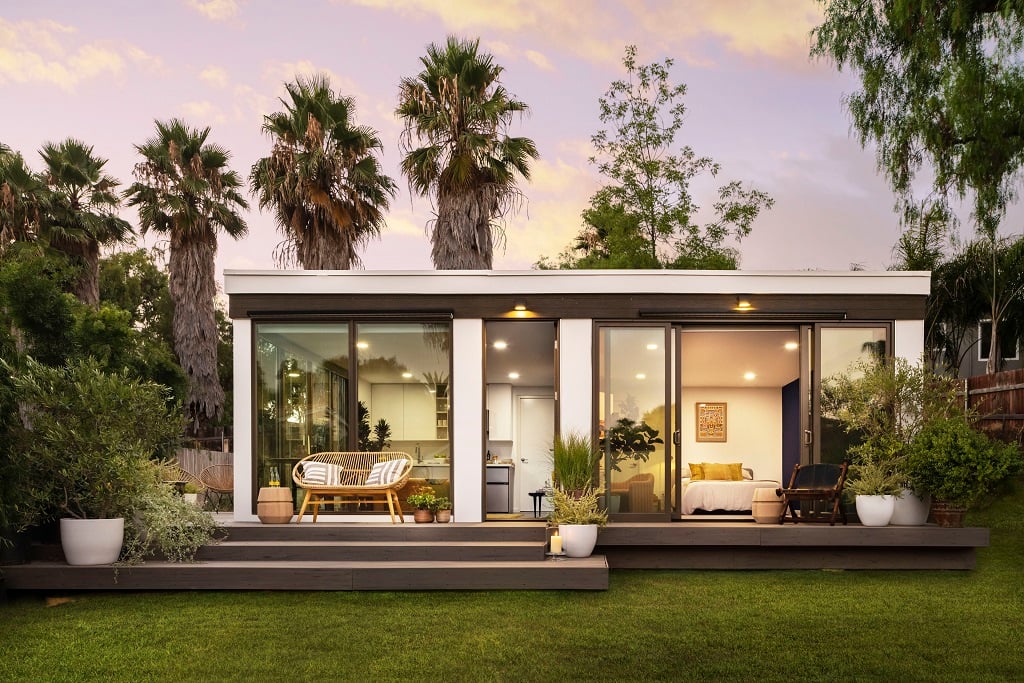
Construction 3D printing is itself still a new venture; Mighty Buildings has emerged with a new take on this technology, though, surpassing some of the hype of other participants.
We’ve all seen the headlines by now: “3D Print A House In 24 Hours!”
Really, no. For the most part, what those headlines mean is that several enterprises have emerged that can 3D print four walls in 24 hours. Those walls still need a lot to turn them into a house, from HVAC, plumbing, and electrical to simple things like flooring, windows, roofing — and for the 3D printed concrete to set. Neither Rome nor an actual house was built in a day.
But maybe there’s a way to 3D print a house without the hype, the concrete, and the worry about whether that house will actually be livable.
Enter Mighty Buildings
California-based Mighty Buildings was officially incorporated in August 2017 and emerged from stealth last month, touting a $30M funding and, perhaps more impressively, UL certification.
I spoke with Sam Ruben, Mighty Buildings’ Co-Founder and Chief Sustainability Officer, to learn more about the company’s offerings and operations.
A few simple facts stuck out to the four leaders who would eventually become the company’s co-founders: There’s a housing crisis in the Bay Area, as well as many (many) areas around the world, where affordable, available housing is in very short supply; as advanced as Silicon Valley is in terms of most technologies, it — and the US in general — is far behind areas like Singapore in embracing new construction technologies.
Eventually — skimming over the company’s early history as a Y Combinator company, close work with California housing authorities and UL, moving from tabletop 3D printing to a container 3D printer, and a whole lot of work with both technology and regulations — what has emerged is an interesting offering in new construction.
Mighty Buildings didn’t want to jump onto the scene with fireworks and fog machines; they wanted to make their public debut as a proven, viable offering. Hence three years of stealth.
“We waited so long to come out of stealth because we wanted to make sure we could really deliver on our promises,” Ruben said. “We didn’t want to create a lot of hype or expectations we couldn’t meet, and we wanted to show that we’d done the work on the regulatory side. If you piss off a planner, you’re not building anything. It’s really important to work with the industry, with regulatory, with building officials. We’re not trying to replace legacy companies or skirt the rule, we’re trying to go by the book, to create new opportunities in technology and design, and do so at the scale necessary to really have an impact on the housing affordability crisis.”
Upon their introduction, they are already able to point to two installed hybrid (part-3D printed, part-traditionally made) accessory dwelling units (ADUs), the type of dwelling that marks their launch point. These first hybrid ADUs are in San Ramon and San Diego; within a year, the team is planning to move to fully-3D printed units.
