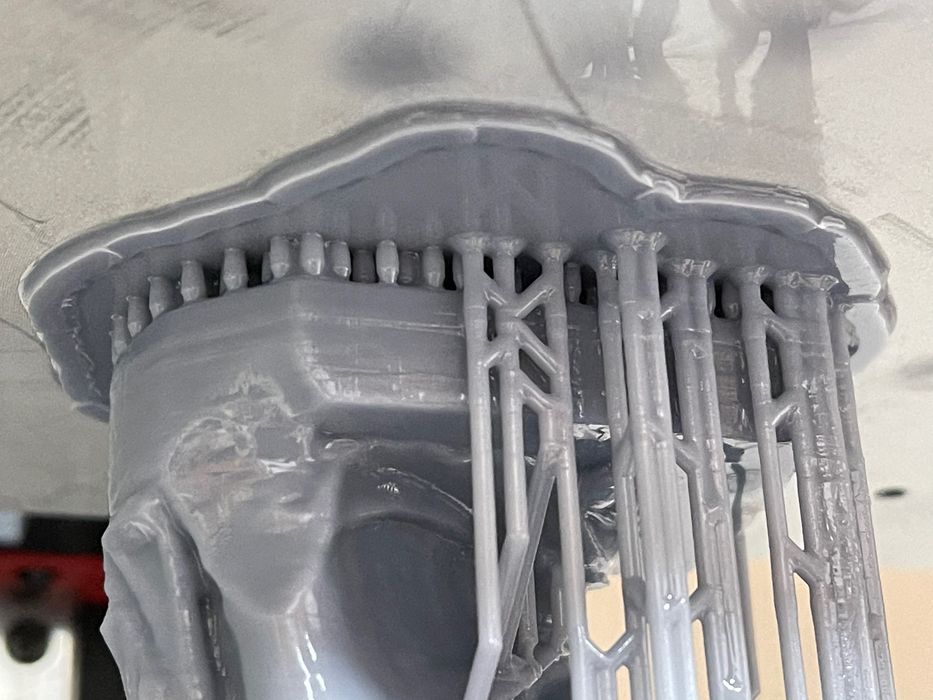
Support material is support material. Or is it?
Anyone who’s done any 3D printing very likely has had to deal with support material. It’s those extra bits that hold up unsupported areas that would otherwise collapse during 3D printing.
Almost all 3D printing processes require support material, aside from powder-based processes where the support is provided by surrounding non-polymerized powder.
For the rest of us, though, we have to worry abut support structures.
They’re a necessary evil for successful printing, but at the same time cause multiple problems:
- They use up more material
- They can mess up the print’s surface quality
- They lengthen print job durations
- They cause extra (usually manual) effort to remove them
- They sometimes require the purchase of specialty devices for removal
The issue is that the support structures are typically made from the same material as the model itself. Because the act of support requires the two to touch, they bond together. This is why it’s hard to detach support structures: they are literally part of the model.
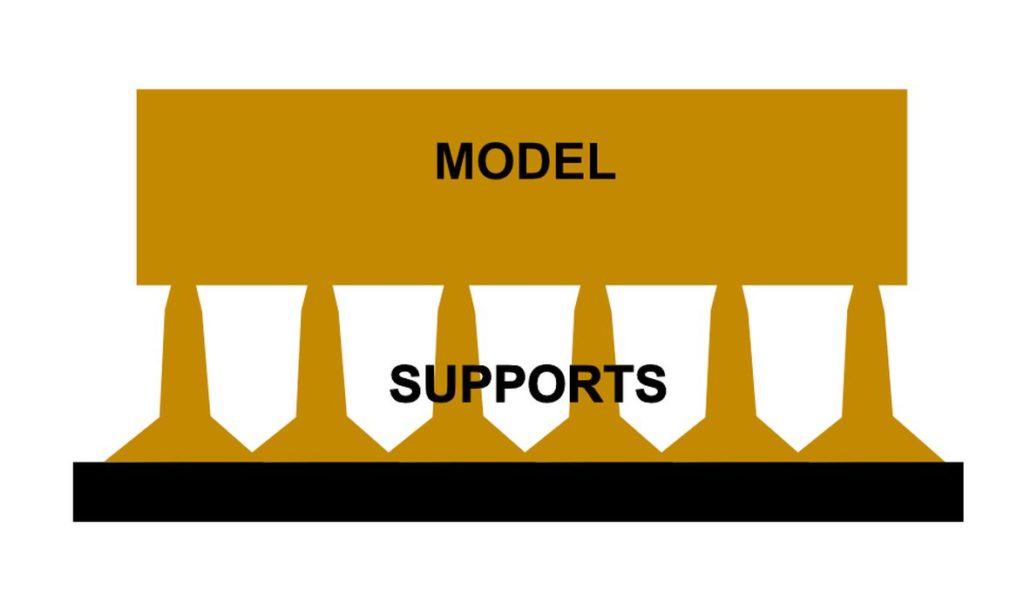
There are ways to reduce the effort of handling support structures in polymer 3D printing, and that’s by increasing the gap between the support structure and the model. This is usually a deeply hidden parameter in the print settings.
