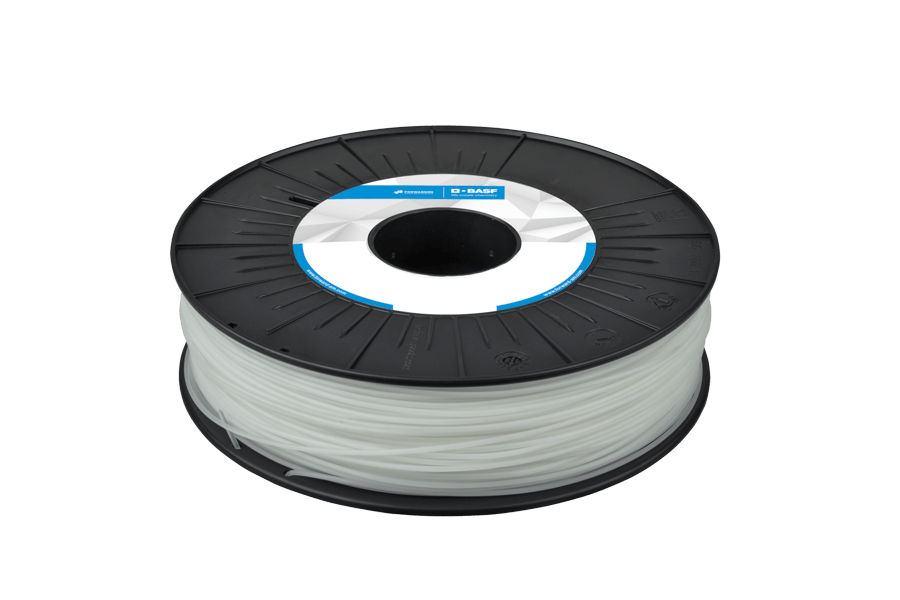
Among the many enduring repercussions of last month’s disastrous winter storm in Texas is a plastics supply chain shortage that could impact filament raw suppliers.
Texas Winter Storm
Texas is known for many things: big hats, big hair, and at least according to 3D printing trade shows past, armadillo racing. Disaster preparedness in terms of freezing temperatures is, unfortunately, not among these qualities. Texas is normally a rather warm state, with fairly sedate winters, which understandably might be a relative thing.
For reference, please note I live in Cleveland, where lake effect snow is a very normal thing bringing several feet at a time; most winters are sedate next to ours. Winter preparedness is in my DNA. That is, though, out of familiarity and regular necessity. While I’ve admittedly chuckled at reports of Southerners refusing to drive when there’s an inch of snow on the ground, there are very real reasons why that can be an actual danger. Lack of infrastructure, salt trucks, and deeply ingrained driver training add up to unsafe driving conditions really quickly.
And so it is for Texas. While they’ve had big winter storms in the past, they’ve been infrequent enough that state officials have time and again ignored calls to strengthen their infrastructure to protect against future disruptions. Wikipedia offers a handy backgrounder on previous winter storms and ignored calls to upgrade the state’s electrical grid.
When Winter Storm Uri hit, it hit hard. Not just Texas, of course, but this state has faced some of the farthest-reaching consequences. Dozens lost their lives; millions lost power for days; boil-water warnings lasted for weeks in some areas. The power outages and subsequent ridiculous pricing — “wholesale electric prices went to as high as $9,000/megawatt-hour which was limited as a ‘system cap’, compared to a more typical $50/MWh,” Wikipedia recaps — created, to put it mildly, significant problems.
3D Printing Supply Chain Shortages
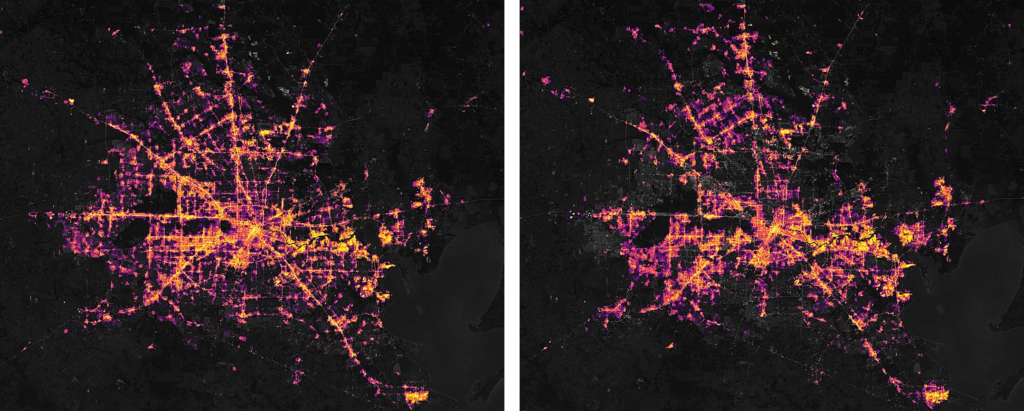
The storm was terrible…but what does that have to do with 3D printing? Aside from power issues where 3D printing can be brought into play in, for example, generator production, repercussions are reaching the supply chain.
