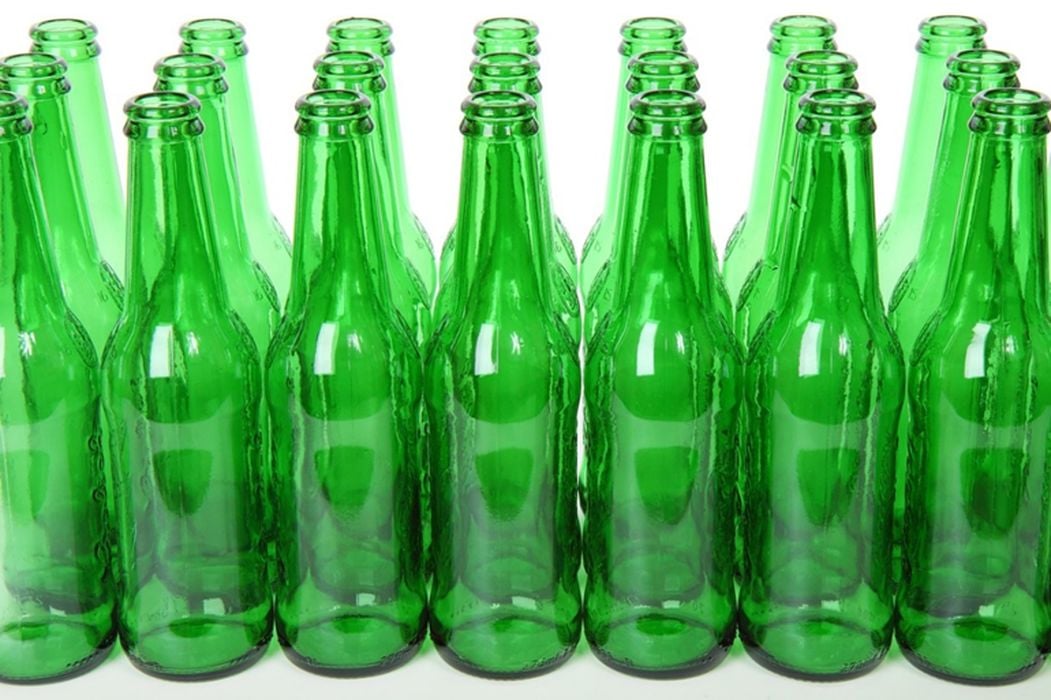
Charles R. Goulding and Andressa Bonafe sit down and chat with Alex Stiles, co-founder of Vitriform3D.
Despite being infinitely recyclable, only a small fraction of discarded glass in the US is actually given new life. In 2024 alone, an estimated 8 million tons of glass will end up in landfills, where they can take between 4,000 and 1 million years to decompose. We met with Alex Stiles, who is working to change this scenario with the help of 3D printing. The co-founder of Vitriform3D gave us an interesting overview of the challenges of glass recycling and how additive manufacturing can be used to convert low-quality glass waste into the next generation of eco-friendly engineered stone products.
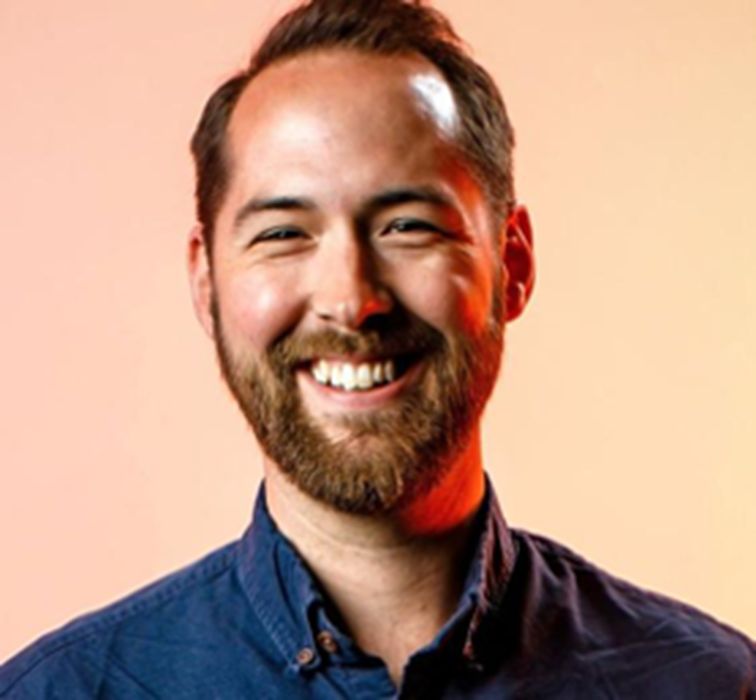
The US has an average 33% recycling rate for glass waste. In your perspective, what are the factors that contribute to this scenario?
