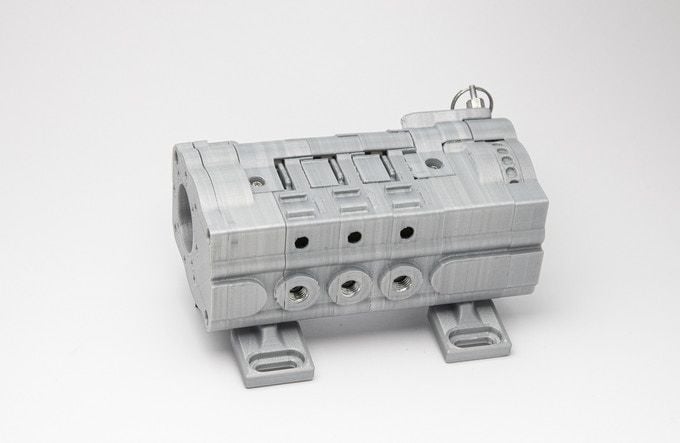
A new Kickstarter project offers a different kind of 3D printer multi-material upgrade.
3Dfeedy has developed a replacement filament feeder for desktop 3D printers that implements automated multi-material changes. In other words, you can load up to nine different spools and 3Dfeedy will control which one is delivered to the 3D printerâs hot end during printing.
There are several solutions on the market for upgrading to multi-material capability, including:
- Mosaic Manufacturing Palette
- Prusa MMU
- 3D Chameleon
These products exist simply because itâs far too expensive and sometimes impractical to add more extruders and hot ends to a 3D printer (although the E3D Toolchanger might contest that statement). The idea is to leverage existing hardware and provide a means to swap the filament only.

3Dfeedy works slightly differently from the others in that it requires only a single stepper motor to both feed filament and switch filaments. The Prusa Research MMU2S, for example, has one motor to drive filaments to the hot end, and another to rotate a cam to select different filaments. Iâm not sure how 3Dfeedy does it, but I suspect thereâs some sequence of movements that cause its selection mechanism to activate. The result is a device with one less motor to pay for.
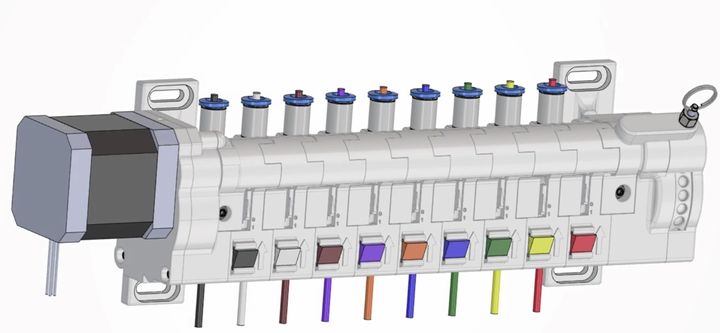
Another interesting feature of 3Dfeedy is that it is modular â you can add more or fewer selectors depending on your needs. The base 3Dfeedy includes the ability to handle three filaments, but you can add more selectors up to nine in total. Thatâs more than any other filament switching technology Iâve seen so far.
3Dfeedy says their product is able to handle a wide variety of materials, particularly flexible materials. This seems curious, as youâll soon understand.
3Dfeedy physically is two components: one is the main switching unit that you can clip onto the top or side of your existing 3D printer. It accepts the input filaments and pushes the selected material.
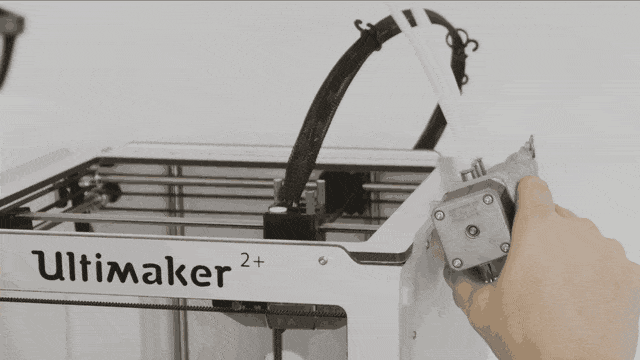
The other component is a multi-orifice device that is inserted into the 3D printerâs hot end. Unlike the MMU2S, where the filament is isolated âfar awayâ from the hot end, 3Dfeedy does this just above the hot end using this component.
This seems to be me to a be a somewhat superior approach than the MMU2S, as the filaments are permanently âloadedâ and need only to be pushed or pulled. On my MMU2S, I am constantly opening it up to ensure filaments are positioned properly; this should not be required on 3Dfeedy.
However, I think you might be realizing whatâs actually going on here: 3Dfeedy is simply replacing a Bowden extrusion system. In a Bowden system, the filament is pushed down a long tube towards the hot end. In a direct drive system, the filament is pulled from the hot end instead.
Because a Bowden system has an external (from the hot end) drive, it is much more easily replaced, as shown in the images from 3Dfeedy.
This makes a lot of sense, but then 3Dfeedy says their product is compatible with all 3D printers, except those with closed systems. Does this mean it could be used with a direct drive system?
Sort of. I read 3Dfeedyâs explanation of how this is accomplished, and they suggest using both the direct drive and adding a Bowden stepper motor to operate 3Dfeedy. This would end up configured something like the MMU2S, with an extra motor. That defeats the motor advantage of 3Dfeedy, however.
3Dfeedy also says you can simply ignore the motor on your direct drive system and operate it like a Bowden system. Iâm not sure owners of direct drive machines would like to do this, however, as they chose their machine for reasons.
Back to flexibles. Since the filaments are retracted only slightly with 3Dfeedy, it may indeed be possible to use them. However, I suspect this works best if there is a direct drive system involved, since pushing a flexible noodle-like filament down a long tube is not going to be reliable. Thatâs why Bowden systems have so much trouble with flexibles, and I canât see why 3Dfeedy wouldnât have the same issues.
Software is done externally. 3Dfeedy says you slice your 3D model on any slicer, and then post-process it on their software, which will be offered online for maximum platform portability. It would seem that you would use the original slicerâs ability to choose multiple materials, and then 3Dfeedyâs software will alter the material changes within the command stream to use their GCODE snippets.
As of now, 3Dfeedyâs Kickstarter is still active for a few more days. Theyâre offering the system for âŹ248 (US$299), which is comparable to the MMU2S, and a lot lower than the Palette. Note: they are shipping only to certain European countries at this stage, but hope to expand shipping in the future.
Via Kickstarter
This appears to be not much different than the mmu1 which did not work that well and was only used on the prusa mk2. retracting to unload is complicated, as is keeping the filament from getting stuck in the manifold, and that was with 4 filaments, image what sort of a porcupine it will look like with 9.
I had a palette for 30 days (amazon return) and that was one of the most promising options for use with any printer, in that 30 days i was able to print 1 item successfully. the rest failed spectacularly.
I don’t hold out much hope for this device.