“We’ve been moving incrementally,” Ruben affirmed. “Our first units are hybrid, they have that traditional steel frame structure.”
Mighty Buildings 3D Printing
Here’s a look at how their 3D printing works, in this case for a 350-square-foot studio unit:
A few things might stick out in this video:
- That’s not concrete
- The roof is 3D printed
Mighty Buildings uses a light-cured 3D printing process: “We’re not dealing with concrete or thermoplastics, but a UV-set thermoset composite,” Ruben said.
The closest thing on the market to their Light Stone Material (LSM) is DuPont’s familiar Corian solid surface material, often seen on countertops. Corian is an acrylic polymer and alumina trihydrate material, for reference.
“What we’ve done is find a way to print it into anything, and to print without supports, so we can not only print floors and walls, but ceilings,” Ruben explained of the UV-set LSM. “This new material cures so quickly it can support its own weight, but not so quickly we don’t get full chemical cohesion between layers. That’s the key to our technology. Printing a roof also opens up more opportunities in form, enabling design that hasn’t been available to architects.”
Indeed, most 3D printed homes we’ve seen to date have been made of concrete. In addition to concerns about what that might mean for the environment, concrete’s curing time means that that 24-hour turnaround time really only refers to the actual 3D printing process. Actual curing takes much longer for the finished walls (again, before taking into account the additional construction time and labor necessary to finish the structure into a livable dwelling).
“When we say we can print 350 square feet in 24 hours, we actually mean that: in 24 hours. When others say 24 or 48 hours, the concrete has to set, you have to do rebar, steel supports; ours cures literally that quickly,” Ruben added.
Furthermore, concrete isn’t amenable to 3D printing in all environments. Most concrete 3D printing — though not all — takes place on-site. Mighty Buildings works with prefab housing, 3D printing in a warehouse that can still be quite close to points of demand. They use robotic finishing cells and other automation to further enhance their high-tech approach to construction.
“One other cool thing,” Ruben added, “even though our material is really strong, and similar to concrete, we can mill the surface. We can go for that raw look, and some work really embraces that look, but can also make it really smooth and mimic traditional looks like siding. What really sets us apart is flexibility. We can unlock productivity in this industry in ways other 3D printing can’t at this point.”
Mighty Building ADUs And Beyond
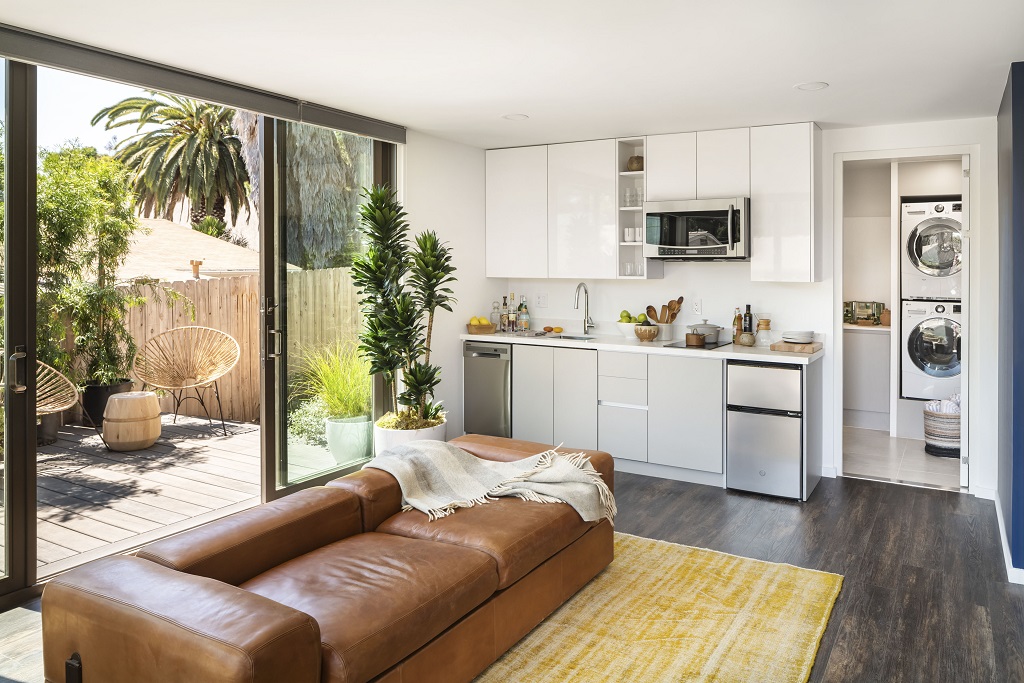
As noted, the company is starting off with ADUs (think the popular HGTV concept of the backyard in-law suite) — but they’re thinking well beyond that as well.
