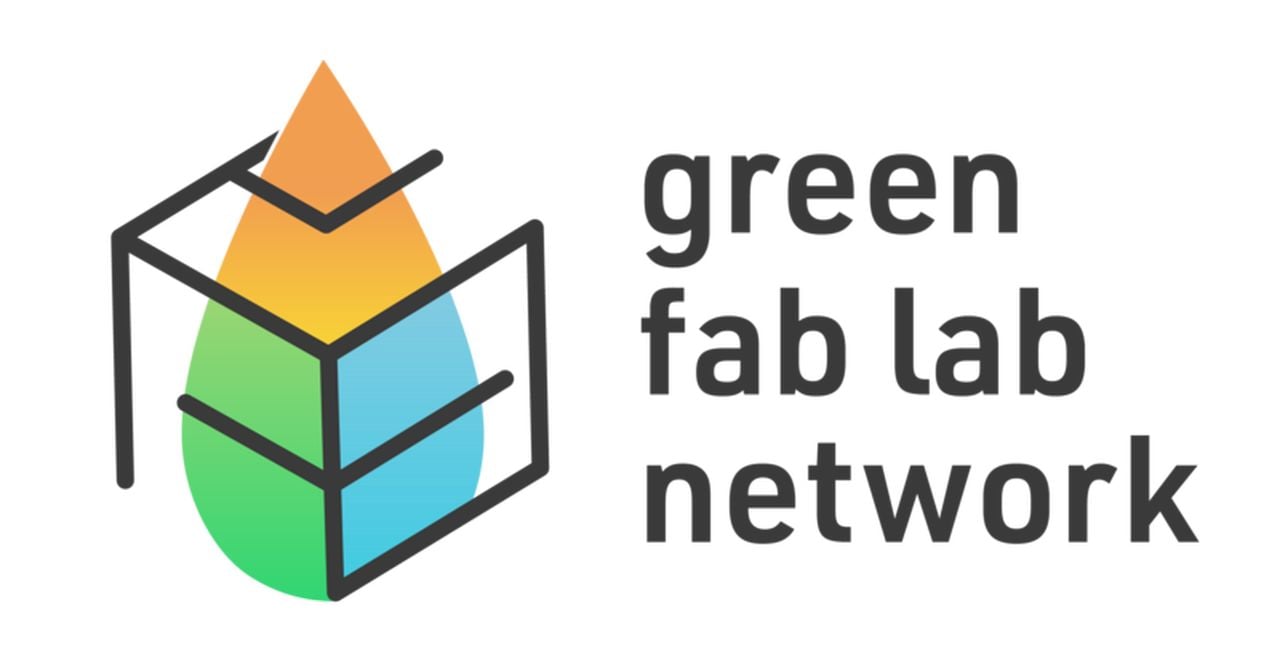
I’m reading a paper analyzing the economic effectiveness of the Green Fab Lab Network concept.
The “GFLN” is a distributed network that promotes “green” practices for fabrication labs and makerspaces. They say:
“We are a distributed network that works promoting green entrepreneurship. Our business models include green fab academy, boutique hotels, and green eco factories, and integral biofarms.”
One of those practices could be to capture some of the waste 3D print scraps that inevitably are produced by 3D printers.
Those scraps include failed prints, spaghetti, support structures, and waste filament coils.
Normally, fabrication labs tend to throw this stuff in the trash, as there aren’t any convenient (or sometimes any) ways to properly recycle the material.
The research paper, entitled, “Green Fab Lab Applications of Large-Area Waste Polymer-based Additive Manufacturing” proposes a system to perform recycling on site at these facilities.
Their concept is that a fabrication lab could serve as a kind of local recycling facility for 3D print waste. They explain:
“With the use of industrial 3D printers capable of fused particle fabrication/ fused granular fabrication (FPF/FGF) printing directly from waste plastic streams, green fab labs could act as defacto recycling centers for converting waste plastics into valuable products for their communities. Clear financial drivers for this process have not been studied in the past.”
The paper then proceeds to do that very analysis by performing experiments with a Gigabot X, a typical 3D printer one might find in a makerspace.
