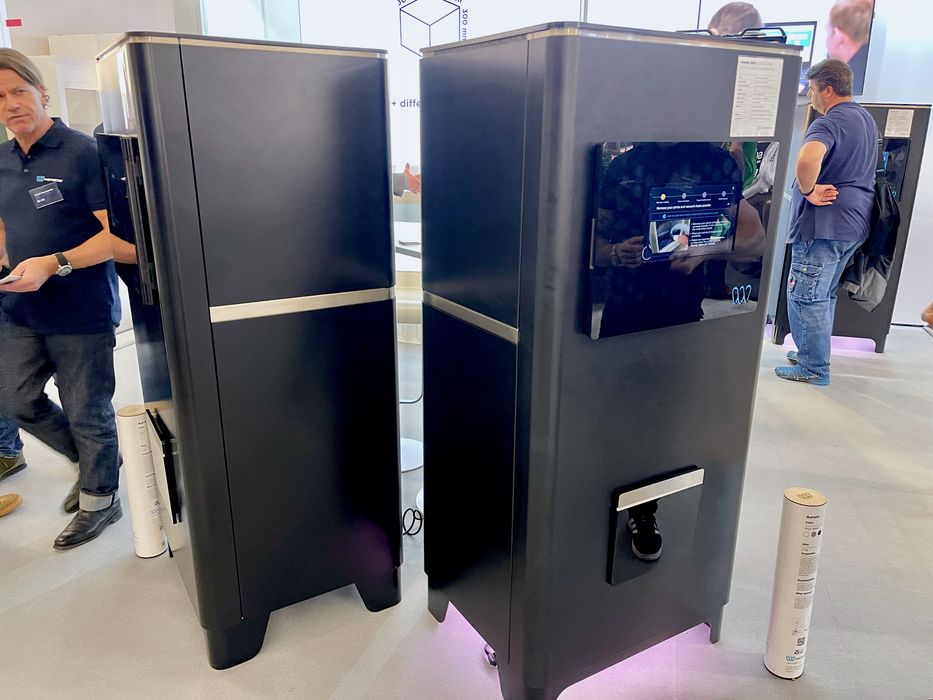
I spoke with Wematter representatives about several things happening with the company recently.
The biggest item is certainly the companyâs agreement with 3D Systems to act as a global reseller for the much smaller Swedish company.
My first question focused on the overlap between the two companiesâ technologies. 3D Systems has long offered SLS systems, while the much younger Wematter also offers an SLS system, the Gravity. Is there room in the 3D Systems universe for both?
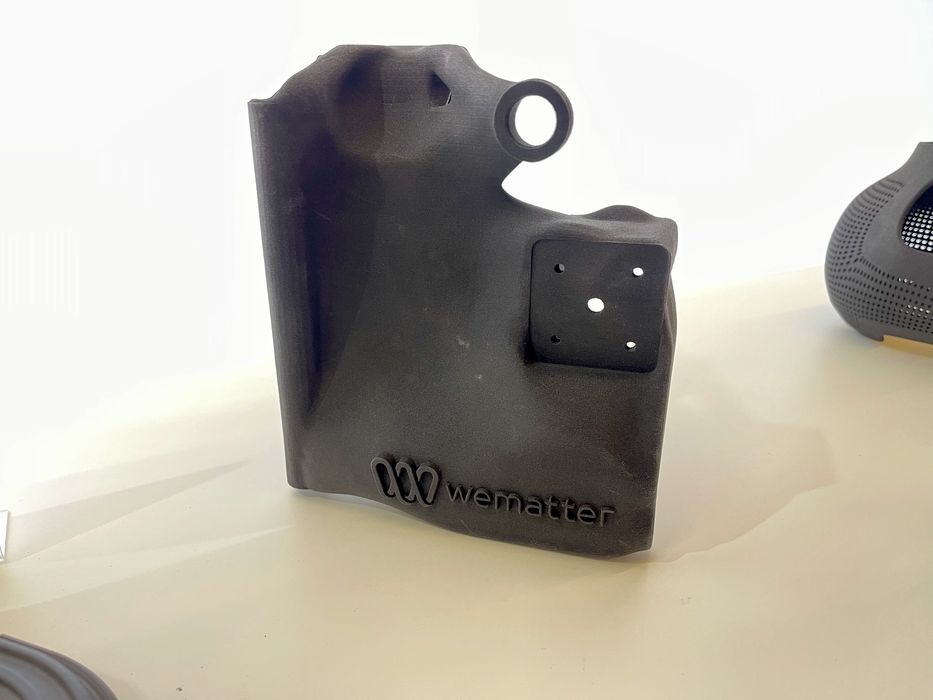
It turns out there is, simply because Wematter addresses a different market segment. 3D Systems tends to sell much larger industrial systems at higher costs to manufacturers, whereas Wematterâs system is much smaller, with only a 300 x 300 x 300 mm build volume. Wematterâs system price starts at only âŹ125,000 (US$132,000), whereas 3D Systemsâ larger SLS systems start at âŹ400,000 (US$423,000).
A price difference of that much is significant, and would enable many more clients to get into SLS technology while still staying within the 3D Systems umbrella. Companies wishing to make prototypes rather than volumes of end-use parts would likely be better served with the Wematter option.
Wematter is a bit different from most 3D printer manufacturers in that they donât actually sell machines. Instead they rent them. This allows the customers to avoid big one-time charges, but also benefits Wematter: they can easily push firmware updates since they own the machine. They can also swap machines out when necessary.
