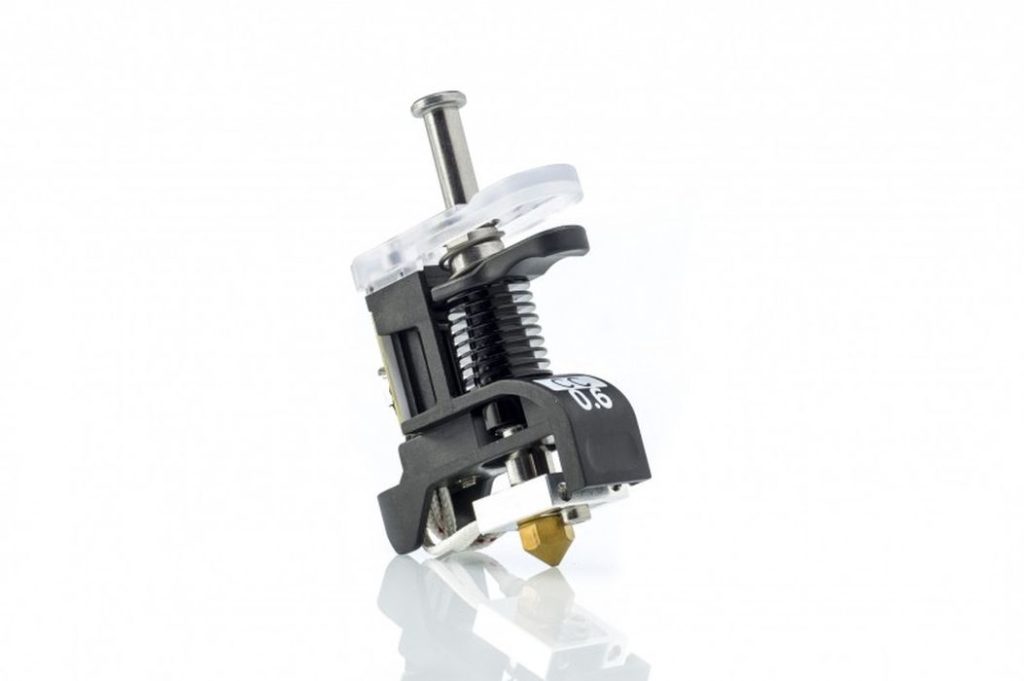
Ultimaker announced a significant update for their CC print core.
The print core concept is a powerful feature of the company’s S-line of 3D printers. It is a system for quick-swappable hot end / nozzles, and is used to accommodate different types of materials.
Ultimaker currently offers three different print cores: AA, BB and CC. The AA core is used for most common 3D printable materials, such as PLA, PETG, ABS, etc., while the BB core is optimized for water soluble support materials such as PVA. Finally, the CC core is a high-strength unit capable of handling abrasive composite materials such as carbon fiber-reinforced nylon, or glass-filled PETG.
The print cores include a chip that is read when installed on the 3D printer, and that means the 3D printer always knows what type of core is present. That information can be used to ensure there are no mistakes, where a job attempts to 3D print a filament on the wrong type of print core.
Now they’ve improved the CC core in several significant ways.
First, they have added a 0.6mm nozzle option, whereas previously the CC core was only available in the standard 0.4mm format. This means that it will now be possible to, for example, 3D print larger parts in carbon fiber material much faster.
The second improvement deals with the abrasive resistance of the nozzle. The original CC core used a ruby tip to counteract the highly abrasive nature of carbon or glass fibers that flow through the nozzle during 3D printing operations. Without protection, a common brass nozzle would be easily worn away after several large prints.
The new CC core does away with the ruby tip and instead uses a titanium-nitride coating. This unusual ceramic material is extremely hard, with a Vickers hardness of 1800-2100. According to Wikipedia, a coating of only 5 micrometers is required for significant protection, and that’s likely what Ultimaker is doing here.
Ultimaker has also swapped out the brass heat block on the hot end and replaced with with an aluminum equivalent. Since the thermal conductivity coefficient of aluminum is 239 and that of brass is only 96, there is a notable difference in heat flow.
In practice this means that not only is the heat more uniform around the filament path, but the heater block warms up to operating temperature a bit more quickly. That will be advantageous when performing repeated prints with swapped nozzles.
Jabil Additive Manufacturing Process Engineer Levi Loesch said:
“The new print core CC has been a workhorse for us here at Jabil. Our PA 4035 CF filament, which is a PA 12 with 35% carbon fiber by weight, is quite abrasive, so having a highly wear-resistant nozzle is a must. We were excited to learn about the new print core CC 0.4mm offering, which gives us the flexibility to print finer feature detail than the 0.6mm nozzle, while maintaining the same reliability and durability we’ve come to appreciate.”
This is a very good move by Ultimaker, as it strongly complements their ongoing strategy of expanding the breadth of available industrial materials. Now users can 3D print larger objects much faster, and do so for longer with the more resistant upgraded CC core.
Via Ultimaker