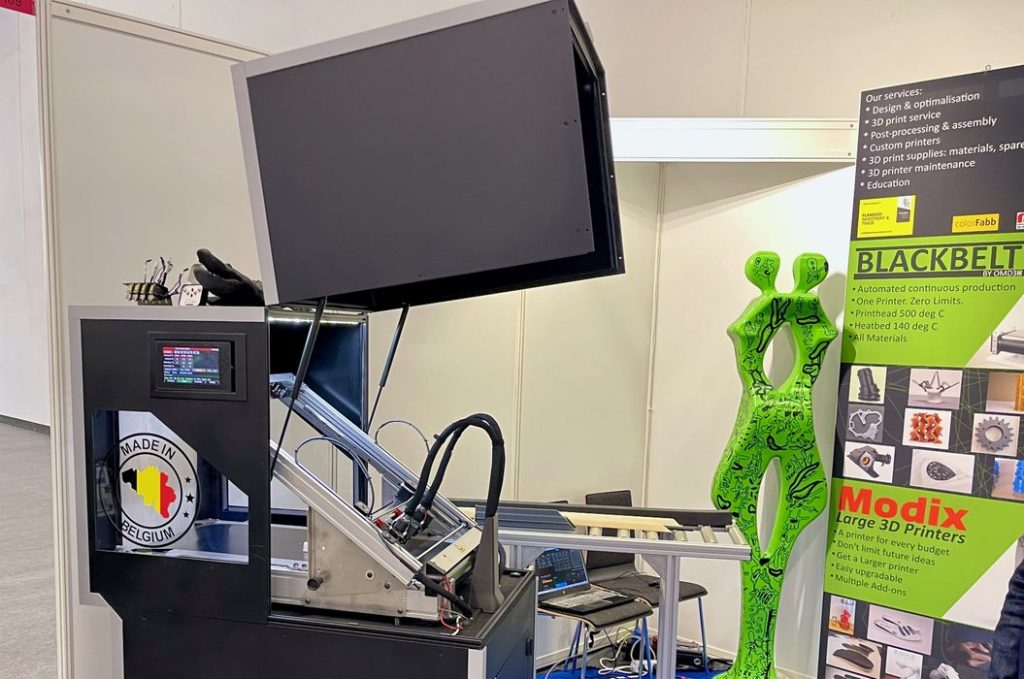
There’s an interesting tale about the Blackbelt 3D printer, the first successful belt 3D printer.
Belt 3D printing differs from typical FFF 3D printing in that the print surface is a moving conveyor belt. The print head is angled at 45 degrees, and therefore prints objects with angled layers and require far less support material. However, the belt approach means very long objects can be made, far larger than the printer itself. Alternatively, belt 3D printers can continuously produce smaller items that roll off the belt into a bin for low volume production.
The concept was first proposed a long time ago by a MakerBot fan, back when that company still was in open source mode. The concept was implemented as their “Automated Build Platform”. I actually tested this item over ten years ago, and it actually worked — until the belt warped due to heat after a few runs.
The concept mostly disappeared for a few years, but then re-emerged as a commercial product, the “Blackbelt” 3D printer around 2017. This system solved the belt problem and produced a device that actually worked properly. Although high-priced, it was a very novel product, and we wrote a history of the project in 2018.
In the interim a number of alternative belt 3D printers have emerged, including PowerBelt 3D, the open source TigTag, the White Knight, and most notably, Creality’s 3DPrintMill.
But since 2018 there wasn’t very much news from the Blackbelt3D, and it turns out there was a reason for this.
The gang that originally designed the Blackbelt 3D printer focused more on a different product from PodoPrinter.
Hold, on which company is which here? It turns out there are a number of individuals associated with Helian Polymers, colorFabb, Blackbelt 3D and PodoPrinter, all at the same address in The Netherlands, which we looked at in 2020.
PodoPrinter produces a specialized 3D printer, the SOLE, which is used to produce custom insoles for footwear. It’s a belt 3D printer mounted vertically, but specifically designed for footwear applications. It would appear that belt knowledge from the Blackbelt 3D project assisted in the development of the SOLE 3D printer.
Evidently these folks felt the market might be stronger for the footwear printer, so focus on the Blackbelt 3D project decreased.