What happens to the swapped out machines? It turns out they are refurbished and then provided to educational institutions. Rather than having a company hang on to an older machine for âtoo longâ, here we repurpose the equipment to help train the next generation of additive manufacturing engineers.
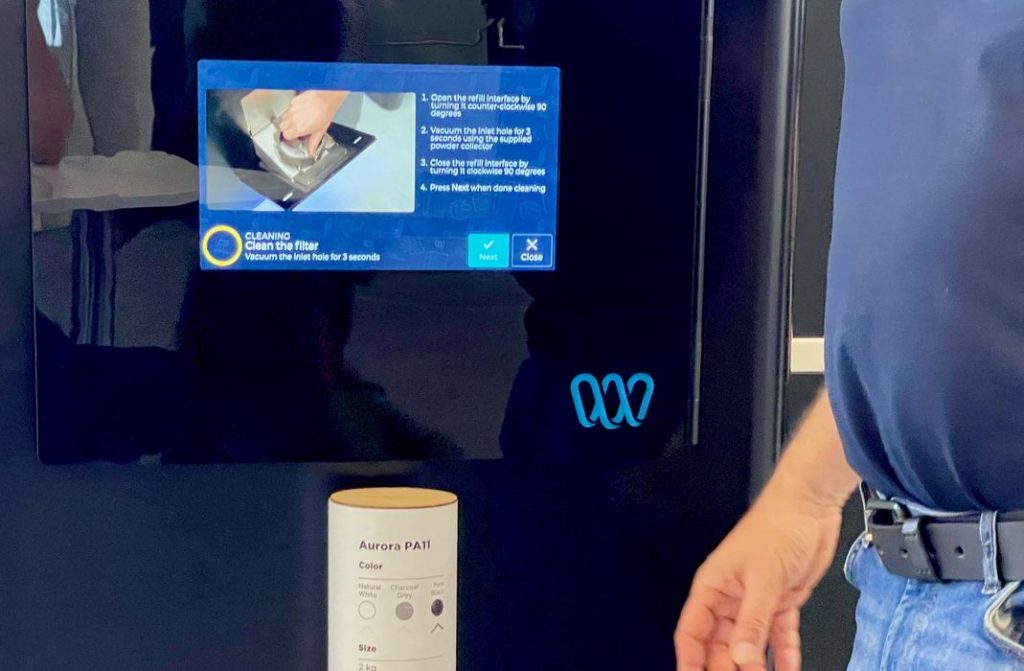
The Wematter concept is to make machine operation as simple as possible. They provide easy to use interfaces, some of which come with instant âwizardsâ and short videos to assist the operator through each procedure. The system also includes âchecklistsâ to ensure operators actually do each of the required steps within procedures.
The powder is secured throughout the entire operational cycle, including the powder cleaning unit. Even the cleaning water is recycled.
The idea is to provide a lower cost SLS system that can be placed directly in an engineering or design office. This avoids the delays that occur when requesting a print from a central facility. Instead, the Gravity can produce the parts overnight without delay.
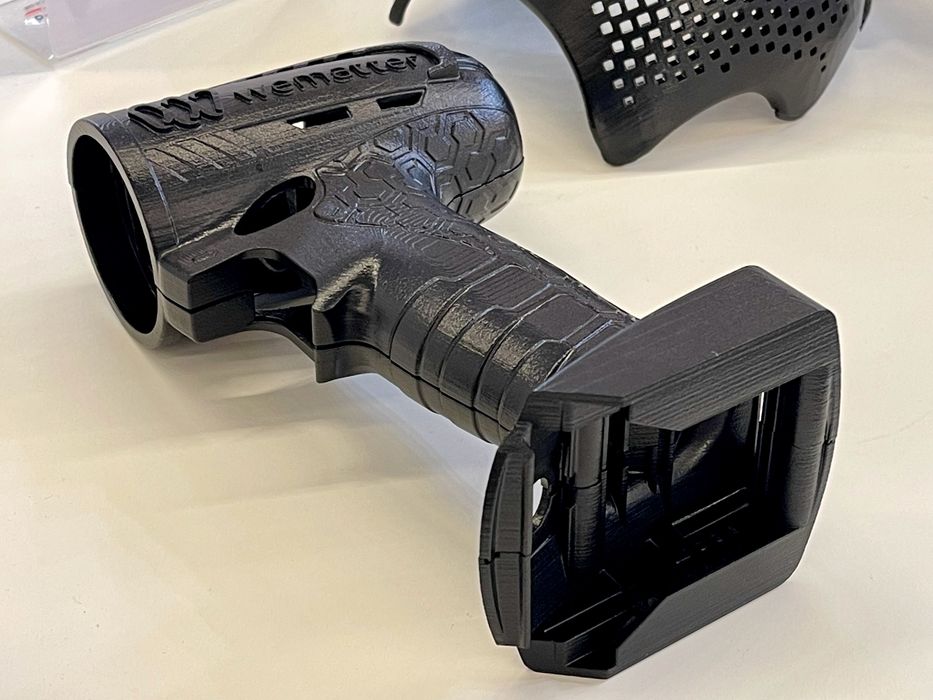
You can see that even if 3D Systems sold their device at a lower price point, thereâs more to the story: the operators have to use the machines effectively.
Typical 3D Systems SLS systems are running 24×7 mass producing parts. They will have dedicated operators that are fully trained on the equipment. However, in the Wematter market scenario, the Gravity operators may be more casual and thus be less familiar with machine operation. Thatâs why the company has taken such a strong focus on ease of use.
Is there an overlap between Wematterâs and 3D Systemsâ SLS systems? Absolutely not.
Via Wematter