Over the course of starting Vitriform3D and getting it off the ground, I’ve learned a lot about the logistics of glass recycling in the United States. It all boils down to the fact that glass is heavy and has low scrap value.Ā Ā Unless a city has the right processing center for handling glass, chances are that it isnāt economically sustainable for that city to ship its glass out for recycling. The economical shipping radius is about 150 miles, meaning that if the processing center is more than 150 miles away, the shipping costs outstrip the scrap value.
Government programs like bottle bills change those economics, but that’s a good rule of thumb. A good example is Knoxville, TN, where the closest glass processing center is in Atlanta, which is a four-hour drive and over 150 miles away. That is why most of the glass waste that is generated in Knoxville is not getting recycled. If you zoom out to the entire United States, only a third of all of the glass waste actually gets recycled. Two-thirds of it, or about 8 million tons per year, is just getting landfilled. This, despite the fact that glass is a durable, strong, and infinitely recyclable material.
In talking with people involved in the recycling ecosystem in different states and different cities across the country, I see a consistent trend: if you don’t have a glass processing center nearby, then either the city has to pay (and sometimes it is quite a lot) to ship the glass to a recycler, or it just goes to landfill. There are dozens of cities just like Knoxville all around the US that have this same dilemma. When you think about the conventional recycling approach of turning old bottles into new bottles, there are only a handful of dedicated glass processing centers in the country equipped for this processing. Since most of these are centered around major metropolitan areas, mid-sized cities and rural communities can fall through the cracks in the recycling ecosystem.
I could see this happen firsthand. Right around the time that I moved to Knoxville for graduate school, the city dropped glass collection from their recycling program. They have a single-stream curbside recycling program where you throw all of your recyclables into one bin. However, the Materials Recovery Facility (MRF), in Knoxville wasn’t set up to handle glass. The MRF contractor decided to no longer collect glass, to avoid damage to their equipment. This reduced glass recycling options in Knoxville to a handful of public drop-off sites, and the glass that is collected there is shipped down to Atlanta. As I was finishing up my graduate school program, I started thinking about the mountain of glass going to landfills in my community and considering ways that we could take this waste material and turn it into useful new products. It was in grad school that my cofounder, Dustin Gilmer, and I began brainstorming, and we realized that 3D printing could provide a solution.
It sounds like your experience at the University of Tennessee was determinant to the co-founding of Vitriform3D. Can you tell us more about your educational and professional background leading up to that?
It’s a bit of a meandering path, but my background is in mechanical engineering. My Bachelor’s is in mechanical engineering, and after undergrad, I went to work in the railroad industry doing product design. I became very familiar with the different aspects of product design and the need to satisfy the sometimes conflicting needs of our end customers. In the railroad industry, most of our products need to be able to take a beating.
In some cases, that need is literal – the product may be used as a hammer, even if it wasn’t meant to be a hammer! I became fascinated by the important role that materials play in product design and decided to go back to graduate school to study composites. I already had some experience working with composites in my undergrad and even before then, so I went to the University of Tennessee for my PhD and studied under Dr.Uday Vaidya, a world-renowned expert in advanced composites manufacturing.
