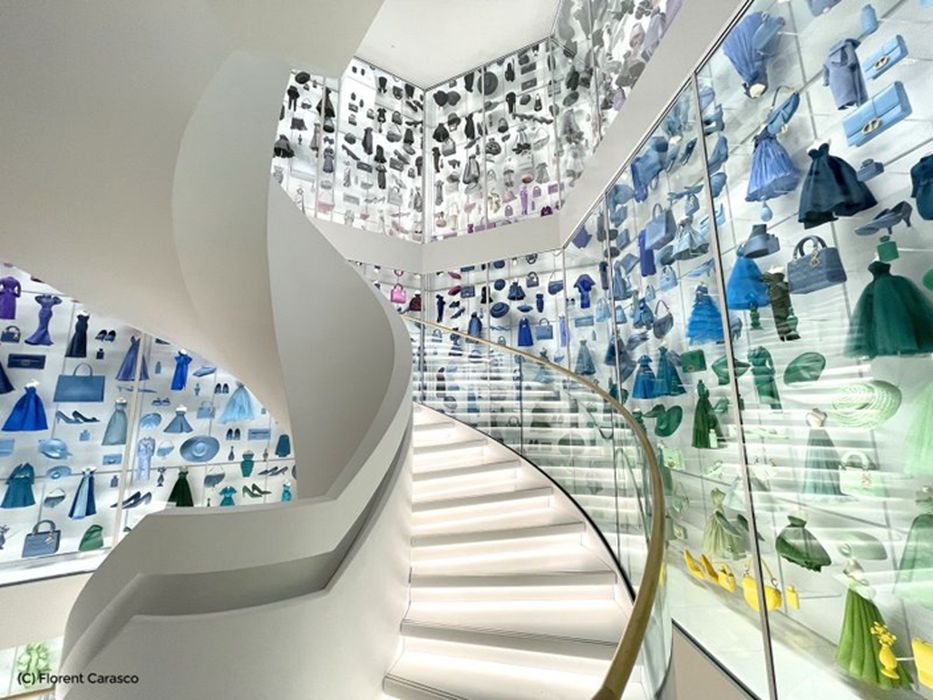
Charles R. Goulding and Preeti Sulibhavi look at the use of 3D printing in the high fashion industry.
In April 2022, Paris Fashion Week took place and one of the major events was the relaunch of the flagship Dior Boutique on the Champs-Elysees after two years of being shuttered due to Covid-19. Built in 1865 by the son of Napolean I, the 8th arrondissement hotel particulier, the massive, 108,000 square-foot space is the largest Dior boutique in the world.
Art runs deep within the house’s origins. Before becoming a fashion icon, Christian Dior was a gallerist. He co-founded Paris’s Galerie Jacques Bonjean in 1928, and from 1931 he was affiliated with Galerie Pierre Colle.
We have written about 3D Printing and the Rise of Professional Designer Artisan Fabricators, so the artisan and design worlds are no strangers to 3D printing. We have also covered 3D printing in the fashion industry, particularly the brand that houses Dior, LVMH.
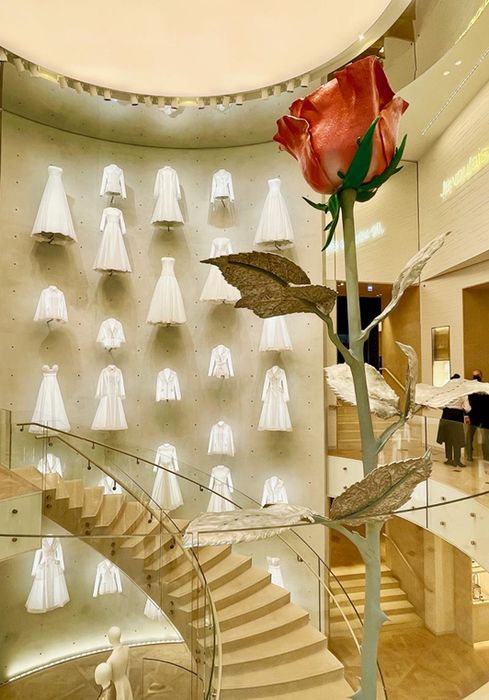
The Paris Dior Boutique also encompasses a full range of Dior products, including fashion lines for men and women, jewelry, handbags, shoes, glassware, crystalware, perfume and cosmetics.
The museum, La Galerie de Dior, opened next door and displays 130 mannequins wearing the haute couture outfits, films and newsreels, artifacts, sketches, with Dior perfume bottles, shoes and accessories in its 21,000 square-foot gallery covering three stories.

The products, mannequins and miniatures depicted in the images above are all items that can be 3D printed. There is no shortage of opportunities for 3D printing to avail itself to in terms of design, shape, texture, and materials.
Dior is utilizing 3D printing. In fact, much of the nearly 1,500 objects were possible because of the collaboration between the Agency Alighieri and La Ferme 3D, a French 3D printing farm based in Saint Rémy de Provence. It is no surprise that 3D printers helped to create historical, exceptional, delicate, and intricate replicas of Dior’s sublime designs.
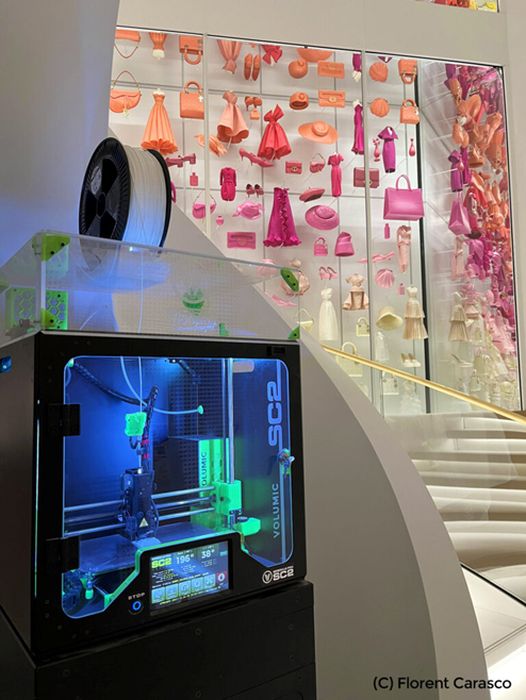
The Research & Development Tax Credit
The now permanent Research and Development (R&D) Tax Credit is available for companies developing new or improved products, processes and/or software.
3D printing can help boost a company’s R&D Tax Credits. Wages for technical employees creating, testing and revising 3D printed prototypes can be included as a percentage of eligible time spent for the R&D Tax Credit. Similarly, when used as a method of improving a process, time spent integrating 3D printing hardware and software counts as an eligible activity. Lastly, when used for modeling and preproduction, the costs of filaments consumed during the development process may also be recovered.
Whether it is used for creating and testing prototypes or for final production, 3D printing is a great indicator that R&D Credit eligible activities are taking place. Companies implementing this technology at any point should consider taking advantage of R&D Tax Credits.
Conclusion
Fashion is an industry where there is room for 3D printing to grow and be more intricately utilized. Particularly now, with the customization and more modern material selection, 3D printing is more relevant in the fashion industry today, than ever before.