
Sinterit has updated their 3D print job preparation software with a powerful feature.
Only weeks after introducing a new polypropylene material, the company introduced a new capability in their slicing and print management software, Sinterit Studio: automated nesting.
SLS 3D Printing Advantages
Before getting to the new feature, we must first understand a bit more about how their SLS system works. SLS is a powder-based process in which a laser selectively fuses powder layer by layer to build up an object.
As the job proceeds, the prints are naturally surrounded by unfused powder, which provides implicit support to loose model components. This eliminates the need for support material, but also provides for an unusual property not available in other 3D printing processes: stacking.
Virtually all other 3D print processes are limited to one “layer” of parts. That is, you cannot stack parts on top of each other in FFF, SLA or other non-powder processes. While the game in those processes is to ensure there are parts covering the two-dimensional area of the print plate, it’s quite different with powder 3D printing.
In SLS 3D printing the game is to fill the complete three-dimensional VOLUME of the print chamber, not just a two-dimensional print area.
You can thus fill the build chamber from top to bottom and then run the long print job overnight to completion. The next morning an operator simply digs out all the parts from the build chamber that’s then filled with powder.
This is a very economical approach to 3D printing because you can push through more parts per each job. Because every print job has some amount of manual effort required, you can reduce that labor by increasing the number of parts in each job.
This effect has led many service bureaus to squeeze the maximum efficiency of their SLS equipment by “Tetrising” in parts as tightly as possible. Initially this was done manually, and what a complex job that was!
How many possible combinations of orientations could be made in a large build chamber? Well, the answer is “lots”. Usually manual efforts were noble, but often did not achieve the maximum part density.
Advanced systems for much more expensive systems emerged that could perform the tricky process of determining an optimal three-dimensional arrangement of parts, but this capability has been difficult to find in lower-cost SLS systems.
Sinterit Auto Nesting
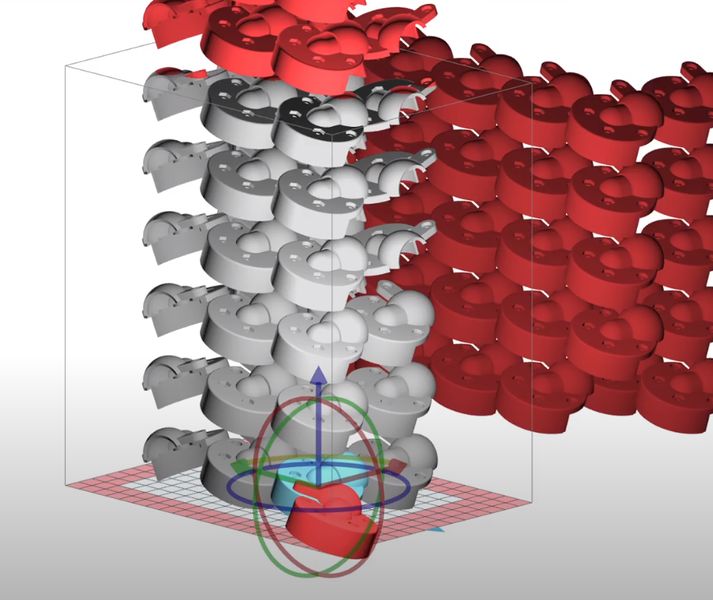
Enter the new Sinterit Studio, which now includes “Auto Nesting”. This feature can prepare a fully-utilized build chamber. Sinterit explains:
“With the auto-nesting feature available in the new version of the Sinterit Studio, Lisa and Lisa PRO users could simply pack the Print Bed with prepositioned models. It significantly shortens the time of build preparation and saves hours of work on precisely re-positioning each model individually. What is even more important, it decreases printing time and material cost per build and per part.”
This feature will be of particular interest to anyone using Sinterit equipment for serial production. It may even be possible to significantly reduce operational costs by more optimal print packing.
Open Materials
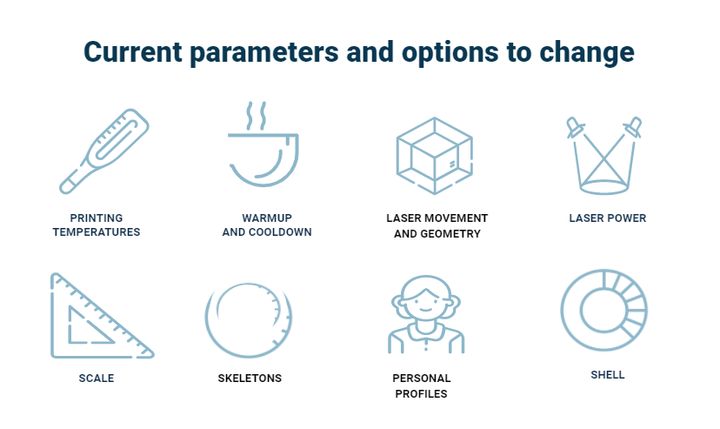
That’s not all. The new Sinterit Studio also includes increased abilities to manage open materials. While many 3D printers use proprietary materials in an effort to ensure ease-of-use and customer print success (and sometimes increased pricing), there are some operators that must use unusual materials.
They could be research laboratories, or perhaps advanced educational institutions that for one reason or another have to compose their own powder mixes.
Fortunately, Sinterit Studio can now completely handle this situation. It provides the ability to directly affect multiple print parameters, including temperatures, timing, laser movement and power, and much more.
A dedicated operator could then slowly dial in the correct print parameters for any given powder mix. This enables these operations to successfully use unusual — and sometimes secret — materials for their own purposes. Sinerit explains:
“With the open parameters feature Sinterit gives users full control over the printing process. They can modify 4 heating zones settings with a total of 22 heating elements placed in the Lisa and Lisa PRO printers. This gives users many options to modify and adjust parameters to their needs. As a result, researchers or academics can optimize the printing process for developed materials or test new research methodologies.“
This makes the Sinterit equipment one of the few viable choices for the powder research market.
Via Sinterit