Grad school gave me a deeper appreciation for the interplay of part design, materials, and manufacturing and the strengths and limitations of conventional manufacturing processes. Companies often approached our lab with a project in which they wanted to switch a metal part over to a carbon fiber part, for example. They wanted to make something that was stronger and lighter, but they didn’t know how.
Together with other grad students in the group, I would guide these companies through different ways that they could make a part out of carbon fiber based on part complexity and production volume. We would then go through prototyping and testing to ensure that the resulting product fit their needs. For me, this hands-on approach was really the best form of graduate school that I could have chosen, solving real problems for companies that had a need. That is especially true because I never quite saw myself as a scientist, more as an applied researcher.
How has this willingness to solve real-world problems informed the co-founding of Vitriform3D?
The fact is that in the US, there’s a minimum amount of glass waste needed in a region to make a traditional glass processing center economical. These centers take in tens of thousands of tons a year to be profitable. For these processing centers, contaminants like stone and ceramic are a major concern, and the higher volumes allow them to afford specialized automated equipment to remove contaminants. While these processing centers excel in producing cullet to make new bottles or fiberglass insulation, they also create a market opportunity for technologies that can harness lower volume, lower quality glass supplies.
And thatās where our technology comes in. We can work with lower-quality glass and lower volumes of glass because we use a room-temperature 3D printing process. For us, it doesn’t matter if there’s a little bit of ceramic blended in. If there happens to be a coffee mug that made its way into that glass scrap, it’s fine. We also have flexibility as far as the quantity we take in. Our goal is to be able to build regional factories that can process up to 10,000 tons of glass per year, converting it into 3D-printed engineered stone products.
Could you tell us more about Vitriform3Dās technology and its potential applications?
Most companies that are offering 3D-printed glass target very small, low-volume applications, such as lenses, for instance. That is fantastic work, and some of these companies can even use recycled glass in their process. Where we stand out is that we will produce larger scale, higher volume products because we are using binder jetting as our core technology. This powder-based process is well adapted to work with a wide variety of materials. We’ve already proven that it can work with crushed glass, which is essentially sand.
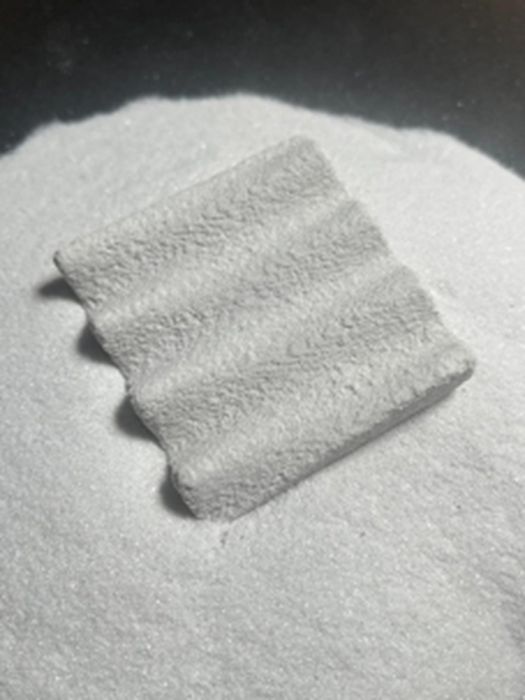
Developed alongside cofounder Dr. Dustin Gilmer, a binder jetting expert, our patent-pending addition to the technology is that we are combining binder jet printing with photopolymers. Using UV-curing polymers as our binder, we can streamline the binder jet process to get parts with full strength directly from the print bed. We don’t need to sinter or oven-cure it afterward. Stone-like strength is achieved straight out of the print bed, rivaling or even exceeding the strength of typical cement and engineered stone products.
