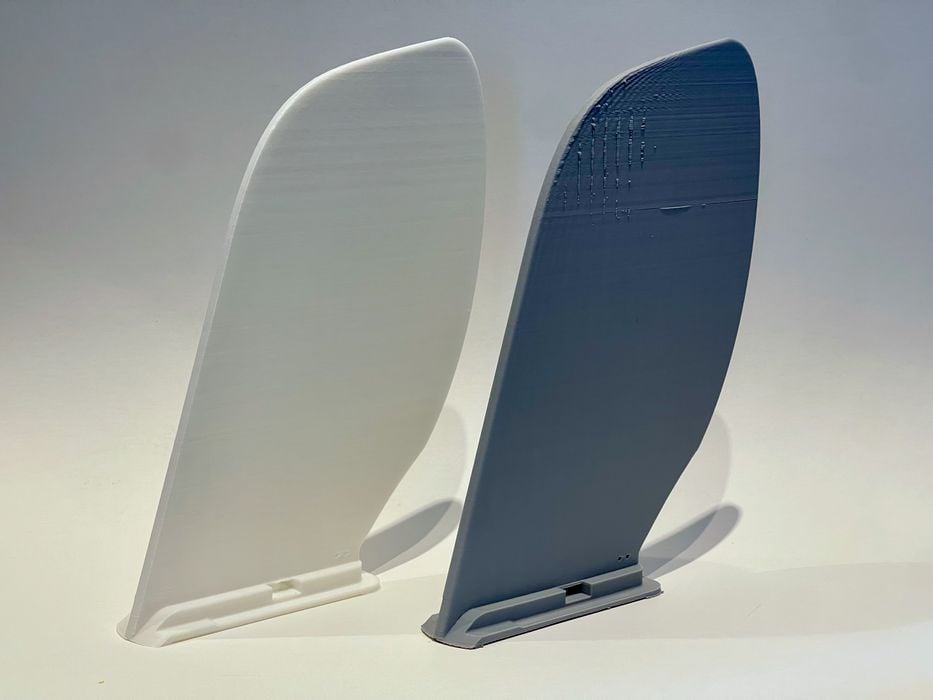
I just printed an outstanding example demonstrating why CoreXY 3D printers are much more desirable.
CoreXY is something you will hear more about as time passes, and there are good reasons for this. Itās a motion system variant thatās increasingly used in 3D printers.
The current most popular motion system is the i3 style, which involves sliding the print surface forwards and backwards (Y-axis), while moving the X-axis along a rail.
The i3 style proved very popular for one important reason: it can be implemented at low cost. This motion system is why most inexpensive desktop FFF 3D printers are gantry style, with no enclosure. You need only a couple of struts in order to build an i3 3D printer. The i3 style is also known as a ābedslingerā, because it āslingsā the print bed back and forth while printing.
The CoreXY style is quite different, and substantially more complex. It involves a series of belts that run between the four corners of the print plane. These act in a coordinated fashion to move the toolhead in both X and Y directions, unlike the i3 style where the toolhead only moves along the X axis.
The CoreXY style is becoming very popular in high speed 3D printers because it is far more compatible with rapid movements.
Many desktop 3D printer manufacturers have produced high speed versions of their i3 machine designs. These machines indeed operate at very high speeds and can produce very good quality output.
But there are some scenarios where high speed and bedslingers just donāt match very well. I ran into one of them this week.
My project was to produce some mountable fins for an inflatable kayak. The kayak came with three fins, but they are quite small and provide insufficient control, particular in windy conditions. The idea was to 3D print replacement fins that were quite a bit larger.
I was fortunate to discover that several people had already 3D modeled the exact fin design and posted their results to multiple 3D model repositories. It turns out there is quite an online community for this type of 3D model.
I needed a couple of these fins, so I launched jobs on two 3D printers: the Creality K1C and the Kobra 2 Pro. Both are high speed 3D printers, but the K1C is a CoreXY style device, and the Kobra 2 Pro is a bedslinger.
After the jobs completed, I had two decent fins. But a closer inspection revealed some issues with the Kobra 2 Pro print.
Here is a detailed view of the top of the K1C print, which looks very good.
