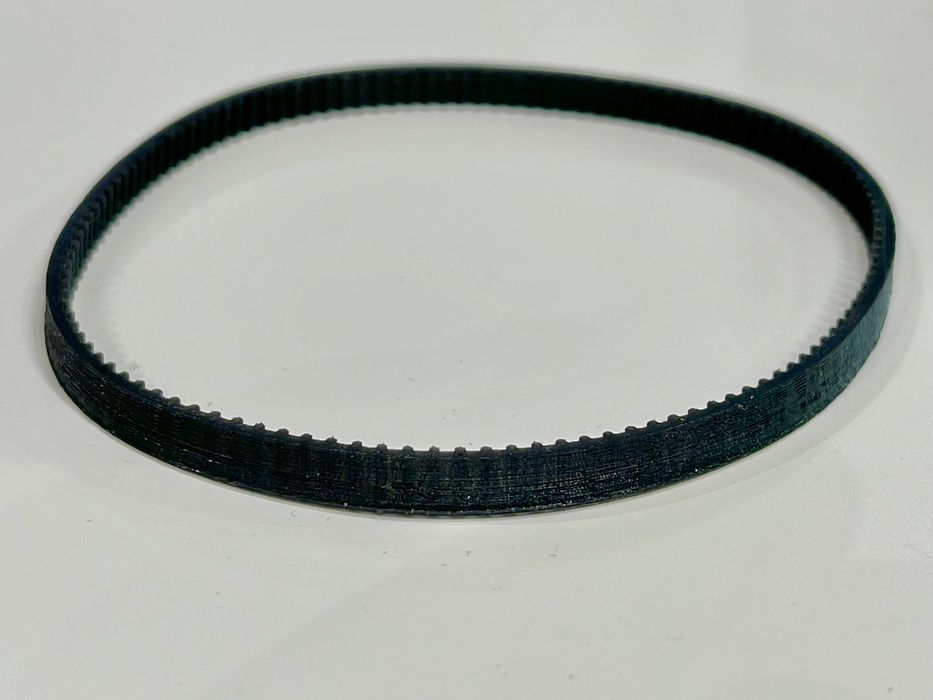
Iām impressed with the 3D prints that can be made with BCN3Dās new VLM process.
BCN3D, a long-term 3D printer manufacturer of FFF equipment, suddenly announced āVLMā earlier this year, a process entirely different from their traditional equipment.
āVLMā is an acronym for their new 3D printing process that stands for āViscous Lithography Manufacturingā. The company spent three years in secret developing the new process, and itās one that will dramatically change their future.
VLM uses a photopolymer reaction to fuse materials together, as do many other 3D printing processes, but other processes have a big limitation.
Typical processes such as SLA, MSLA and similar methods rely on the flow of liquid resin to quickly refill so a subsequent layer can be 3D printed. This implies that the resin cannot be particularly viscous, otherwise that flow canāt happen. More advanced systems actually include heaters to āsoften upā the resins to make them flow, but there are limits to that approach.
Thatās a big problem material-wise, because the most interesting photopolymer resins are infused with particles to create material properties. The more particles, the more interesting is the resin.
In other words, you canāt always make strong or durable parts with traditional photopolymer processes.
VLM overcomes those limitations by using a very different approach to apply resin. Hereās how it works:
- A transparent film is passed through resin, causing a thin layer of the resin to stick to the bottom of the film
- The film is shifted into the build chamber and tensioned to be perfectly flat, still holding the wet resin on the bottom
- The build plate moves upward to come in contact with the film. For further layers, only the solid portions of the object come in contact with the film
- From above a LED/LCD panel UV light source selectively illuminates the transparent film, solidifying portions of the resin
- The build plate lowers slightly, peeling the freshly printed layer off the film
- The film, now having only unused wet resin on it, slides back out of the build chamber where the resin is recovered and made ready for subsequent layers
- The process repeats, layer by layer
The wonder of VLM is that the process allows for the use of very viscous resins: there is no need for liquid flow as the resin is directly deposited uniformly on the film. Apparently BCN3D can even perform multimaterial resin 3D printing with VLM.
This means that VLM can use materials that are far stronger and, frankly, more interesting than the typical set of 3D printer resins that are in general use on SLA and MSLA equipment.
But how tough can these materials be? Recently I saw some examples in person, and I was quite impressed.
At the top we see one of them, a 3D printed belt for use in a mechanical system ā perhaps even a 3D printer. The materials are apparently sufficiently strong to be used in such an application. This capability also takes the āRepRapā concept a little bit further, as a 3D printer could print another type of part for itself.
