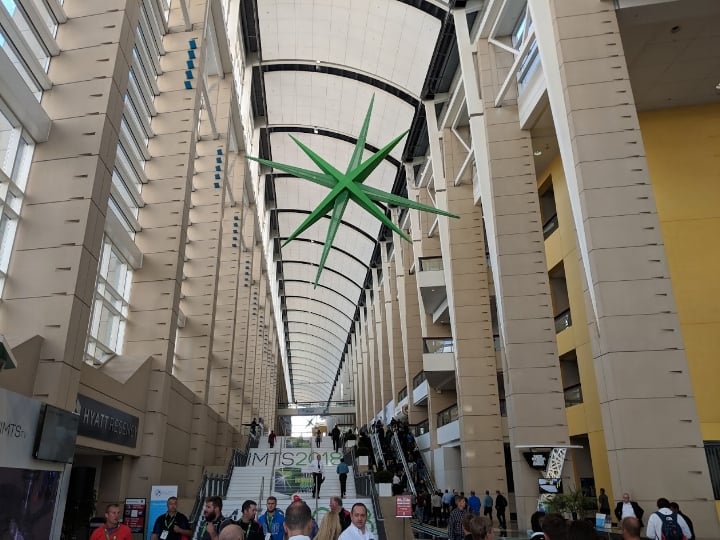
This year’s IMTS doesn’t just feel bigger than ever; it’s the biggest in the International Manufacturing Technology Show’s history.
Per an app on my phone that’s vaguely accurate on step counts, I logged 5-6 miles per day walking around Chicago’s packed McCormick Place, where 125,363 registered visitors (as of the time of writing) have been keeping busy in the convention center’s four halls — which were completely filled for the first time.
IMTS 2018 continues through the 15th and is hosting:
-
1,424,232 square feet of exhibit space
-
2,123 booths with 2,563 exhibiting companies
-
55 million pounds of machinery
IMTS, held every even-numbered year, features a dedicated Additive Manufacturing Pavilion at the front of the West Hall, though several 3D printing companies can be found a trek away in other buildings.
While it was occasionally pleasant to duck out of the additive-focused areas to peek at other areas of advanced manufacturing — it’s never not fun to watch a car go ‘round overhead on a single robotic arm, or to watch a robot bartender serve up a cold one — 3D printing is enough to keep a visitor very busy.
Disclosure: I attended IMTS 2018 as a guest of HP Inc. The schedule of events surrounding HP’s unveiling of its new Metal Jet technology filled much of day two, and I appreciated that opportunity to gain additional access to company execs and partners; that said, I also enjoyed a good deal of time visiting many other industry participants.
In the coming days, we’ll dive more deeply into the depths of the IMTS experience, as executive insights into several new launches provide a more detailed picture of some major product launches. For today, while I rest my feet and try to gather together my jumbled thoughts, scrawled pages of notes, and slew of business cards, we’ll look toward some of the overall trends of additive manufacturing at IMTS 2018.
Metal
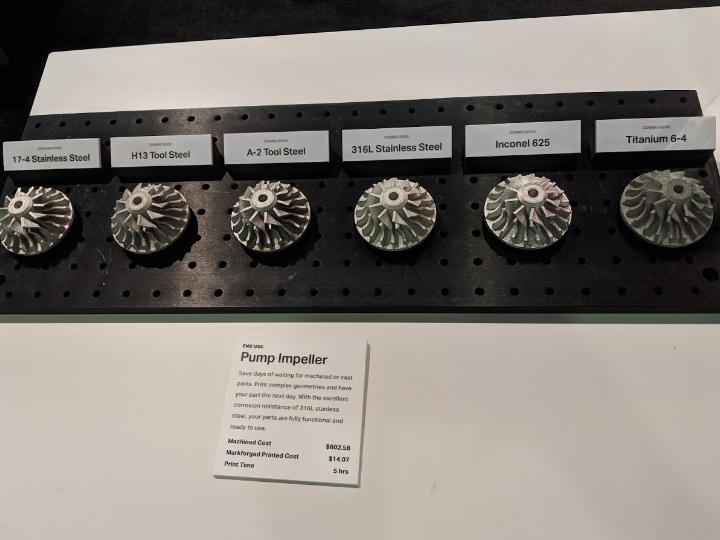
Obviously.
Metal made a massive showing, as Metal Jet launched, Velo3D introduced its Sapphire system, EOS unveiled its M300-4 metal 3D printing system, Desktop Metal showed off its full Production System for the first time, Markforged highlighted new materials, 3D Systems and GF introduced the new DMP Factory 500, BeAM drew attention to multi-modality metals with the ‘Big Ass Isogrid’ component, Stratasys had some more metal parts from its now-named-but-still-super-secret Layered Powder Metallurgy technology-to-come — and much more.