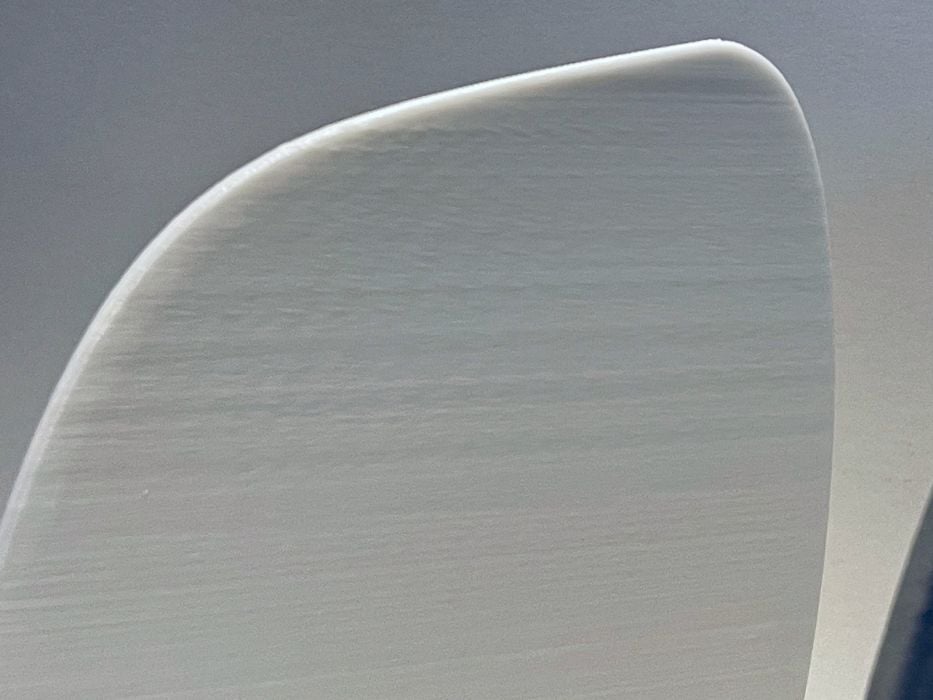
But here is the same view of the Kobra 2 Pro print, which shows quite a bit of spurious material. Whatās going on here?
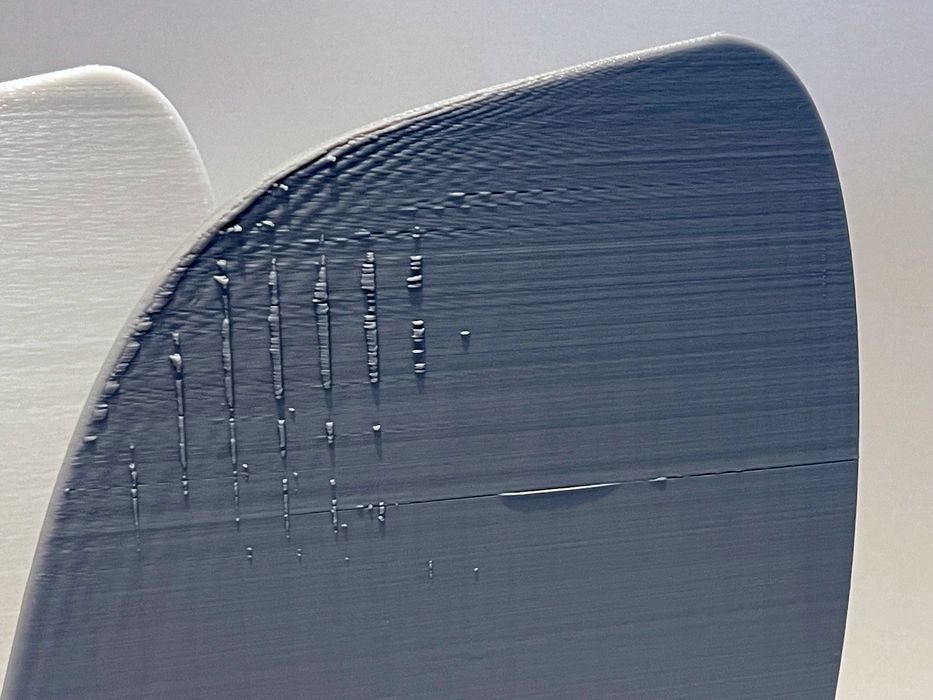
The problem is that the fin is a relatively tall and thin design. As the print proceeds on a bedslinger, the fin is thrust back and forth by the motion of the print bed. This force is amplified by the height of the object and causes a wobble at the top.
As the print gets taller, the wobble increases. This is why the aberrations were worst at the top of the fin.
This could have been overcome by adding side supports, and might not have happened at all if the objectās geometry was more robust. But tall and thin objects have big problems on bedslingers, as you can see.
Meanwhile, the K1C doesnāt move the print surface (aside from the very slow up and down movement during layer changes), so no similar artifacts were generated.
Another factor is that CoreXY systems must have four pillars in the corners to support the motion system. This adds cost to the system, but at the same enables very easy enclosures: just slap some panels on the sides. Enclosures captures stray heat, increasing the quality of the print.
Because of the increasing interest in high speed 3D printing and increased quality, itās likely that products will eventually move towards CoreXY designs, and i3 systems could slowly fade away.