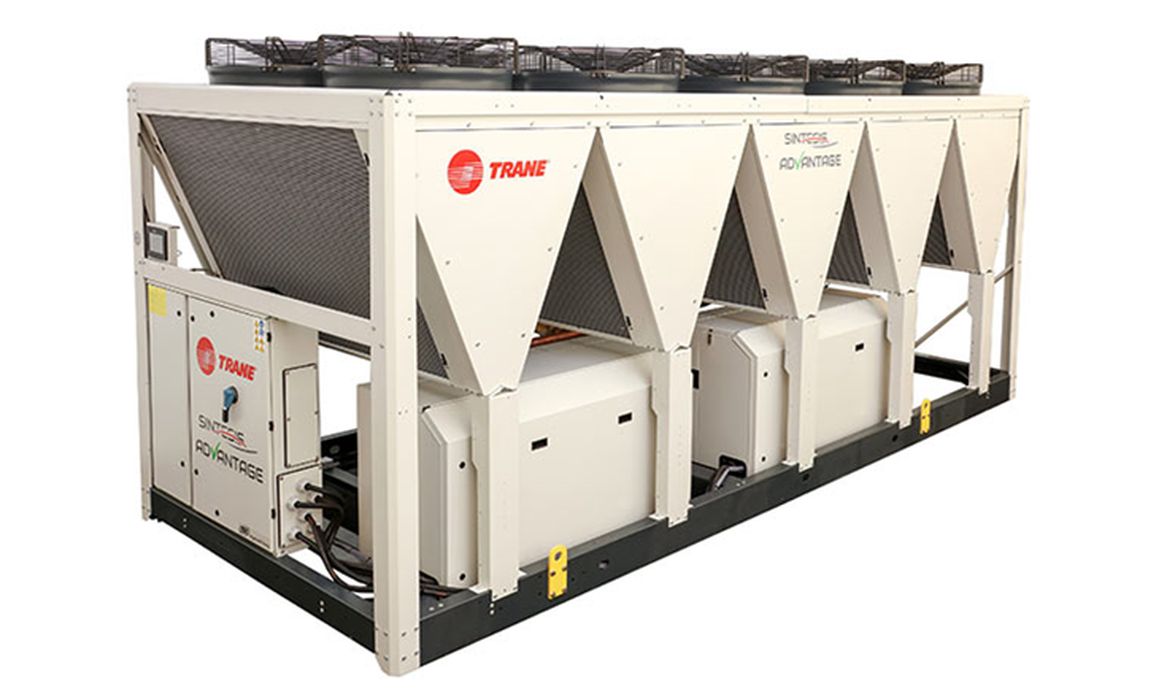
Charles R. Goulding and Preeti Sulibhavi discuss how US federal funding is fueling heat pump innovation, and how Trane, Texas A&M, and Purdue University are leading the way.
The recent announcement regarding US federal funding for heat pump technology development includes the use of 3D printing. Trane Technologies was one of the recipients. Involved in this effort are the Department of Energy’s (DOE) Oak Ridge National Laboratory, Purdue University and Texas A&M.
These new heat pump innovations build on Trane Technologies’ position as an industry leader in decarbonization solutions for the built environment. A company that essentially connects energy sources with the right technology is now heating things up.
The company’s latest heat pump technology for commercial buildings combines heating and cooling systems into one, high-efficiency electric solution. Its residential cold-climate heat pump surpassed the DOE requirements for high-efficiency heating in freezing temperatures.
Through bold, industry-leading action, Trane Technologies is advancing its 2030 Sustainability Commitments, including its Gigaton Challenge, and its net-zero by 2050 pledge, with emissions reduction targets validated by the Science Based Targets Initiative (SBTi).
Recent heat pump federal program participants include Carrier and Lennox. These companies, like Trane, are vying for funding to find solutions for transformative heat pump technology for decarbonization.