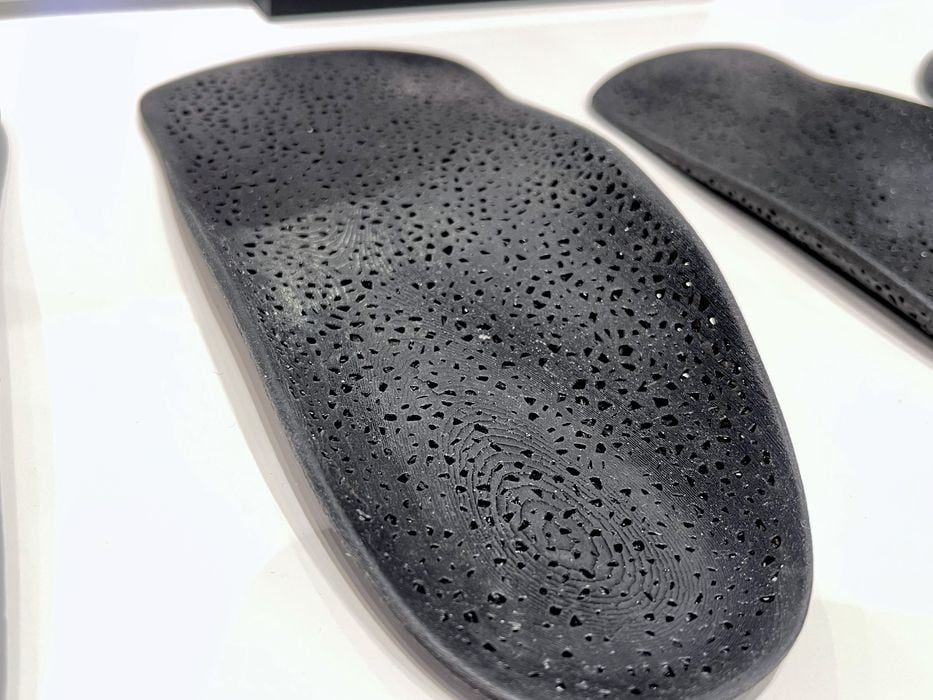
Hereās another example, a support insole for footwear. This is a part that will literally take a beating, all day long. Every footstep will deform the part, and it has to spring back to its original geometry.
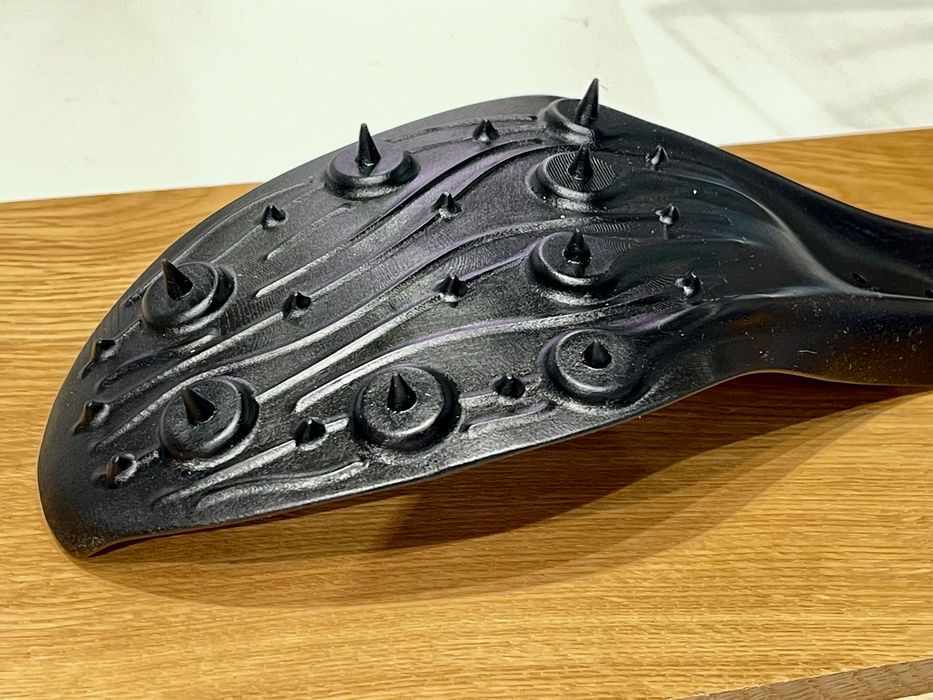
Another example is this footwear outsole, which will be in contact with the ground, incurring constant impacts.
These are the new, meaningful 3D print applications that can be enabled by VLM.
One could say that VLM is quite āimpactfulā.
Via BCN3D