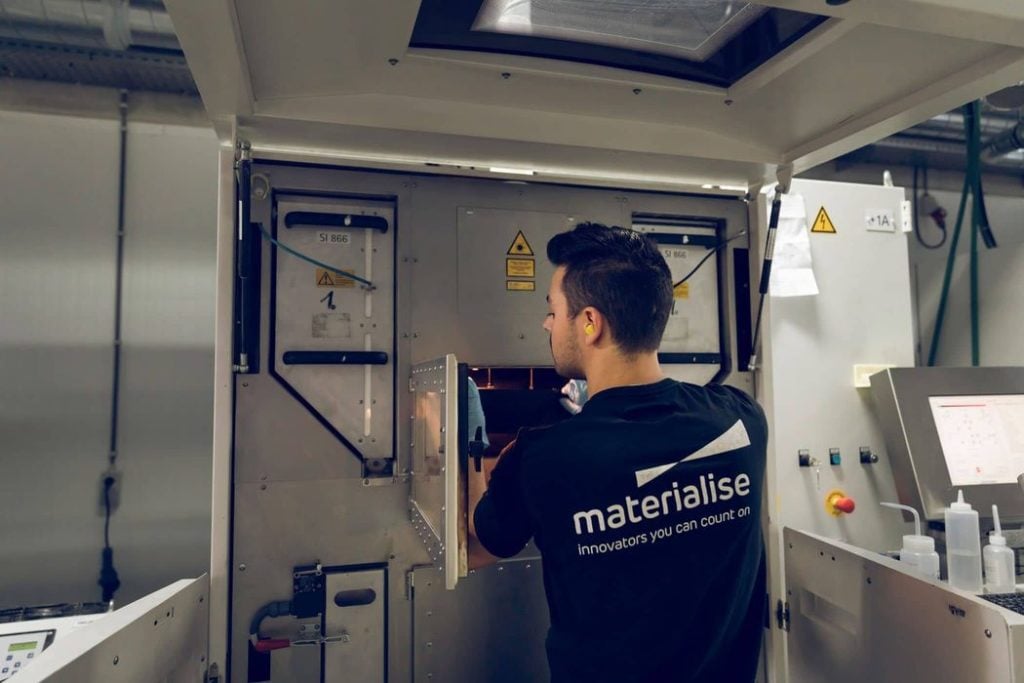
Smart data is a powerful tool that can enhance 3D printing and turbocharge manufacturing operations.
In the earliest days of 3D printing technology in manufacturing, traditional manufacturing processes and newer methods involving 3D printers and additive manufacturing existed in separate realms. The hardware and materials for 3D printing may not have even been under the same roof, with companies delegating production to contract manufacturers. As it becomes clear that 3D printing has staying power and the potential to add tremendous value to manufacturers, manufacturing and 3D printing are becoming less separate and are increasingly fully integrated.
With 3D printing working in tandem with traditional manufacturing systems, companies hope to make their operations more efficient and highly scalable while exerting greater control over their products. That isnāt possible if the systems fail to work together and communicate effectively.
The answer is smart data.
The Value Of Smart Data
Additive manufacturing and conventional manufacturing are two separate ecosystems that increasingly coexist on the same production floor. To realize all the benefits of integrating 3D printing, companies must give their systems a common language, and that language is data. It isnāt hyperbole to claim that an increased understanding of the power of data and analytics has transformed most major industries, and 3D printing and manufacturing are no different. As production environments become digital and new technology is integrated, manufacturers must be able to smartly and quickly analyze all the data generated and break down disparate data sets generated from new equipment, materials and processes and understand their relationship with established practices.
Data is at the heart of unleashing the gains in efficiency, repeatability, scale and control that come with breaking down the walls between conventional manufacturing processes and 3D printing, and Materialise, a company offering software solutions for 3D printing, believes it has the answers the industry needs. Harnessing the power of smart data is needed to increase the adoption of 3D printing, according to Materialiseās Chief Technology Officer Bart Van Der Schueren.
āWidespread adoption of 3D printing has been a slow revolution, but today, companies are looking for efficient ways to adopt 3D printing for large-scale production across multiple sites. Historically, 3D printing and conventional manufacturing processes have been carried out in isolation from each other. Now, weāre seeing the walls between these two manufacturing environments disappear, and access to data and analytics will play a significant role in integrated production,ā he said.
If companies can utilize smart data while operating their 3D printers, they will be able to continue scaling and expanding production. Over the long term, this has the capacity to unlock the potential of 3D printing, helping designers and engineers to create better, more useful products with higher levels of efficiency. In this scenario, everyone wins.
An incredible number of data points are created during the 3D printing process because the material and product are created simultaneously, rather than cut and shaped from a sheet of metal or welded or bolted together. Applied correctly, data analytics in the 3D printing environment can lead to reduced scrap rates, improved quality and the prediction of failures before they occur so that preventive maintenance can help to avoid delays and rework. Over a long-term, smart data helps make it possible to identify which processes contribute to failures so that operations can be adjusted.
In the manufacturing world, generating data is certainly not the challenge. A single day on the factory floor can produce hundreds of thousands of data points that can be analyzed. Where expertise is really needed and where value can be unlocked is finding a way to do something with that data. Some of the larger manufacturing firms already employ fully staffed teams of data scientists whose expertise focuses entirely on the 3D printing industry. These companies have their own processes in place to explore and analyze data on their own. They just need the right software tools to help them harvest the data that is being targeted.
However, not every company has a strong data science team or the ability to invest heavily in analytics and software. For these companies, all that is needed are quick and dirty tools that can provide an overview of the data being generated. If they can extract useful data without a heavy investment or deep data analysis and can relay the key takeaways to their engineering staff, then that could be sufficient.
Whose Data Is It Anyway?
The rise of 3D printing has made it possible for manufacturing to take place anywhere that the right hardware and materials are available. With this shift in manufacturing comes rapid gains in the freedom to produce goods efficiently anywhere on the planet. As design information is distributed widely to contract manufacturers and 3D printers, there is another question that needs to be addressedāwho owns the data produced?
āOverall, itās less about the amount of data but rather about collecting the right data, using it the right way and the confidence to keep control and ownership,ā explained Van Der Schueren.
Ownership of the data and information related to printing specific products and goods is a sticky issue, especially in heavily regulated industries like the aerospace or medical industry. Companies are also extremely competitive and do not want to see their data analyzed by competitors seeking to gain an edge. Anonymizing data is one way to work around this matter, helping to fuel innovation without sacrificing that edge.
āMost manufacturers will not only claim ownership of designs and processes but also express the desire to control them. They may decide to share some of these insights in order to empower other users, but manufacturers should retain ownership and control. This will enable them to create smarter production processes that allow them to leap ahead of the competition,ā said Materialise Executive Chairman Peter Leys.
Read more at ENGINEERING.com