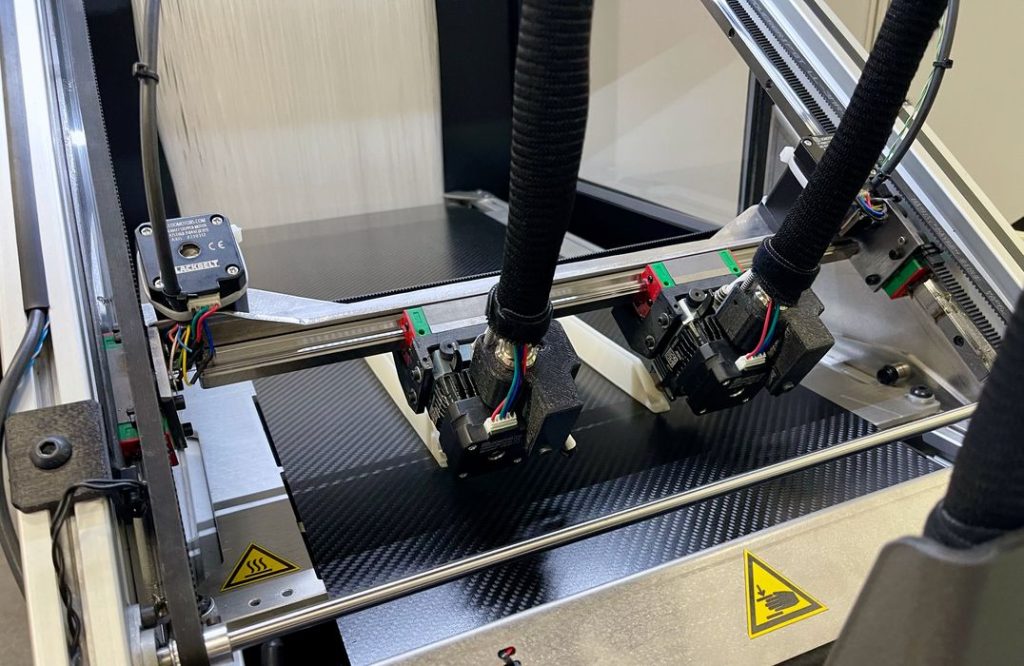
Enter OMD3D, the largest reseller of Blackbelt 3D printers, which had a very strong relationship with the company. Based in Belgium, OMD3D made an arrangement with the other parties to take over the Blackbelt 3D project, and even share patents.
As of now, OMD3D makes and sells Blackbelt 3D printers.
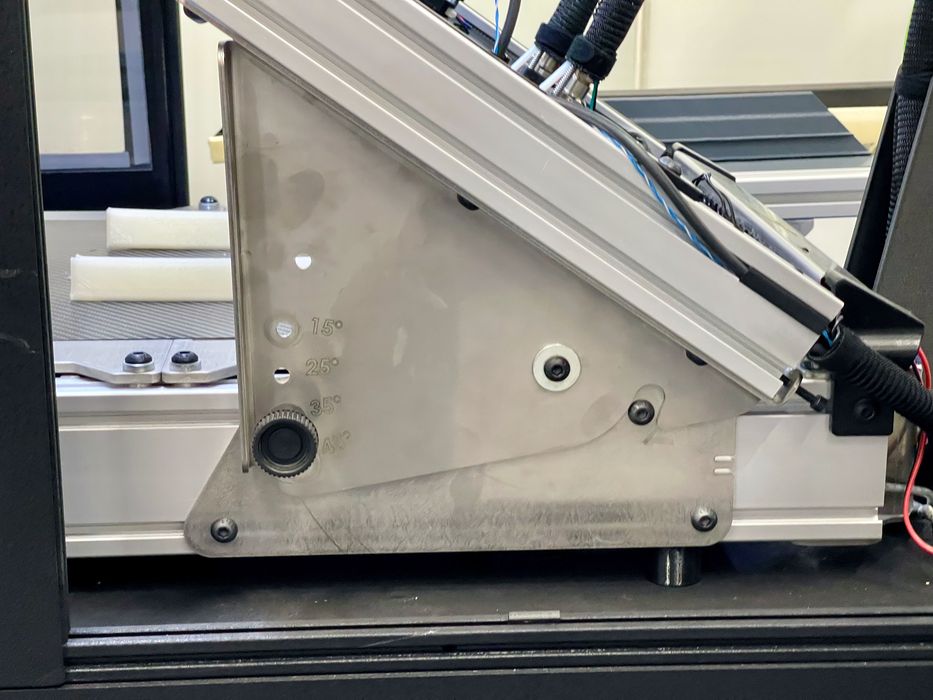
But it’s more than just selling. It turns out that OMD3D has been making some very significant improvements to the Blackbelt 3D printer. We had a discussion with OMD3D representatives, who explained they’ve done the following:
- Added a new, dual independent extrusion system (IDEX)
- Added an actively heated build enclosure
- Enabled use of advanced composite materials (PETG-CF)
- Ability to 3D print flexible materials
- Hot end can hit 500C, able to 3D Print PEKK
- Using DUET, not RAMBO controller board
- Developed “macros” for standard procedures, setting temperatures, etc.
