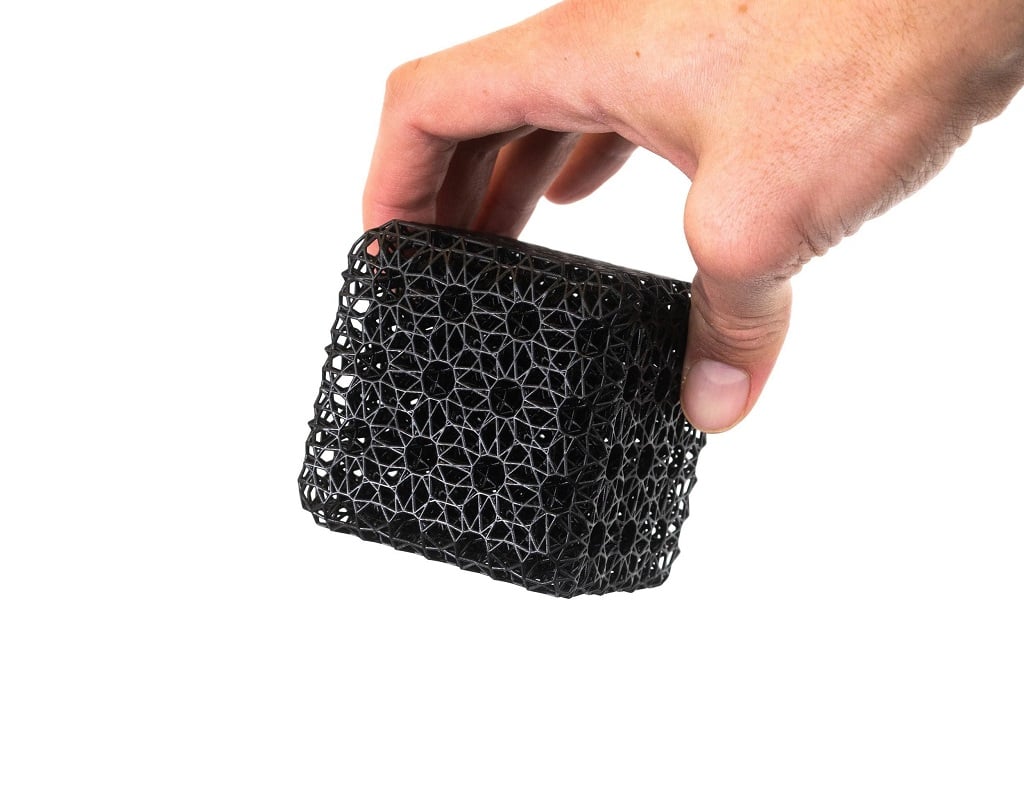
Carbon has introduced a new automated lattice design tool poised to send shockwaves throughout production-focused 3D printing.
Best-known for its Digital Light Synthesis (DLS) 3D printing technology and the hardware and materials that shape new products, Carbon also focuses significantly in software. Carbon’s software expertise is a driving engine for the company.
I spoke with Phil DeSimone, Chief Product and Business Development Officer, and Hardik Kabaria, Director of Software Engineering (R&D), for a look at the newly announced Design Engine.
Lattices in 3D Printing
One of the most oft-touted benefits of 3D printing is the technology’s ability to lightweight parts while maintaining high strength. Lattices are one of the most popular ways of enabling these capabilities. Optimized internal structures can ensure that the right mechanical properties are in place exactly where needed so a part can have the right support, give, or flex, for example. One of the most visible (and relevant) examples of this is the midsole structure of the adidas shoes Carbon enables:
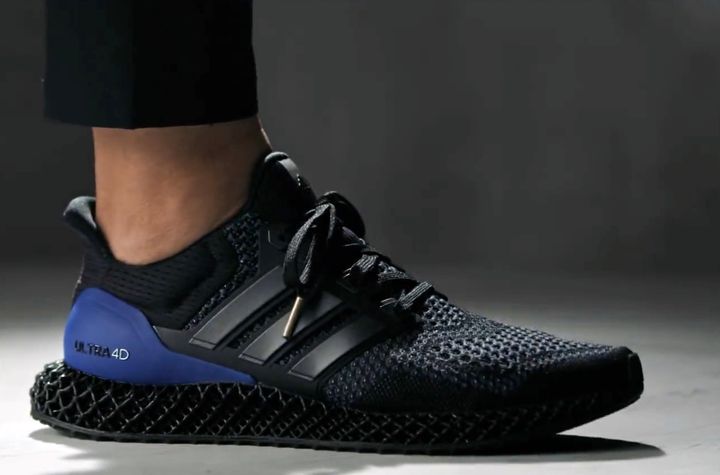
These lattices are also seen in others of Carbon’s growing number of high-profile announcements. Take, for example, the athlete-specific cushioning of helmets with 3D printed liners from Riddell and CCM Hockey. There’s also the bike saddles at Specialized and fizik.