Their analysis technically involved using waste material as input, and producing “large sporting equipment” test products, with ABS, PLA, Ninjaflex and PP as the materials. Their analysis included not only the technical feasibility, but also a complete, end-to-end view of the costs of the process, including electricity consumed.
Products produced included skateboards, snowshoe parts, and paddles.
The experiment tested both pellets and granular material, which would be the normal input from recycling streams. However, this would require a device to chop up the scraps into appropriately sized chunks. The use of pellets and granular material eliminates the need for any type of filament-production equipment.
The Gigabot X is a fairly large machine, with a build volume of at least 610 x 610 x 610 mm. This allows the device to produce larger objects that would be less susceptible to the vagaries of random recycled input materials.
The paper estimated the cost of the Gigabot X machine at around US$22,000, including the specialized pellet extruder, so it’s not inexpensive to get this program launched, especially for often-poor makerspaces.
However, those startup costs were amortized over several years and offset against prints made with the device.
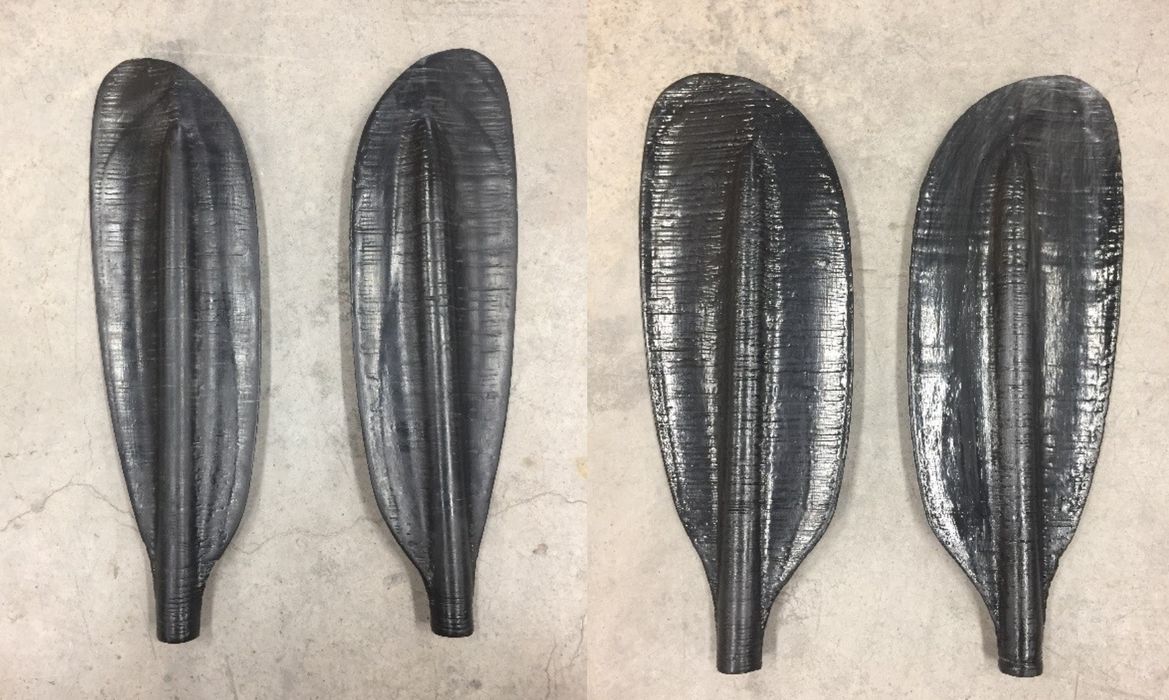
They found that the costs of producing the sporting goods products was vastly less than if using standard filaments. This is unsurprising, given that pellets are less expensive, and in this case the cost of scraps is zero. Thus the real cost in running the machines was electricity and a bit of operator time.
The paper investigated a number of operational scenarios, including “one print per week” all the way to “continuous printing”. In all cases, they found the configuration could make at least a small profit. Depending on the sale price of the items produced, the payback time was as low as 0.04 years (two weeks).
That’s an impressive result, and shows that it may be possible for fabrication labs and makerspaces to become profitable recycling depots for local areas.
The next step would seem to be a standard configuration and operating process for this approach that could make it easy for labs to participate.
Via Green Fab Lab Network and Academia