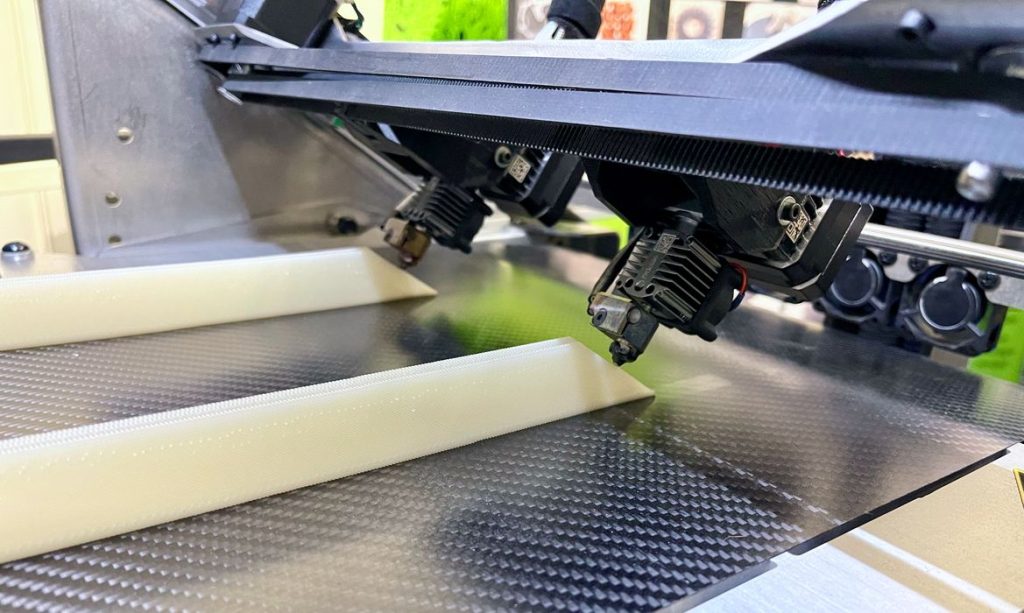
I asked about the extreme heat and how that would affect the belt, given my previous experience with the MakerBot device. It seems that the belt is made from a single material, PE, and is only 0.8mm thick, enabling very good heat transfer and no degradation. This means that prints should stick, even at very high temperatures.
It seems that the Blackbelt 3D printer is far more capable than it was previously. The ability to 3D print many more engineering materials, particularly carbon fiber, will be extreme interest to those performing low volume production of end-use parts.
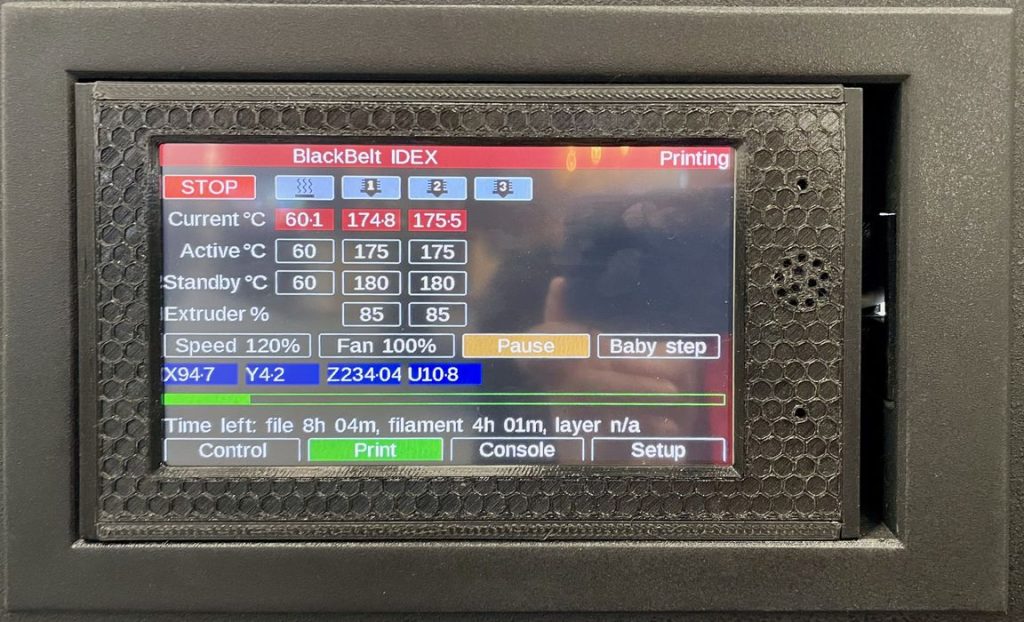
The high temperature materials are even better, particularly when combined with the IDEX system, which can supply soluble support material. That would enable the Blackbelt 3D printer to produce continuous streams of very strong, complex parts.
That’s a unique capability among belt 3D printers.
Via Blackbelt 3D and OMD3D