Texas A&M
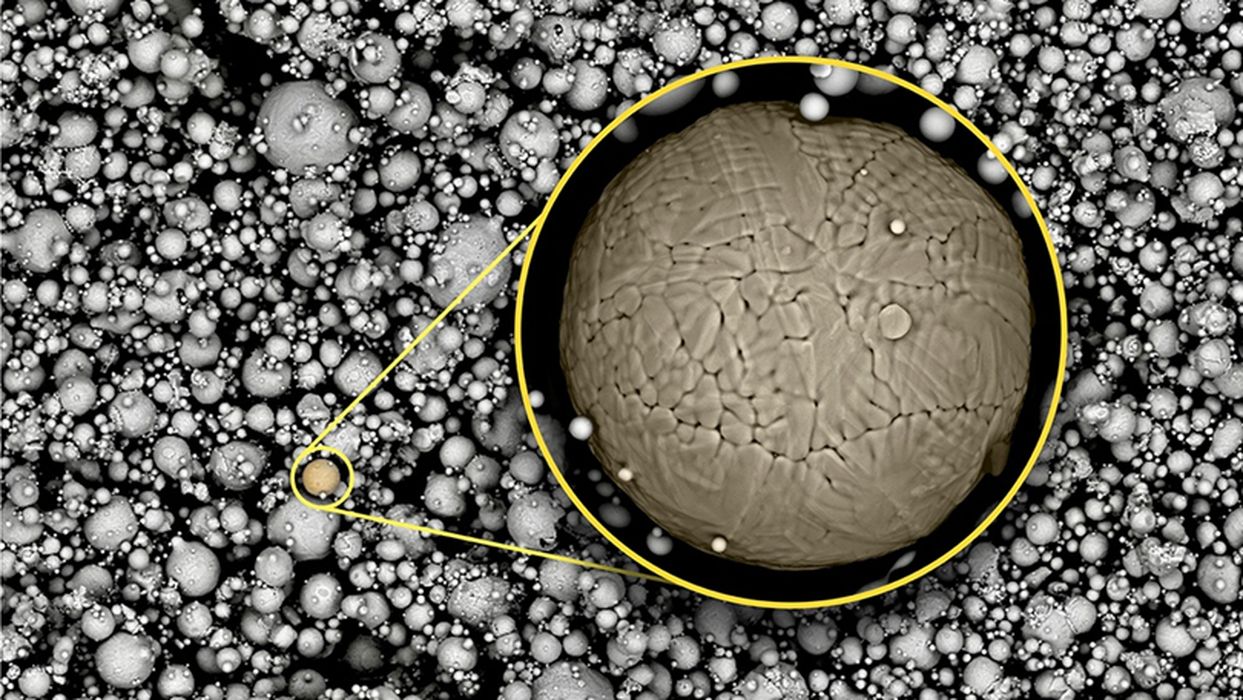
Texas A&M University is home to advanced 3D printing developments. Texas A&M announced in 2020, that it is working with the Air Force Research Laboratory and they determined how to 3D print martensitic steel “into very sturdy, defect-free objects of nearly any shape.”
According to Texas A&M, 3D printing martensitic steels historically left the metal with unwanted pores.
“Porosities are tiny holes that can sharply reduce the strength of the final 3D printed object, even if the raw material used for the 3D printing is very strong,” Texas A&M Materials Science and Engineering Department head Ibrahim Karaman said in a statement. “To find practical applications for the new martensitic steel, we needed to go back to the drawing board and investigate which laser settings could prevent these defects.”
Texas A&M and the Air Force Research Lab figured out how to predict which settings yielded better martensitic steel.
Another promising development at Texas A&M is the ME 3D printing technique, known technically as fused-deposition modeling (FDM), molten plastic is squeezed out of a nozzle that prints parts layer-by-layer. As the printed layers cool down, they fuse together to create the final 3D part.
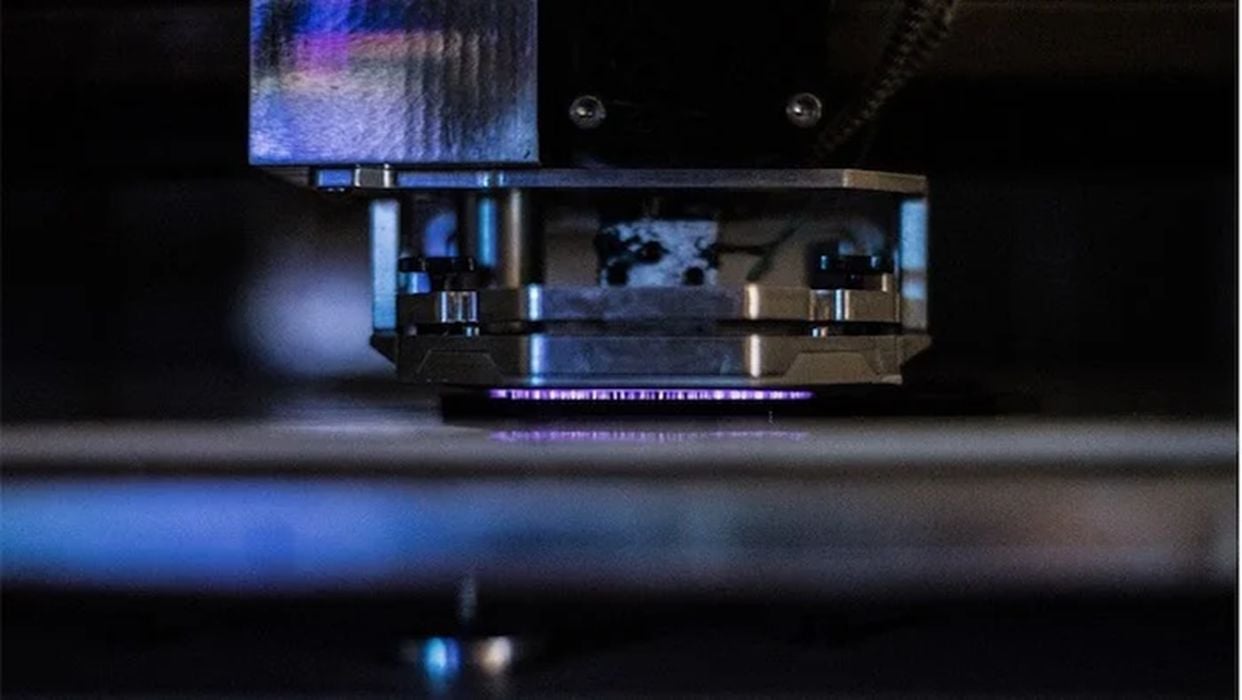
However, previous studies have shown that these layers bond inadequately; the final printed parts when the ME method is used are notably weaker than identical parts made by injection molding where melted plastic assumes the shape of a pre-set mold when it cools down.