They’re great products — but if they can’t be digitally printed, and mass customized, at scale, what’s the (commercial) point?
“When we started engaging with adidas in 2015 and really getting ready for applications going forward, what we realized quickly was the necessity for their ability to make designs repeatably,” DeSimone recalled. “This is not only for testing new designs out on a shoe level, but taking that design and making it available for every size, every half-size, for all men’s shoes and all women’s shoes. Previously something like that had to be done manually, but manipulating these without computer-aided help was detrimental. At that point in time, there weren’t a whole lot of options out there. We recognized that foam replacement applications would be a big opportunity for us at Carbon over the long haul. So we started investing our own resources.”
Kabaria led the development of Design Engine from the engineering side. The tool his team created has since become a backbone, DeSimone said, for scalable applications.
“This tool has powered some of the largest applications in additive that the world has seen to this point, whether the helmets we launched with Riddell and CCM, or the saddles with Specialized and fizik. They were all created using this tool, which is a backbone to make that process seamless and scalable,” DeSimone added. “That’s really what drove the creation of this tool. It wasn’t anything else, just need from our customers to do great things.”
Carbon Design Engine
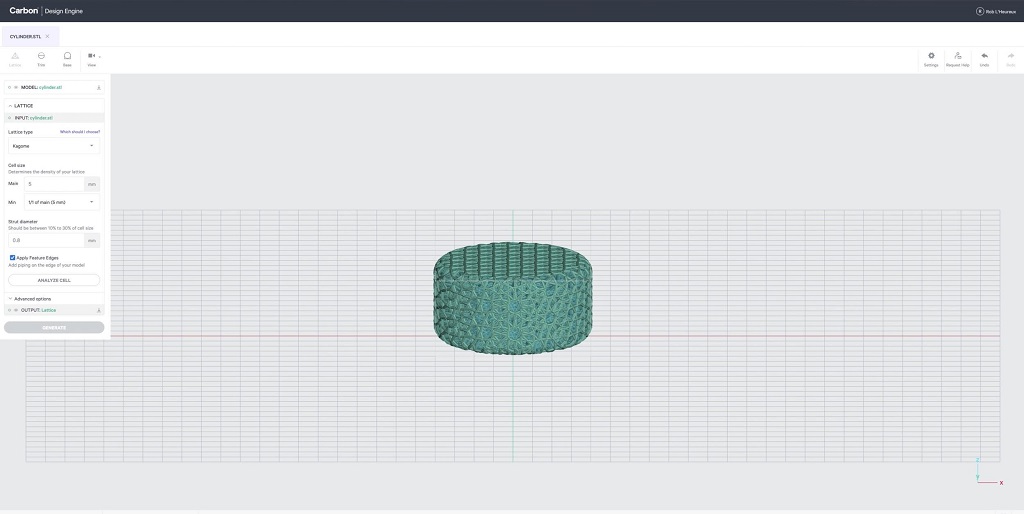
So what exactly is this tool? Design Engine is an automated software process that creates “performance-oriented lattices.”
Where helmets and bike saddles would traditionally have used foam, for example, engineers can now displace foam with application- (and even user-) specific lattice structures. Complex lattices allow for shock absorption, strength, and even collection capabilities. Think verticals like automotive, bedding, construction, electronics, furniture, packaging. Or, hey, how about COVID-19 testing swabs? The swabs developed with Resolution Medical were prototyped, optimized via Design Engine, produced, and out in the real world testing within a 20-day span.
Take special note of that timeframe, as acceleration is key to the power of Design Engine.
“This tool’s inception has been around wanting to help our customers build products that could be manufactured on our printer,” Kabaria noted. “We have a full end-to-end view of it. We were able to figure out the places where the product they’re making is better in some aspects, compared to some other designs they could produce using traditional methods. We wanted to achieve performance they could achieve no other way, or to enable mass customization not feasible other ways. Those became our north stars, as it were, wanting to make sure our customers can do those things.”
The customized helmet liners for Riddell and CCM offer a look at just what he means. 3D printing fully individualized helmet liners to protect specific heads is great — but beyond proof-of-concept, scalability is important. Carbon wanted to create a “tool that can automate design for any user-specific data” that “can be deployed on a manufacturing line,” Kabaria said. That way, when producing 700 helmets, “you don’t need 700 design engineers; you input the data from upstream and we catch it.”
Automation is great — but also key to unlocking the full potential of a scalable production solution is accessibility.
Built into Design Engine is know-how. Essentially, Kabaria and his team understand the intricacies of lattices — what they do, how they work, the many different varieties — so you don’t have to.
