
voxeljet announced the first beta client for their VX1000 HSS system.
The companyās HSS process is quite interesting. The acronym stands for āHigh Speed Sinteringā, and they arenāt kidding.
Itās a curious process that is a combination of binder jetting and SLS processes. HSS is a powder process in which layers are produced successively. However, the manner in which the layers are produced is unique: a special liquid is selectively dropped on the powder surface by a rapid-pass arm. Then, an infrared light source blasts energy into the build chamber onto the current layer. The binder jet liquid absorbs the energy and heats up. The heat is sufficient to sinter the thermoplastic powder particles together. Meanwhile, dry powder remains unsintered and loose.
There are a couple of very intriguing advantages to HSS.
First, the infrared energy can be applied to the entire layer at once. This is much faster than tediously tracing a laser across selected areas of the layer. The liquid deposition can also be quite rapid, based on high-performance inkjets.
Like other powder processes, there is no need for support structures, because overhangs are supported automatically by surrounding powder. This makes post processing quite a bit simpler than is found with several other popular 3D printing processes.
The process can produce highly detailed objects, as the resolution is largely proportional to the size of the liquid droplets. However, the process can also be scaled up significantly in size, and this matches voxeljetās traditional huge build volumes.
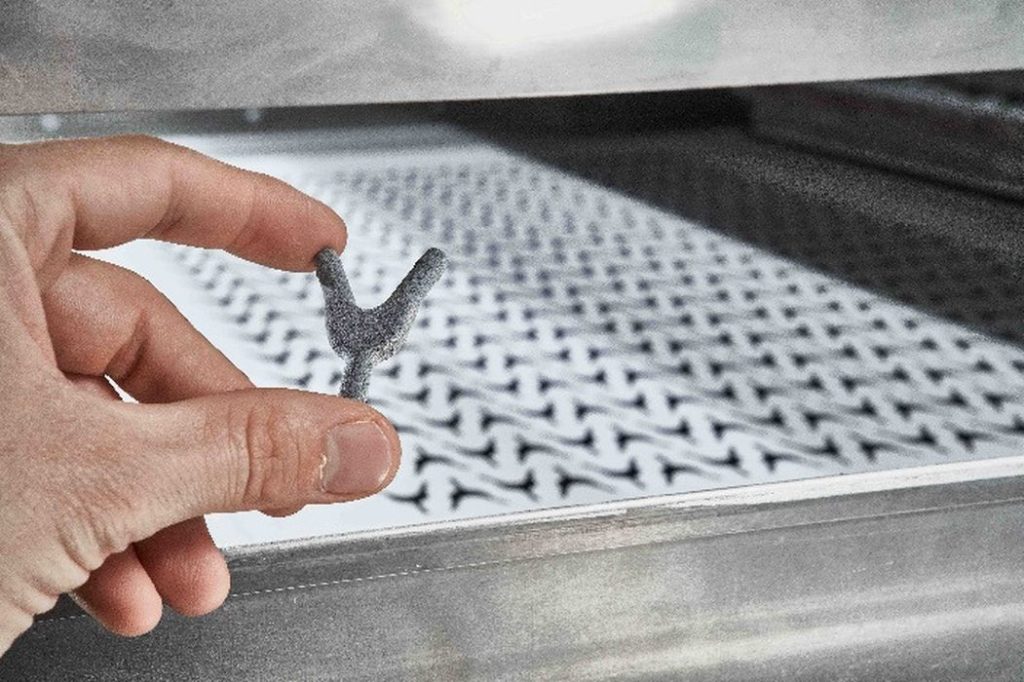
voxeljet announced HSS technology some years ago, but now we find their client, automotive supplier Brose, is the first in their early-access beta program for the VX1000 HSS 3D printer. voxeljet explains:
āThe aim of the HSS Beta Program is to test the features and capabilities of the VX1000 HSS in an extensively designed program for use in industrial production environments. After a joint three-month development phase at voxeljet’s headquarters in Munich, the system will be moved to the Brose Additive Manufacturing Center in Coburg, integrated into the production environment and optimized for customer-specific applications.ā
What, exactly is Brose doing with the VX1000 HSS? It seems they are organizing a digital inventory, where digital models of required parts are stored and printed when necessary, instead of mass manufacturing and warehousing spare parts years in advance. Digital inventory is vastly more efficient than traditional approaches to spare parts.
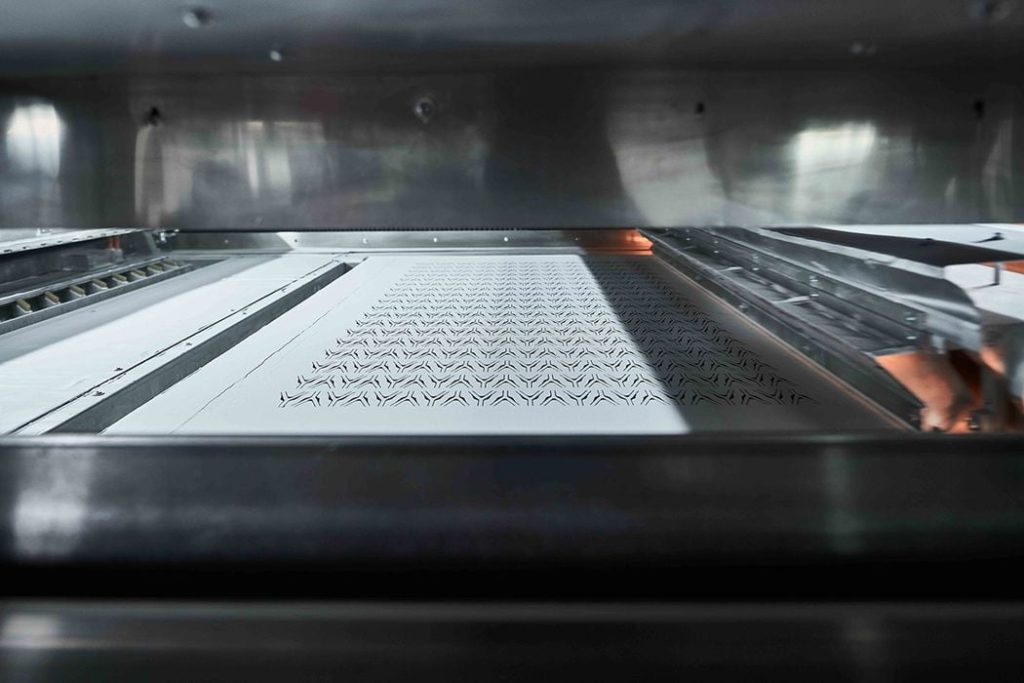
Broseās Christian Kleylein explains:
“Sustainability is a top priority at Brose. Thanks to additive manufacturing, tools for āend of lifeā components no longer need to be stored and spare parts pre-produced, but can be stored digitally and retrieved and printed on demand. With the HSS technology and its high printing speeds, we can begin to reduce physical storage for both tools and spare parts.ā
Apparently the system allows Brose to 3D print entire door sections on demand, as the build volume on the VX1000, 540 x 1000 x 180 mm, is large enough to do so.
Imagine being able to rapidly 3D print parts of that size rather than having to pre-produce thousands and store them in warehouses for years just in case they are needed. Digital Inventory is a breakthrough technology that eventually will be used by most manufacturers.
Via voxeljet