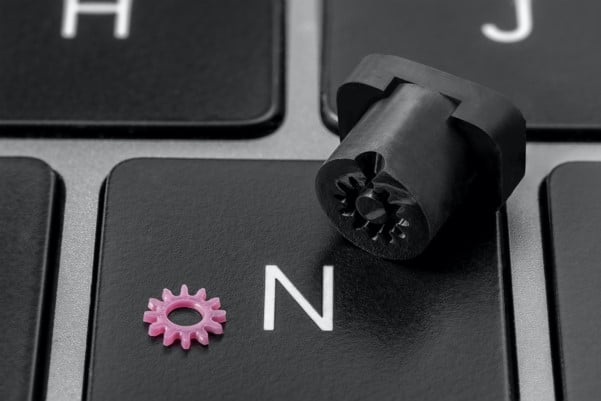
SPONSORED CONTENT
I sat down with Nanofabrica’s Executive Vice President Global Sales, Avi Cohen, to discuss the past, present, and future of micro additive manufacturing and the benefits and applications of the company’s Micro AM technology.
Avi started working with Nanofabrica as the EVP Global Sales. His career started in sales, marketing, and high-level management positions in various biomedical companies, and he has over 23 years of experience in additive manufacturing.
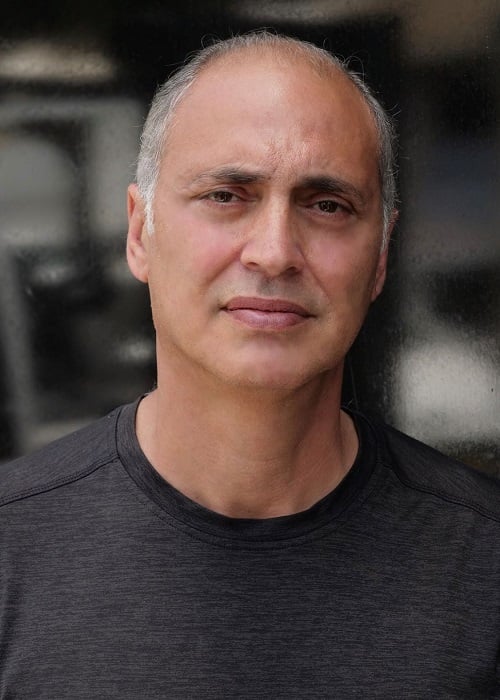
Existing at the interface of 3D printing for production and the industry-wide drive towards miniaturization, Nanofabrica has commercialized its industrial micro additive manufacturing (AM) technology, the Tera 250. The technology lifts the lid for designers and manufacturers in their quest to embrace the inherent advantage of AM, and enables them to exploit the ability that exists through 3D printing to build complex parts in small, medium, and high volumes in a timely and cost-effective fashion. We asked Avi Cohen, Global EVP Sales at Nanofabrica, about the growth and future plans for the company.
Fabbaloo: Can you briefly explain how the Tera 250 works?
Avi Cohen: “The Tera 250 is based around a Digital Light Processor (DLP) engine, but to achieve repeatable micron levels of resolution combines DLP with the use of adaptive optics. This tool in conjunction with an array of sensors, allows for a closed feedback loop, the reason that Nanofabrica’s Tera 250 can achieve very high accuracy while remaining cost-effective as a manufacturing solution. In addition, through rigorous R&D, Nanofabrica has managed to develop its own proprietary materials which enable ultra-high resolution in parts built.”
Fabbaloo: How is Nanofabrica reacting to the easing of COVID-19 lockdown restrictions?
Avi Cohen: “In common with many companies, trading through the lockdowns contingent upon the global COVID-19 pandemic has distorted Nanofabrica’s ability to engage with its customers and potential customers. Now that there seems to be an end point in the pandemic-related restrictions, Nanofabrica is today emerging with an aggressive and concerted campaign that sees it taking a prominent position at various leading trade shows and events, and also taking part in online and face-to-face activities that allow us to engage properly with our potential customer base.
