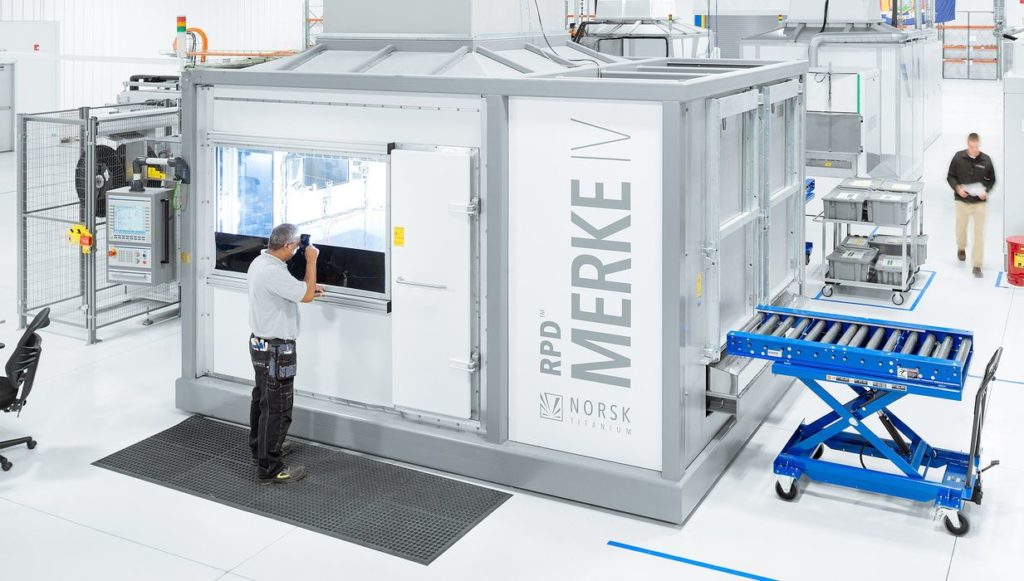
Norsk Titanium’s MERKE IV metal 3D printer is suitable for large part production.
The Norwegian company was founded 14 years ago in 2007, with a goal to provide a new means of producing high-quality metal parts for the aerospace industry.
In the intervening years the company has produced multiple generations of metal 3D printers, each with improved functionality. They’ve also received investment from several parties to boost their growth.
In 2017 the company 3D printed the very first FAA-approved structural part for a commercial aircraft, a titanium part for the Boeing Dreamliner 787 aircraft.
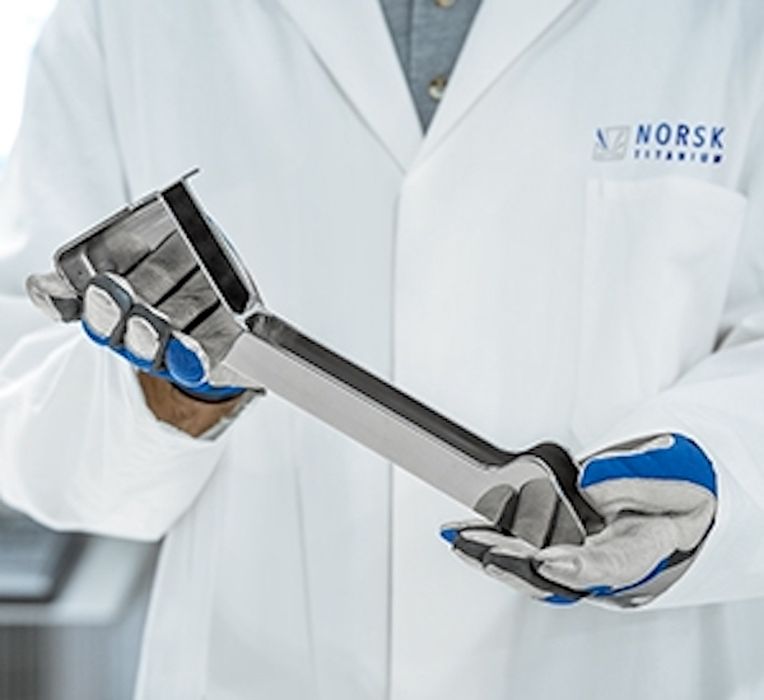
The company focuses on their own patented form of 3D printing process, which they call “RPD”, or “Rapid Plasma Deposition”. It’s similar to several related processes, but it involves extruding a metal wire into a hot plasma, where the metal instantly melts. By moving the melt zone with a CNC-style gantry motion system, an object can be gradually built up layer-by-layer.
They’ve leveraged this process into large-scale commercial metal 3D printers, with the current version being the massive MERKE IV, their fourth-generation machine.
This device has a massive build volume of 900 x 600 x 300 mm, as you can see in the image at top.
The plasma and extrusion takes place inside the build chamber, which is filled with inert argon gas to prevent reactions and increase print quality.
Norsk Titanium believes their RPD process can achieve superior metallurgy due to the nature of the process. Advantages include:
- Material properties (such as tensile, fatigue, and elongation) at the level of forged titanium*
- Basketweave wiedemann microstructure
- Consistent microstructure across layers and part features
- Absence of “lack of fusion” or voids in the material
One reason why they can achieve these results is that the MERKE IV carefully monitors melt activity 600 times per second. This allows the machine to easily make adjustments to ensure operations proceed in consistent conditions.
The material deposition rate is notable, at 5-10kg per hour, or 120-240kg per day.
One reason for the rapid deposition is the layer sizes achievable on the MERKE IV. According to specifications, the layer height is between 3-4 mm, while the layer width is 8-12 mm. These broad extrusions imply a healthy amount is deposited as the motion system operates.
That said, the resolution is rather coarse as 3D printers go. Because of this, it’s normally assumed that RPD 3D printed parts will undergo a machining step after printing to provide smooth surfaces.
Why not just CNC mill the entire part, then? It’s because the additive nature of the RPD process dramatically reduces the amount of metal being used. While there is still some machining involved, the overall weight of metal used in production is far less, sometimes dramatically so.
However, this also limits the possible geometries on the device to those matching CNC capabilities.
As you might guess, Norsk Titanium provides high-grade titanium wire as their prime material. This is a material frequently used in the aerospace industry due to its low weight and high strength. The company explained nickel alloys, tool steel and stainless steel can also be used on the MERKE IV.
Today the company also operates a US office based in Pittsburgh, where they continue to work with aerospace companies on advanced structural parts.
Via Norsk Titanium