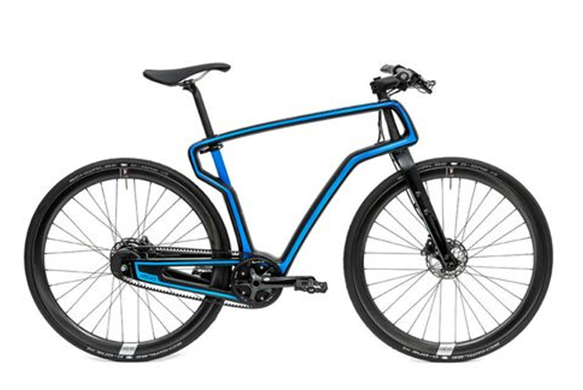
Peter Saenz examines how 3D printing might help in bicycle supply.
We are a little over six months into the pandemic of 2020. Both fear and conspiracies are floating in the air along with a new deadly virus. The future of the economy is uncertain — and it’s impossible to get your hands on a bicycle. The demand for bicycles has skyrocketed since the start of the pandemic. Research conducted by NPD Group shows a 121% increase in adult leisure bicycle sales in March.
Everyone has their reasons for buying a nice new bike. For some, cycling is a cathartic release after a prolonged stent of social isolation and is seen as an activity where they can socialize while maintaining a safe distance. For others, SARS-CoV-2 is a wakeup call, and cycling is a matter of life or death. Either they get in shape or roll the dice and potentially become another at-risk person who succumbs to COVID-19. There are the commuters who once relied on public transit but now will not dare ride in a confined train or bus. Cycling is their new mode of transportation to and from work. Then you have the fitness enthusiasts who can no longer go to the gym to exercise, homeschooled children that will need an activity for recess, the people who were going to buy bikes anyway, and everyone else trying to hop on the cycling bandwagon. Unfortunately, not everyone is going to be able to pedal around town this summer.
First things first, you can’t simply walk into any bike shop and buy a bike. Along with a variety of characters, you must bake in the summer heat as you wait on long lines that wrap around corners. When you reach the front of the line, you learn that there are slim pickings because every bicycle in the store has been sold. There are no longer any bikes that you can take on a test ride, let alone purchase off the display floor. The display floor now consists of only sold bikes that and are waiting to be picked up by those fortunate enough to procure them before inventories ran low. Bicycles must now be purchased on backorder. But the plot thickens because many models and sizes are out of stock, or the wait time is anywhere from months to “we will give you a call when it becomes available.”
Customers looking to have their bicycles repaired face similar frustrations. They wait in long queues, only to be told that there is a 2-3 week lead time. Excessive lead times are due to a workforce that lacks the resources to hold pace with a never-ending flood of repair bikes. The bicycle industry has not been immune to workers falling sick or deciding to stay home until the pandemic subsides. Repairs are also taking longer because of an inability to source parts needed to perform the repairs.
The impetus of The Great American Bicycle Drought is due to both supply-side and demand-side factors. As the world bore witness to the unprecedented scale of social engineering orchestrated by the People’s Republic of China to contain the virus, it also observed the breakdown of the bicycle industry’s supply chains and the source of 86% of the United States’ bicycle supply. This disruption came at the prelude of the U.S.’s northeastern bicycle season, which begins in March. The China lockdown was expected to affect the bicycle industry adversely, but no one anticipated how much demand would spike in light of the pandemic.
The bicycle industry has always been one of the most innovative industries and relies on advanced manufacturing processes such as 3D printing to continually improve product performance and manufacturing efficiency. For example, Trek utilizes the Connex printer to perform multi-material and multi-color 3D printing, which enables them to develop prototypes that more closely resemble production-ready parts. Many companies, such as Specialized, leverage additive manufacturing technologies to develop the next generation of bicycle saddles.
Bicycle component and accessory manufacturers widely use 3D printers as a cost-effective way to develop and test if their designs mount appropriately onto different makes and models. 3D printing allows them to quickly identify design conflicts and to optimize geometries to enable products to fit on a wide range of bicycles. It is almost certain that manufactures will double down on 3D printing technologies to improve production efficiency. Printers will be used to iterate through more (DFM) Design for Manufacturability concepts and develop jig, fixtures, and other elements that can be used to improve workpiece throughput and quality.
3D printing will also play a significant role in the adoption of electric bicycles. The burgeoning electric bicycle market will undoubtedly see immense growth in the years to come as people seek public transit alternatives.
The Research & Development Tax Credit
Enacted in 1981, the now permanent Federal Research and Development (R&D) Tax Credit allows a credit that typically ranges from 4%-7% of eligible spending for new and improved products and processes. Qualified research must meet the following four criteria:
- Must be technological in nature
- Must be a component of the taxpayer’s business
- Must represent R&D in the experimental sense and generally includes all such costs related to the development or improvement of a product or process
- Must eliminate uncertainty through a process of experimentation that considers one or more alternatives
Eligible costs include US employee wages, cost of supplies consumed in the R&D process, cost of pre-production testing, US contract research expenses, and certain costs associated with developing a patent.
On December 18, 2015, President Obama signed the PATH Act, making the R&D Tax Credit permanent. Beginning in 2016, the R&D credit can be used to offset Alternative Minimum tax for companies with revenue below $50MM and, startup businesses can obtain up to $250,000 per year in payroll tax cash rebates.
Conclusion
Despite some consumers being squeezed out of the bicycle market this ridding season, The Great American Bicycle Drought presents the dawn of the golden age of bicycles. For years bicycle culture has been gained traction, but the pandemic has accelerated bicycle ownership. In fact, Fabbaloo’s recent articles on 3D printed bicycles and 3D printed accessories such as helmets illustrate the emphasis on bicycles, particularly at this time.
Both established bicycle manufacturers and new entrants will utilize 3D printers to optimize their designs and help them navigate a bicycle crazed post-pandemic world. 2020 has been a tumultuous year so far, but you can expect The Great American Bicycle Drought to only last one ridding season as the bicycle industry innovates to meet demand.
About the author – Peter Saenz is a Senior Tax Analyst at R&D Tax Savers. Besides working at R&D Tax Savers he is a biomedical PhD candidate and a long-time bicycle mechanic who likes to repair bikes on the weekends.