In addition, we are able to announce details of a growing customer base that has invested in the Tera 250 technology, and are beginning to see the commercial advantages of using a micro AM solution for precise plastic part production, instead of having to rely on traditional and often time-consuming and relatively expensive technologies such a micro injection molding.”
Fabbaloo: Can you give us some details of these customers?
Avi Cohen: “Well, one is Aran Research and Development in Caesarea in Israel. Aran R&D has been using AM for many years and so already understood the value of the technology for its customers. But they were constrained by the fact that there was not an AM technology that could produce micro-parts with the levels of accuracy or resolution necessary for its clients across industry. Nanofabrica’s Tera 250 changed that perception.
Aran R&D sees the investment in the Tera 250 as a game changer. It is a strategically important move for the company which can now cater for small and medium volume runs of micro-parts uneconomic with conventional molding technologies.
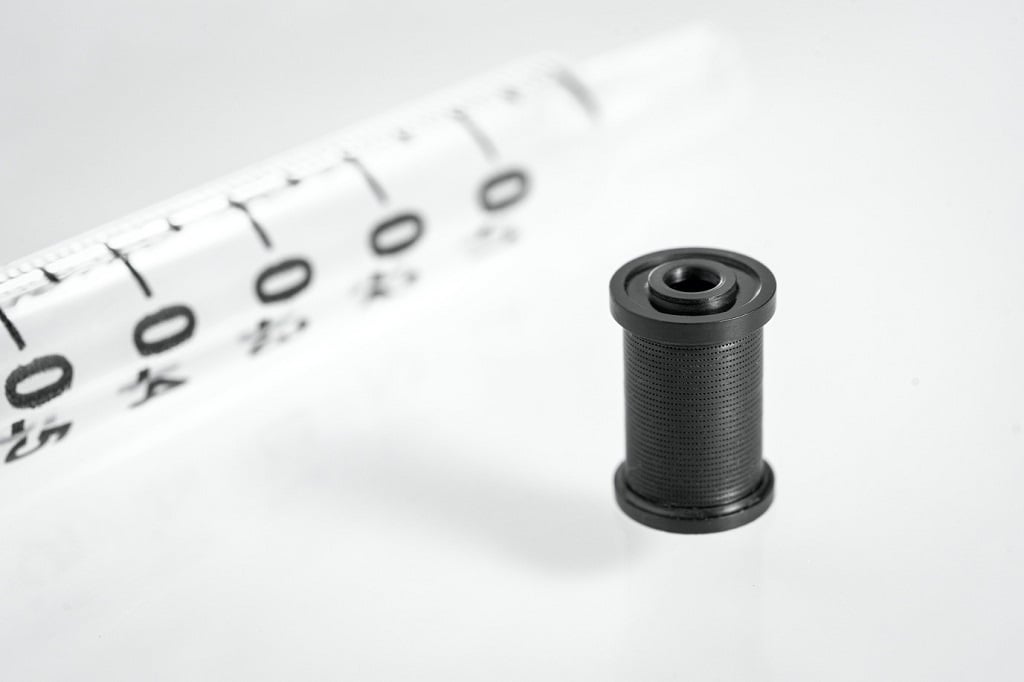
However, Aran sees the use of the Tera 250 to push product innovation as most important.
AM allows the manufacture of parts with geometric complexity impossible using traditional manufacturing processes, and the Tera 250 therefore places Aran R&D in a unique position to cater for the demand from across industry for extremely accurate and innovative micro-parts.
Moving forward, AM will continue to be used as a replacement for traditional manufacturing technologies, and this will continue to be focussed on applications where the use of the technology reduces the time and cost of manufacturing as is the case with Aran. 3D printing is no longer a technology that can only be used for one-offs or very short runs. The technology in general is now able to cater for mid-volume runs today, and at Nanofabrica in particular (where the focus is on the production of micro-scale parts and components), the Tera 250 can obviously fit numerous products in a single build envelope, so the company nudges into the area of mass high volume manufacturing very easily.
