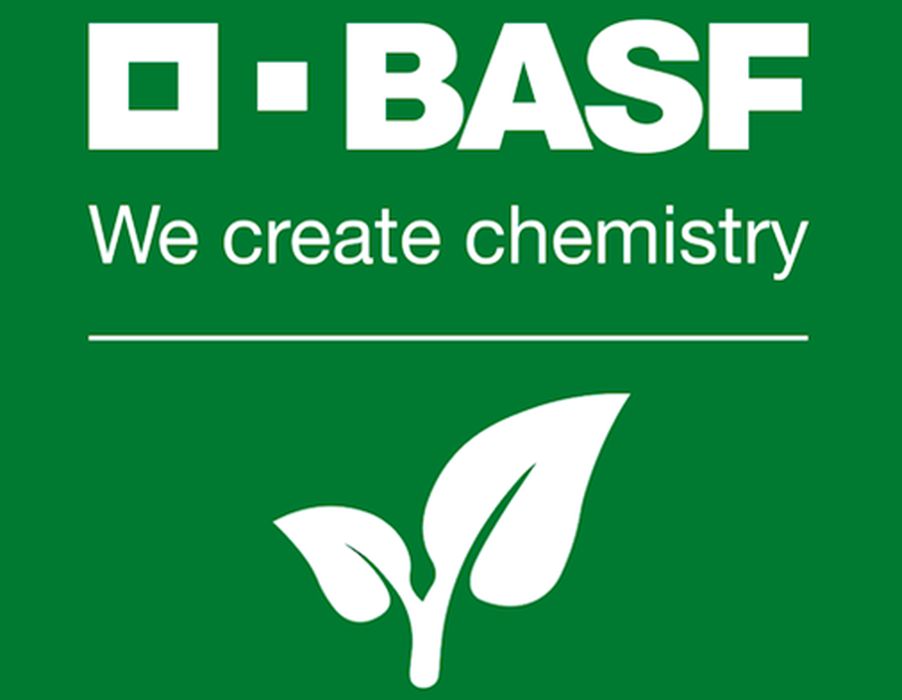
Charles R. Goulding and Preeti Sulibhavi examine BASF’s moves in Europe and Asia.
BASF, the world’s largest chemical company, is reducing its industrial operations in Europe while increasing its activities in Asia. BASF’s new US$10B China plant that we covered in 2020 has just opened last month and it appears it is just the beginning of BASF’s de-industrialization in Europe and expansion into Asia.
The prime culprit for the de-industrialization in Europe, not only of BASF but of companies in various verticals such as steel, cars and even personal product manufacturers, is the increasingly prohibitive cost of energy in Europe now. This, of course, can be directly attributed to the war in Ukraine. We have covered how the international glass industry is shifting resources and operations to other regions as well, all because of high energy prices.
BASF and 3D Printing
Recently, BASF has been involved with several 3D printing projects. In 2017, BASF 3D Printing Solutions GmbH, a subsidiary of BASF New Business GmbH, was formed. BASF 3D Printing Solutions GmbH also offers an Additive Manufacturing (AM) chain under the brand, Forward AM.
The majority of their customers are companies looking to use 3D printing for industrial production.
