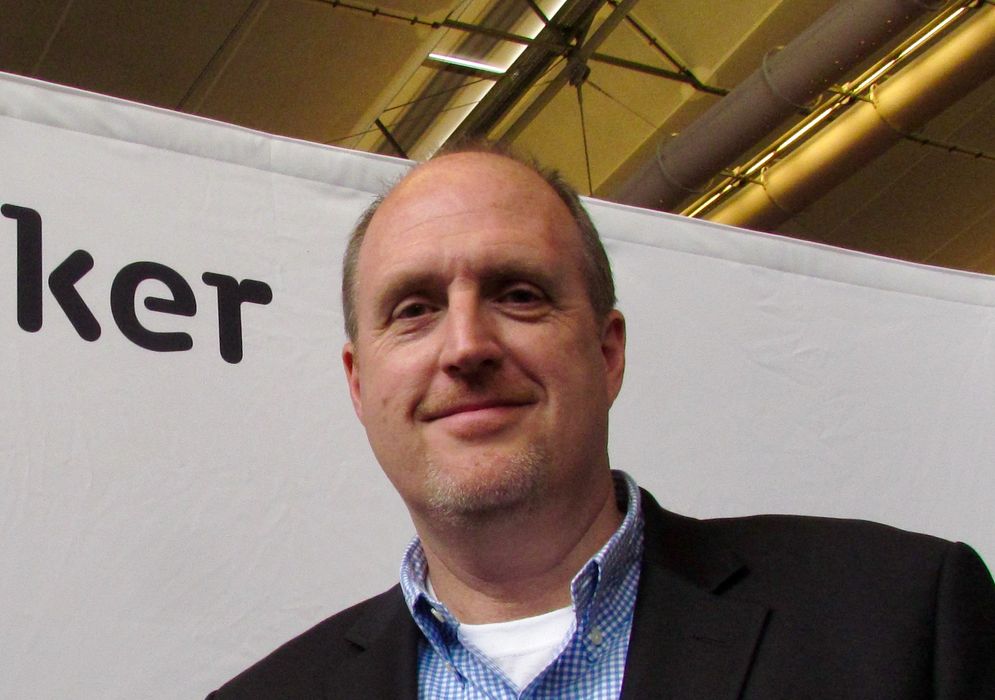
Consolidation, innovation and the drive toward production-ready additive manufacturing could bring another order-of-magnitude change in the industry over the next decade.
You won’t find many leaders in the 3D printing industry with a longer pedigree than John Kawola.
“I’ve been in additive manufacturing/3D printing for about 25 years,” he explains. “I started in the late 90s at a company called Z Corporation, where I was the CEO for my last five years until 2012. I went away from the industry for a few years to work on some other things, but I came back to it when I joined Ultimaker in early 2016 to help them set up their North American business. Now, for the past three years, I’ve been involved with a company called Boston Micro Fabrication, which is focusing on high-precision, high-accuracy and high-resolution applications.”
3D Printing: Then and Now
Between his early days at Z Corporation and today, Kawola has seen the 3D printing industry grow by more than an order of magnitude, both in terms of the number of machines and materials available as well as the number of dollars spent by investors and consumers.
“Back in the early 2010s, there were probably only 20 companies in the world that were offering what we now call ‘desktop systems’ at low cost,” he recalls.
Today, there are dozens—if not hundreds—of companies making desktop 3D printers with a host of different configurations and features. Then there are the big players, many of which seem poised to become even larger through mergers and acquisitions, such as Stratasys and Desktop Metal. While the biggest impact from desktop 3D printers has been in prototyping, when it comes to real additive manufacturing, it’s the companies offering large-format and/or metal 3D printing that are changing the way we design and manufacture end-use products.
Additive materials have seen a similar growth trajectory: 15 years ago, it was largely the same companies building 3D printers and supplying the materials for them. “It was a fantastic business model,” explains Kawola, “But if you’re talking about only a handful of companies with relatively small teams, was that the best way to push the material science forward? Probably not.”
These days, additive manufacturing materials are being produced by global companies, such as Jabil, as well as startups like polySpectra. Even small machine shops are able to offer their own alloys for metal 3D printing.
What’s Driving the 3D Printing Industry?
The case for 3D printing’s value as a prototyping technology has been firmly established, but when it comes to its growth as a production technology, there’s still one key element missing: demand from the big original equipment manufacturers (OEMs).
“When things move into production,” says Kawola, “they’re about economics. I think a lot of innovation [in 3D printing] has been driven by these large OEM customers having a clear idea about what their thresholds are for moving into production, with the vendors trying to find ways to meet their requirements and make the economics work.”
Of course, this raises the question of what’s driving the OEMs to take additive manufacturing more seriously as a production technology. Ongoing issues in the global supply chain that began with COVID are certainly a factor, but there’s also the potential advantages 3D printing offers in terms of design and manufacturing costs. GE’s famous fuel nozzle for the LEAP engine is the obvious example, but there are many others.
Kawola’s current company, Boston Micro Fabrication, works primarily on parts at the submillimeter scale. These are typically expensive to make using traditional manufacturing technologies, such as molding or stamping, but there’s also a growing demand for them. As a result, this sort of 3D printing is at an advantage for electronics manufacturing, where antennas and other components are continuing to shrink, as well as medical device manufacturing, where smaller devices make for less invasive procedures.
Ultimately, whether it’s a matter of localizing production and creating digital inventories to reduce supply chain risks or responding to customer demands by finding more economical ways to produce next-generation components, it’s the economics of additive manufacturing that will continue to drive innovation and expansion in the industry.
Read the rest of this story at ENGINEERING.com