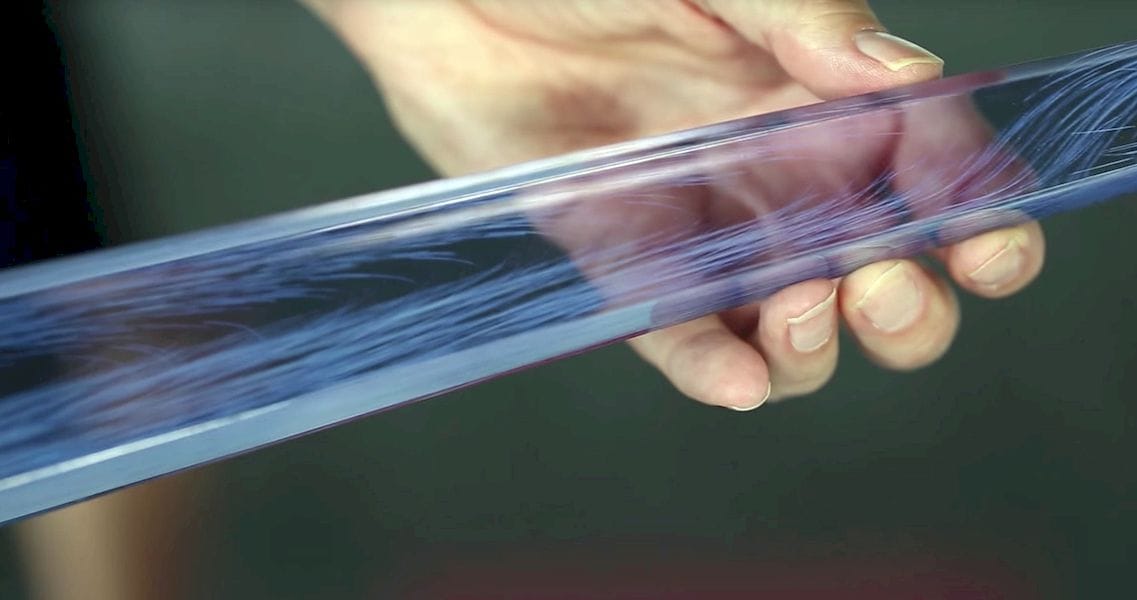
Stratasys announced something profoundly important this week, but I don’t think many people understand exactly how important this is.
What did they announce? It’s something called “VoxelPrint”, a GrabCAD feature, and would appear to be a specialty software tool that can make their full color J750 device work a bit better. Ho Hum…
But no, it’s not “Ho Hum”. This is a really big deal. Let me explain.
Stratasys had a problem when they introduced the J750. They had a device that, with its six input materials and jetting heads, can literally deposit any of the six materials – or any MIX of them – in any position in the print.
However, initial uses of the J750 were mostly limited to providing incredible color textures to the surfaces of prints. Prototyping phone cases, for example, is a perfect application of this technology.
But it seems a bit of a waste of the technology to “merely” 3D print color textures on the surface, when the interior of the object could also be varied, doesn’t it?
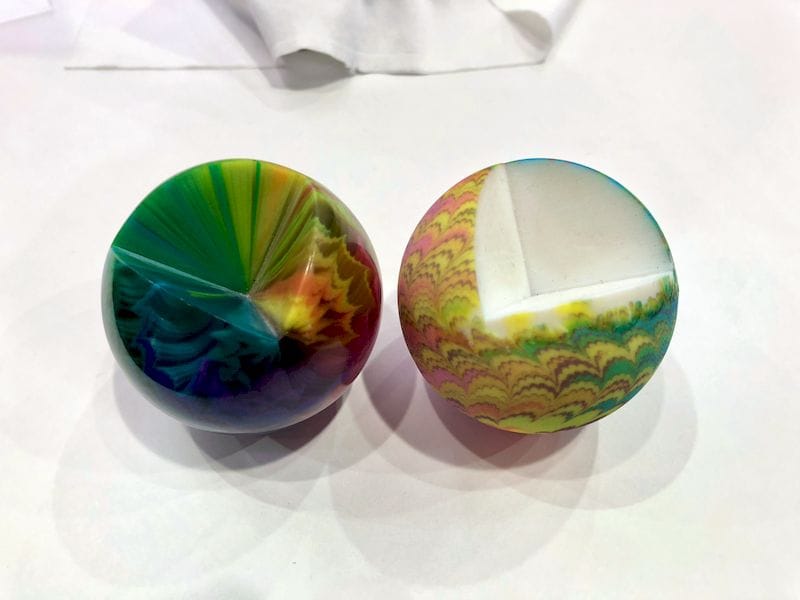
There wasn’t a problem with the J750. No, instead there was a problem with the software preparing complex designs to put into the J750.
