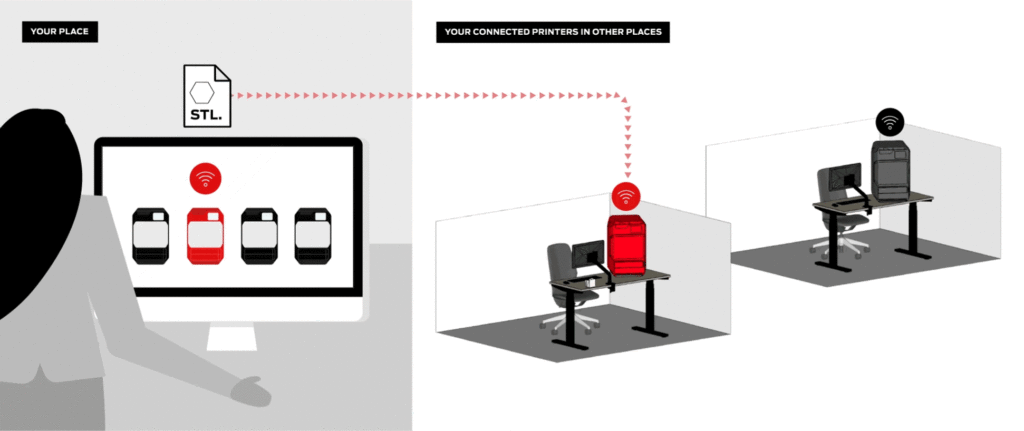
MakerBot hosted a roundtable today for an intimate conversation on 3D printing and its impact on the future of supply chain manufacturing.
The event was a virtual summit welcoming experts from MakerBot, CONTEXT, Mobility goes Additive, and the media. More than a summit, though, it was a conversation — and taking part in it certainly offered food for thought on several fronts.
Participants today included:
- Nadav Goshen, CEO, MakerBot
- Stefanie Brickwede, Managing Director, Mobility goes Additive e.V.
- Chris Connery, VP Global Research & Analysis, CONTEXT
And from the media perspective:
- Fabbaloo, Sarah Goehrke
- Machine Design, Marie McBurnett
- MM MaschinenMarkt, Simone Kaefer
- TCT Magazine, Laura Griffiths
Following a presentation from the ever-insightful Connery covering impact on shipments and revenues on 3D printing in Q1 2020, as well as overarching industry trends — more on that later — the floor was open for questions.
Remote Work And The New Normal In 3D Printing
As we met via Zoom from locations around the world, the day after the launch of MakerBot CloudPrint, I asked what 3D printing companies have learned about remote work capabilities to better network 3D printers and how this may impact future globally networked digital manufacturing capabilities.
Goshen indicated that from the MakerBot perspective, remote work has enabled new ways of working, including engineering from home. The team began working remotely on March 18 due to COVID-19 countermeasures closing offices.
“The MakerBot engineers are very innovative, and have been utilizing their bathrooms, basements, you name it, as improvised labs,” he said.
Glossing over how many recent MakerBot innovations may have emerged from bathrooms, he noted that “this will not go back to how it was before; it opens up for different kinds of opportunities.”
“I think it will be kind of a hybrid,” he added, looking ahead. “We were able, during that four months, to launch four products, one being a new printer. It proved to work very well.”
It was this experience, and actively having to answer for themselves an important question (“What is missing?”) that led to the development and launch of MakerBot CloudPrint. Remote working isn’t just having machines out in the field; it requires connection, collaboration, and an ease of joining separate workflows.
“We had two engineers share the same print and look at it through a Zoom meeting to solve a problem. This kind of additive manufacturing will enable that. The usual way of doing that is to have a centralized point with one print… We will see this remote platform continue to improve, to enable remote design and production processes. Software is moving into that cloud-based offering. This is a great opportunity as both a manufacturer and a participant in the industry, and it is something that will continue to improve,” Goshen said.