“Mechanical engineers might not know too much of lattices but want to take advantage. They don’t know which lattices are good for which type of mechanical behavior, for example. Design Engine can say, you want to imitate memory foam, here’s what we recommend and what you can expect to get out of it. We educate and shorten the journey,” Kabaria said. “You can take advantage of lattice design but don’t need a deep knowledge of lattice design to use it.”
Design Engine is a cloud-based tool, available now throughout the Carbon Production Network, that “provides the computational power to generate complex shapes quickly and efficiently without requiring local resources,” per the announcement.
Design Engine Implications
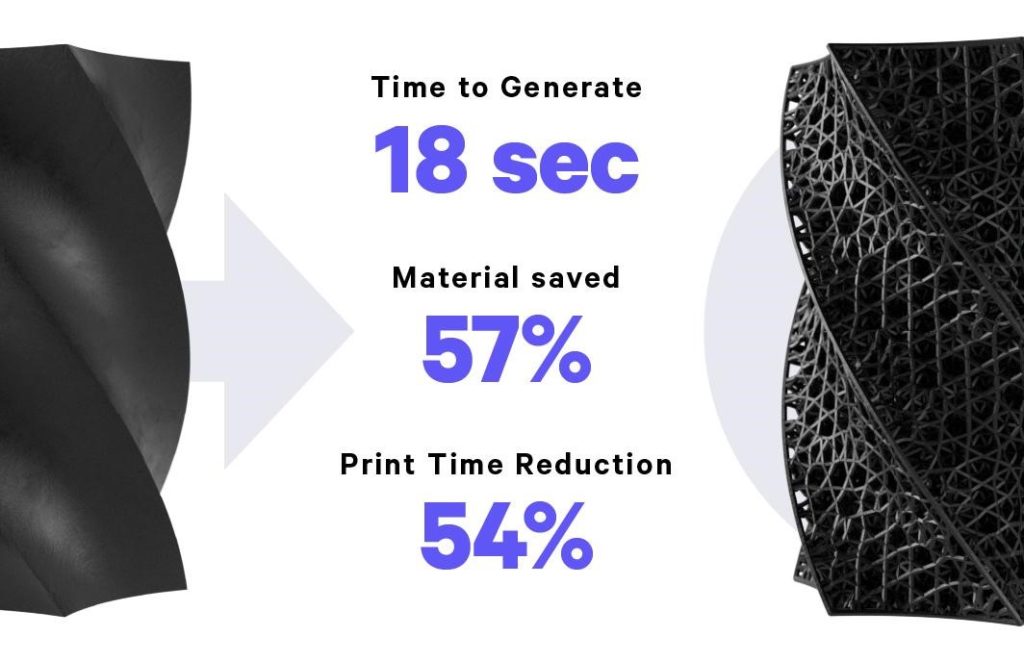
The Carbon team has been using Design Engine for some time now internally. Beta customers have brought it into their workflows. So, I asked: how has the real-world user reaction been?
“We’ve had great feedback already, and our entire customer base has access now,” DeSimone noted. “A lot of people have been surprised at how easy it is to use, but the second thing about it is speed.”
Ease-of-use for a fast, complex software solution makes for a very, very intriguing market launch — not just for Carbon, but for the 3D printing industry more broadly.
“We’re talking population of the lattice in a conformal manner in single-digit minutes, if not seconds,” DeSimone continued. “That’s been a major drag of time historically. You send your parameters in, the tool goes off and does its work and comes back hours later and you have your completed structure. This tool is very fast and has the ability to do lattices conformally with very little post-process manipulation in order to get the part to look like how you want it.”
This, though, is just the beginning for Design Engine. More advanced capabilities will be added as they develop. Multi-zonal manipulation and other deeper tools will continue to be added, further reducing bottlenecks during the discovery stage of new product development.
Ultimately, though, it’s not only the features that will be exciting, but the scope:
“The direction we’re going, from a Carbon perspective, is that there’s more around helping people through the product development process, whatever the technology they’re using,” DeSimone said. “We believe that expertise could be leveraged across all additive companies. This tool launch is not just big for DLS, but is important for the industry as a whole to find additional opportunities to rise all boats together.”
While Design Engine has its roots in DLS technology and materials, Kabaria added, “we believe it is easy to expand from there in multiple directions.”
“A lot of things about Design Engine are expandable; populating lattices, or moving from one type of lattice to another that can enable multiple mechanical qualities in one build. This will be powerful when available for other manufacturing methods,” he said.
The team still has to determine the best way forward for this wider reach, but “we also think lattices are the first pillar of design engineering we can do,” Kabaria said.
Taking speedy, intuitive advanced design generation capabilities to other technologies could be massive. Think, for example, what might be possible in metal 3D printing with custom implants, as one area of interest DeSimone touched on.
“I think design tools are something you’ll be hearing a lot more about from us in the future,” DeSimone summed up.
Via Carbon