As a general rule of thumb, for 3D printing to be used as a rapid manufacturing technology for any given application it will have to have demonstrate at a minimum a 10-fold improvement in cost and/or time savings to offset the cost and risk associated with changing over from a traditional manufacturing technology. For Aran, this is absolutely the case, and proves that for them, 3D printing is a clear and efficient alternative to traditional manufacturing processes today.”
Fabbaloo: We hear news that a leading micro molding company has also recently purchased a Tera 250 machine?
Avi Cohen: “Yes indeed. Using Nanofabrica’s technology, manufacturers can benefit from the inherent advantages that AM offers: part complexity with no increase in cost, eliminating expensive tooling, reducing part counts and the need for assembly, reduction of time-to-market, easy revision of part design, providing opportunities for mass customization, as well as reducing waste and energy costs.
The Tera 250 micro AM system empowers our customers with new service capabilities, most notably in low and medium volume production runs where the cost of traditional tooling would render projects non-viable. A main area of interest is the production of direct rapid soft tooling (DRST) with the Tera 250, which facilitates prototyping and low volume production without the lead times and costs associated with traditionally fabricated tooling. In addition, the Tera 250 opens up the possibilities of mass customisation and promotes design freedom as AM can manufacture parts with geometric complexity which are impossible when using traditional plastic processing technologies.
Prior to the launch of the Tera 250, DRST had been regarded as sub-optimal when viewed through the prism of surface finish, precision, accuracy, and repeatability, while the number of materials that could be processed has also been a limiting factor. The Tera 250 system addresses these challenges to reach micron-level resolution, produce high surface finish, and reduce the time-consuming and costly need to cut steel.
Nanofabrica has achieved ground-breaking successes fabricating high numbers of parts of a single DRST made using the Tera 250 technology. The Tera 250 has succeeded in injecting standard thermoplastic materials such as PP, PE and ABS into a 3D-printed mould that was manufactured with a new proprietary material the company developed. Nanofabrica and its customers will work together to further enhance the DRST process on the Tera 250, marking a pivotal and strategic partnership which will be mutually beneficial and rewarding for both companies.”
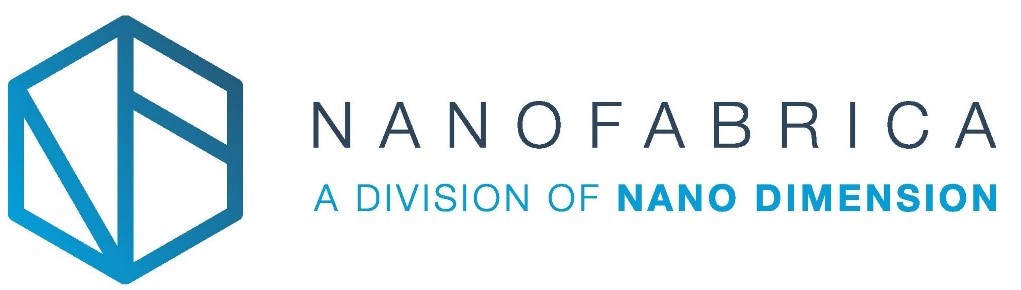
Fabbaloo: What are Nanofabrica’s immediate next steps as we move to the end of 2021?
Avi Cohen: “The relationship with all our new customers indicates that Nanofabrica has remained busy during the pandemic, and has established a healthy customer and user base, and has secured positive interest from across various industry sectors for an array of end-use part and component applications.
Moving forward, the key is to build on this momentum, and Nanofabrica will be exhibiting at the upcoming Rapid 2021 and Formnext events. At Rapid 2021 13-15 September in Chicago, IL, USA Nanofabrica will be showcasing the parts that can be produced on the Tera 250 machine on booth E8540. At Formnext 16-19 November, Frankfurt, Germany, the Tera 250 machine will for the first time be accessible to a wide potential customer base, and attendees at both events are invited to engage with the Nanofabrica team to discuss specific applications and their appropriateness to micro AM.”
Via Nanofabrica