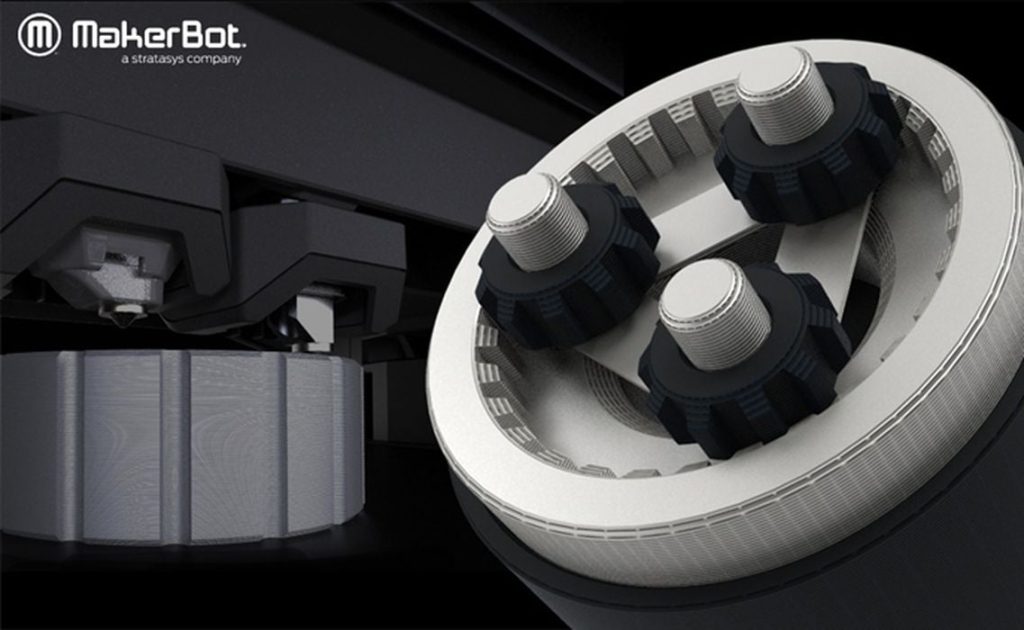
In 2021, Stratasys announced that the BASF Ultrafuse 316L Stainless Steel material by Forward AM was qualified for the MakerBot LABS™ Experimental Extruder for the MakerBot METHOD® 3D printers. This was a huge development in the industry and really solidified BASF’s commitment to advancing 3D printing in its industry and beyond.
BASF invests in research and development, as well as in business development of the industrial and functional application of 3D printing. Together with numerous specialist industry partners, new materials, integrated system solutions and service offers are developed continually. BASF R&D laboratories are located in Ludwigshafen (Germany), Lyon (France), Shanghai (China), and Wyandotte (US).
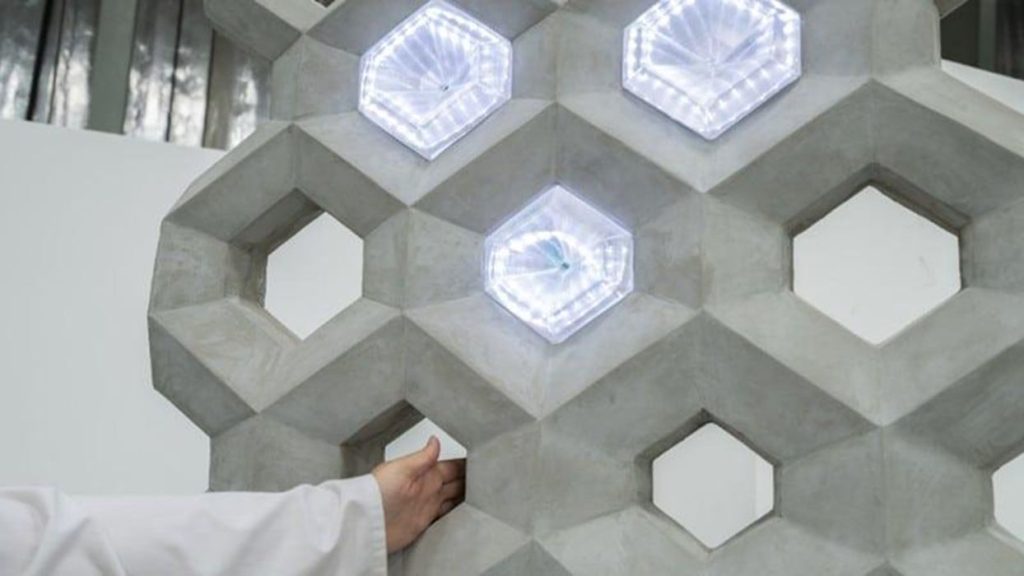
In 2020, BASF offered 3D printing products on its 1688.com online flagship store. With more than 20 products for 3D printing, including plastic filaments and UV-curable photopolymers, the online channel only enhances conventional distribution channels and support customers in different segments that include local, small and micro businesses.
An example of 1688.com’s relevance in the 3D printing industry is its use of Ultracur3D® ST 45B, a polymer product that can fulfill the requirements of functional applications regarding high accuracy and mechanical strength, where existing photopolymer materials often show limitations.
