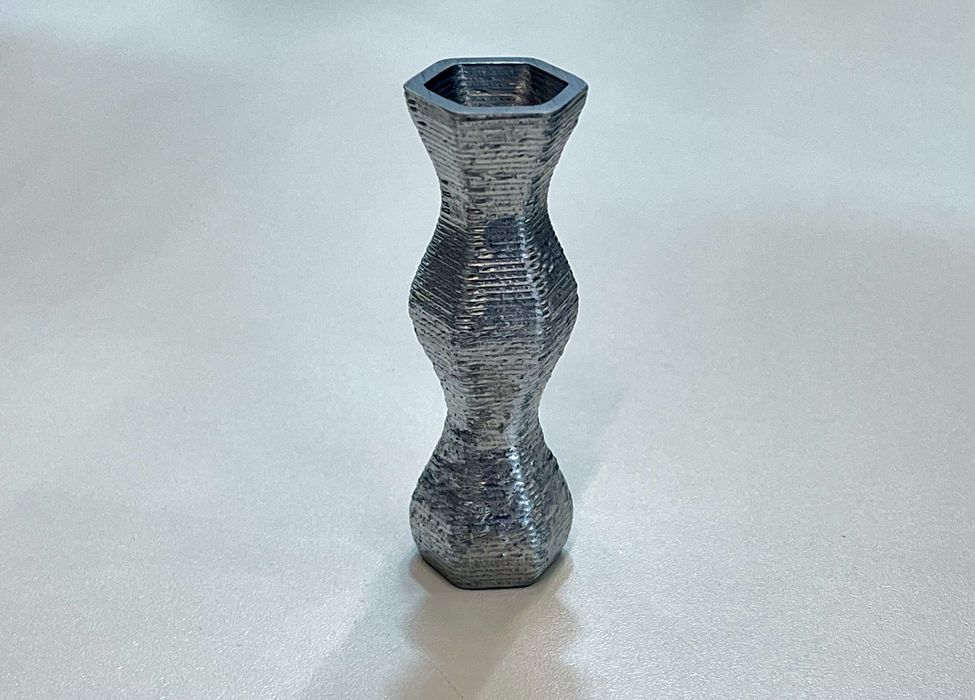
A startup seems to have developed a way to 3D print liquid aluminum.
At Formnext 2022 we had a discussion with a Belgian startup that Iād never heard from previously. Founded only in 2019, ValCUN is developing a unique process for 3D printing aluminum, which uses a nozzle to extrude liquid aluminum.
Ok, that sounds preposterous: the liquid aluminum would pour out of the nozzle just like opening a Coke upside down, wouldnāt it?
Wouldnāt it?
Well, it turns out thatās not true. Somehow theyāve got this figured out. Essentially, they can print aluminum in the same way as FFF 3D printers operate.
Instead of filament, ValCUN’s process uses aluminum welding wire, something thatās commonly available. The ceramic nozzle is heated to something around 800C, sufficient to melt aluminum. In fact, they say the temperature is ājust above the melting pointā.
How on Earth does this possibly work? Evidently ValCUN has determined a way to have proper volumetric extrusion: for every 10mm of aluminum going into the extruder, 10mm worth of aluminum comes out the nozzle. They say they can precisely stop the extrusion ā no leaks ā and this is apparently done without retraction.
I pressed the companyās metallurgist, Dr. Chola Elangeswaran, on how exactly the liquid aluminum is extruded so precisely, but all he would admit is that their secret process has something to do with āsurface tensionā of the aluminum fluid. By tweaking parameters they can alter the properties of the extrusion.
The prices can print aluminum objects in 1mm layers, but theyāve already experimentally achieved layers as thin as 0.7mm and as large as 4.0mm. Company representatives insist that 0.1mm layers are possible in the future.
Even so, the images show an object with a somewhat coarse surface texture. While that might be unsuitable for, say, a hip implant, rough surfaces would be perfectly fine for many applications.