Supply chain difficulties are nothing new at this point, following what 2020 brought in terms of pandemic disruptions and closed borders. Most of the time when we talk about 3D printing and supply chain difficulties, the conversation is focusing on 3D printing as a solution. Decentralized production has proven a stop-gap supply solution in many cases, and built up new business cases for enduring use. But a new domestic supply chain shortage could impact 3D printing materials.
In discussions with AON3D, a 3D printer company with a wide view of the filament / thermoplastics market:
“There is a plastics supply chain shortage coming down the pipeline and it’s already hitting some of the filament raw material suppliers.”
The Wall Street Journal reports that chemical plant shutdowns in the state following the power disruption are “disrupting a global supply chain for consumer goods.” The article, aptly headlined “Texas Freeze Triggers Global Plastics Shortage,” highlights raw material impacts for, primarily, plastics.
The WSJ reports:
“The power outages brought the world’s largest petrochemical complex to a standstill, forcing more plants in the Gulf of Mexico region to shut down than during Hurricane Harvey in 2017. A month later, many remain offline, and analysts said it could be months more before all are fully back.”
Furthermore:
“Prices for polyethylene, polypropylene and other chemical chemical compounds used to make auto parts, computers and a vast array of plastic products have reached their highest levels in years in the U.S. as supplies tighten. For example, prices for polyvinyl chloride, or PVC, have more than doubled since last summer, according to S&P Global Platts.”
Among other industries noted as being impacted are production of natural gas, semiconductors, automotive, construction, PVC piping, and medical supplies (e.g., sharps containers). But a lot of those plastic materials are also familiar in production of 3D printing filament, and so may touch on even more industries indirectly.
Plastics Force Majeure
Petrochemical — and thus plastic — supply chain difficulties will be far-reaching. Impacts and high prices are expected to endure for months yet.
M. Holland has collected an up-to-date list of force majeure and allocation announcements from plastics suppliers. Merriam-Webster reminds us that:
“In business circles, ‘force majeure’ describes those uncontrollable events (such as war, labor stoppages, or extreme weather) that are not the fault of any party and that make it difficult or impossible to carry out normal business. A company may insert a force majeure clause into a contract to absolve itself from liability in the event it cannot fulfill the terms of a contract (or if attempting to do so will result in loss or damage of goods) for reasons beyond its control.”
The growing M. Holland list includes many companies familiar to the additive manufacturing polymer supply chain. As of the 15 March update, just a few of these impacts include:
- BASF declared force majeure on all PA6 and PA66 compounds.
- Braskem declared force majeure on polypropylene products.
- Covestro announced a new force majeure effective Feb. 14 on all polycarbonate products, superseding a prior force majeure that was in place.
- DuPont declared a global force majeure for Zytel (including Zytel HTN and Zytel Specialty Nylons), Crastin, Rynite, Selar, Minlon and Pipelon.
- INEOS declared force majeure on polypropylene and polyethylene products due to the storm.
- INEOS Styrolution declared force majeure on Luran S ASA, Terluran ABS, and Novodur high heat ABS from its Altimira, MX facility.
- LyondellBasell declared force majeure on polyethylene and polypropylene products due to the storm.
- LyondellBasell announced a partial lifting of force majeure, affecting Line 5 at its Morris, Illinois, facility and LD1, LD2 and PF4 at its Clinton, Iowa, facility.
- Sabic declared force majeure on LEXAN resins, CYCOLOY resins, XENOY resins, GELOY XP series resins, VALOX FR resins and XYLEX resins, as well as ABS product from its Tampico, Mexico, plant. In addition, Sabic declared force majeure on SABIC PP Compound and STAMAXX resins from its Bay Saint Louis, Mississippi plant.
M. Holland is updating its COVID-19 impacts on the plastics industry, now including updates to its force majeure list re Winter Storm Uri, regularly.
The full impact of the winter storm’s impacts on the US supply chain remain to be seen. Frankly, until it came up in this one discussion I hadn’t heard — or thought — about a direct impact on the polymer 3D printing industry. Looking over the WSJ’s report and M. Holland’s curated list of plastics industry disruptions, though, it’s hard to think this is the last we’ll be thinking of this latest disruption to the supply chain.
Via Wall Street Journal and M. Holland / Hat Tip: Eric