What was available for use? Applying an image or texture map to the surface of an object was a feature in many 3D modeling tools, and that’s what has been used primarily on the J750 to create color surface textures.
But such 3D modeling tools were not designed for 3D printing; they were designed for preparing visual 3D models for use in, for example, games. In games the objects are virtual and have no interior structure. You only see the surface and that’s all that’s needed in a game. Thus the tools go only that far.
This left the J750 with a bit of a software gap: how could you properly leverage the full power of the system? You could laboriously segment your object and painstakingly assign different properties to each, but that brute force approach is essentially impractical.
This gap encouraged Stratasys to create GrabCAD VoxelPrint, which is an interface to their system to accept “slices” of a 3D model that can, at a voxel level, contain different attributes.
Now, for the first time, a commercial 3D printing system can accept voxel-by-voxel instructions enabling the use of different materials and colors.
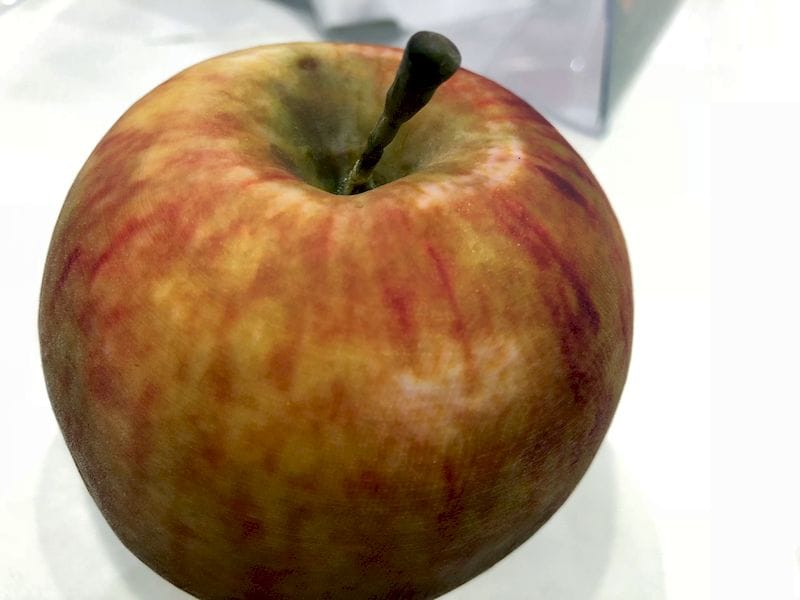
Stratasys has created a few rough examples of this technology that I’ve imaged here. This apple, for instance is quite astonishing. It looks EXACTLY like an apple. It even feels like an apple if you pick it up, although it’s a bit heavy.
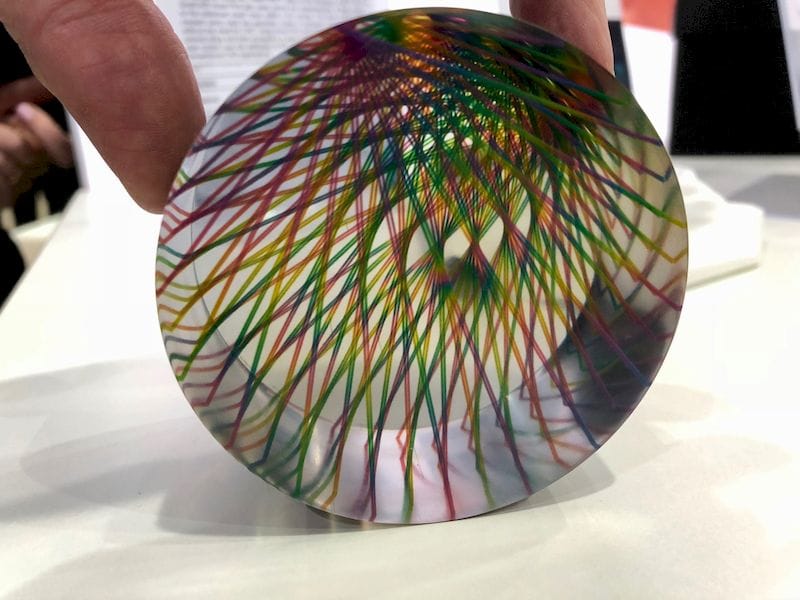
This structure shows a primitive attempt at embedding different materials in the interior of an object.