More 3D printing products including metal filaments for fused filament fabrication (FFF) and plastic powders for Selective Laser Sintering (SLS) will be rolled out on this online platform soon. The products are also environmentally sustainable as well.
“The ability to validate Polypropylene prototypes in the same base material as production enables cost and time saving opportunities for all customers,” said Aaron DeLong, Solutions Architect for HP (in collaboration with ShapeWays). “Further, this breakthrough provides enhanced saving opportunities in bridge production, full production, and service applications,” DeLong went on to say.
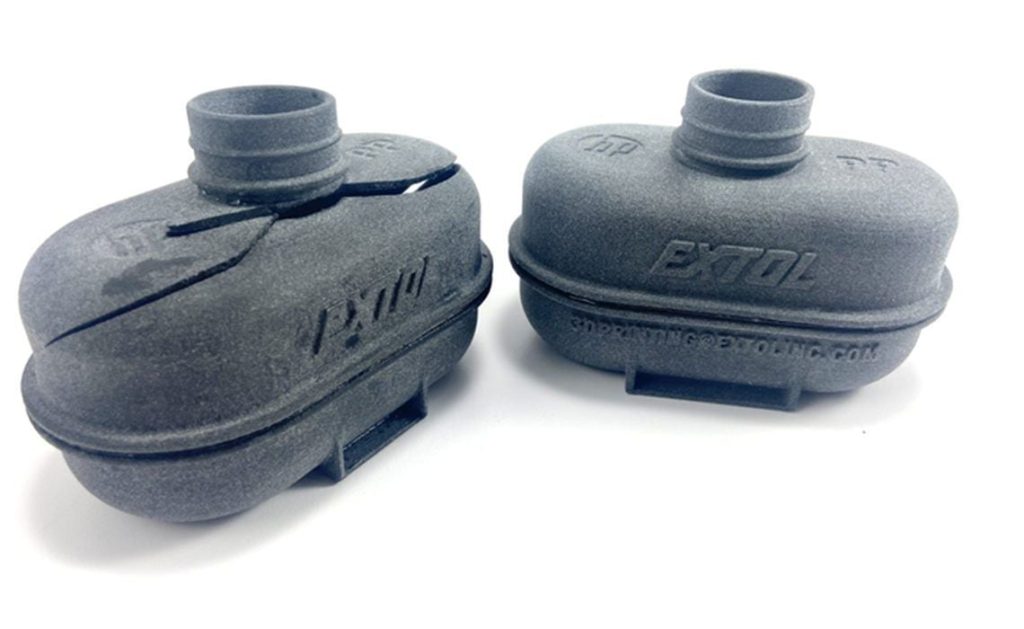
Confronting the energy price increase, BASF has embarked upon a US$500M cost cutting program. In the first nine months of 2022, the additional costs for natural gas at BASF’s European sites amounted to around €2.2B compared with the same period in 2021.
“First, the European chemical market has been growing only weakly for about a decade. Second, the significant increase in natural gas and power prices over the course of this year is putting pressure on chemical value chains,” said Martin Brudermüller, CEO.
“Moreover, uncertainties due to the enormous number of regulations planned by the E.U. are weighing on the chemical industry,” Brudermüller added.
The Research & Development Tax Credit
The now permanent Research and Development (R&D) Tax Credit is available for companies developing new or improved products, processes and/or software.
3D printing can help boost a company’s R&D Tax Credits. Wages for technical employees creating, testing and revising 3D printed prototypes can be included as a percentage of eligible time spent for the R&D Tax Credit. Similarly, when used as a method of improving a process, time spent integrating 3D printing hardware and software counts as an eligible activity. Lastly, when used for modeling and preproduction, the costs of filaments consumed during the development process may also be recovered.
Whether it is used for creating and testing prototypes or for final production, 3D printing is a great indicator that R&D Credit eligible activities are taking place. Companies implementing this technology at any point should consider taking advantage of R&D Tax Credits.
Conclusion
The recent developments at BASF, its shifting of operations from Europe to Asia, should not be taken lightly. Hopefully, when global conditions are normal again, BASF can resume its 3D printing materials leadership position.