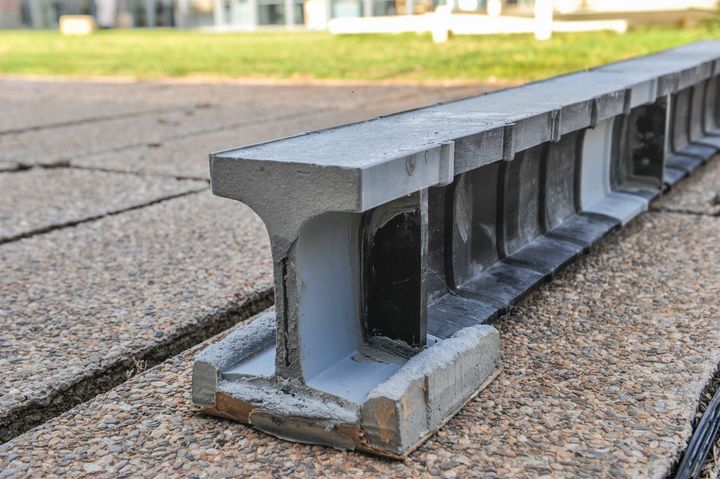
Making business sense of a proposed 3D printing application can be a lot more complex than you might imagine.
Iâm looking at an interesting research project undertaken by the Universitat Politècnica de València, who have developed a method of 3D printing large construction girders. The polymer girders have a number of advantages over conventional metal girders, including:
- Lightweight due to use of polymers and a sparsely-dense interior
- Long-term resistance to the elements, including no possibility of rusting out years later
- Ability to produce segments of desired lengths
- Made from recycled plastics
I always consider the business aspects of research projects like this, because even if they are fascinating, ingenious and inspiring, they wonât have legs unless there is a clear business case to attract buyers.
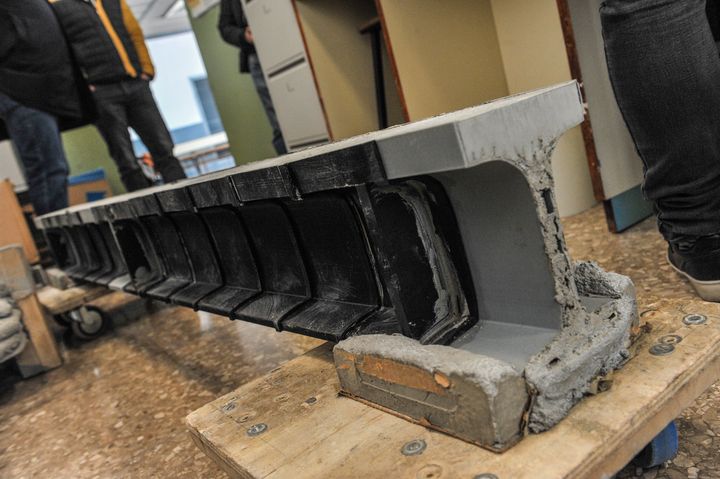
For this innovation, the market would be buyers of structural girders. For decades these buyers have been purchasing and using typical metal units. When faced with the option of acquiring hypothetically commercialized polymer girders, what goes through their minds?
3D Printed Beam Advantages
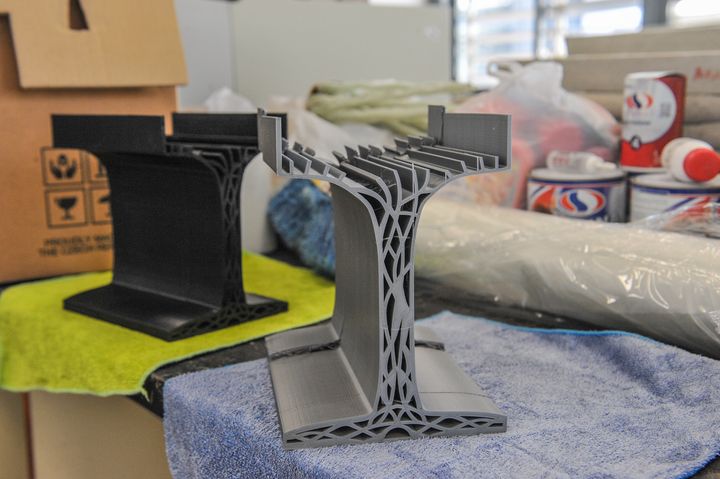
There are obvious aspects, such as the lighter weight and corrosion resistance, but there are a number of other potential advantages they might not immediately recognize. Letâs take a look at a few of them for this specific application.