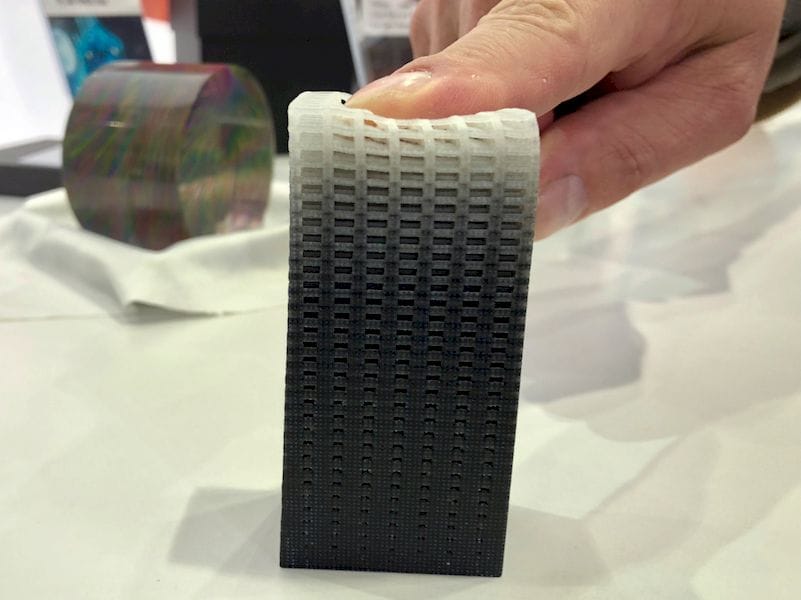
Here is a lattice structure, apparently comprising of some 900 MILLION voxels, is varied by flexibility. The top is compressible, but the bottom is not. This is an example of a “flexibility gradient”.
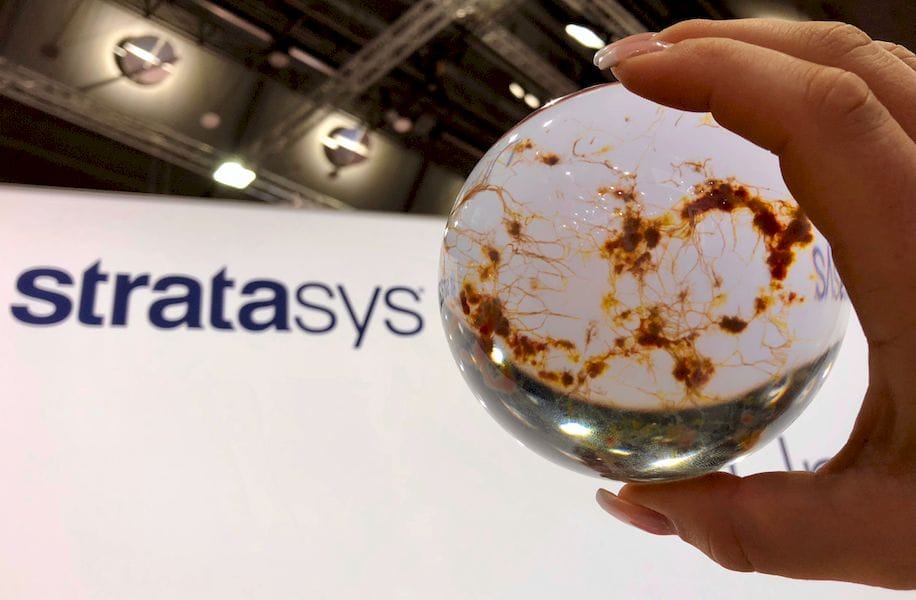
This is a 3D print of a human tumor. The idea here is to 3D print the tumor portion using materials that simulate real cell properties, enabling this object to be used as a “test item” for medical scanning devices.
These are, as I say, rough examples of what might be possible in the future.
This is why it’s important: imagine a complex 3D object with voxel-by-voxel materials. You could, for example, make a beam that has a “gradient” from hard to soft – and embed that within another structure. You can make portions transparent on a voxel level. You can mathematically generate astoundingly complex structures that vary in engineering properties for the most efficient use of material. And think about the possibilities when Stratasys eventually introduces electrically conductive material.
This is what 3D printing is ultimately all about. The ability to create “anything”, including functional objects with moving parts, electrical circuits and much more.
Is this actually possible now with the J750 combined with GrabCAD VoxelPrint?
Not exactly. VoxelPrint is actually just an interface. The complex 3D models I’ve just thrilled you with must be created in separate 3D design tools.
Design tools that don’t yet exist.
But they will. The possibilities opened up by Stratasys here will encourage researchers to commence work on developing the “3D Photoshop” of the future that will enable many people to more easily design incredible objects.
And it’s not just Stratasys, either. If such tools exist, they could be used to create voxel-level 3D models that might be printed on OTHER 3D printers.
This could be the beginning of a whole new industry.
Via Stratasys