These were just the booths where I spent significant time; Optomec was demoing its new metal hybrid system, GE Additive drew visitors to see its variety of technologies, Mazak’s massive hybrid system was impossible to miss, Formalloy and others presented intriguing materials and applications; there was no shortage of metal.
To a one though, executives from each of these above companies, when asked, expressed enthusiasm for the growing participation in metal additive manufacturing.
Strength in Polymers
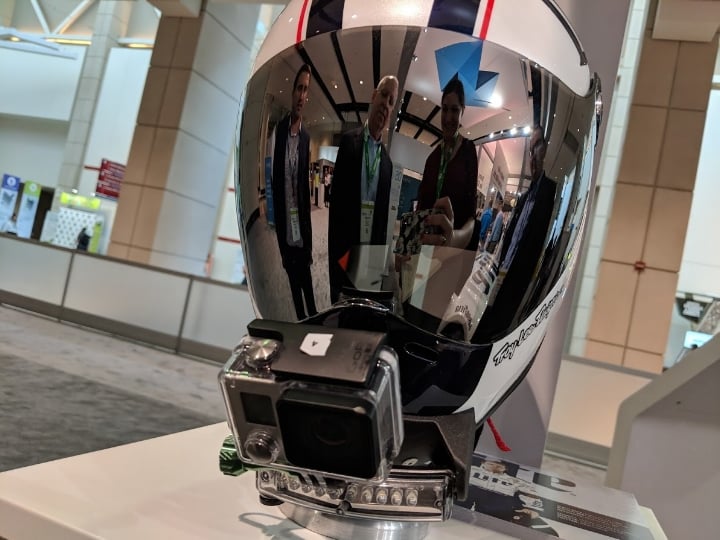
IMTS being above all dedicated to manufacturing, the plastics technologies on display were highlighting high strength and automated processes.
One of my first stops day one was to Carbon’s booth, where the team showed off an example of an automated production line alongside its expanding portfolio of materials. Stratasys had a lot to show with its carbon fiber focus, while 3D Systems’ Figure 4 setup drew a crowd to see more in automation and precision. Tooling was in focus with showings from Markforged, Roboze, and Rize (appearing with Fuji), Stacker drew attention to investment casting applications, Multi Jet Fusion had no shortage of examples for production 3D printing and full-color prototyping, and some seriously large prints presented the large-scale possibilities with BigRep and Titan. LulzBot and Ultimaker stood strong with use cases for desktop 3D printers, and MakerGear brought its new industrial Ultra One.
Partnerships
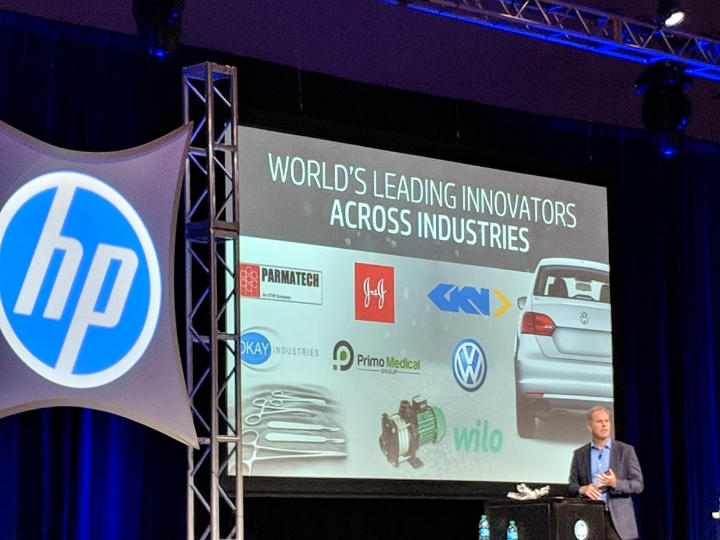
3D printing is growing as an industry, but it’s not doing so alone.
3D Systems and GF; HP and Volkswagen and GKN Powder Metallurgy; EOS and Siemens; Stratasys and Team Penske: additive manufacturing is working with partners in hardware, software, design, and end use. Many, many partnerships were highlighted, with strong messaging going beyond the lovely photo ops of CEOs shaking hands.