The lighter weight beams could potentially:
- Reduce the need for expensive equipment usually required to move heavy metal girders
- Reduce job site injuries
- Simplify foundation strength requirements
- Reduce overall structural needs due to lighter weight upper floors
Another series of advantages results from the girderâs ability to be 3D printed on site:
- Reduction in girder cutting as parts are made to desired lengths
- Elimination of the normal transportation costs to move girders from distribution center to job site
- Reduction in CO2 emissions
- Eliminates the need for construction and tear down of formworkâs
- Eliminates the need for bending girders to fit placements
As you can see, some of the advantages are quite indirect, yet are definitely present. Someone casually comparing polymer girders with metal girders might not note these advantages because they might mistakenly make assumptions about how the product would be used. They could assume the remainder of the work process remains the same, yet in fact the work process would change significantly because of the new type of girder.
3D Printed Beam Questions
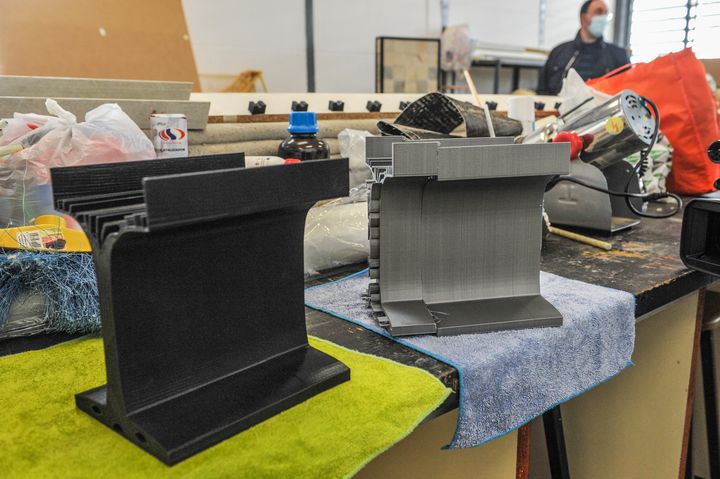
That might get you thinking that these polymer girders are clearly the correct solution. But there are more things to consider:
- What is the cost per length of the polymer girder? Is it less than a metal girder?
- What is the total installed cost of the polymer girders vs that of metal girders, accounting for all the changes?
- How quickly can polymer girders be produced on site? Will the workforce have to wait hours for girders to be printed? What does that cost?
- What is the cost and time required to set up, operate and tear down the girder printer?
- How often do prints fail?
- How reliable is the 3D printer? If it fails, is there someone to repair it?
- Are special skills required to operate the printer or use the girders? Who needs to be trained?
- What is the cost of training or experienced contractors? Are they even available?
- Would building regulations allow use of polymer girders? Or is an administrative effort required to gain approval before the project can proceed?
As you can see, the analysis for this â or any â unusual 3D print application is far from clear and requires considerable thought. What is the answer for this application? Who knows? It might be a good idea, or it might not. It might make sense in one region, but not in another.
Imagine a mid-level manager who has never heard of this type of product trying to work through all of these factors, if they even realize they exist. In many cases I fear that they would simply want to avoid the trouble of figuring it out and go with the tried and true solution that theyâre familiar with.
For someone attempting to sell the new product, they face an incredible obstacle of understanding. To overcome this barrier sophisticated marketing and education is required, and thatâs not easy to do.
The analysis shown here is, I think, representative of the problems facing the 3D printing industry: itâs complicated!