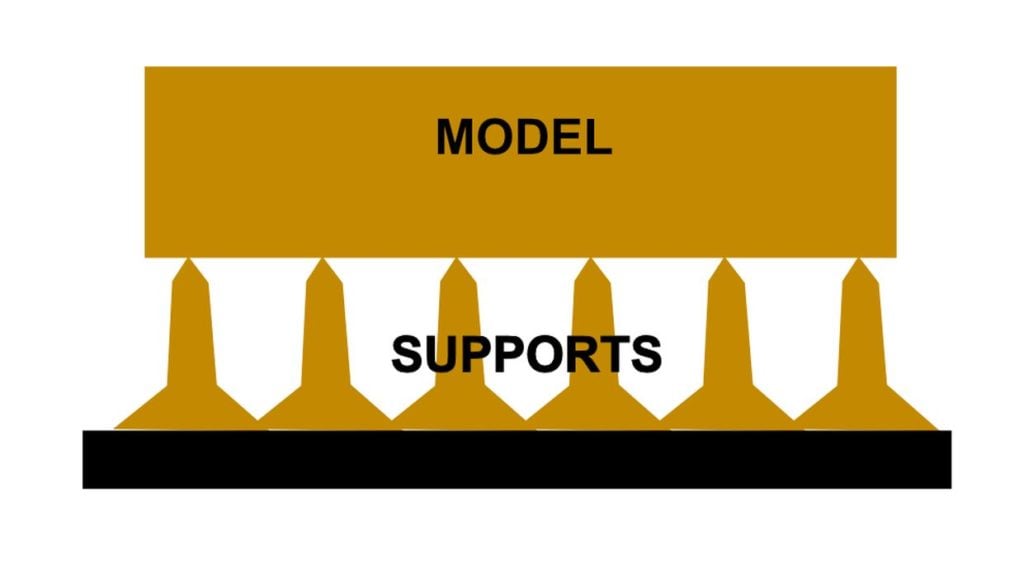
If the gap is increased the amount of material bonding the two together is decreased, making it easier to rip off the support structure. However, if it’s increased too much its job to support an overhang may be compromised.
Another approach is to reduce the density of support structures. For example, instead of having 24 support points on an overhang, maybe 8 will do? But if the density is too low you’ll begin to see “sags” in the unsupported areas.
All these problems are maddening, so is there any way to overcome the support structure problems?
There are two ways. One way is to use soluble support material. That’s a material deposited by a second extruder, and it can be passively washed away after printing. Soluble support material is a great way to tackle highly complex 3D prints where manually extracting support structures would be difficult.
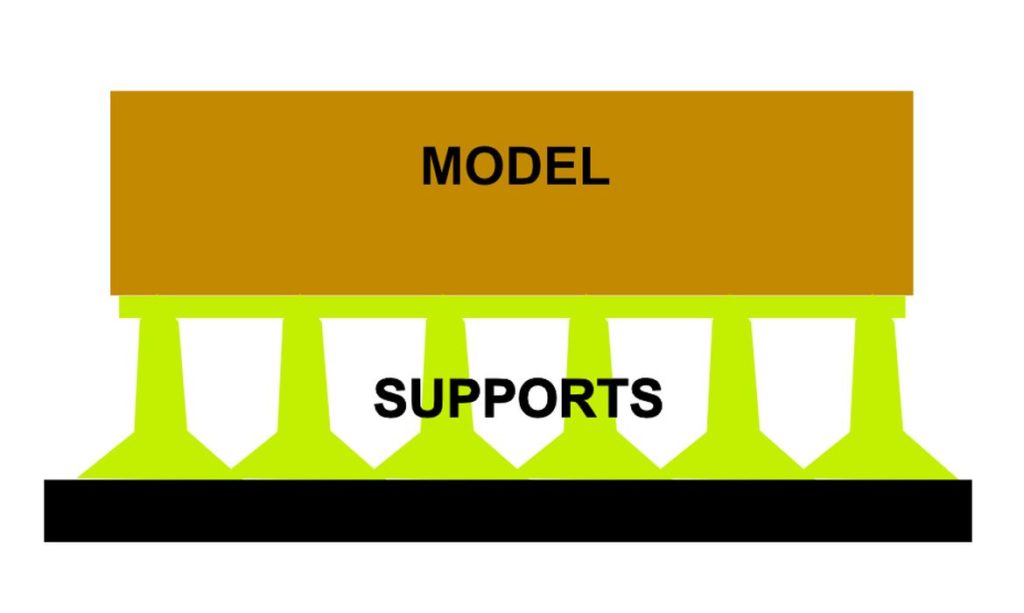
But there is another type of support structure that could be considered: breakaway supports.
Breakaway support is not soluble, and the idea is that you literally pull it off the print with your hands in a rapid manner. Normal mono-material supports can’t always be torn off because they are bonded to the print.
How do breakaway supports manage this feat? It’s all due to chemistry.
The breakaway support is typically deposited by a second extruder and is a different polymer type from the model material. And by “different”, I mean they do not bond together.
This means the support structure can touch the model as much as possible and there is no danger of permanent bonding. Because there is no bonding the breakaway support can be simply lifted off the print. Usually this can be done in seconds, unless the breakaway support is trapped within a void.
A big advantage of breakaway support is that it doesn’t compromise the surface quality of the print. You can actually have the support structure provide a perfectly flat surface to print an overhang, and the overhang will be smooth.
Where do you find breakaway support material? In some cases it’s simply a case of selecting a non-bonding pair of materials. I’ve seen attempts using HIPS as a support material for PLA, for example. The key is to use little support material to avoid it becoming a large rigid object that can’t be pulled off due to geometry constraints.
One company that provides breakaway support in a different way is RIZE. Their support material is in fact the same as their model material, but at the points where the two touch, their equipment deposits a liquid that inhibits polymer bonding. Thus the support and model are completely separate and the support becomes “breakaway”.
For most 3D printer operators soluble support is the way to go, but in some cases where the geometry allows easily broken off supports and production requirements are high, breakaway supports could be the best option.