Software
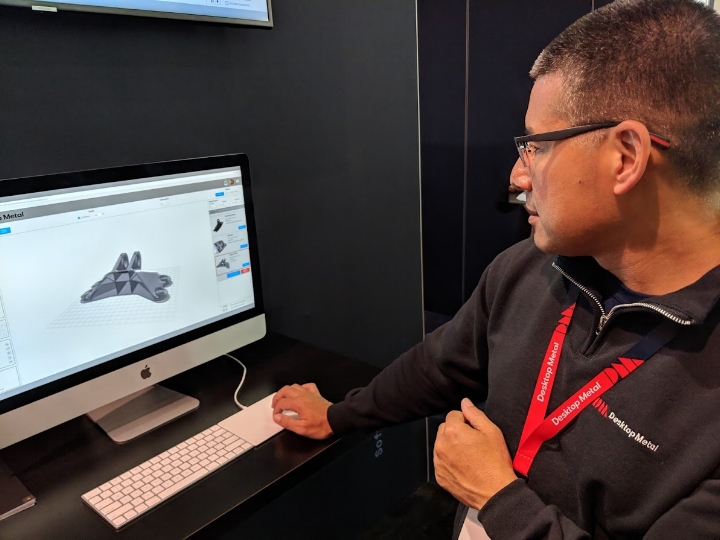
Software makes the 3D printing world go ‘round (but mostly layer by layer)
This week we learned more about SOLIDWORKS 2019, always an anticipated series of announcements with annual enhancements; while my chats with the team took place outside of IMTS, SOLIDWORKS was of course well represented at McCormick Place. Desktop Metal, in addition to its hardware offering expansions announced last week, also introduced its new Fab Flow software. I’m admittedly not a software person; Fab Flow struck me as a particularly wonderful concept, and definitely one we’ll be diving into soon. Velo3D’s system stands out as well for its clever software, developed in-house, that enables the platform’s unique full closed-loop melt pool control capabilities.
The Competition
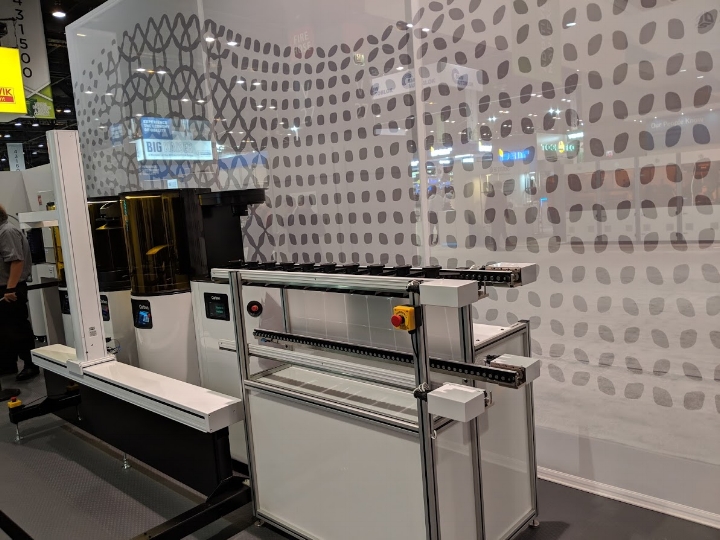
I’m a big fan of competition; none of us will do it alone.
Such sentiment runs deep through the industry, fortunately. One enterprise does not an industry make, especially one hoping to be part of “the next industrial revolution.” To close every interview, and even many casual conversations, during my time at IMTS, I asked a simple question that everyone hates: “What do you think of what the other guys are doing?”
The more honest responses noted some sleepless nights following other promising announcements, but not a single person shied away from responding or wished ill upon “the competition.”
This is another area well worth its own look in upcoming coverage, as product introductions continue to ramp up and seemingly pile up. How does a company stand out from the pack now that there’s, well, more of a pack? How do announcements from IMTS 2016 compare to where we found the same companies two years later? What’s actually made it onto the market? What’s actually impacting the market?
IMTS 2018
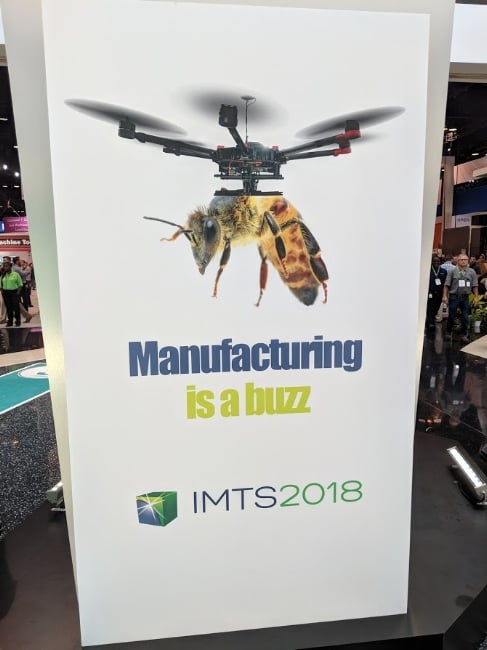
This year’s IMTS continues on for a couple more days; my three days there weren’t nearly enough time to see everyone or every company I’d have liked, but then there never is enough time at these major shows.
As with any trade show, while the products on the floor offered a look at the tangible realities of today’s industry, the real value lay in the conversations at — as well as well away from — the booths.
[All photos: Fabbaloo]
The fate of major 3D printing conferences in 2020 is unclear with the ongoing virus outbreak. We have thoughts on what it could mean.