Photopolymers will also enable us to tap into other aspects of inkjet technology, such as full-color printing. UV binder jetting will produce parts with stone-like properties in a vast range of textures and full-color patterns or even embedded graphics such as logos. Our technology is particularly appealing to architects and designers. The combination of aesthetics and strength is especially well-suited for interior and exterior surface applications. If you think about the fiber cement board that would go on the exterior of a house as cladding or siding material, thatās what we are targeting. If you think about tile, whether that’s porcelain, ceramic, or cement tile, we are targeting those types of applications for interior and exterior use.
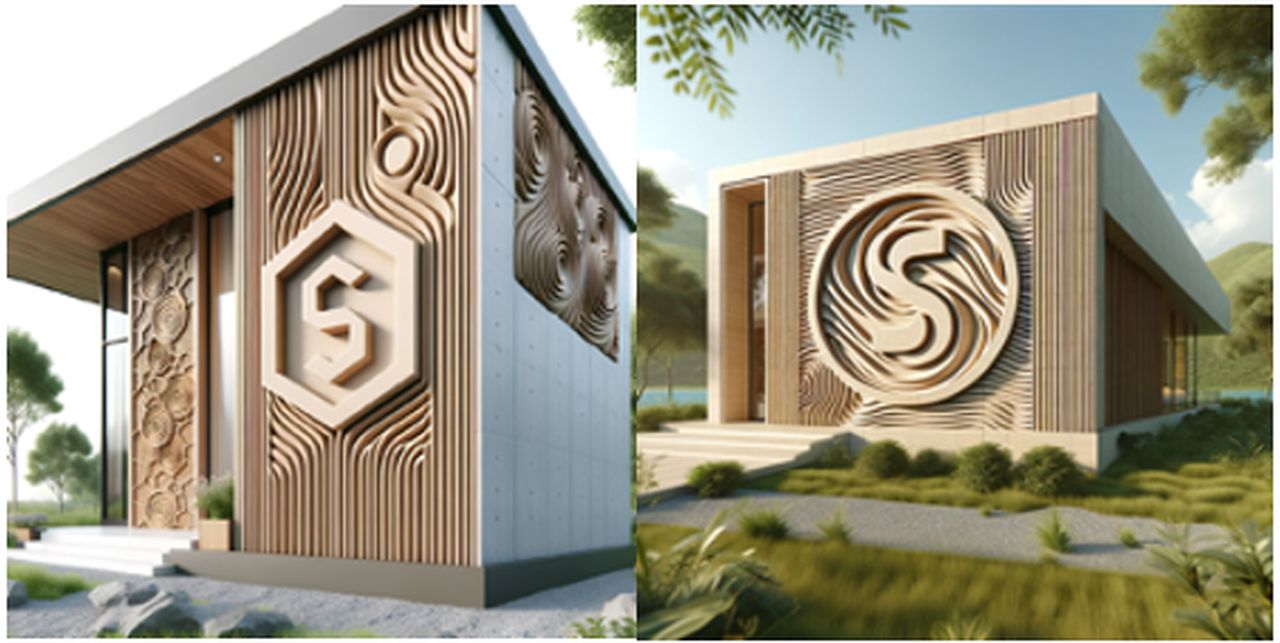
In addition to the design freedom offered by our technology, there is a tremendous carbon reduction benefit to printing with recycled glass. Cladding materials are the 3rd highest source of embodied carbon in a typical home, and building materials overall are responsible for 11% of global greenhouse gas emissions. With 95% locally sourced recycled glass, zero cement, and no kiln firing, our 3D printed products will have an embodied carbon estimated to be 4x less than a typical ceramic tile or fiber cement board.
At which stage of development and testing are you currently in? What were some of the main milestones so far and what do you envision for the future of Vitriform3D?
Right now, we are at the prototype stage. We’re a spin-off company from the University of Tennessee, Knoxville. My co-founder, Dr. Dustin Gilmer, and I had this concept together. Dustin is an expert in binder jet technology and worked on that for his entire PhD. My background is on the composites manufacturing side. We were able to come together with this concept by bringing my experience in photopolymer composites and his experience in binder jetting. Vitriform3D is licensing the technology from the University.