A lot of this “beyond” will come through new developments in their material offerings. They’re “continually developing” on this front, and looking to certify and introduce a new reinforced material in the relatively near future. This material will enable them to build multi-story units.
“We’re looking at that as a way to move into multi-story buildings; not just single-story, single-family units, but also multi-story, multi-family structures that can help in urban areas. In the Bay Area there’s just not a lot of land; it will be imperative to have that verticality,” Ruben noted, in keeping with the company’s mission to offer scalable solutions to the housing shortage.
The warehouse-made nature of the work will be “particularly impactful when we have other reinforced materials online that will allow five-to-six-story units,” he added.
Keeping an eye to what it means to bring in more robotics and automation to a sector that traditionally includes a significant amount of manual labor, and thus laborers, Ruben also addressed their vision for the workforce.
“What we’re trying to do at the end of the day isn’t replace labor, but to optimize productivity. There’s a lack of skilled labor, especially in California; many have left the construction industry or retired. What we’re trying to do is optimize that labor and attract a new generation of workers familiar with technology, and create a space for them in the construction industry,” he said.
Mighty Buildings estimates that 3D printing a 350-square-foot volumetric module in 24 hours reduces labor requirements by about 90%. But, Ruben notes, “that’s more work for the labor force but less work per unit” by making more buildings in a more streamlined way.
This approach also addresses another difficulty in construction: workplace injuries. Construction is the second most dangerous job in the US, after mining, Ruben said is his understanding, and so: “We’re making a safer work environment. We also build twice as fast with ten times less space, and eliminate waste.”
That waste elimination also led to another important point: milling the LSM to a smoother look allows the Mighty Buildings team to capture that extra material and use it again as new material. They’re keeping an eye on the importance of end-of-life recyclability, as well.
Regulatory-Compliant 3D Printed Homes
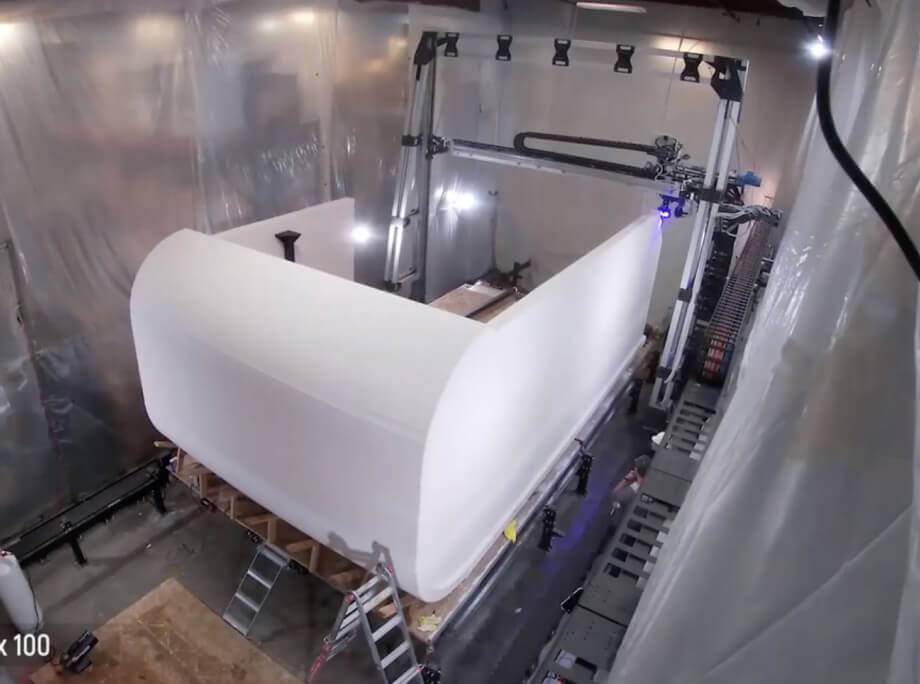
Very, very importantly is one other point for Mighty Buildings: regulatory compliance.
“We have been working with UL from the beginning,” Ruben explained. “It’s important to make space on the regulatory side. These are people’s homes; we have to be cognizant of that. We’ve been engaging from early on with building departments, with planning departments, and we’re addressing that with what we’re doing. Part of why we decided to launch in California as opposed to somewhere with more permissive building codes; California has some of the strictest building codes, and if we can build here, we can build anywhere.”
Because Mighty Buildings is planning to create scale solutions to address the housing shortage, they understand the importance of working with the right people. While their current business model is starting off with direct-to-homeowner sales, they also need to engage with builders, with developers, with planners.
Having UL certifications in their portfolio opens up a lot of doors so that Mighty Buildings’ buildings can eventually open up their own doors.
Obviously there’s still a lot to learn and prove out as construction 3D printing continues to pick up, and Mighty Buildings has a long road of work ahead of it. But it seems like this company is already, pun intended, building a strong foundation.
Via Mighty Buildings