Brickwede added though that these workflows will, at least in the near term, vary considerably from country to country. In Germany, she noted, workers have been returning to offices. But that doesn’t mean the return to such workplaces will be a full return to how work had been done before.
“Apart from corona, since everyone has now tried out working from home, we will not go back to the previous logic of being in the office every day from 9 to 5, this will not happen again. When I talk to huge corporations, they offer their employees not only for corona times the opportunity to work from home. This will stick,” she said. “To engineer anything, the need is to do so via platforms and the cloud, and then it will be crucial that those clouds are safe.”
Such new ways of approaching work require additional concerns — and certainly security is high among them. Her reaction to Goshen’s engineers comparing a part on Zoom was surprise: “If you say that in Germany, everyone will say, ‘no, no this is not safe enough!’” But, she acknowledged, “this will be the new trend,” to find ways to compare and collaborate virtually.
From the analytical point of view, Connery weighed in with the CONTEXT perspective. The changeover to remote working represents “a new starting place, not a new ending place.” That is, we’re collectively at the beginning of whatever this transformation will be as more work is happening from different locations.
However, there are inherent holdbacks. Perhaps most notably is one of the simplest facts, as he laid out:
“Most serial production will not be taking place remotely. We can’t do large-scale additive manufacturing from home. The modality of metal printers, for example, you can’t do that from home, you need an industrial area.”
A bright side emerging, though, is that collaboration is widening, especially as more professional 3D printers have been brought into individual workplaces. (CONTEXT defines professional 3D printers as those in the $2,500-$20,000 range — such as MakerBot’s systems.) This individualized work will “help drive their thoughts later on in production facilities.”
Distributed Manufacturing And The New Normal In 3D Printing
Outside of individual work from home situations, though, what have we collectively learned about remote work? I added to my question, asking our experts about that oft-touted benefit of additive manufacturing: distributed manufacturing.
That is, working from different areas for decentralized production, which can bring productin closer to the point of demand as global installations remove the need to rely on one single production facility. That mode of supply has been under the microscope as supply chain weaknesses emerged in full force in the face of pandemic.
“Now people are more understanding of the idea that what they print on this printer in Singapore is the same as what they print in Brooklyn or Istanbul, getting comfortable with the idea that they don’t just need that one giant manufacturing facility in this part of the world,” Connery said. “They’re more comfortable, because they’ve been working remotely, so they’re getting more comfortable producing remotely, distributing files and working collaboratively with the idea that the same thing they manufacture here is what they manufacture there. Industrial machines all over the world are closer to where consumption is, as opposed to being in one central location.”
Goshen agreed, digging in a bit to the idea of the digital factory — and the idea that we are at the start of this new way of functioning.
“What is the end of it? I’m not sure we know now,” he said philosophically.
Among the factors at play are the ever-driving need to shorten the time of design and production cycles. Digital manufacturing allows additional agility, and “a remote team and collaboration accelerates development” as there are now “way more models for us to follow,” Goshen continued.
“We must make sure we are answering the requirements of industrial and IP protection for customer needs; digital manufacturing will follow that,” he said.
IP security is “definitely an issue,” Brickwede agreed — and this is something that those companies already working with 3D printing technologies are already addressing. The need for protection is only rising as more virtual collaboration continues.
Further, she added, there is the need to open up machine accessibility. While remote workers may have a desktop 3D printer at home, “they do not have a metal machine; therefore you need to give people access to these production facilities also remotely.”
What the new normals in 3D printing will be remain to be seen — as Brickwede, Connery, and Goshen all agreed, we are still in early days of this latest revolution in manufacturing workflow. The good news is that both opportunities and challenges are becoming much better understood as additive manufacturing continues to rise as a supply chain solution around the world.
From OEMs acting as service bureaus to newly installed 3D printer fleets and what they might mean, the roundtable offered a variety of different thought points to explore. Distributed manufacturing and the impact of remote workforces are a tip of one iceberg to be explored; more soon as I continue to consider some of the points raised in this discussion.
Via MakerBot, CONTEXT, and Mobility goes Additive