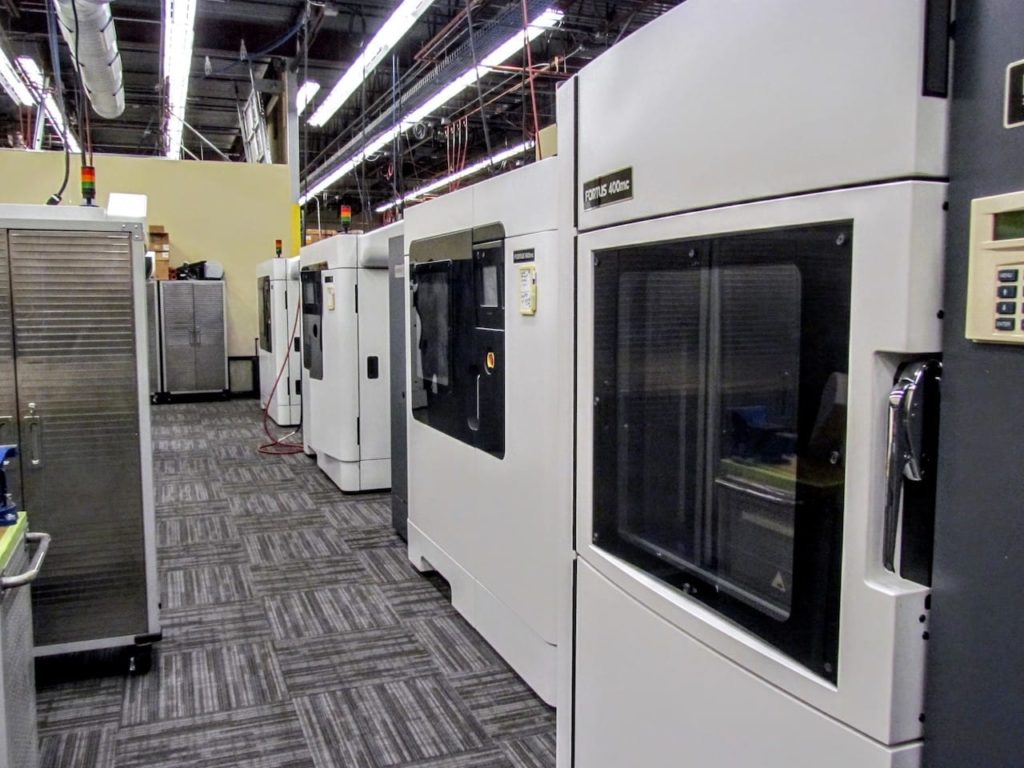
Moving to additive manufacturing has been quite a challenge for many companies, but perhaps there’s another perspective.
Manufacturers, if they’ve been around for any length of time, already have an existing process to produce their products. This workflow includes the design of the product, as well as the actual manufacturing. Those experienced with 3D printing technology know that the two are tightly interlinked if one hopes to use the technology effectively.
In fact there’s been an entire discipline developed to ensure this partnership remains tight: DfAM, or “Design for Additive Manufacturing”. It’s a way of designing parts to ensure they will not only be 3D printable, but will exploit the advantages of the technology and avoid its pitfalls.
However, that’s definitely not where most manufacturers start with 3D printing.
Most typically they simply view a 3D printer as “another making machine” and attempt to reproduce an existing part design. That’s the simplest thing to do, but it also provides the worst result.
The best one could hope for in such a test is a complete part, but one costing far more than one made using the former process. Any manager observing that scenario would immediately declare AM technology to be “too expensive”.
That’s how many AM adoption scenarios unfortunately end.
Some may go further by redesigning the original non-AM part. Tweaks to the design may enable it to be properly 3D printed. Walls may be made thicker, overhangs adjusted, etc. However, the result is still going to be pretty much the same: a more expensive part that took too long to produce.
“Too Expensive.”
The best way forward is to continue using the traditional approaches to produce the older parts, and instead start from scratch on a completely new part. Even better, start design for a part that in the past was rejected because it was “impossible to produce”.
Those ventures are where the money truly lies in additive manufacturing: impossible parts. They may make use of incredibly complex internal lattice structures to lighten the part considerably. Or they may involve geometry that would be difficult to produce using injection molding due to overhangs. Or they may be a larger part that was previously made from several smaller parts and joined together — done that way because older making technologies could not produce the complex part.
Those are the ways of success in AM.
Back to the “expensive manager” problem.
What if at that stage the problem were reversed? What if you had a highly complex part and it was proposed to make it using, say, CNC milling?
Impossible! Expensive! Time consuming!
Those are the same words heard when AM is proposed, except in reverse.
The truth here is that there are two kinds of parts: those that are best for 3D printers, and those that are not.
Choose your machine wisely.