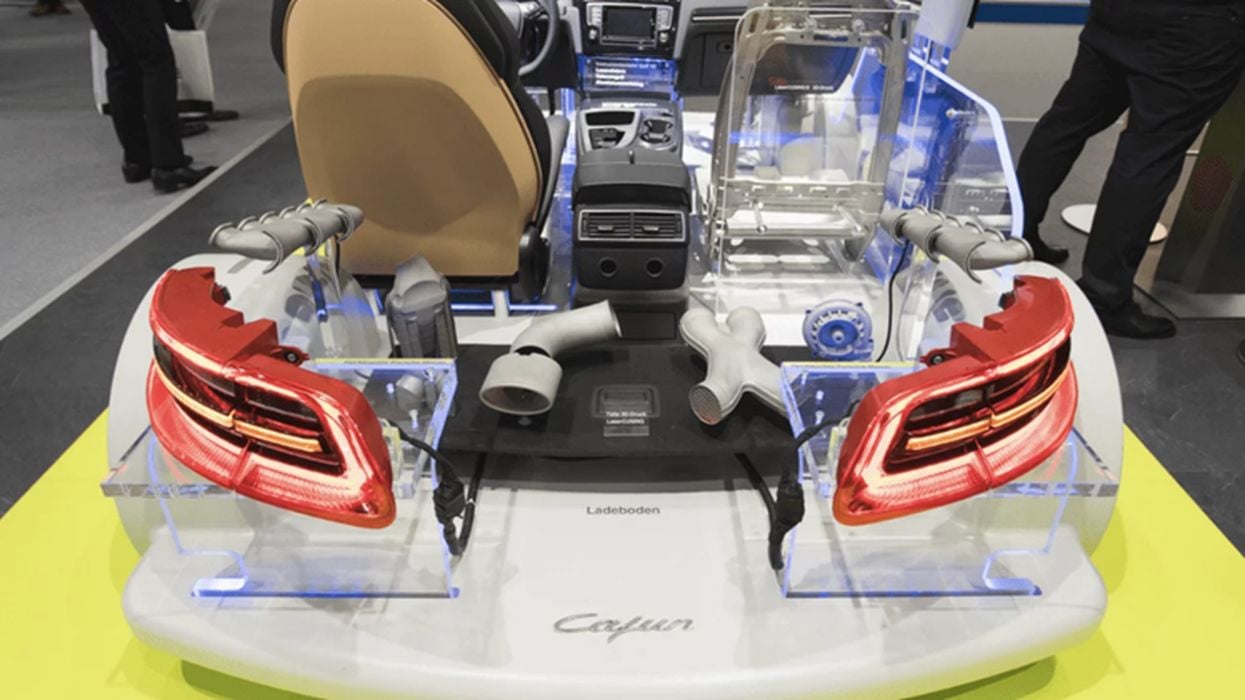
The Research & Development Tax Credit
The now permanent Research and Development (R&D) Tax Credit is available for companies developing new or improved products, processes and/or software.
3D printing can help boost a companyās R&D Tax Credits. Wages for technical employees creating, testing and revising 3D printed prototypes can be included as a percentage of eligible time spent for the R&D Tax Credit. Similarly, when used as a method of improving a process, time spent integrating 3D printing hardware and software counts as an eligible activity. Lastly, when used for modeling and preproduction, the costs of filaments consumed during the development process may also be recovered.
Whether it is used for creating and testing prototypes or for final production, 3D printing is a great indicator that R&D Credit eligible activities are taking place. Companies implementing this technology at any point should consider taking advantage of R&D Tax Credits.
Conclusion
Increased used car auto deproduction is good for the environment. Deproduction data analysis should identify 3D printing part production opportunities and growth areas. With increased auto 3D printing volumes, the auto parts industry should compare the capital cost of auto deproduction equipment versus 3D printing capital equipment. The right combination will result in an optimal economic result.