The development process started with concepts in 2021. We have since worked with senior design groups at the University to help get our first proof-of-concept printer to demonstrate the functionality of combining UV curing with glass powder. We were then accepted into Oak Ridge National Laboratoryās Innovation Crossroads program in 2022. This program has given us access to world-class scientists in additive manufacturing and allowed our company to go from basic bench-top scale testing to full prototype capabilities. Through Innovation Crossroads, weāve developed our next-level prototype printer, a custom system from B-Jetting. This equipment will give us the flexibility for binder development and test different glass powders, different color combinations of glass, and even blend in other materials.
While we’re still in the R&D phase, weāve secured over $1.1 million in funding from the U.S. Department of Energy. This funding will take us through our next printer, a robot arm-based system capable of printing 3-ft by 3-ftpanels. This pilot scale system should be operational within the next year.
We anticipate launching our first 3D-printed building product line in 2025. In 2024, we plan on raising a seed funding round to help us grow our team and secure a location for commercial production.
Before we conclude, could you tell us more about Fourth & Glass Recycling Co. and how it relates to Vitriform3D?
We are part of the circular economy, and our company is actually two companies in one. We recently launched Fourth & Glass Recycling Co., which is responsible for glass collection and processing to bring in the raw material supply that can then be utilized by Vitriform3D.
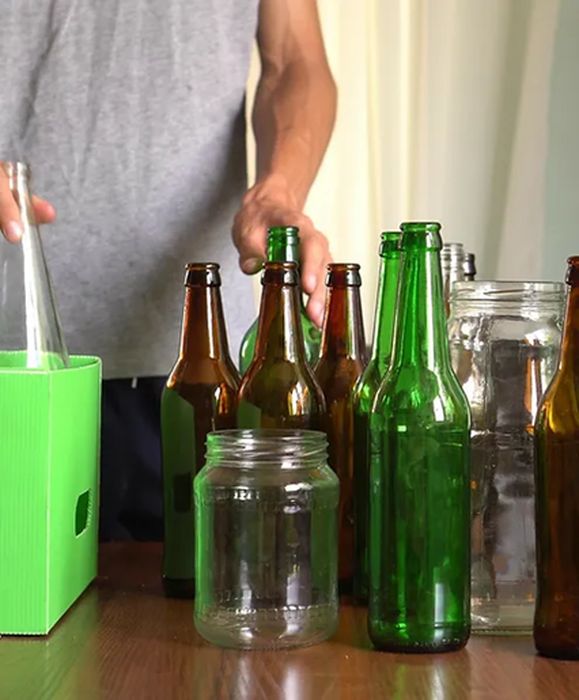
Fourth and Glass grew out of the same circumstances that led to the creation of Vitriform3D, which was that moment when glass was dropped from the curbside collection. As we’ve been developing the technology, we started to bring more and more glass into our lab, and we realized that there was still this unmet need in Knoxville – residents who are interested in recycling glass but want to have the convenience of a curbside program.
For us, launching a residential glass pickup program is a great way to help meet this need. We now have 108 households subscribed for collection, and so far weāve been diverting over 1 ton of glass per month from the landfill. Our goal is to have 1000 subscribers.
In the next few years, as this program expands, it will feed directly into our 3D printing process. What we are envisioning for Knoxville is a factory with 10 large-scale robot arm binder jet printers. Together, they will be capable of producing 5,000,000 square feet of tile or exterior cladding per year, diverting up to 10,000 tons of glass from Knoxvilleās landfills. From there, our goal is to build regional-level factories throughout the country.
Conclusion
Our conversation with Alex Stiles from Vitriform3D gave us an interesting perspective on how additive manufacturing can help reduce the proportion of glass waste that ends up in landfills across the U.S. Potential applications of 3D-printed, stone-like products in architecture are particularly exciting and add to the vast array of transformative solutions that promise to revolutionize our built environment.