The aluminum freezes almost instantly when extruded, and this allows the system to build up 3D objects. In addition, it also permits extreme overhangs. Apparently they can handle overhangs of up to 10 degrees off horizontal, which is quite impressive, and suggests the system could be made to print complex geometries.
Elangeswaran told us that it is theoretically possible to use their process with other metals besides aluminum, but that for the moment they are focusing on aluminum because it is often difficult to print with LPBF and the lower melting temperature simplifies things somewhat.
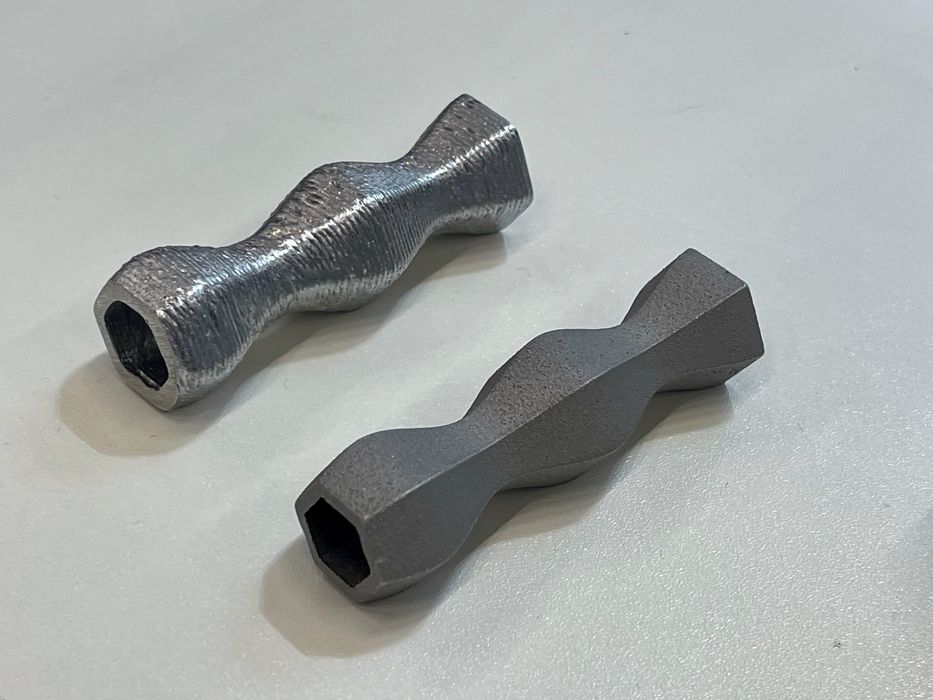
The play is is all about cost. Here we see an object printed with two different processes: ValCUN’s on the left, and a standard LPBF process on the right. The LPBF part would typically cost about US$100 to produce. Meanwhile, the Valcun part cost was said to be āmore than 10X cheaperā to produce.
They may be a bit vague on costs, but thatās likely because they arenāt producing a 3D printer. This project is all about the print head technology, which could be integrated into a variety of 3D print systems. Itās likely ValCUN will license the tech to existing 3D printer companies, particularly those with FFF tech seeking ways to enter the metal market. They say they are currently doing āpilot projectsā with unnamed partners, so we may see this technology appear a lot faster than expected.
Combining the rough surface quality with low cost suggests to me that this technology could be of significant interest to the countless companies producing inexpensive metal parts that have been left behind by the extreme costs of the LPBF process. There could be a vast market for this tech.
As for the future, ValCUN is also developing a āgreen scrap toolheadā. The idea here is that instead of using welding wire, use aluminum scraps. These would presumably be chopped up into bits and then fed into the system, permitting true aluminum recycling onsite and perhaps even within a 3D printer itself.
The ValCUN technology is one of the most interesting Iāve seen lately, as it could be a huge enabler for expanded use of AM in metal foundries.
Via ValCUN