“Finding a way to remedy the inadequate bonding between printed layers has been an ongoing quest in the 3D printing field,” said Micah Green, associate professor in the Artie McFerrin Department of Chemical Engineering. “We have now developed a sophisticated technology that can bolster welding between these layers all while printing the 3D part.”
To join the various joints and interfaces of a 3D part printed via the ME technique, more thoroughly, additional heating is required. However, heating 3D printed parts using a furnace-like solution has a major drawback. “If you put something in an oven, it’s going to heat everything, so a 3D-printed part can warp and melt, losing its shape,” Green explained. “What we really needed was some way to heat only the interfaces between printed layers and not the whole part.”
Integrating plasma science and carbon nanotube technology into standard 3D printing to weld adjacent printed layers more effectively, increasing the overall reliability of the final piece.
Since carbon particles heat in response to electrical currents, the researchers coated the surface of each printed layer in them. Similar to how a microwave heats up food, the team found that the carbon nanotube coatings can be heated using electric currents, thereby enabling the printed layers to bond together.
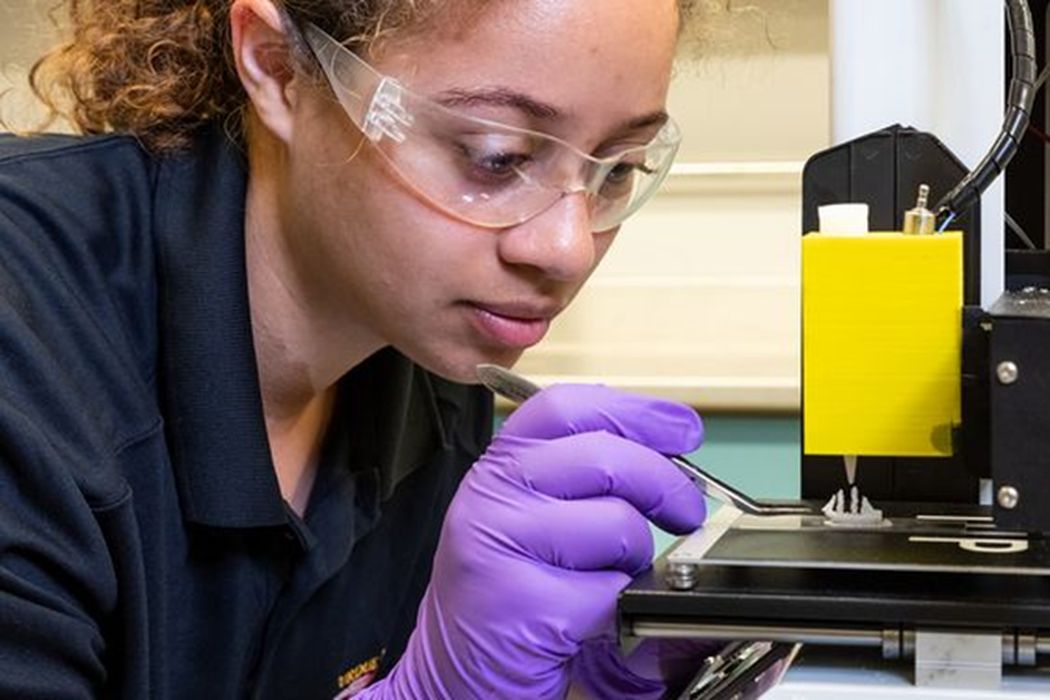
So, the team collaborated with Associate Professor David Staack to generate a beam of charged air particles, or plasma, that could carry an electrical charge to the printed part’s surface. This technique enables the currents to pass through the printed part, heating the nanotubes and welding the layers together. All while not overheating the part or heating irrelevant parts.
