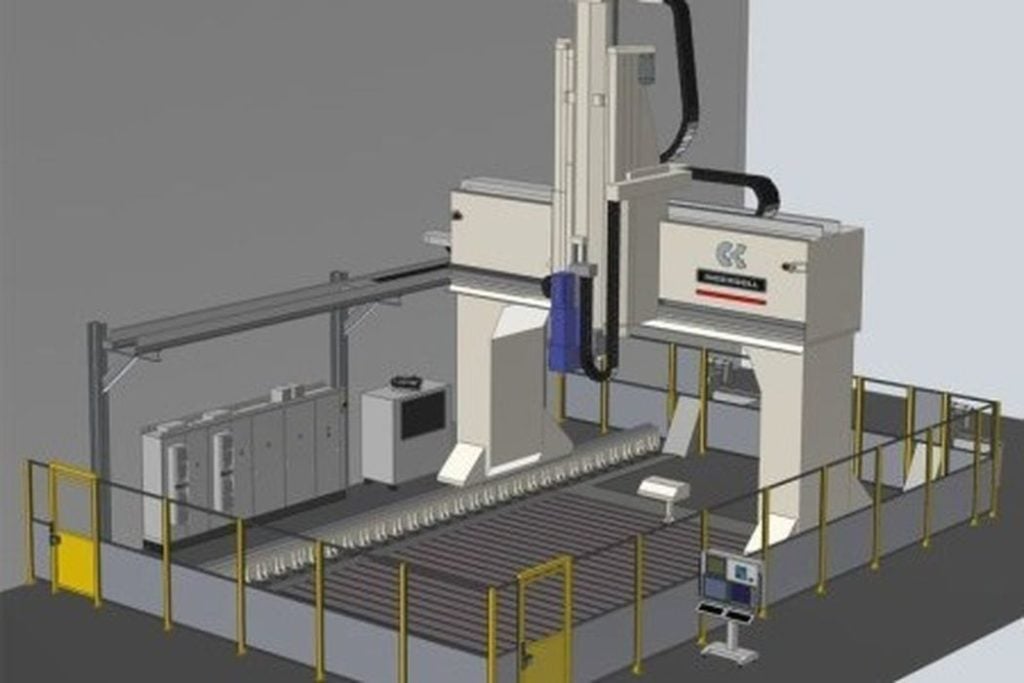
The US army has awarded a contract to a group to construct what will likely be the largest metal 3D printer ever built.
Specifically, the DEVOM Army Ground Vehicle Systems Center (GVSC) is interested in 3D printing the metal hulls for several types of advanced ground vehicles.
They’ve contracted ASTRO America, a non-profit, US government-sponsored research organization as the prime contractor. They’ll in turn be working with subcontractors Ingersoll Machine Tool, Siemens and MELD Manufacturing.
The targeted print volume for the unnamed device is said to be 30’ x 20’ x 12’ (9144 x 6096 x 3658 mm, but millimeters are a poor measure at this scale). That print volume should be sufficient to build many different styles of ground vehicle hull.
One can understand the presence of Ingersoll Machine Tool and Siemens in this team, but why MELD Manufacturing? What makes them appropriate for this job over other more well-known 3D printer manufacturers?
The most typical metal 3D printing processes are PBF-based, where high energy is used to selectively solidify particles in fine layers of powder. However, in order to make the process work properly the build environment must be completely purged of oxygen and humidity to prevent explosions and ensure print quality.
While there have been relatively large PBF systems built, none are anywhere near the scale of the US Army project.
The reason for that not happening is that it would be extraordinarily expensive to build a sealed chamber of that build volume, which would have to be repeatedly filled with inert gases. It would be quite impractical.
Another possibility for the US Army project might have been DED or WAAM, where a robotic system wields a welding toolhead to gradually deposit material. However, as high temperatures are involved in the process, it’s possible the selectors were concerned with part quality and thermal complications.
Two other processes would be worthy of consideration for this project. One would be SPEE3D’s supersonic 3D printing process, where fine metal particles are blasted towards a target at supersonic speeds. The particles adhere together and gradually accumulate into a complete part. No high temperatures are required, as the particles’ kinetic energy is sufficient to bind them together.
However, it seems that they instead selected MELD Manufacturing, which uses an unusual solid state 3D printing process. The idea behind their process is that identical metal molecules, when adjacent to each other, will automatically bind and become a single object.
Then why won’t two pieces of metal bind together when touching? It’s because every metal surface is coated with other materials, typically oxides, that prevent the binding from happening.
However, MELD Manufacturing’s process involves a rotational print head that jams the incoming material against the print surface repeatedly in a circular motion. The oxides are worn away and the metal binds perfectly.
This process deposits metal reliably and quite rapidly, but the results are rather coarse compared to what you could obtain from a PBF process. The best part is that no high temperatures are used, and thus the resulting parts are of exceptionally high quality due to the highly effective molecular binding.
It also does not require any special chambers, inert gases, high energy lasers or high temperatures. You simply need to rotate the toolhead and move it around, which should require a minimum of electricity.
You can see how the process works in their short introductory video here:
The US Army project calls for a smaller version of the eventual device to be first built as a pilot project, followed by the full-size device later. That’s an excellent idea that can reveal design issues in this unprecedented device.
Once complete, the US Army will be free to build all kinds of unusual uni-body vehicle hulls that include unusual geometries not easily made with other technologies.
For MELD Manufacturing, this project could represent a breakthrough in the market. If the huge 3D printer proves worthy, then it may be that other clients will become interested, resulting in many more sales.
Via US Army