Purdue University
3D printing activities at Purdue University include use with its TRAILS project. TRAILS 2.0 offers a place-based learning context that enables students to explore their local environment and connect with STEM professionals from their region. The program promotes 3D printing as enhancing student learning by providing tangible, real-world student design projects to provide opportunities to test and analyze products, refine and redesign quickly, and replicate final solutions.
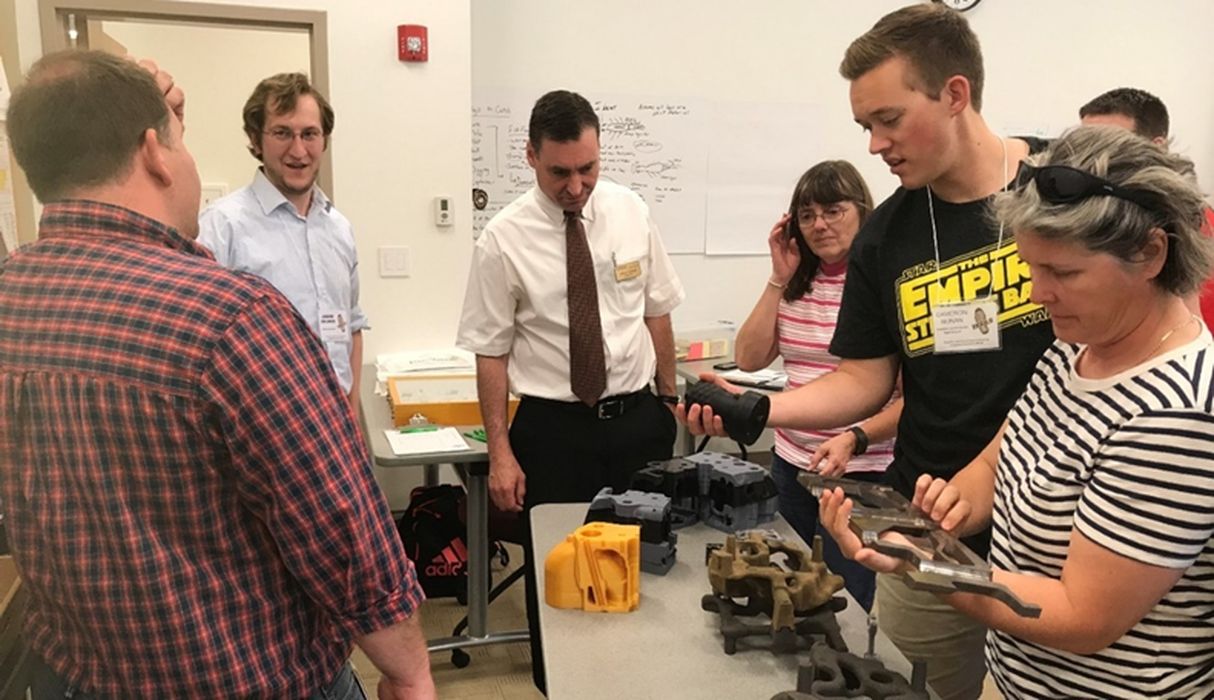
In fact, the Purdue Rapid Prototyping Laboratory has a range of FDM 3D printers suitable for prototyping complex designs. The 3D printers at the lab include Lulzbot, MatterHacker and Ultimaker.
The Research & Development Tax Credit
The now permanent Research and Development (R&D) Tax Credit is available for companies developing new or improved products, processes and/or software.
3D printing can help boost a company’s R&D Tax Credits. Wages for technical employees creating, testing and revising 3D printed prototypes can be included as a percentage of eligible time spent for the R&D Tax Credit. Similarly, when used as a method of improving a process, time spent integrating 3D printing hardware and software counts as an eligible activity. Lastly, when used for modeling and preproduction, the costs of filaments consumed during the development process may also be recovered.
Whether it is used for creating and testing prototypes or for final production, 3D printing is a great indicator that R&D Credit eligible activities are taking place. Companies implementing this technology at any point should consider taking advantage of R&D Tax Credits.
Conclusion
Recognizing that buildings make up a large portion of energy usage, the US federal government is providing substantial funding for heat pump technology development. Appropriately, the funding specifically includes 3D printing technology development. The 3D printing industry needs to optimize this participation and bring all its improving expertise to this major initiative.